Valve Body Material Compatibility
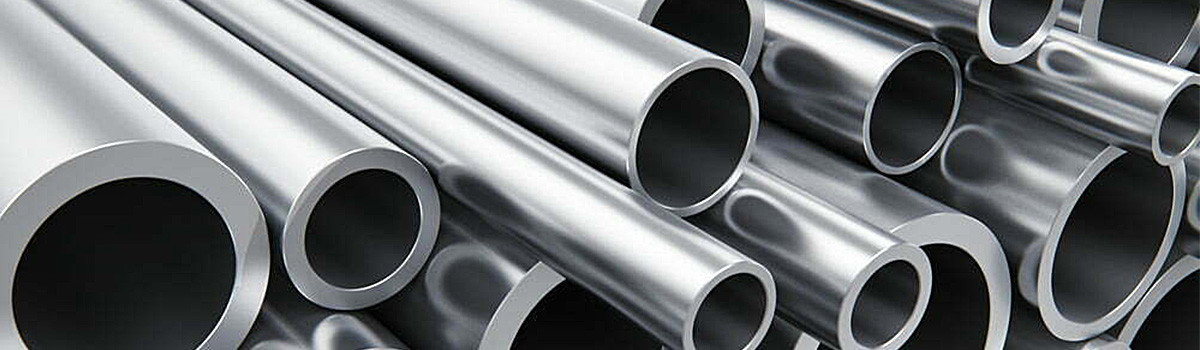
How to choose the right material for valves
There are several factors to consider when choosing material for your valves. First, you need to consider what media they will handle. The material must be able to withstand the media normally present in the line as well as media that may enter the line or the external environment around the valve.
Then you also need to consider:
*the specific requirements of your application
*process conditions
*and compatibility requirements
The material selection is critical for ensuring long-term performance, reliability, and safety.
The choice of material for the valve body and the seals (diaphragm, O-rings) is determined by the type of liquid or gas, the concentration, the pressure and temperature. Manyconditions can affect the material choices. Carefulconsideration must be given to temperature, pressure and chemical concentrations before a final material can be selected.
Valve Body Material Compatibility
The most common body materials for the valve body are brass, stainless steel and nylon. Brass is the most popular material for solenoid valves. It is very robust and resistant to many chemicals, but for example less suitable for sea water or distilled water. Stainless steel is recommended for corrosive media, such as seawater. Moreover, it is wear-resistant, which makes it very suitable for intensive use. Nylon is the cheapest variant, has good mechanical properties and is suitable for many media.
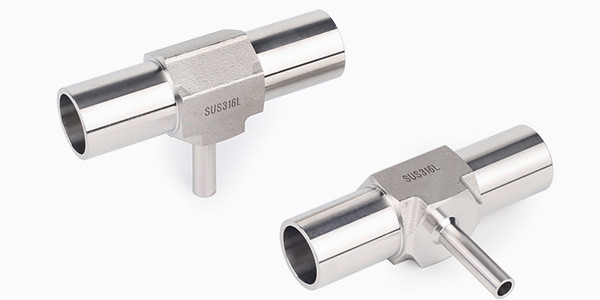
Chemicals
Valve materials compatibility with chemicals can vary depending on the specific chemicals involved. Some materials may corrode, i.e. rust. Which material is suitable depends on how resistant it is to corrosion caused by the liquid or gas to be handled. However, certain materials are commonly used due to their general chemical resistance properties.
We offer several valve materials for chemical applications. Here are some of them and their typical chemical compatibilities:
Stainless Steel (EN 1.4408 and 1.4409): Stainless steel is widely used due to its excellent corrosion resistance properties. It is compatible with a wide range of chemicals, including acids (such as sulfuric acid, hydrochloric acid), alkalis, organic solvents, and many corrosive fluids.
Titanium is a material that can withstand chlorides, which are found in e.g. salt water and chemicals. While titanium is a more expensive option, its light weight can bring down the cost of transport, operation and maintenance.
Steel alloys such as acid-resistant steel (EN 1.4409, EN 1.4408) are very common, but to offer higher corrosion resistance, duplex, super duplex, 904L or SMO grades such as 254 may be sufficient at lower concentration of chlorides e.g sea water at low temperatures. Carbon steel and cast iron corrode rapidly in an industrial environment, unlike the more expensive acid-resistant steels.
Hastelloy: Hastelloy alloys (such as Hastelloy C276) offer exceptional resistance to a wide range of corrosive chemicals, including strong acids, alkalis, oxidizing agents, and harsh environments. They are commonly used in demanding chemical processing applications.
Gas
Valve materials compatibility with gases depends on the specific gas being handled. Helium for example is a gas that is very difficult to isolate. Hydrogen atoms are forced into the material and damage the valve from the inside, a process called Hydrogene embritelment. Helium therefore requires the right material in the valve for the seals to hold.
Leakage of toxic gases or gases that have a climate impact on the atmosphere is a problem in all industries. By using valves meeting the fugitive emission standards according to ISO 15848-1 and VDI 2440 (TA-luft), the problem can be avoided or limited.
Here are some materials we use in our valves and their general compatibility with gases:
Stainless Steel (EN 1.4408 and 1.4409): Stainless steel valves are generally compatible with a wide range of gases, including inert gases, hydrocarbons, and non-corrosive gases. Stainless steel offers good resistance to corrosion and can withstand high-pressure and high-temperature gas applications. In addition, Stainless steel is highly resistant to hydrogen embrittlement, making it a safe and reliable choice for hydrogen gas applications.
Hastelloy: Hastelloy alloys, such as Hastelloy C276, are highly resistant to corrosive gases, including acidic or alkaline gases. They are commonly used in demanding gas processing applications where high corrosion resistance is required.
Duplex and Super Duplex: Duplex and super duplex materials (e.g., SAF 2205, SAF 2507) provide superior corrosion resistance in aggressive environments, making them suitable for handling corrosive gases. These materials offer excellent resistance to pitting, crevice corrosion, and stress corrosion cracking. Duplex and super duplex valves are commonly used in offshore, chemical, and oil and gas applications, where gases with high chloride content or acidic gases are encountered.
904L: 904L is a high-alloy austenitic stainless steel known for its excellent resistance to a variety of aggressive media, including sulfuric acid, phosphoric acid, and other acidic gases. It offers good strength and toughness, making it suitable for gas industry, chemical, and pulp and paper applications where corrosive gases are present.
254SMO: 254SMO (EN 1.4547), a super-austenitic stainless steel, exhibits exceptional resistance to a wide range of corrosive gases, such as sulfuric acid, hydrochloric acid, and acetic acid. It is highly resistant to pitting, crevice corrosion, and stress corrosion cracking, even in harsh environments. 254SMO valves are commonly utilized in chemical, pulp and paper, and offshore applications.
Titanium*: Titanium is highly resistant to a wide range of corrosive gases, including wet chlorine, hydrochloric acid, and many organic compounds. It offers exceptional resistance to pitting and crevice corrosion and maintains its integrity at elevated temperatures. Titanium valves find applications in the chemical industry, petrochemical plants, and other environments where extreme corrosion resistance is required.
*There are different grades of titanium. The grades refer to different alloys or compositions of titanium and are designated by numbers or alphanumeric codes, each representing a specific composition and set of properties. Grade 5 is the most used one for valves, but also grade 2 is used. The choice of grade depends on the specific requirements of the application.
METALS USED IN VALVES & FITTINGS
ALUMINUM — A non-ferrous metal, very lightweight, approximatelyone-third as much as steel. Aluminum exhibits excellent atmospheric corrosion resistance, but can be very reactive with othermetals. In valves, aluminum is mainly used as an exterior trim component such as a handwheel or an identification tag.
COPPER — Among the most important properties of wrot coppermaterials are their thermal and electrical conductivity, corrosionresistance, wear resistance, and ductility. Wrot copper performswell in high temperature applications and is easily joined by soldering or brazing. Wrot copper is exclusively used for fittings.
BRONZE — One of the first alloys developed in the bronze age isgenerally accepted as the industry standard for pressure-ratedbronze valves and fittings. Bronze has a higher strength than purecopper, is easily cast, has improved machinability, and is very easily joined by soldering or brazing. Bronze is very resistant to pittingcorrosion, with general resistance to most chemicals less than thatof pure copper.
SILICONE BRONZE — Has the ductility of copper but much morestrength. The corrosion resistance of silicon bronze is equal to orgreater than that of copper. Commonly used as stem material inpressure-rated valves, silicon bronze has greater resistance tostress corrosion cracking than common brasses.
ALUMINUM BRONZE — The most widely accepted disc materialused in butterfly valves, aluminum bronze is heat treatable andhas the strength of steel. Formation of an aluminum oxide layer onexposed surfaces makes this metal very corrosion resistant. Notrecommended for high pH wet systems.BRASS — Generally good corrosion resistance. Susceptible tode-zincification in specific applications; excellent machinability.Primary uses for wrot brass are for ball valve stems and balls, andiron valve stems. A forging grade of brass is used in ball valvebodies and end pieces.
GRAY IRON — An alloy of iron, carbon and silicon; easily cast;good pressure tightness in the as-cast condition. Gray iron hasexcellent dampening properties and is easily machined. It is standard material for bodies and bonnets of Class 125 and 250 ironbody valves. Gray iron has corrosion resistance that is better thansteel in certain environments.
DUCTILE IRON — Has composition similar to gray iron. Specialtreatment modifies metallurgical structure, which yields highermechanical properties; some grades are heat-treated to improveductility. Ductile iron has the strength properties of steel using similarcasting techniques to that of gray iron.CARBON STEEL — Very good mechanical properties; good resistance to stress corrosion and sulfides. Carbon steel has highand low temperature strength, is very tough and has excellent fatigue strength. Mainly used in gate, globe, and check valves forapplications up to 850°F, and in one-, two-, and three-piece ball valves
3% NICKEL IRON — Improved corrosion resistance over grayand ductile iron. Higher temperature corrosion resistance andmechanical properties. Very resistant to oxidizing atmospheres.
NICKEL-PLATED DUCTILE IRON — Nickel coatings have received wide acceptance for use in chemical processing. Thesecoatings have very high tensile strength, 50 to 225 ksi. To someextent, the hardness of a material is indicative of its resistance toabrasion and wear characteristics. Nickel plating is widely specified as a disc coating for butterfly valves.
400 SERIES STAINLESS STEEL — An alloy of iron, carbon, andchromium. This stainless is normally magnetic due to its martensitic structure and iron content. 400 series stainless steel is resistantto high temperature oxidation and has improved physical and mechanical properties over carbon steel. Most 400 series stainlesssteels are heat-treatable. The most common applications in valvesare for stem material in butterfly valves and backseat bushingsand wedges in cast steel valves.
316 STAINLESS STEEL — An alloy of iron, carbon, nickel, andchromium. A nonmagnetic stainless steel with more ductility than400SS. Austinetic in structure, 316 stainless steel has very goodcorrosion resistance to a wide range of environments, is not susceptible to stress corrosion cracking and is not affected by heattreatment. Most common uses in valves are stem, body and ballmaterials.
17-4 PH STAINLESS STEEL® — Is a martensitic precipitation/age hardening stainless steel, offering high strength and hardness.17-4 PH withstands corrosive attack better than any of the 400series stainless steels, and in most conditions its corrosion resistance closely approaches that of 300 series stainless steel. 17-4PH is primarily used as a stem material for butterfly and ball valves.
ALLOY 20Cb-3® — This alloy has higher amounts of nickel andchromium than 300 series stainless steel and with the addition ofcolumbium, this alloy retards stress corrosion cracking and hasimproved resistance to sulfuric acid. Alloy 20 finds wide use in allphases of chemical processing. Commonly used as interior trimon butterfly valves.
MONEL® — Is a nickel-copper alloy used primarily as interiortrim on butterfly and ball valves. One of the most specified materials for corrosion resistance to sea and salt water. Monel is alsovery resistant to strong caustic solutions.
STELLITE® — Cobalt base alloy, one of the best all-purpose hardfacing alloys. Very resistant to heat, abrasion, corrosion, impact,galling, oxidation, thermal shock and erosion. Stellite takes a highpolish and is used in steel valve seat rings.Normally applied with transfer plasma-arc; Stellite hardness isnot affected by heat treatment.
HASTELLOY C® — A high nickel-chromium molybdenum alloy,which has outstanding resistance to a wide variety of chemicalprocess environments, including strong oxidizers such as wetchlorine, chlorine gas, and ferric chloride. Hastelloy C is also resistant to nitric, hydrochloric, and sulfuric acids at moderate temperatures.