CAD & 3D Prototyping For Pressure Regulator & Valve
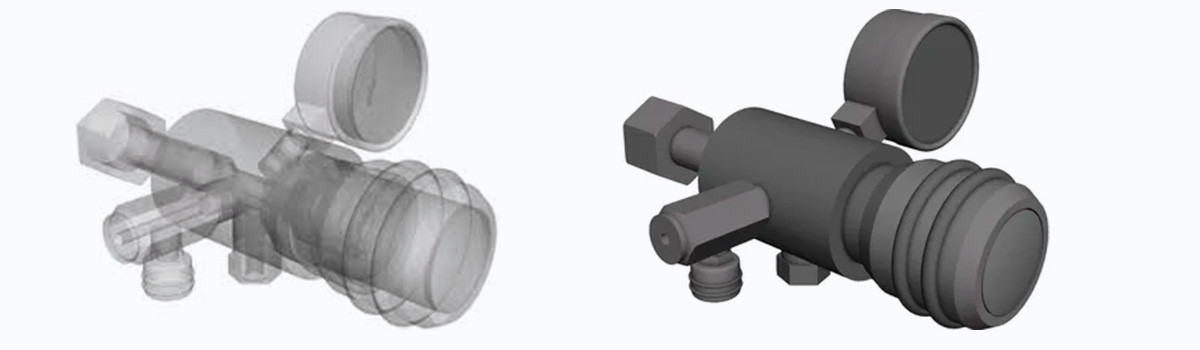
Prototyping with 3D Printing
Prototyping is an extremely important step in product development. Prototyping custom manufactured parts, in particular, provides the opportunity to evaluate your design, demonstrate its concept, inspect it for flaws, correct any issues, and improve overall design. However, traditional prototyping can be a very time-consuming and expensive process.
Valve manufacturers today have increasingly adopted techniques for 3D design and are exploring the possibility of Metal 3D printing. Originally developed in the 1980s, 3D printing (also known as additive manufacturing) has evolved dramatically over the past 30 years, enabling companies to fully customize and create more accurate prototypes and products than ever before.
Besides saving costs and time, additive manufacturing allows the same CAD software to be used to create various geometries, making it an extremely versatile process. And unlike CNC machining, 3D printing produces minimal waste, as the process only prints the material actually needed to create the desired product.
Steps of 3D Valve Design
The first step of designing any valve is assessing need. A request is made to create a new valve, with specific requirements as indicated by the purchaser. The valve manufacturer adheres to the specifics of the order, determines the best course of action, and the process(es) needed to fulfill it. In this stage, a 3D CAD drawing of the valve is created. The drawing, or design file is then uploaded to the related software program via computer.
The next step is Finite Element Analysis (FEA), which uses mathematical models to quantify real world effects on the valve. The simulations are conducted using specialized software that helps determine the source of potential problems, such as area of fault, weakness, or tension.
“The 3D soft-ware system is similar to creating a virtual environment. You plug in the perimeters of the valve, including materials, wall thicknesses and so forth, then conducts real life analysis and strength to verify it meets all given requirements,” said the valve expert. Following analysis, building begins as the 3D printer creates the product or part layer by layer over a series of hours. The time frame to print is determined based on size, specifications, and the like. Once printing is completed, the printed piece is removed and inspected. Further inspections can include dimensional inspections, various non-destructive examinations, performance testing and/or pressure testing depending on the component.
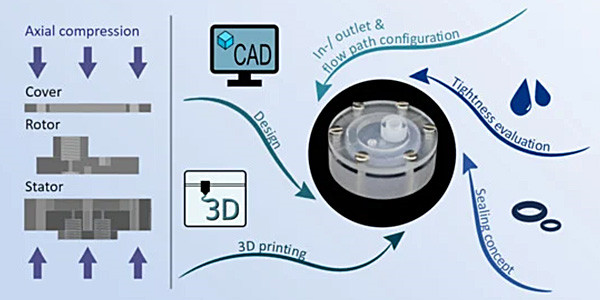
The benefits of 3D designing valves are obvious; increasing production efficiencies, and reducing overall wait time for customers to make, create, and receive their valves is very important to the market. The less time spent waiting for parts, the more up time the process or application will endure. Less time wasted directly translates to profit increase for companies, as valves are often critical components in industry. For example, a refinery in need of an isolation valve on a storage tank responsible for maintaining the separation of different oil products is imperative to avoid the cross contamination of fuels and maintain high quality product. This rapid improvement of prototypes, and the ease of access for customers, are huge benefits of the 3D valve design.
Elimination of material waste is another added benefit of 3D design. With computer-aided design, printing is precise and done layer by layer. This process further permits the manufacturing of unique and highly specified components. While 3D metal printing is currently applicable on smaller valve parts, traditional manufacturing methods are often wasteful and consume large amounts of raw materials and energy. Instead of foundering and machining a valve component from a large piece of material, 3D printing, in comparison, can create the component with considerably less waste. As much of the design is created on the computer, improvements are easier to implement, and simulations are made easier.
In some cases, 3D design imagery helps customers identify what they are requesting. If there is any type of customization, it also gives them a chance to review and improve upon it prior to its manufacture. That eliminates any guesswork for EPCs and engineering companies working on, for example, complex piping systems. 3D design is more detailed and flexible, as opposed to classic blue line drawings.
Those who build chemical plants and refineries utilize many different piping systems, running in several directions. With 3D design, engineers can walk through and inspect each valve and related piping component as if it was a virtual 3D environment. This often translates to earlier design approvals. 3D design can also streamline the manufacturing process, leading to greater efficiency gains.
3D technology ultimately increases speed and design flexibility, and reduces the risk and the amount of waste within additive manufacturing. No material limitations, alongside complete customization, higher yields, and lower costs are all extremely advantageous to 3D design and printing. This technology also offers huge benefit to those looking to create a prototype quickly and accurately.
As valve manufacturers continue to optimize 3D valve design and printing processes, end users will be offered more options than ever before. Real economic benefit will arrive as 3D printing becomes intrinsic to all facets of the manufacturing industry. In theory, the only limitation with 3D design is your imagination, and manufacturers like ISV are well equipped to manage the requests of existing, and future valve users.
3D Printing for Valve Prototypes
Prototyping is notoriously challenging in the valve industry; valves are incredibly complex multi-component parts that require a full set of custom tooling to prototype. Tooling is a huge driver of time and costs for valve prototyping, especially for check valve prototyping. Luckily, 3D printing is making as big an impact in valve manufacturing as it is in car manufacturing.
A 3D printer that can use for valve prototyping, and its impact has been tremendous. This printer provides us with functioning 3D models to present to clients, which has proven to be a huge boon for collecting quality feedback from customers.
Compatible with all existing CAD software, it allows our designers and engineers to incorporate that feedback almost immediately and carry those ideas forward as the project progresses. Perhaps most importantly, it allows us to prototype valves for customers at drastically lower price points than we were capable of previously.