Blog
Jewellok is a professional pressure regulator and valve manufacturer and supplier.
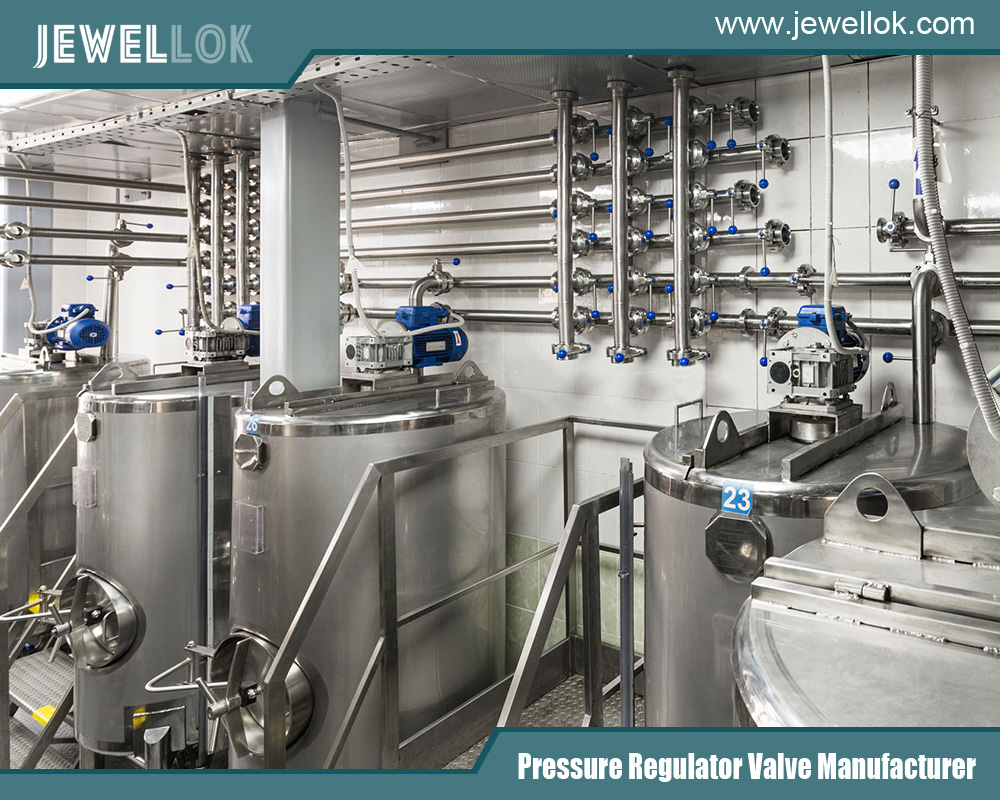
Understanding the Two Stage Pressure Regulator: Mechanism, Benefits, and Applications
- Pressure Regulator Valve Manufacturer
- 1/2 gas pressure regulator, adjustable propane pressure regulator, adjusting propane regulator, argon gas pressure regulator, high purity regulator, hydraulic regulator, low pressure regulator, pressure gauge manufacturers, safety relief valve vs pressure relief valve, solenoid water valve, stainless steel two stage pressure regulator, stainless steel two stage pressure regulator factory, stainless steel two stage pressure regulator hotsale, stainless steel two stage pressure regulator manufacturer, two stage pressure regulator, two stage pressure regulator factory, two stage pressure regulator hotsale, two stage pressure regulator manufacturer, two stage pressure regulator OEM, two stage pressure regulator supplier, what is a gas pressure regulator
- No Comments
Understanding the Two Stage Pressure Regulator: Mechanism, Benefits, and Applications
Two Stage pressure regulators are essential in various industries where maintaining a consistent, controlled gas or liquid flow is crucial. Unlike single-stage regulators, Two Stage regulators provide more stability in output pressure, even as inlet pressure fluctuates. This capability makes them indispensable in the aerospace, healthcare, energy, and laboratory industries. This article will explore the workings of Two Stage pressure regulators, their advantages over single-stage counterparts, and their broad applications.
Table of Contents
- What Is a Two Stage Pressure Regulator?
- How Does a Two Stage Pressure Regulator Work?
- Advantages of Using a Two Stage Pressure Regulator
- Applications of Two Stage Pressure Regulators
1. What Is a Two Stage Pressure Regulator?
A Two Stage pressure regulator is designed to maintain a steady output pressure regardless of variations in input pressure. This type of regulator has two distinct pressure reduction stages, which help maintain consistency and accuracy. Here’s an overview of its construction and purpose:
- Construction:Two Stage regulators comprise two regulating mechanisms or “stages” within a single unit.
- Purpose: By reducing pressure in two stages, these regulators offer greater precision in applications where stable pressure is essential.
2. How Does a Two Stage Pressure Regulator Work?
The working principle of a Two Stage pressure regulator involves two sequential steps:
- First Stage:The regulator reduces the high-pressure inlet gas or liquid to an intermediate level. This initial reduction helps stabilize significant fluctuations.
- Second Stage:The second stage further reduces the pressure to the desired output level, ensuring minimal deviation.
Critical Components of a Two Stage Regulator
Two Stage pressure regulators typically have the following parts:
- Diaphragm: Responds to pressure changes and adjusts the output pressure.
- Valve Seat: Regulates the flow of gas or liquid through each stage.
- Spring: Provides resistance, enabling pressure adjustments.
Working Mechanism at a Glance
- High-pressure gas enters the regulator and passes through the first stage.
- First-stage diaphragm compresses, controlling the pressure.
- Intermediate pressure is set, reducing large pressure fluctuations.
- The gas flows into the second stage, where the output is fine-tuned.
- The output pressure remains consistent regardless of inlet changes.
3. Advantages of Using a Two Stage Pressure Regulator
Using a Two Stage pressure regulator offers several benefits, making it the preferred choice in sensitive applications.
- Stable Output Pressure:The Two Stage design ensures minimal pressure fluctuation at the output, even as inlet pressure decreases over time.
- Improved Accuracy:With two control stages, these regulators offer higher accuracy and consistency in output pressure.
- Reduced Downtime and Maintenance:The stability provided by Two Stage regulators often results in less wear on equipment, leading to fewer maintenance needs.
Key Benefits at a Glance
- Reduced variation in output pressure
- Enhanced durability due to less strain on internal parts
- Increased safety in high-risk applications, such as gas handling
- Improved process efficiency in laboratory and industrial settings
4. Applications of Two Stage Pressure Regulators
Two Stage pressure regulators find uses in a range of applications where precise pressure control is crucial:
- Healthcare and Medical Equipment:A stable pressure flow is critical for patient safety in oxygen delivery systems.
- Laboratory Settings:Laboratories handling gasses for research purposes rely on precise pressure controls to ensure experimental accuracy.
- Welding and Cutting Operations:In industrial applications like welding, Two Stage regulators provide consistent pressure, vital for safety and quality.
- Aerospace and Defense:Ensuring stable pressure is essential for high-altitude operations, where equipment may experience rapid changes in environmental conditions.
Notable Applications by Industry
- Medical: Oxygen cylinders, ventilators, anesthesia machines
- Industrial: Gas welding, chemical processing
- Scientific Research: Laboratories working with volatile or sensitive gasses
- Energy Sector: Fuel cell research, alternative energy applications
Key Considerations When Choosing a Two Stage Pressure Regulator
When selecting a Two Stage pressure regulator, it’s essential to consider the specific requirements of your application to ensure optimal performance and safety. Below are vital factors to keep in mind:
Material Compatibility: Ensure the regulator’s materials are compatible with the controlled gas or liquid to avoid corrosion or damage.
- For corrosive gasses, look for stainless steel or other resistant materials.
- Brass or aluminum can be cost-effective choices for inert or non-reactive glasses.
Flow Rate Requirements: The regulator should be able to handle the required flow rate without causing excessive pressure drops.
- Select a regulator with a flow capacity suited to your system needs.
- Ensure it can accommodate peak flow demands without compromising pressure stability.
Pressure Range: Each regulator has a maximum inlet and outlet pressure rating. Choose one that matches your system’s requirements.
- Higher pressure ranges are typically needed for industrial applications.
- A lower pressure range may suffice for precision control for medical or laboratory use.
Temperature Conditions: Regulators perform differently under various conditions; ensure the regulator suits your environment.
- Look for high-temperature tolerance in industrial settings.
- Ensure cryogenic compatibility if used in low-temperature applications.
Maintenance and Lifespan: Consider how frequently the regulator will require maintenance based on your application’s intensity.
- Opt for regulators with minimal maintenance needs for continuous processes.
- Ensure availability of replacement parts or support for easy servicing.
Safety Features: Especially in high-pressure applications, safety features can prevent hazards.
- Check for built-in relief valves or shut-off mechanisms.
- Ensure compliance with industry standards for added safety.
Maintenance Tips for Two Stage Pressure Regulators
Regular maintenance of Two Stage pressure regulators is essential to ensure they continue performing accurately and safely. Here are crucial maintenance tips to help extend the lifespan of your regulator and maintain stable pressure control:
Regular Inspection: Check the regulator for any visible signs of wear or damage.
- Look for leaks, cracks, or signs of corrosion on the body or connectors.
- Inspect the diaphragms and seals, as these are prone to wear over time.
Cleaning: Ensure the regulator is kept clean if used in dusty or corrosive environments.
- Use a soft cloth or brush to remove dust and debris from external surfaces.
- Avoid using harsh chemicals that may damage sensitive internal components.
Lubrication: Apply lubricant to moving parts as the manufacturer recommends to keep the regulator operating smoothly.
- Only use lubricants approved for the specific type of regulator.
- Avoid over-lubricating, as this can attract dust and cause internal blockages.
Calibration: Regularly calibrate the regulator to maintain accuracy, especially when precise pressure is crucial.
- Follow the manufacturer’s guidelines for calibration intervals.
- Use proper calibration tools and follow safety procedures to ensure accurate results.
Replace Worn Parts: To maintain performance, seals, valves, and diaphragms must be replaced over time.
- Keep a maintenance schedule for part replacement based on usage intensity.
- Only use genuine replacement parts to ensure compatibility and reliability.
Pressure Testing: Conduct pressure tests periodically to verify that the regulator maintains stable output pressure.
- Perform leak tests after maintenance to ensure there are no gas leaks.
- Test the regulator under normal operating conditions to ensure stability.
Conclusion
Two Stage pressure regulators maintain stable output pressures in various high-precision applications. Their two-step pressure reduction process provides enhanced accuracy, improved stability, and reduced maintenance demands, making them invaluable across industries. From healthcare to aerospace, Two Stage regulators ensure the safety, consistency, and efficiency required in today’s advanced technological landscapes. A two stage pressure regulator is often the ideal solution for any setting that requires precise and stable pressure control.
For more about understanding the two stage pressure regulator: mechanism, benefits, and applications, you can pay a visit to Jewellok at https://www.jewellok.com/ for more info.
Recent Posts
Tags
Recommended Products
-
774L Stainless Steel UHP Fittings Butt Weld Bulkhead Union For High Flow Special Gas Fluid
-
Stainless Steel 316L Single Stage Regulator Pressure Control Panels JSP-1E Series For Semiconductor Fluid Control
-
High Purity High Pressure Stainless Steel Needle Valve Natural Gas Flow Control Valve JNV Series
-
Fully Automated Gas Cabinet Gas Rack Gas Delivery Systems JW-300-GR
-
High Purity Bulk Specialty Gas Pressure Control And Filtration Bulk Gas Skid Systems JW-300-BSGS
-
FT-BOX JW-FTB-C Valve Manifold Panels And Boxes With High Purity Configurable Systems
-
764L Stainless Steel Union Tee High Purity Fitting Union Tee Reducing Tubing Connection
-
316L Stainless Steel Tube Butt Weld Reducing Fittings Union Reducer RW Series Ultrahigh Purity Process