Blog
Jewellok is a professional pressure regulator and valve manufacturer and supplier.
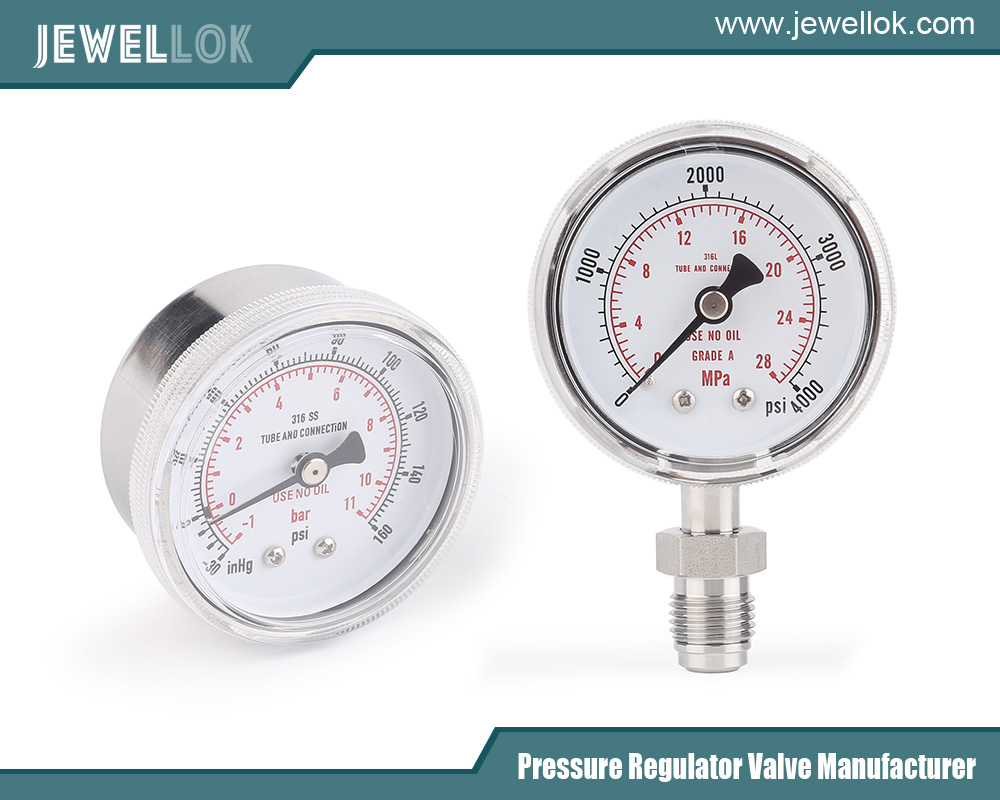
Ultra High Purity Diaphragm Valves: Key Applications and Developments in High-Purity Fields
- Pressure Regulator Valve Manufacturer
- 1 1 2 gas pressure regulator, 1 2 gas regulator, 1 2 propane regulator, 1/2 gas pressure regulator, 12v electric valve, 8mm compression fitting, adjustable propane pressure regulator, electric water valve, gas pipeline valve, gas pipeline valves, gas used in semiconductor chip manufacturing, gases used in semiconductor manufacturing, high pressure argon regulator, high pressure flexible hose pipe, high purity regulator, how a regulator works, how solenoid valve works, industrial regulators, irrigation timer valve, lab fittings exporter, laboratory gas valves, pressure regulator, pressure safety valve vs relief valve, propane pressure regulator valve, relief valve and safety valve difference, safety valve vs relief valve, semiconductor gas, single stage pressure regulator, Ultra High Purity Diaphragm Valves, ultra high purity diaphragm valves manufacturer, valve manifold box, water valve timer, what is a flame arrestor
- No Comments
Ultra High Purity Diaphragm Valves: Key Applications and Developments in High-Purity Fields
In modern industry, the requirements for the precision and purity of fluid control are becoming increasingly stringent. As a type of valve capable of meeting extremely high purity requirements, ultra-high purity diaphragm valves play an indispensable role in numerous fields. In addition to the well-known semiconductor manufacturing field, ultra-high purity diaphragm valves also have important applications in many other industries with extremely high purity requirements. This article will delve into these application fields and their key roles.
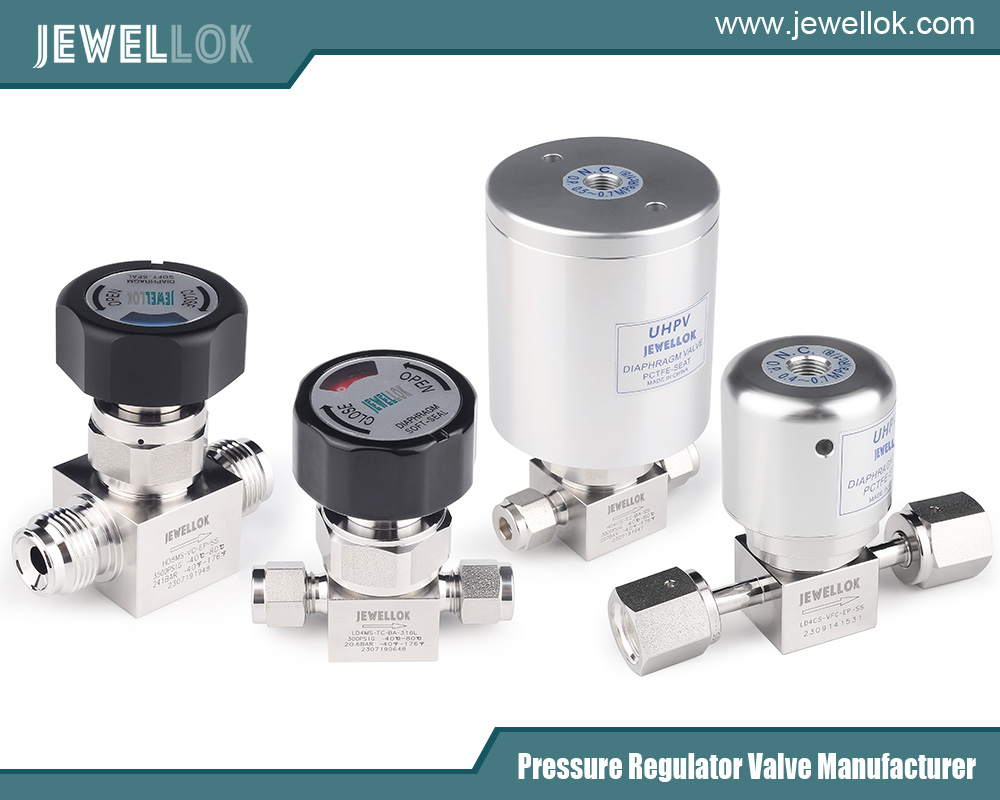
Working Principle and Characteristics of Ultra-High Purity Diaphragm Valves
I. Working Principle
Ultra-high purity diaphragm valves are mainly composed of components such as the valve body, diaphragm, valve stem, and driving device. Their working principle is based on the elastic deformation of the diaphragm. By controlling the up-and-down movement of the valve stem through the driving device, the diaphragm is driven to change its shape, thereby achieving the opening, closing, or flow regulation of the fluid passage. When the diaphragm moves upward, the fluid passage is opened, and the fluid can pass through smoothly; when the diaphragm moves downward and closely adheres to the valve seat, the fluid passage is blocked, preventing the fluid from flowing. This unique working method isolates the fluid from other components of the valve, effectively avoiding fluid contamination.
II. Characteristics
- Ultra-High Purity: All components of the ultra-high purity diaphragm valve that come into contact with the fluid, such as the diaphragm and valve body, are made of special high-purity materials. Moreover, strict cleanliness control measures are implemented during the production, processing, and assembly processes to ensure that the valve itself will not cause any contamination to the fluid, meeting the demanding requirements of high-purity applications.
- Good Sealing Performance: A tight seal can be formed between the diaphragm and the valve seat, effectively preventing fluid leakage. This is of vital importance in occasions with extremely high fluid purity requirements, avoiding the mixing of external impurities into the fluid and the loss of the fluid.
- Corrosion Resistance: For different application fluids, ultra-high purity diaphragm valves can be made of materials with excellent corrosion resistance, such as special plastics and alloys, to ensure long-term stable operation in various corrosive media environments and extend the service life of the valve.
- Precise Flow Control: Through a reasonably designed driving device and valve stem mechanism, ultra-high purity diaphragm valves can achieve precise regulation of fluid flow, meeting the strict requirements of different process processes for flow, which helps to improve production efficiency and product quality.
Review of the Application of Ultra-High Purity Diaphragm Valves in the Semiconductor Manufacturing Field
In the semiconductor manufacturing process, ultra-high purity diaphragm valves are one of the key components to ensure the precision of the chip manufacturing process and product quality. For example, in key processes such as photolithography, etching, chemical vapor deposition (CVD), and atomic layer deposition (ALD), precise control of the flow and on-off of various ultra-pure gases and chemical liquids is required. Ultra-high purity diaphragm valves, with their ultra-high purity, fast response speed, and precise flow control ability, can meet the strict requirements of these processes for fluid control. In the ALD process, ultra-high purity diaphragm valves are used to accurately measure and transport precursor gases, ensuring the growth of high-quality films layer by layer on the chip surface. Their small flow control accuracy and fast switching response are crucial for ensuring the performance and reliability of the chip.
Applications of Ultra-High Purity Diaphragm Valves in Other Fields with High Purity Requirements
I. Pharmaceutical Industry
- Fluid Control in the Pharmaceutical Production Process: In pharmaceutical production, from the transportation of raw materials, the preparation of medicinal liquids to the filling of finished products, every link has strict requirements for the purity and control precision of the fluid. Ultra-high purity diaphragm valves are used to control the flow of various pharmaceutical raw materials, solvents, purified water for injection, and other fluids, ensuring that the pharmaceutical production process is free from pollution and guaranteeing the quality and safety of the drugs. In the production of sterile drugs, the sealing performance and cleanliness of ultra-high purity diaphragm valves are of great importance, which can effectively prevent the intrusion of microorganisms and particles and comply with the requirements of Good Manufacturing Practice (GMP) for pharmaceutical production.
- Cleaning and Disinfection of Pharmaceutical Equipment: Pharmaceutical equipment needs to be strictly cleaned and disinfected before and after use to prevent cross-contamination. Ultra-high purity diaphragm valves can be used to control the flow of cleaning liquids and disinfectants, ensuring the effectiveness and reliability of the cleaning and disinfection process. Their corrosion resistance enables them to adapt to various strongly corrosive cleaning and disinfection media, while maintaining good sealing performance and avoiding the impact of media leakage on the equipment and the environment.
- Waste Liquid Treatment and Recycling: Various waste liquids will be generated during the pharmaceutical process. Some waste liquids need to be treated to meet the discharge standards, while some valuable components need to be recycled and reused. Ultra-high purity diaphragm valves are used to control the flow direction and transfer of waste liquids, ensuring the standardization and high efficiency of the waste liquid treatment process, and at the same time realizing the recycling of resources, reducing production costs, and minimizing environmental pollution.
II. Food and Beverage Industry
- Transportation Control of Raw Materials and Products: In the production process of food and beverages, from the procurement of raw materials to the processing and packaging of finished products, ultra-high purity diaphragm valves are used to control the transportation of various food raw materials, additives, beverages, and other fluids, ensuring the purity and hygiene safety of the products. In the production of fruit juices, milk, and other beverages, ultra-high purity diaphragm valves can accurately control the flow of ingredients, ensuring the consistency of product taste and quality, and at the same time preventing the mixing of impurities, which meets food safety standards.
- Equipment Cleaning and Sterilization: Food and beverage production equipment needs to be regularly cleaned and sterilized to ensure the cleanliness of the equipment and prevent the growth of microorganisms. Ultra-high purity diaphragm valves are used to control the flow of cleaning water, cleaning agents, and sterilizers. Their good sealing performance and corrosion resistance can ensure the smooth progress of the cleaning and sterilization process and avoid pollution to the equipment and products. For example, in the beer brewing process, the cleaning and disinfection of fermentation tanks and pipelines require ultra-high purity diaphragm valves to accurately control the flow and on-off of cleaning and sterilization media to ensure the quality and flavor of the beer.
- Supply of Pure Water and High-Purity Gases: In the food and beverage production, pure water and high-purity gases are indispensable. Ultra-high purity diaphragm valves are used to control the preparation and transportation process of pure water, as well as the application of high-purity gases (such as nitrogen, carbon dioxide, etc.) in food preservation and inflatable packaging, ensuring the purity and quality of these key resources and meeting the strict requirements of the food and beverage industry for the production environment and product quality.
III. Liquid Crystal Display (LCD) and Organic Light Emitting Diode (OLED) Manufacturing Industry
- Photolithography and Etching Processes: In the manufacturing process of LCD and OLED panels, photolithography and etching processes are key links, which require precise control of the flow and on-off of various ultra-pure chemical reagents and gases. Ultra-high purity diaphragm valves can meet the high-precision requirements of these processes for fluid control, ensuring the formation of precise circuit patterns and thin film structures on the panel. In the coating and development process of photoresist, ultra-high purity diaphragm valves are used to control the flow of photoresist and developer, ensuring the precision and quality of the pattern; in the etching process, ultra-high purity diaphragm valves are used to control the flow of etching gas, achieving precise etching of different materials and improving the performance and production efficiency of the panel.
- Transportation of Liquid Crystal Materials and Organic Light Emitting Materials: The purity of liquid crystal materials and organic light emitting materials has a direct impact on the display effect of LCD and OLED panels. Ultra-high purity diaphragm valves are used to control the transportation process of these materials, ensuring that they are not contaminated during transportation and use and maintaining good performance and stability. Their precise flow control ability can also achieve accurate control of the material usage, reducing production costs and improving product quality.
- Supply of High-Purity Gases: In the manufacturing process of LCD and OLED, a variety of high-purity gases, such as nitrogen, argon, etc., are required for processes such as protective atmosphere, cleaning, and drying. Ultra-high purity diaphragm valves are used to control the flow and on-off of these gases, ensuring the purity and supply stability of the gases, providing a good production environment for panel manufacturing, and ensuring the quality and performance of the products.
IV. Solar Photovoltaic Industry
- Silicon Wafer Manufacturing Process: In the solar photovoltaic industry, silicon wafers are the main raw materials, and their manufacturing process has extremely high requirements for purity. Ultra-high purity diaphragm valves are used to control the flow and on-off of various chemical reagents such as silicon wafer cutting fluid, cleaning fluid, and etching fluid, ensuring that the silicon wafers are not contaminated during the processing process and guaranteeing the quality and performance of the silicon wafers. In the silicon wafer cutting process, ultra-high purity diaphragm valves are used to precisely control the flow of cutting fluid, improving the cutting efficiency and the flatness of the silicon wafers; in the silicon wafer cleaning and etching processes, ultra-high purity diaphragm valves can ensure the uniform supply of cleaning fluid and etching fluid, removing impurities and defects on the surface of the silicon wafers and improving the photoelectric conversion efficiency of the silicon wafers.
- Cell Production Process: From the silicon wafer to the cell production process, there are multiple links that require high-precision fluid control, such as diffusion, coating, printing, and other processes. Ultra-high purity diaphragm valves are used to control the flow of various gases and liquids in these processes, ensuring the production quality and consistency of the cells. In the diffusion process, ultra-high purity diaphragm valves are used to control the flow of phosphorus source gas, precisely controlling the impurity concentration on the surface of the silicon wafer and forming a good PN junction; in the coating process, ultra-high purity diaphragm valves are used to control the flow of coating materials, ensuring the uniformity and quality of the film and improving the photoelectric conversion efficiency of the cells.
- Supply of High-Purity Gases: The solar photovoltaic production process requires a large amount of high-purity gases, such as hydrogen, nitrogen, oxygen, etc., for various process links. Ultra-high purity diaphragm valves are used to control the flow and on-off of these gases, ensuring the purity and supply stability of the gases, providing a reliable guarantee for the production of solar photovoltaic cells, reducing production costs, and improving production efficiency.
V. Medical Diagnosis and Biological Analysis Industry
- Preparation and Transportation of In Vitro Diagnostic Reagents: In the field of medical diagnosis, the quality and purity of in vitro diagnostic reagents directly affect the accuracy of the diagnostic results. Ultra-high purity diaphragm valves are used to control the preparation and transportation process of various in vitro diagnostic reagents, ensuring that the reagents are not contaminated and guaranteeing the reliability of the diagnostic results. In biochemical analyzers, immunoassays, and other equipment, ultra-high purity diaphragm valves are used to precisely control the flow of reagents, achieving accurate detection and analysis of samples.
- Biological Sample Processing: In biological analysis and research, the processing of biological samples requires strict control of the environment and the purity of the fluid to avoid sample contamination and interference. Ultra-high purity diaphragm valves are used to control the flow and on-off of various liquids in the biological sample processing process, such as buffer solutions, lysis solutions, elution solutions, etc., ensuring the integrity and purity of the biological samples and providing reliable experimental conditions for biological research and diagnosis.
- Laboratory Pure Water Systems: Medical diagnosis and biological analysis laboratories need to use high-purity water to prepare reagents, clean instruments, and conduct experimental operations. Ultra-high purity diaphragm valves are used to control the transportation and distribution of pure water in the laboratory pure water system, ensuring the purity and quality of the pure water, meeting the strict requirements of the experiment for water quality, and ensuring the accuracy and reproducibility of the experimental results.
Special Requirements for Ultra-High Purity Diaphragm Valves in Different Fields
I. Special Requirements of the Pharmaceutical Industry
- Strict Cleanliness and Aseptic Requirements: The pharmaceutical industry has extremely high requirements for the cleanliness and asepticity of ultra-high purity diaphragm valves. The valves need to go through strict cleaning, disinfection, and sterilization treatments to ensure that no microbial and particulate contaminants are introduced during the pharmaceutical production process. The surface roughness of the valve, the biocompatibility of the material, and the sealing performance all need to meet relevant regulations and standards.
- Corrosion Resistance and Chemical Resistance: In the pharmaceutical process, various corrosive chemicals and solvents will be encountered. Ultra-high purity diaphragm valves need to have excellent corrosion resistance and be able to operate stably for a long time in these media without problems such as corrosion, deformation, or leakage, to ensure the safety and stability of pharmaceutical production.
- Traceability and Verification Requirements: In order to ensure the reliability and traceability of drug quality, the pharmaceutical industry requires detailed records and verification documents for the production, installation, use, and maintenance processes of ultra-high purity diaphragm valves. Information such as the source of the valve materials, the production process, and the quality inspection report all need to be traceable, so that the cause can be found in a timely manner and corresponding measures can be taken when problems occur.
II. Special Requirements of the Food and Beverage Industry
- Food Safety and Hygiene Standards: The food and beverage industry has strict requirements for the food safety and hygiene standards of ultra-high purity diaphragm valves. The materials of the valves must meet food-grade standards, be non-toxic, odorless, and pollution-free, and will not have any adverse effects on food and beverages. The structural design of the valve should be easy to clean and disinfect to avoid the residue of food debris and microorganisms.
- Wear Resistance and Fatigue Resistance: In the food and beverage production process, the valve needs to be opened and closed frequently and withstand certain mechanical stress and fluid impact. Therefore, ultra-high purity diaphragm valves need to have good wear resistance and fatigue resistance, be able to maintain stable performance and reliable sealing effects during long-term use, and reduce the frequency of equipment maintenance and replacement.
- Flow Stability and Precise Control: The food and beverage production has high requirements for the flow stability and precise control of the fluid to ensure the consistency of product quality and taste. Ultra-high purity diaphragm valves need to be able to accurately control the flow of the fluid and maintain the stability of the flow under different working conditions to meet the requirements of the food and beverage production process.
III. Special Requirements of the Liquid Crystal Display and Organic Light Emitting Diode Manufacturing Industry
- High-Precision Flow Control: The LCD and OLED manufacturing processes have extremely high requirements for the flow control precision of the fluid. Ultra-high purity diaphragm valves need to have sub-micron-level flow control capabilities to ensure the precise transportation of various chemical reagents and gases during the panel manufacturing process, achieving high-precision pattern formation and film growth, and improving the performance and production efficiency of the panel.
- Fast Response Speed: In the LCD and OLED manufacturing process, the process rhythm is relatively fast, and ultra-high purity diaphragm valves need to have a fast response speed, be able to achieve the opening, closing, and flow regulation of the fluid in a short time, meet the requirements of high-speed production on the production line, and avoid affecting the production efficiency and product quality due to the slow response of the valve.
- Low Particle Release and Anti-Static Performance: LCD and OLED panels are very sensitive to particulate contaminants. Even tiny particles may cause defects in the panel. Therefore, ultra-high purity diaphragm valves need to have extremely low particle release characteristics and good anti-static performance to prevent the adsorption of particles due to static electricity and cause contamination to the panel, ensuring the high-quality production of the panel.
IV. Special Requirements of the Solar Photovoltaic Industry
- Resistance to Harsh Environments and High Temperature Performance: The production environment of solar photovoltaic is relatively harsh. Ultra-high purity diaphragm valves need to have good resistance to harsh environments and be able to operate stably for a long time under conditions such as high temperature, high humidity, and strong ultraviolet rays. In some high-temperature process links, such as the diffusion and sintering processes, the valve needs to withstand high temperatures. Therefore, it needs to have high-temperature resistance to ensure that the materials and sealing performance of the valve are not affected.
- Large Flow and High Pressure Control: In the solar photovoltaic production process, sometimes a large amount of gas and liquid need to be transported, and high pressure will be generated in some process links. Ultra-high purity diaphragm valves need to have large flow and high pressure control capabilities to meet the requirements of fluid transportation and control in the production process and ensure the smooth progress of production.
- Cost-Effectiveness: The solar photovoltaic industry is a cost-sensitive industry. On the premise of meeting the performance requirements, ultra-high purity diaphragm valves need to have high cost-effectiveness. The design and manufacture of the valve should consider reducing costs and at the same time improve the reliability and service life of the product to reduce the total cost of solar photovoltaic production.
V. Special Requirements of the Medical Diagnosis and Biological Analysis Industry
- Biocompatibility and Low Adsorption: The medical diagnosis and biological analysis industry requires that the materials of ultra-high purity diaphragm valves have good biocompatibility, will not have any adverse effects on biological samples, and at the same time have low adsorption, avoiding the adsorption and residue of biological molecules on the surface of the valve, and ensuring the integrity of biological samples and the accuracy of detection results.
- Micro Flow Control: In biological analysis and medical diagnosis, trace amounts of biological samples and reagents often need to be processed. Ultra-high purity diaphragm valves need to have high-precision micro flow control capabilities, be able to accurately transport and distribute microliter-level or even nanoliter-level liquids, and meet the requirements of trace liquid operations in biological experiments and diagnoses.
- Easy Integration and Automatic Control: With the development of medical diagnosis and biological analysis technologies, more and more equipment needs to achieve automation and integration. Ultra-high purity diaphragm valves need to be easy to integrate with other equipment and be able to achieve remote monitoring and precise control through an automatic control system, improving experimental efficiency and the accuracy of detection.
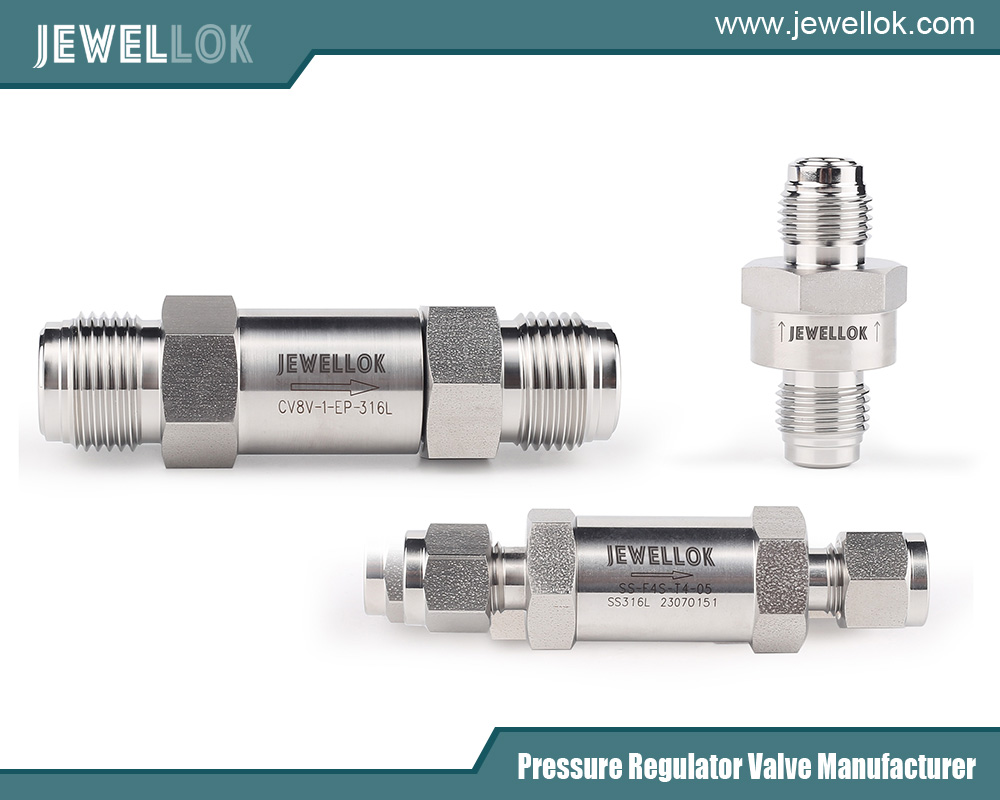
Conclusion
As a key fluid control device, ultra-high purity diaphragm valves have a wide range of important applications in many fields with extremely high purity requirements, such as the pharmaceutical, food and beverage, liquid crystal display and organic light emitting diode manufacturing, solar photovoltaic, and medical diagnosis and biological analysis industries, in addition to semiconductor manufacturing. Different fields put forward their own unique requirements for ultra-high purity diaphragm valves in terms of cleanliness, corrosion resistance, flow control precision, response speed, etc., according to their own process characteristics and requirements. With the continuous development and technological progress.
For more about ultra high purity diaphragm valves: key applications and developments in high-purity fields, you can pay a visit to Jewellok at https://www.jewellok.com/ for more info.
Recent Posts
Best Top 10 Specialty Gas Regulators Suppliers In Thailand
Best Top 10 Specialty Gas Regulators Manufacturers In India
Can Industrial Gas Regulators Be Used In Laboratories?
Tags
Recommended Products
-
765LR Reducing Tee | Stainless Steel 316 High Purity Butt Weld Fittings Metal Face Seal For Welding Pipe Fitting Reducing Tee
-
764L Stainless Steel Union Tee High Purity Fitting Union Tee Reducing Tubing Connection
-
768L Stainless Steel Male Tube Butt Weld Connector | Clean Weld Fittings And Ultra-High Purity Fittings
-
High Purity Configurable Systems VMB Valve Manifold Box JW-200-VMB-C & JW-100-VMB-C
-
763L Stainless Steel High Purity Pressure Reducing Union Fittings And Tubing Pressure Reducing Valve Adjustment
-
Stainless Steel High Purity High Temperature Pneumatic Actuated Ball Valves JBV2 Series
-
Line And Panel Mounting Adjustable Low Pressure Propane And Nitrogen Pressure Regulator JSR-3L & JSR-3LP Series
-
774L Stainless Steel UHP Fittings Butt Weld Bulkhead Union For High Flow Special Gas Fluid