Blog
Jewellok is a professional pressure regulator and valve manufacturer and supplier.
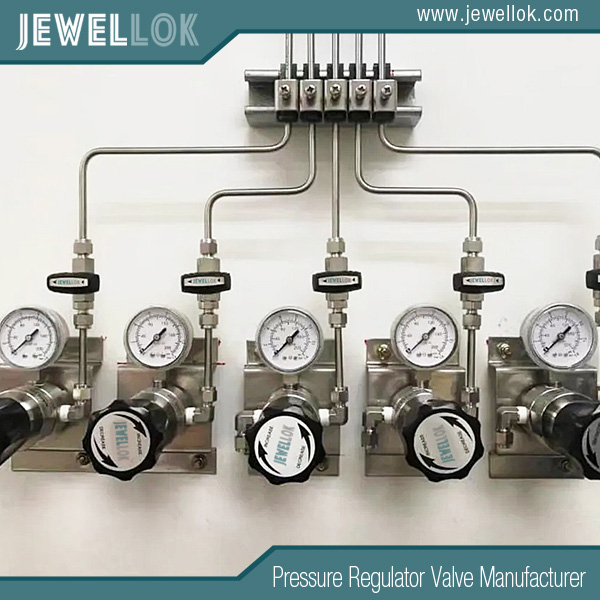
Types Of High Purity Pressure Reducing Valves Used In Semiconductor Manufacturing
- Pressure Regulator Valve Manufacturer
- China Pressure Regulator Manufacturers, Gas Pressure Reducing Valve, High purity gas regulator Manufacturer, High Purity L-Type Pressure Reducing Valve, High Purity Pressure Reducing Regulators, high purity pressure reducing valves manufacturer, high purity pressure reducing valves manufacturer in china, High-purity Pressure Reducing Regulator, Pressure Reducing Valve, Pressure Reducing Valve China, PRV Valve Manufacturer India, Reverse Osmosis Pressure Reducing Valve, Stainless Steel High Purity Line Pressure Regs
- No Comments
Types Of High Purity Pressure Reducing Valves Used In Semiconductor Manufacturing
Introduction
Semiconductor manufacturing is a highly precise and controlled process that demands the utmost purity and reliability in every component of the production system. From the deposition of thin films to the etching of intricate circuits, the integrity of the final product hinges on maintaining a contamination-free environment. One critical aspect of this process is the management of gas and fluid pressures, which is where high purity pressure reducing valves (PRVs) come into play. These specialized valves regulate the pressure of gases and liquids while ensuring that no contaminants are introduced into the system—a non-negotiable requirement in the semiconductor industry.
High purity PRVs are designed to handle ultra-pure gases like nitrogen, argon, hydrogen, and silane, as well as corrosive or reactive chemicals used in processes such as chemical vapor deposition (CVD), atomic layer deposition (ALD), and wafer cleaning. Unlike standard industrial valves, high purity PRVs must meet stringent standards for cleanliness, material compatibility, and leak-tight performance. This article explores the primary types of high purity pressure reducing valves used in semiconductor manufacturing, their design features, and their specific applications in this cutting-edge industry.
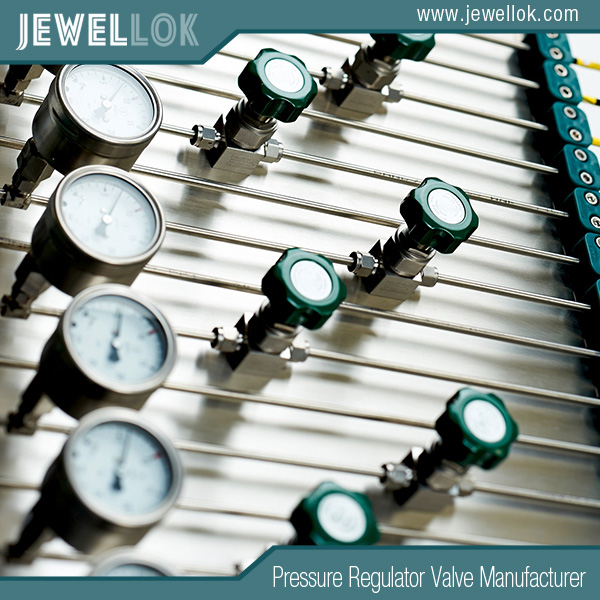
The Role of Pressure Reducing Valves in Semiconductor Manufacturing
Before delving into the types of high purity PRVs, it’s worth understanding their critical role in semiconductor fabrication. Semiconductor processes often require gases to be delivered at precise pressures—sometimes as low as a few millibars or as high as several bars—depending on the stage of production. For example, during CVD, gases must be supplied at a stable, low pressure to ensure uniform film deposition, while high-pressure gas delivery might be needed for purging systems or driving pneumatic actuators.
A pressure reducing valve reduces the pressure from a high-pressure source (e.g., a gas cylinder or bulk supply system) to a lower, controlled output pressure suitable for downstream processes. In semiconductor manufacturing, these valves must also prevent contamination from particulates, outgassing, or chemical reactions between the valve materials and process media. This necessitates the use of high purity designs featuring electropolished stainless steel, minimal dead volume, and advanced sealing technologies.
Types of High Purity Pressure Reducing Valves
High purity PRVs come in various designs, each tailored to specific needs within semiconductor manufacturing. Below are the main types commonly employed in the industry:
1. Diaphragm-Type Pressure Reducing Valves
Diaphragm-type PRVs are among the most widely used in semiconductor manufacturing due to their reliability, precision, and contamination-resistant design. These valves use a flexible diaphragm—typically made of stainless steel or a high-purity elastomer like PTFE—to sense and regulate downstream pressure.
Design Features:
-
Materials: The wetted surfaces (those in contact with the process gas) are typically made of 316L stainless steel with an electropolished finish to achieve a surface roughness as low as 5 Ra (microinches). This minimizes particle generation and facilitates cleaning.
-
Sealing: The diaphragm itself acts as a seal, eliminating the need for dynamic O-rings or packing that could wear and introduce contaminants.
-
Low Dead Volume: The design minimizes internal cavities where gas could stagnate, reducing the risk of contamination buildup.
Applications: Diaphragm PRVs are ideal for delivering ultra-high purity (UHP) gases such as nitrogen, oxygen, and argon to process chambers. They are commonly found in gas delivery systems for CVD, physical vapor deposition (PVD), and dry etching processes, where consistent low-pressure output is critical.
Advantages:
-
High sensitivity to pressure changes, ensuring precise regulation.
-
Minimal risk of leakage or contamination due to the all-metal or inert construction.
-
Long service life in cleanroom environments.
Limitations:
-
Limited flow capacity compared to other designs, making them less suitable for high-flow applications.
2. Bellows-Type Pressure Reducing Valves
Bellows-type PRVs utilize a metal bellows—often made of stainless steel or Hastelloy—as the pressure-sensing element instead of a diaphragm. This design is particularly suited for applications requiring higher durability and resistance to corrosive gases.
Design Features:
-
Bellows Construction: The bellows is a flexible, accordion-like structure that expands or contracts in response to pressure changes, controlling the valve’s opening.
-
Corrosion Resistance: Materials like Hastelloy or Inconel are used for compatibility with aggressive gases such as chlorine or hydrogen chloride.
-
Leak-Tight Performance: The welded bellows design ensures zero leakage to the atmosphere, a critical feature in handling toxic or reactive gases.
Applications: These valves are prevalent in processes involving corrosive or reactive gases, such as plasma etching and ALD. They are also used in gas delivery systems for bulk specialty gases where absolute containment is required.
Advantages:
-
Superior resistance to chemical attack, extending valve lifespan in harsh environments.
-
High reliability in maintaining pressure under fluctuating conditions.
-
Suitable for both low- and medium-pressure applications.
Limitations:
-
Higher cost due to complex construction and exotic materials.
-
Slightly lower precision compared to diaphragm-type valves in ultra-low pressure ranges.
3. Piston-Type Pressure Reducing Valves
Piston-type PRVs use a piston mechanism to regulate pressure, offering a robust alternative for high-flow or high-pressure applications. While less common in ultra-high purity systems, they are still employed in specific semiconductor processes where durability and flow capacity take precedence.
Design Features:
-
Piston Mechanism: A piston moves within a cylinder to adjust the valve opening based on downstream pressure feedback.
-
Materials: Wetted parts are typically 316L stainless steel, though seals may include high-purity elastomers like Viton or Kalrez for compatibility with certain gases.
-
Rugged Design: Built to withstand higher pressures and mechanical stress.
Applications: Piston-type PRVs are used in upstream gas delivery systems, such as reducing pressure from high-pressure cylinders (e.g., 200 bar) to a more manageable level (e.g., 10 bar) before finer regulation by diaphragm or bellows valves. They are also found in facilities handling bulk gas supplies or in purge systems requiring high flow rates.
Advantages:
-
High flow capacity, making them suitable for large-scale gas distribution.
-
Durable construction for long-term use in demanding conditions.
-
Cost-effective for applications where ultra-high purity is less critical.
Limitations:
-
Potential for contamination from seals or lubricants if not designed for UHP standards.
-
Less precise regulation at very low pressures.
4. Spring-Loaded Pressure Reducing Valves
Spring-loaded PRVs are a simpler, mechanically operated design where a spring applies force to a valve seat, balancing against downstream pressure to maintain a setpoint. While not as sophisticated as diaphragm or bellows valves, they are still used in certain high purity applications.
Design Features:
-
Spring Mechanism: A preloaded spring determines the output pressure, adjustable via a set screw or knob.
-
Compact Size: Smaller footprint compared to other types, ideal for space-constrained systems.
-
High Purity Variants: UHP versions use electropolished stainless steel and minimize elastomeric components.
Applications: These valves are often used in point-of-use applications, such as regulating pressure at the inlet of a process tool or in secondary gas lines for non-critical processes like inert gas blanketing.
Advantages:
-
Simplicity and ease of maintenance.
-
Cost-effective for less demanding applications.
-
Quick response to pressure changes.
Limitations:
-
Limited precision compared to diaphragm or bellows designs.
-
Potential for wear in the spring or seat, requiring periodic replacement.
5. Electronic Pressure Reducing Valves
The advent of smart manufacturing has introduced electronic PRVs, which integrate sensors and actuators for real-time pressure control. These advanced valves represent the cutting edge of pressure regulation in semiconductor fabrication.
Design Features:
-
Closed-Loop Control: A pressure sensor monitors downstream pressure and adjusts the valve via an electronic actuator, often with PID (proportional-integral-derivative) control algorithms.
-
Digital Integration: Compatible with fab-wide automation systems for remote monitoring and adjustment.
-
High Purity Materials: Retains the same UHP construction as mechanical valves (e.g., 316L stainless steel, minimal dead volume).
Applications: Electronic PRVs are used in next-generation processes requiring dynamic pressure adjustments, such as advanced lithography or multi-step deposition sequences. They are also critical in R&D environments where process parameters are frequently optimized.
Advantages:
-
Unmatched precision and adaptability to changing conditions.
-
Integration with Industry 4.0 systems for data logging and predictive maintenance.
-
Reduced human intervention in cleanroom settings.
Limitations:
-
Higher cost and complexity, requiring skilled technicians for setup and maintenance.
-
Dependence on electrical power and control systems.
Material and Cleanliness Standards
Regardless of type, all high purity PRVs in semiconductor manufacturing must adhere to rigorous standards. The SEMI (Semiconductor Equipment and Materials International) guidelines, such as SEMI F20 for material purity and SEMI F19 for valve performance, dictate specifications for surface finish, leak rates, and particle generation. Valves are typically cleaned and assembled in ISO Class 5 cleanrooms, double-bagged, and certified free of hydrocarbons, moisture, and particulates.
Selection Considerations
Choosing the right PRV depends on several factors:
-
Process Media: Corrosive gases like HF require bellows-type valves with Hastelloy, while inert gases like N2 suit diaphragm designs.
-
Pressure Range: Ultra-low pressure applications favor diaphragm valves, while high-flow needs may call for piston types.
-
Flow Rate: Electronic or piston valves excel in high-flow scenarios.
-
Cost vs. Performance: Spring-loaded valves offer a budget-friendly option, while electronic valves provide premium control.
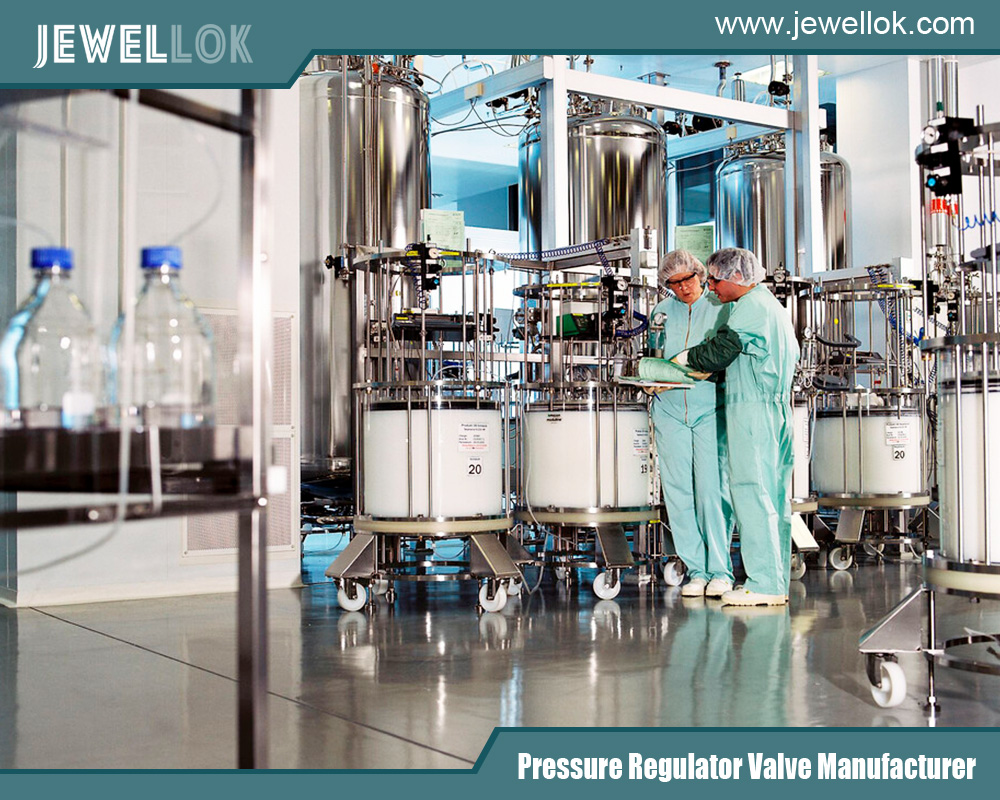
Conclusion
High purity pressure reducing valves are indispensable in semiconductor manufacturing, ensuring that gases and fluids are delivered with precision and purity. From the versatile diaphragm-type to the robust bellows and cutting-edge electronic designs, each valve type serves a unique purpose in the complex ecosystem of a semiconductor fab. As the industry pushes toward smaller nodes and more intricate processes, the evolution of PRVs will continue to play a pivotal role in enabling innovation. By balancing material science, engineering precision, and contamination control, these valves uphold the stringent demands of an industry that shapes the modern world.
For more about types of high purity pressure reducing valves use in semiconductor manufacturing, you can pay a visit to Jewellok at https://www.jewellok.com/product-category/ultra-high-purity-regulators/ for more info.
Recent Posts
Tags
1 1 2 gas pressure regulator
1 2 gas regulator
1/2 gas pressure regulator
2 inch irrigation solenoid valve
2 inch irrigation valve
6mm compression fitting
6mm equivalent
8mm compression fitting
adjustable low pressure propane regulator
adjustable propane pressure regulator
adjustable propane regulator
adjusting propane regulator
air compressor non return valve
argon hose fitting
diaphragm suppliers
fluid systems components
gases used in semiconductor manufacturing
gas pipeline valve
gas pipeline valves
gas regulator
high purity valves
how a pressure regulator works
how does a needle valve work
how does pressure regulator work
how often should pressure relief valves be replaced
how solenoid valves work
humming propane regulator
irrigation timer valve
low pressure regulator
pressure gauge manufacturers
pressure regulator
pressure regulator valve leaking
regulator valve alibaba international market
relief vs safety valve
safety relief valve vs pressure relief valve
safety relief valve vs safety valve
safety valve and relief valve
safety valve and relief valve difference
safety valve vs pressure relief valve
single stage pressure regulator
stainless pressure regulator
stainless steel 1/4 in. pressure gauge fitting - 3/8 qc
two stage pressure regulator
valve timer water
what is a gas pressure regulator
Recommended Products
-
772L Male Branch Tee | Stainless Steel High-Purity Tube Fitting Male Branch Tee
-
Semi Automatic Gas Cabinet Gas Panels High Purity Gas Delivery Systems JW-200-GC
-
Line And Panel Mounting Adjustable Low Pressure Propane And Nitrogen Pressure Regulator JSR-3L & JSR-3LP Series
-
Ultra High Purity Pressure Gauge For Laboratory And Semiconductor JR Series
-
FT-BOX JW-FTB-C Valve Manifold Panels And Boxes With High Purity Configurable Systems
-
767LT Reducer Pressure Reducing Valve Adjustment High purity Pressure Reducing Union Fittings And Tubing
-
765L Stainless Steel Union Elbow Reducing High Purity Fitting Tubing Extension Tubing Connection
-
Clean Connection Cabinet JW-300-CCB Valve Manifold Box And Control Valve Box