Blog
Jewellok is a professional pressure regulator and valve manufacturer and supplier.
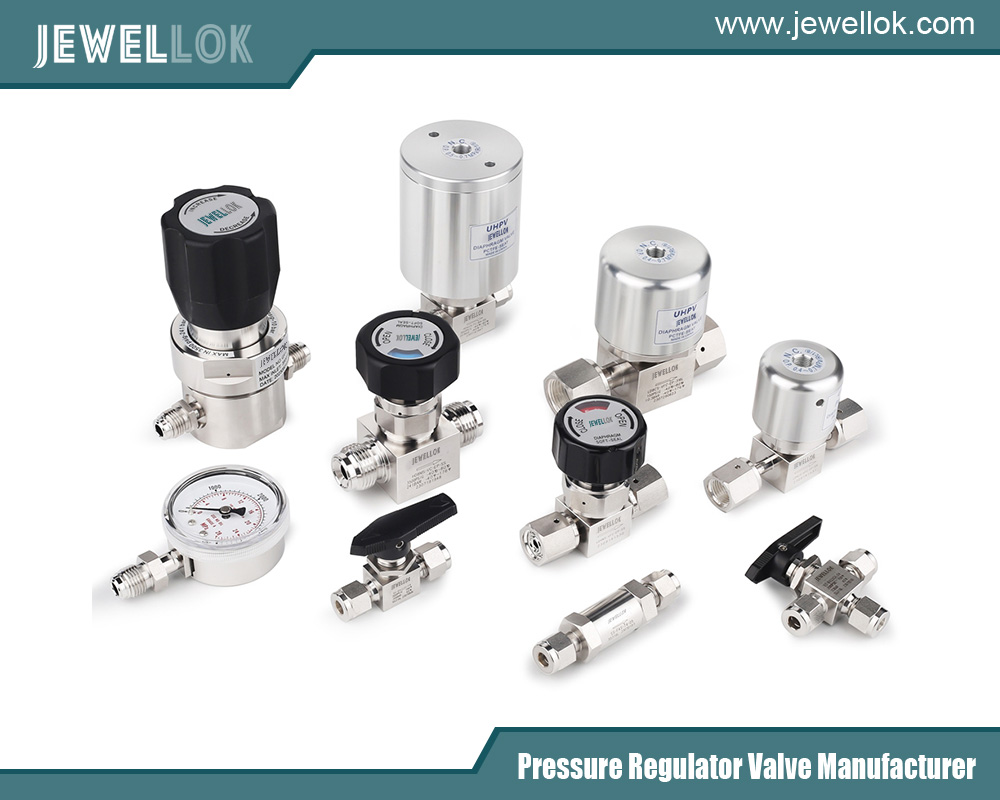
Types Of Gas Delivery Systems In The Semiconductor Industry
- Pressure Regulator Valve Manufacturer
- China Customized Medical Gas System Manufacturers, China Gas Panels Manufacturers, China Gas System Manufacturers, Fuel Gas Supply System, Gas Control Systems in Semiconductors, Gas Delivery Cabinet Systems, gas delivery system in semiconductor, gas panel semiconductor, High Purity Gas Delivery Equipment, Integrated Central Medical Gas Supply System, integrated gas supply system, integrated gas system, integrated gas system china supplier, Integrated Gas System in Semiconductor, Semiconductor Gas Delivery Systems, Semiconductor Gas Storage and Delivery, UHP Gas Distribution Panel, Ultra-High-Purity Gas Delivery Systems
- No Comments
Types Of Gas Delivery Systems In The Semiconductor Industry
Introduction
The semiconductor industry is the backbone of modern electronics, producing the microchips that power everything from smartphones to spacecraft. A critical aspect of semiconductor manufacturing is the precise delivery of gases, which are used in processes like deposition, etching, and doping. Gas delivery systems (GDS) ensure that these gases—often toxic, flammable, or highly reactive—are transported safely, accurately, and efficiently to the processing equipment. The complexity of these systems stems from the need for ultra-high purity, precise flow control, and stringent safety standards.
This article explores the various types of gas delivery systems employed in the semiconductor industry, their components, applications, and the technological advancements driving their evolution. From bulk gas systems to point-of-use delivery, each type serves a unique role in meeting the demands of cutting-edge fabrication processes. As the industry pushes toward smaller nodes and higher performance, understanding these systems becomes essential for engineers, researchers, and manufacturers alike.
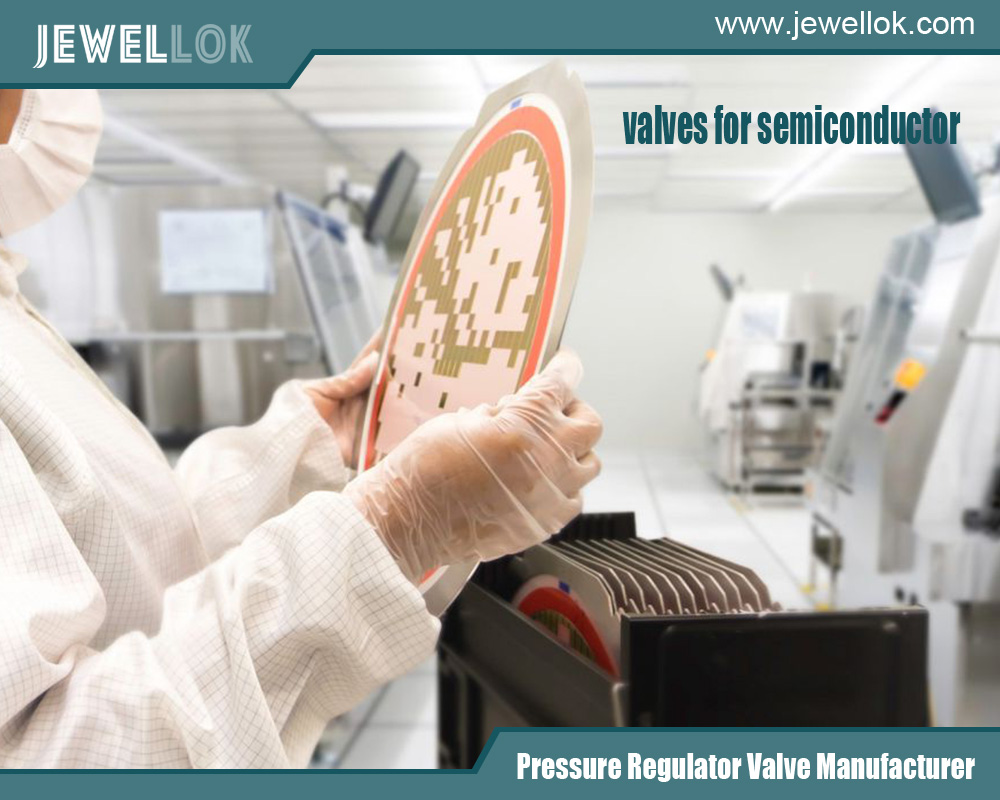
Section 1: Overview of Gas Delivery Systems
Gas delivery systems in the semiconductor industry are engineered to transport process gases from their source—such as cylinders, bulk storage tanks, or on-site generators—to the point of use within a fabrication facility (fab). These systems must maintain gas purity at parts-per-billion (ppb) levels, as even trace contaminants can compromise wafer quality. Additionally, they must regulate pressure, flow rate, and temperature while adhering to strict safety protocols due to the hazardous nature of many gases, such as silane (SiH₄), arsine (AsH₃), and chlorine (Cl₂).
A typical GDS consists of several key components:
Gas Source: Cylinders, bulk tanks, or generators.
Piping and Valves: Stainless steel tubing and high-purity valves to prevent leaks and contamination.
Regulators and Flow Controllers: Devices to maintain consistent pressure and flow.
Purifiers: Filters to remove impurities like moisture or particulates.
Monitoring Systems: Sensors for leak detection, pressure monitoring, and gas composition analysis.
The design of a GDS depends on the type of gas, its intended application, and the scale of the operation. Broadly, gas delivery systems can be categorized into bulk gas delivery systems, specialty gas delivery systems, and point-of-use systems, each tailored to specific needs within the semiconductor manufacturing process.
Section 2: Types of Gas Delivery Systems
This section delves into the primary types of gas delivery systems, their configurations, and their roles in semiconductor fabrication.
2.1 Bulk Gas Delivery System
Bulk gas delivery systems are designed to supply large volumes of commonly used gases, such as nitrogen (N₂), oxygen (O₂), argon (Ar), and hydrogen (H₂), which are essential for processes like chemical vapor deposition (CVD) and wafer cleaning. These systems typically involve large-scale storage solutions, such as cryogenic tanks or high-pressure vessels, located outside the fab. The gas is then distributed through a network of stainless steel piping to various tools within the facility.
Components: Bulk systems include storage tanks, vaporizers (for liquefied gases), pressure regulators, and extensive piping infrastructure. Advanced systems may incorporate on-site gas generators, such as pressure swing adsorption (PSA) units for nitrogen.
Advantages: High capacity, cost-efficiency for high-consumption gases, and reduced need for frequent cylinder changes.
Challenges: Maintaining purity over long distances, managing thermal expansion in piping, and ensuring uninterrupted supply during maintenance.
Applications: Inert gases like nitrogen are used for purging and creating controlled atmospheres, while oxygen is critical for oxidation processes.
Bulk systems are the backbone of a fab’s gas infrastructure, often integrated with automated control systems to monitor supply levels and detect anomalies in real time.
2.2 Specialty Gas Delivery Systems
Specialty gas delivery systems handle low-volume, high-purity gases required for specific fabrication steps, such as doping or plasma etching. These gases—e.g., phosphine (PH₃), boron trifluoride (BF₃), or tetrafluoromethane (CF₄)—are typically stored in high-pressure cylinders or small tanks and delivered through dedicated lines to avoid cross-contamination.
Components: Cylinder cabinets with automatic switchover manifolds, mass flow controllers (MFCs), and point-of-use purifiers. These systems often use double-walled coaxial piping for added safety.
Advantages: Precision in delivering small quantities, flexibility for exotic gases, and enhanced safety features for hazardous materials.
Challenges: Higher cost per unit volume, complex handling procedures, and the need for frequent cylinder replacement.
Applications: Dopant gases like arsine are used to introduce impurities into silicon wafers, while fluorinated gases are employed in reactive ion etching (RIE).
Specialty gas systems are critical for processes requiring exact chemical compositions, and their design prioritizes safety and purity over volume.
2.3 Point-of-Use Gas Delivery Systems
Point-of-use (POU) gas delivery systems provide localized control and purification immediately before the gas enters the processing tool. These systems are often integrated into the equipment itself or installed nearby, ensuring that gas quality is optimized at the moment of use.
Components: Compact MFCs, inline purifiers, pressure transducers, and shut-off valves. POU systems may also include gas mixing modules to blend multiple gases on-site.
Advantages: Enhanced purity at the tool, reduced contamination risk from long piping runs, and precise flow adjustments tailored to specific processes.
Challenges: Limited capacity, higher maintenance frequency, and the need for compatibility with diverse tool requirements.
Applications: POU systems are used in atomic layer deposition (ALD) for precise precursor delivery or in plasma-enhanced CVD (PECVD) for reactive gas mixtures.
POU systems bridge the gap between centralized delivery and tool-specific needs, offering a final layer of control in the gas supply chain.
Section 3: Technological Advancements and Trends
The evolution of gas delivery systems reflects the semiconductor industry’s push toward smaller feature sizes, higher yields, and sustainability. Key advancements include:
Smart Monitoring: IoT-enabled sensors and AI-driven analytics for predictive maintenance and real-time leak detection.
Ultra-High Purity (UHP) Materials: Adoption of electropolished stainless steel and advanced coatings to minimize outgassing and particle generation.
On-Site Gas Generation: Technologies like membrane separation and electrolysis reduce reliance on external suppliers and improve supply chain resilience.
Sustainability: Efforts to recycle gases like argon or capture emissions from processes involving greenhouse gases (e.g., CF₄).
These innovations enhance efficiency, reduce costs, and align with environmental regulations, ensuring that gas delivery systems keep pace with the demands of 3nm and beyond fabrication nodes.
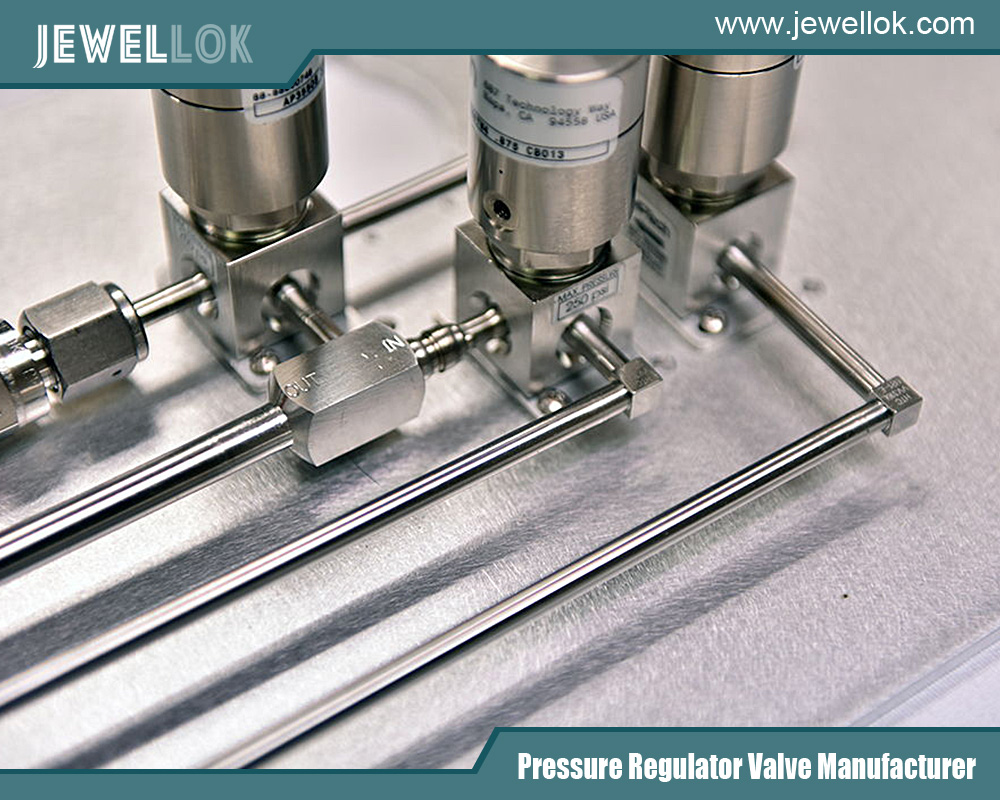
Conclusion
Gas delivery systems are a cornerstone of semiconductor manufacturing, enabling the precise and safe handling of gases that drive critical processes. Bulk systems provide the volume needed for foundational operations, specialty systems offer precision for niche applications, and point-of-use systems ensure quality at the tool level. Together, they form an integrated network that balances scale, safety, and performance.
As the industry advances, gas delivery systems will continue to evolve, incorporating smarter technologies and greener practices to meet the challenges of next-generation chip production. For engineers and manufacturers, understanding these systems is key to optimizing fab operations and maintaining a competitive edge in a rapidly changing landscape.
For more about the types of gas delivery systems in the semiconductor industry, you can pay a visit to Jewellok at https://www.jewellok.com/semiconductor/ for more info.
Recent Posts
Tags
Recommended Products
-
VMB Valve Manifold Panels And Boxes High Purity Configurable Systems JW-200-VMB & JW-100-VMB
-
DPR1 Ultra High Purity Two Stage Dual Stage Pressure Reducing Regulator Semiconductor Grade Regulators
-
High Pressure High-Purity Welded Check Valves And Low Cracking Pressure Check Valve JCV1 Series
-
High Purity High Pressure Stainless Steel Needle Valve Natural Gas Flow Control Valve JNV Series
-
764L Stainless Steel Union Tee High Purity Fitting Union Tee Reducing Tubing Connection
-
JR1300 Series Ultra High Purity Single Stage Regulator High Flow Line Regulator For Ultra High Purity Intermediate Flow
-
767LT Reducer Pressure Reducing Valve Adjustment High purity Pressure Reducing Union Fittings And Tubing
-
771L Male Run Tee | Stainless Steel High Quality High Purity Male Run Tee Branch Tee Pipe Fittings