Blog
Jewellok is a professional pressure regulator and valve manufacturer and supplier.
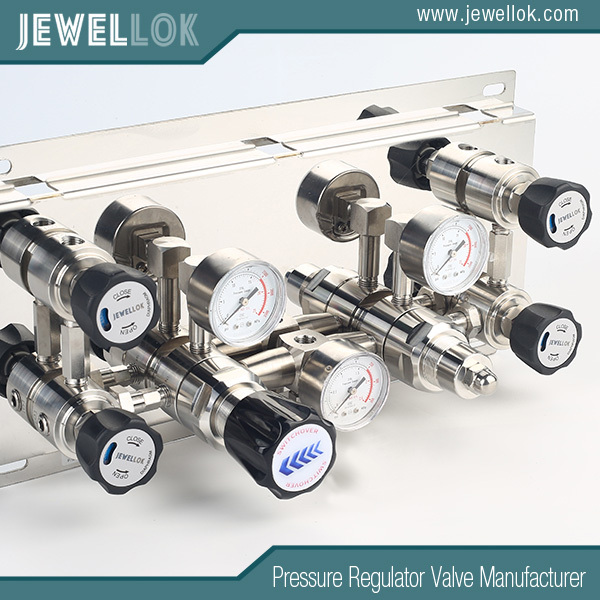
The Uses Of Specialty Gas Line Valves And Pressure Regulators
- Pressure Regulator Valve Manufacturer
- Best specialty gas valves manufacturers china, China Gas Valve Manufacturers, China Industrial Gas Valve Manufacturer, China specialty gas valves manufacturers, Gas Butt Fusion Ball Valves, specialty gas line valves, specialty gas line valves and pressure regulators, Specialty gas line valves manufacturers, Specialty Gas Valves, Specialty Gas Valves and Regulators, Specialty gas valves manufacturers, Specialty gas valves manufacturers china
- No Comments
The Uses Of Specialty Gas Line Valves And Pressure Regulators
Introduction
Specialty gases play an indispensable role in numerous industries, ranging from healthcare and manufacturing to scientific research and environmental monitoring. Unlike common gases such as air or natural gas, specialty gases are high-purity gases, gas mixtures, or reactive substances tailored for specific applications. These gases demand meticulous control over their purity, pressure, and flow rates to ensure safety and efficacy in their use. Whether it’s oxygen sustaining a patient in a hospital, argon shielding a weld in a factory, or a calibration gas ensuring the accuracy of an environmental sensor, the handling of specialty gases requires specialized equipment.
At the core of this equipment are specialty gas line valves and pressure regulators. These components work together to manage the flow and pressure of gases, delivering them precisely and safely to their intended destinations. Specialty gas line valves regulate the movement of gas through pipelines or systems, while pressure regulators maintain a consistent output pressure despite fluctuations in the supply. Their importance cannot be overstated—they enable industries to harness the unique properties of specialty gases while mitigating risks associated with their handling.
This article delves into the uses of specialty gas line valves and pressure regulators, exploring their functions, types, and the diverse industries that depend on them. By examining these components in detail, we can better appreciate their critical role in advancing technology, ensuring safety, and enhancing efficiency across various sectors.
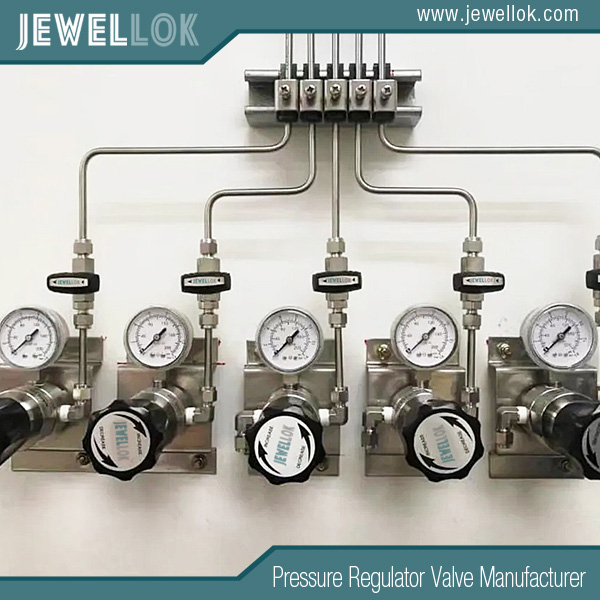
To understand their significance, let’s first examine specialty gas line valves in more detail.
Section 1: Specialty Gas Line Valves
Definition and Purpose
Specialty gas line valves are engineered to control the flow of specialty gases through pipelines, cylinders, or delivery systems. These valves are far more advanced than standard valves used for everyday gases, as they must accommodate the distinct characteristics of specialty gases—such as high purity, reactivity, or toxicity. Their primary purpose is to start, stop, or adjust the flow of gas with precision and reliability, ensuring that the gas reaches its point of use in the desired quantity and condition.
Types of Valves
Several types of valves are employed in specialty gas applications, each selected based on the gas properties and system requirements:
Diaphragm Valves: Widely used for high-purity gases, diaphragm valves feature a flexible diaphragm that seals the gas from the valve’s internal mechanisms. This design minimizes contamination risks, making them ideal for applications like semiconductor manufacturing where even trace impurities can compromise results.
Bellows Valves: These are preferred for toxic or hazardous gases. The bellows—a flexible, accordion-like structure—encloses the valve stem, preventing leaks and ensuring safety in environments where gas escape could pose significant risks.
Needle Valves: Common in laboratory settings, needle valves allow for fine-tuned flow control. Their slender, tapered design enables precise adjustments, making them suitable for experiments requiring exact gas delivery rates.
Ball Valves: While simpler in design, ball valves provide quick on/off control. They are less precise than needle valves and may not be suitable for all specialty gases due to potential leakage, but they are effective in systems requiring rapid shutoff.
Key Features
Specialty gas line valves differ from standard valves in their construction and performance. They are often made from materials like stainless steel, brass, or specialized alloys that resist corrosion and maintain gas purity. Material selection is critical—valves must not react with the gas they control, as this could lead to contamination or equipment failure. For instance, a valve handling a corrosive gas like chlorine might require a corrosion-resistant alloy, while one managing ultra-pure helium might use stainless steel to preserve purity.
In essence, specialty gas line valves are the gatekeepers of gas delivery systems, ensuring that specialty gases are transported accurately and safely. Their tailored design and robust materials make them indispensable in any specialty gas application.
Having explored the types and functions of valves, we now turn to pressure regulators, which work in tandem with valves to control gas delivery.
Section 2: Pressure Regulators for Specialty Gases
Definition and Function
Pressure regulators are devices that reduce the pressure of a gas from a high-pressure source—such as a cylinder or tank—to a lower, usable level. For specialty gases, their role extends beyond simple pressure reduction: they maintain a consistent output pressure, even when the input pressure fluctuates. This stability is crucial in applications where precise pressure is non-negotiable, such as delivering oxygen to a patient or supplying gas to a sensitive analytical instrument.
Types of Regulators
Pressure regulators for specialty gases come in various forms, each suited to specific needs:
Single-Stage Regulators: These reduce pressure in one step, making them suitable for systems with stable supply pressures. They are simpler and more compact but may allow slight output variations if the input pressure changes significantly.
Dual-Stage Regulators: Offering greater precision, dual-stage regulators reduce pressure in two steps. The first stage lowers the pressure to an intermediate level, and the second stage fine-tunes it to the desired output. This design ensures exceptional stability, making them ideal for high-purity or analytical applications.
High-Purity Regulators: Designed to prevent contamination, these regulators use metal-to-metal seals and materials that do not outgas or degrade. They are essential in industries like electronics manufacturing, where gas purity directly impacts product quality.
Corrosion-Resistant Regulators: For reactive or corrosive gases, regulators may be constructed from durable alloys or coated to withstand chemical interactions, ensuring longevity and safety.
Low-Pressure Regulators: Some applications, such as certain laboratory processes, require very low delivery pressures. These specialized regulators maintain stability at minimal levels, catering to niche requirements.
Specialized Features
Specialty gas pressure regulators often include features tailored to their unique applications. For instance, they may be designed for leak-tightness to prevent gas loss or contamination, or they might incorporate high-flow capabilities for industrial processes requiring large gas volumes. Their construction materials—typically stainless steel or brass—are chosen to match the gas’s properties, ensuring compatibility and durability.
In summary, pressure regulators are the backbone of pressure control in specialty gas systems. By delivering gas at a steady, precise pressure, they enable processes that depend on consistency and reliability, complementing the flow control provided by valves.
With a clear understanding of these components, let’s explore their practical applications across various industries.
Section 3: Applications in Various Industries
Specialty gas line valves and pressure regulators are employed in a wide array of sectors, each leveraging their capabilities to meet specific challenges. Below, we examine their uses in key industries.
Medical Industry
In healthcare, specialty gases like oxygen, nitrous oxide, and medical air are essential for patient care. These gases are distributed through hospital pipeline systems to operating rooms, intensive care units, and wards. Valves and regulators ensure precise delivery:
Oxygen Therapy: Oxygen must be supplied at controlled pressures to support patients with respiratory conditions without causing harm.
Anesthesia Delivery: Nitrous oxide and other anesthesia gases require exact flow rates and mixtures, managed by needle valves and dual-stage regulators, to maintain patient safety during surgery.
Medical Gas Pipelines: Diaphragm valves and high-purity regulators maintain gas integrity throughout complex distribution networks.
Manufacturing and Industrial Settings
Industries such as metal fabrication, chemical processing, and electronics rely heavily on specialty gases:
Welding and Cutting: Gases like argon, helium, and acetylene shield welds or fuel cutting torches. Ball valves provide quick shutoff, while regulators ensure consistent pressure for uniform results.
Semiconductor Manufacturing: Ultra-high purity gases (e.g., nitrogen, silane) are used to create microchips. Diaphragm valves and high-purity regulators prevent contamination, ensuring defect-free production.
Chemical Processing: Reactive gases like chlorine or ammonia require corrosion-resistant valves and regulators to maintain process efficiency and safety.
Research and Development
Laboratories and research facilities use specialty gases in analytical and experimental applications:
Gas Chromatography and Mass Spectrometry: Carrier gases (e.g., helium) and calibration mixtures demand precise delivery. Needle valves and dual-stage regulators provide the accuracy needed for reliable measurements.
Rare Gas Experiments: Research involving gases like xenon or krypton uses bellows valves to handle their reactivity or rarity safely.
Calibration Standards: High-purity regulators ensure that calibration gases maintain their integrity for instrument validation.
Environmental and Energy Sectors
These fields utilize specialty gases for monitoring and innovation:
Environmental Monitoring: Calibration gases (e.g., carbon dioxide, methane) are used to calibrate air quality sensors. Valves and regulators ensure accurate delivery for trustworthy data.
Hydrogen Fuel Cells: In the energy sector, hydrogen requires high-pressure regulators and robust valves to support clean energy generation.
Natural Gas Processing: Pressure regulators stabilize gas flow in refining processes, enhancing efficiency and safety.
Across these industries, specialty gas line valves and pressure regulators enable critical processes by delivering gases with precision and reliability. Their adaptability to diverse applications highlights their versatility and importance.
Next, we consider the technical and safety aspects that underpin their performance.
Section 4: Technical and Safety Considerations
The effectiveness of specialty gas line valves and pressure regulators hinges on careful design and adherence to safety standards. Several key factors must be addressed:
Material Compatibility
The materials used in these components must be compatible with the gas they handle. Incompatible materials can corrode, contaminate the gas, or fail under pressure. For example:
Stainless Steel: Durable and resistant, it’s ideal for inert and high-purity gases.
Brass: Suitable for many non-corrosive gases but unsuitable for reactive ones.
Special Alloys: Used for corrosive gases like hydrogen sulfide to prevent degradation.
Precision and Accuracy
Many specialty gas applications demand exact control over flow and pressure. Valves and regulators must offer fine adjustments and maintain stability. In semiconductor production, for instance, even minor pressure fluctuations can ruin a batch of chips, while in laboratories, precise flow rates ensure experimental reproducibility.
Safety Features
Safety is critical, especially with hazardous gases (e.g., flammable hydrogen or toxic carbon monoxide). Key safety features include:
Pressure Relief Valves: These release excess pressure to prevent system damage or explosions.
Burst Disks: Designed to rupture at a specific pressure, they act as a fail-safe mechanism.
Leak-Tight Designs: Welded connections and bellows seals minimize leak risks, protecting personnel and environments.
Standards and Maintenance
Compliance with industry standards—such as those from the Compressed Gas Association (CGA) or ISO—ensures reliability and safety. Regular maintenance and calibration are also vital. Over time, wear can compromise precision or sealing, necessitating routine inspections and servicing.
These considerations ensure that specialty gas line valves and pressure regulators perform optimally, safeguarding both processes and people.
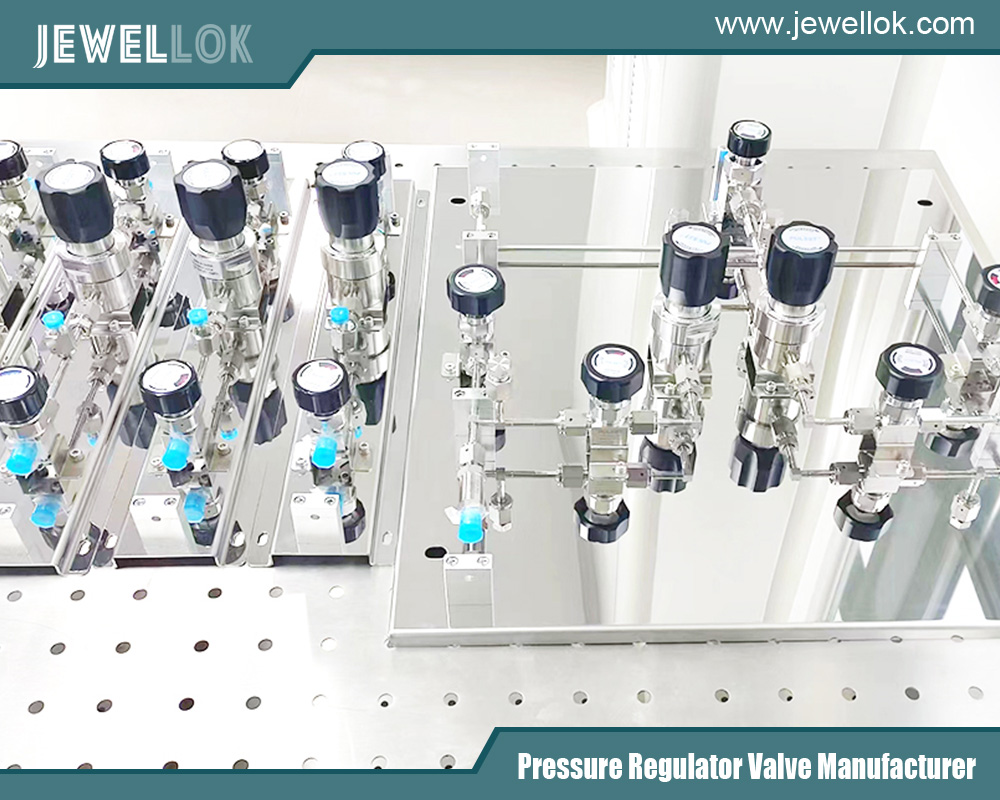
Conclusion
Specialty gas line valves and pressure regulators are unsung heroes in the world of specialty gases, enabling their safe and effective use across diverse industries. From delivering life-saving oxygen in hospitals to supporting cutting-edge research and powering sustainable energy solutions, these components are integral to modern technology and innovation. Their design—emphasizing precision, compatibility, and safety—addresses the unique challenges of handling high-purity, reactive, or hazardous gases.
As industries evolve and new applications emerge, the demand for advanced valves and regulators will continue to grow. Ongoing developments in materials, manufacturing, and safety standards promise to enhance their capabilities, ensuring they meet the rigorous needs of tomorrow’s applications. In essence, specialty gas line valves and pressure regulators not only facilitate today’s processes but also pave the way for future advancements, underscoring their enduring importance.
For more about the uses of specialty gas line valves and pressure regulators, you can pay a visit to Jewellok at https://www.jewellok.com/product-category/high-purity-gas-system/ for more info.
Recent Posts
Best Top 10 Specialty Gas Regulators Suppliers In Thailand
Best Top 10 Specialty Gas Regulators Manufacturers In India
Can Industrial Gas Regulators Be Used In Laboratories?
Tags
Recommended Products
-
DPR1 Ultra High Purity Two Stage Dual Stage Pressure Reducing Regulator Semiconductor Grade Regulators
-
764L Stainless Steel Union Tee High Purity Fitting Union Tee Reducing Tubing Connection
-
High Purity High Pressure Gas Cylinder Pressure Regulators Pressure Reducing Valve JSR-1E Series
-
7121L Plug High Purity Plug Fitting And Blanking Plug
-
767LT Reducer Pressure Reducing Valve Adjustment High purity Pressure Reducing Union Fittings And Tubing
-
Fully Automated Gas Cabinet For Precise UHP Gas Delivery And High Purity Gas Delivery Systems JW-300-GC
-
739LF High Purity Female Adapter Tube To Pipe Fittings And Connectors
-
High Purity High Flow Pressure Control Regulators & Valves Gas Stick Assemblies JSR-2TG Series