Blog
Jewellok is a professional pressure regulator and valve manufacturer and supplier.
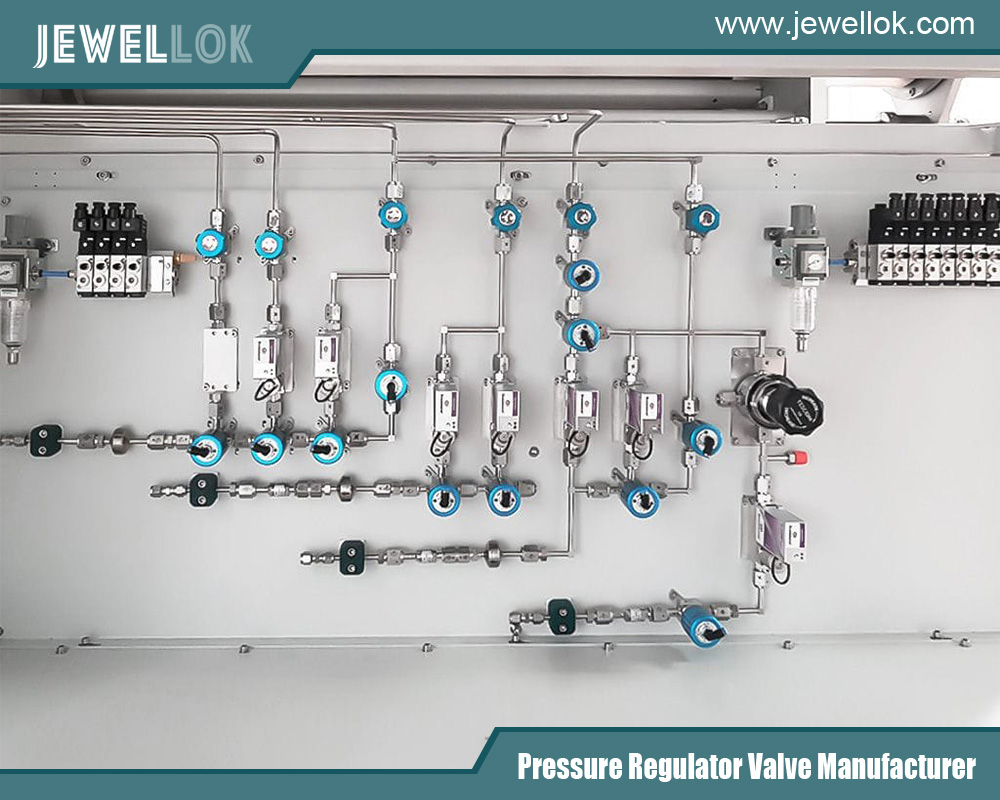
The Uses Of Semiconductor Fluid Control Systems And Components
- Pressure Regulator Valve Manufacturer
- China Diaphragm Valve Manufacturers, China Diaphragm Valve Suppliers, china semiconductor diaphragm valves manufacturers, Fluid Control for Semiconductor Fabrication, Fluid Dynamics Control and Monitoring Systems, Fluid System Components for the Semiconductor, Mass Flow Controller and Module, semiconductor diaphragm valves, semiconductor diaphragm valves manufacturers, Semiconductor fluid control systems, Semiconductor Fluid Control Systems And Components, Semiconductor Valves, UHP Semiconductor Components
- No Comments
The Uses Of Semiconductor Fluid Control Systems And Components
Introduction
Semiconductor fluid control systems are a cornerstone of the modern electronics industry, underpinning the complex processes that enable the production of semiconductor devices such as microchips, transistors, and integrated circuits. These systems are designed to manage and regulate the flow of liquids and gases used throughout the semiconductor fabrication process, ensuring that each step meets the stringent requirements of precision, purity, and efficiency. From delivering ultrapure chemicals for patterning wafers to controlling gases in deposition chambers and managing waste streams, fluid control systems are essential for maintaining the quality and reliability of semiconductor production. As the demand for smaller, faster, and more powerful electronic devices continues to grow, the role of these systems becomes increasingly critical. This article explores the primary uses of semiconductor fluid control systems, delving into their applications in chemical delivery, gas control, cooling, and waste management, while also highlighting the challenges they face and advancements driving their evolution.
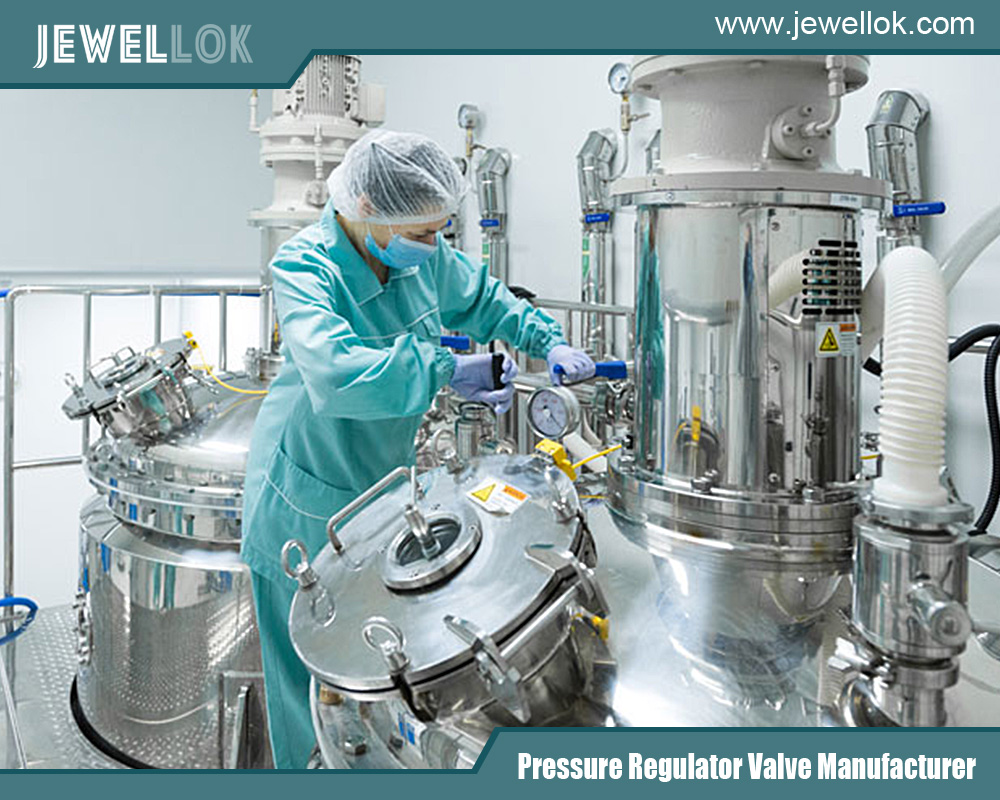
Chemical Delivery in Semiconductor Manufacturing
One of the most significant uses of semiconductor fluid control systems is in the precise delivery of chemicals during the manufacturing process. Semiconductor fabrication, often conducted in specialized facilities known as fabs, involves a series of intricate steps such as photolithography, etching, and cleaning, all of which rely heavily on the use of various liquids. These include photoresists for patterning circuit designs, developers to remove exposed or unexposed resist, etchants to strip away unwanted material, and solvents like ultrapure water for rinsing wafers. The accuracy and purity of chemical delivery directly impact the quality of the final semiconductor product, as even minor deviations or contaminants can introduce defects that compromise device performance.
Semiconductor fluid control systems designed for chemical delivery incorporate several key components:
Pumps: Precision pumps, such as peristaltic or diaphragm types, are used to transport chemicals without introducing contaminants. These pumps are engineered to handle corrosive or reactive substances safely.
Valves: High-purity valves regulate the flow and direction of liquids, ensuring that chemicals are dispensed only where and when needed.
Flow Meters: These devices monitor and control flow rates with exceptional accuracy, often down to microliters, to guarantee uniform application across wafers.
Filters: Inline filters remove particulates and impurities, maintaining the ultraclean conditions required for semiconductor processing.
Tubing and Piping: Constructed from materials like perfluoroalkoxy (PFA) or polytetrafluoroethylene (PTFE), these components prevent chemical leaching and ensure compatibility with aggressive substances.
Consider the photolithography process as an example. Here, a photoresist—a light-sensitive chemical—is coated onto a silicon wafer to define the intricate patterns of a microchip. The fluid control system must dispense the photoresist at a consistent viscosity and temperature, ensuring an even layer that meets exact thickness specifications. Any inconsistency could lead to imperfect patterns, reducing the yield of functional chips. Similarly, during wet etching, etchants must be delivered in precise quantities to remove material selectively without damaging the underlying structure. The corrosive nature of many chemicals also necessitates robust system design to prevent leaks, protect equipment, and ensure operator safety.
The importance of chemical delivery systems extends beyond precision to cost-effectiveness. Many of the chemicals used in semiconductor manufacturing are expensive, and minimizing waste through accurate dispensing is a key factor in maintaining profitability. By enabling tight control over chemical usage, these fluid control systems contribute significantly to the efficiency and economic viability of semiconductor production.
Gas Control Systems
In addition to liquids, gases play a vital role in semiconductor manufacturing, and their management is another critical application of fluid control systems. Process gases such as nitrogen, oxygen, argon, silane, and various dopants are used in steps like chemical vapor deposition (CVD), physical vapor deposition (PVD), etching, and ion implantation. These processes rely on the controlled introduction of gases into reaction chambers to deposit thin films, etch patterns, or modify material properties. The precision with which these gases are delivered directly affects the quality and uniformity of the semiconductor layers being formed.
Gas control systems within semiconductor fluid control frameworks typically include:
Mass Flow Controllers (MFCs): These devices are the backbone of gas delivery, precisely regulating flow rates by measuring the mass of gas passing through them. MFCs ensure that the exact amount of gas enters a process chamber, often in combination with other gases to achieve the desired chemical reaction.
Pressure Regulators: These maintain consistent pressure in gas lines, preventing fluctuations that could disrupt manufacturing processes.
Gas Purification Systems: Filters and purifiers remove impurities from gases, as even trace contaminants can degrade semiconductor quality.
Safety Systems: Given that some process gases are toxic or flammable (e.g., silane), leak detectors and emergency shut-off valves are integral to protecting personnel and equipment.
For instance, in a CVD process, a thin layer of material—such as silicon dioxide or nitride—is deposited onto a wafer by reacting gases like silane and oxygen at high temperatures. The fluid control system ensures that these gases are mixed and delivered at precise ratios and flow rates, determining the film’s thickness, uniformity, and electrical properties. Any imbalance could result in defective layers, rendering the semiconductor unusable. Similarly, in plasma etching, gases like chlorine or fluorine are introduced to remove material selectively, and the fluid control system must maintain stable conditions to achieve the desired etch profile.
The complexity of gas control is heightened by the need to handle multiple gases simultaneously, often under vacuum conditions or at elevated pressures. This requires seamless integration of fluid control systems with the broader manufacturing infrastructure, ensuring that gas delivery aligns perfectly with other process parameters.
Cooling Systems
Semiconductor manufacturing generates significant heat, both from the equipment and the processes themselves, making temperature control a crucial aspect of production. Fluid control systems are employed to circulate coolants—typically water or specialized fluids—through machinery and wafer holders to maintain optimal operating temperatures. Excessive heat can alter reaction rates, damage equipment, or introduce thermal stress to wafers, all of which can compromise the integrity of the final product.
Cooling systems in semiconductor fabs rely on several components:
Chillers: These units cool the circulating fluid to a specified temperature, ensuring consistent heat removal.
Heat Exchangers: Positioned near critical equipment, heat exchangers transfer thermal energy away from sensitive components.
Pumps and Valves: These circulate coolant efficiently and direct it to areas of greatest need.
Temperature Sensors: Integrated into the system, these sensors provide real-time feedback to adjust cooling as conditions change.
A practical example is the etching process, where plasma or wet etchants generate heat that can affect the wafer’s surface. The chuck holding the wafer is often cooled by a fluid control system that circulates coolant to maintain a stable temperature, ensuring uniform etching across the wafer. Similarly, high-powered tools like lithography machines or ion implanters rely on cooling systems to prevent overheating, which could lead to downtime or reduced precision.
Effective cooling not only enhances process stability but also extends the lifespan of expensive manufacturing equipment. As semiconductor devices shrink to nanoscale dimensions, the heat generated per unit area increases, placing greater demands on these fluid control systems to deliver efficient and reliable thermal management.
Waste Management
The semiconductor manufacturing process produces a variety of waste streams, including spent chemicals, contaminated water, and gaseous effluents, all of which must be managed carefully to comply with environmental regulations and ensure safety. Fluid control systems play an essential role in collecting, treating, and disposing of these byproducts, mitigating the environmental impact of semiconductor production.
Waste management systems typically involve:
Collection Systems: Pipes and tanks gather waste from various points in the fab, such as etching stations or cleaning baths.
Treatment Systems: Neutralization tanks adjust the pH of acidic or basic waste, while scrubbers remove harmful gases from exhaust streams. Filtration units may also extract dissolved metals or particulates.
Monitoring Systems: Sensors and analyzers ensure that treated waste meets regulatory standards before it is discharged or recycled.
For example, after a wet etching process, the used etchant—laden with dissolved silicon or metal residues—must be collected and neutralized to prevent environmental contamination. Similarly, gaseous byproducts from deposition or etching processes are passed through scrubbers to remove toxic compounds before release. These fluid control systems ensure that waste handling is both safe and sustainable, aligning with the industry’s growing emphasis on environmental responsibility.
Challenges in Semiconductor Fluid Control
The design and operation of semiconductor fluid control systems face several challenges:
Purity Requirements: The ultraclean standards of semiconductor manufacturing demand systems that minimize particle generation and chemical leaching, often requiring specialized materials and rigorous maintenance.
Precision and Accuracy: As feature sizes shrink to nanometers, fluid delivery must be controlled with tolerances in the microliter or nanoliter range, pushing the limits of current technology.
Chemical Compatibility: Systems must withstand a wide range of aggressive substances without degrading or introducing contaminants.
Scalability: Larger fabs require fluid control systems that can manage increased volumes while maintaining performance.
Automation: Integration with automated process control systems is essential for real-time adjustments and efficiency.
Advancements in Semiconductor Fluid Control Systems
Recent innovations are addressing these challenges:
Smart Systems: Sensors and Internet of Things (IoT) technologies enable real-time monitoring and predictive maintenance, reducing downtime and improving reliability.
Miniaturization: Compact designs fit within the constrained spaces of advanced equipment, supporting next-generation manufacturing tools.
Material Innovations: High-purity polymers and ceramics enhance durability and reduce contamination risks.
Energy Efficiency: New designs lower power consumption, aligning with sustainability goals.
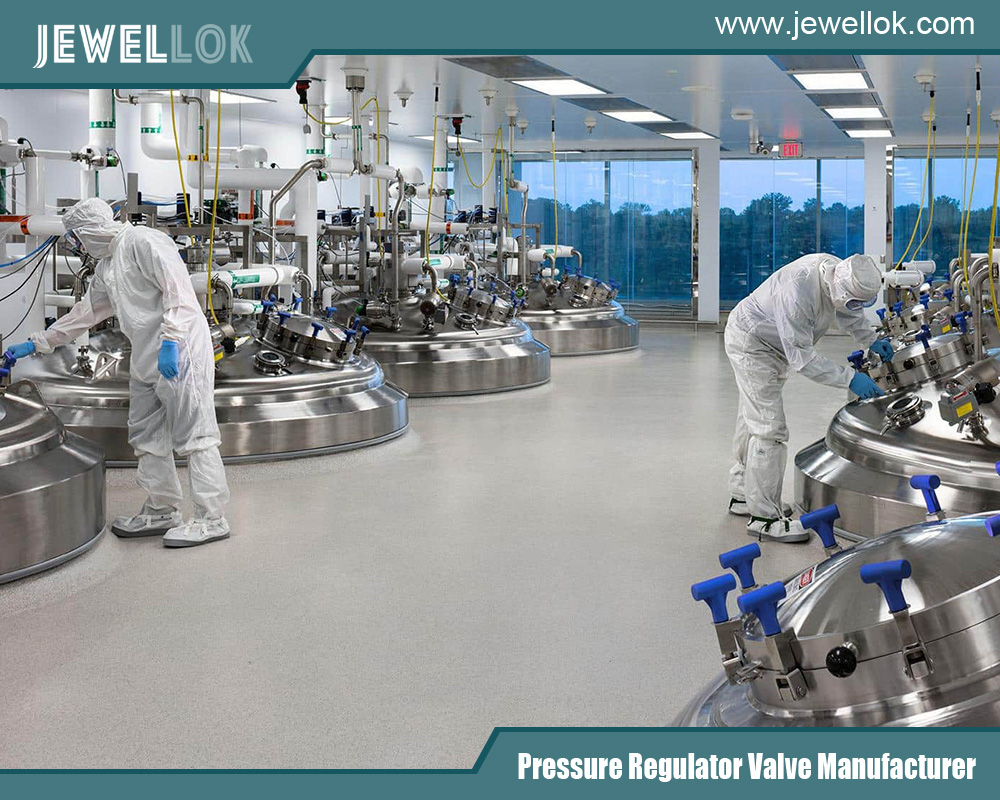
Conclusion
Semiconductor fluid control systems are indispensable to the electronics industry, enabling the precise delivery of chemicals and gases, effective temperature regulation, and responsible waste management. These systems ensure that semiconductor manufacturing meets the exacting standards of purity, precision, and efficiency required to produce the devices that power our digital world. As the industry advances toward smaller, more complex chips, the role of fluid control systems will continue to grow, driven by innovations that enhance their performance and sustainability. Far from being mere support infrastructure, they are vital enablers of technological progress, ensuring the reliability and quality of semiconductors that define modern life.
For more about the uses of semiconductor fluid control systems and components, you can pay a visit to Jewellok at https://www.jewellok.com/semiconductor/ for more info.
Recent Posts
Tags
Recommended Products
-
772L Male Branch Tee | Stainless Steel High-Purity Tube Fitting Male Branch Tee
-
Fully Automated Gas Cabinet For Precise UHP Gas Delivery And High Purity Gas Delivery Systems JW-300-GC
-
7102L Stainless Steel 316L SS Union Cross Ultra High Purity Long Arm Union Elbow Tee Cross Butt Weld Fittings
-
T-BOX JW-TB-C Special Gas Delivery System Gas Valve Manifold Boxes
-
7121L Plug High Purity Plug Fitting And Blanking Plug
-
Pressure Control Panels For High Purity Gas Control System JSP-3AE Series From Pressure Control Panels Suppliers And Manufacturer
-
High Purity High Pressure Stainless Steel Needle Valve Natural Gas Flow Control Valve JNV Series
-
High Purity Chemical Dispense System & Packing System For Semiconductors JW-200L-CDM & JW-1000L-CDM