Blog
Jewellok is a professional pressure regulator and valve manufacturer and supplier.
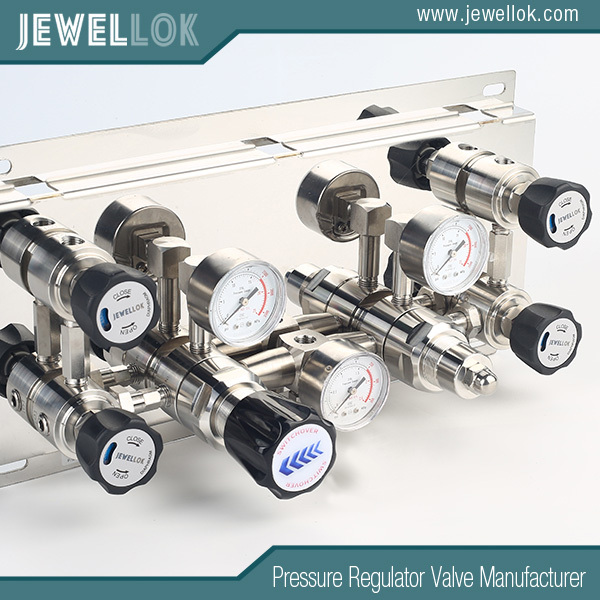
The Uses Of Integrated Gas Systems In The Semiconductor Manufacturing Process
- Pressure Regulator Valve Manufacturer
- China Gas Panels Manufacturers, China Gas System Manufacturers, fully integrated gas supply system, Gas Delivery Cabinet Systems, gas panel semiconductor, IGS Gas Box and Regulator Valves for Gas Systems, integrated gas supply system, integrated gas system, Integrated Gas System (IGS), integrated gas system china supplier, Integrated Gas System in the Semiconductor Companies, integrated gas system supplier, Integrated Gas Systems in the Semiconductor, Modular gas flow systems, Modular Integrated Gas Systems, Natural-gas distributor for CNG and LNG systems, UHP Gas Distribution Panel
- No Comments
The Uses Of Integrated Gas Systems In The Semiconductor Manufacturing Process
Introduction
The semiconductor industry underpins modern technology, powering everything from smartphones to advanced medical devices. At the heart of semiconductor manufacturing lies a complex ecosystem of processes requiring precision, purity, and efficiency. Integrated gas systems (IGS) play a pivotal role in this ecosystem, delivering and managing the specialty gases essential for fabricating microchips. These systems ensure that gases like nitrogen, argon, silane, and others are supplied at the right purity, pressure, and flow rate to meet stringent production demands. As semiconductor devices shrink to nanoscale dimensions and production scales up, the importance of IGS has grown exponentially. This article explores the multifaceted uses of integrated gas systems in semiconductor manufacturing, from deposition and etching to safety and sustainability, highlighting their critical contribution to the industry’s success.
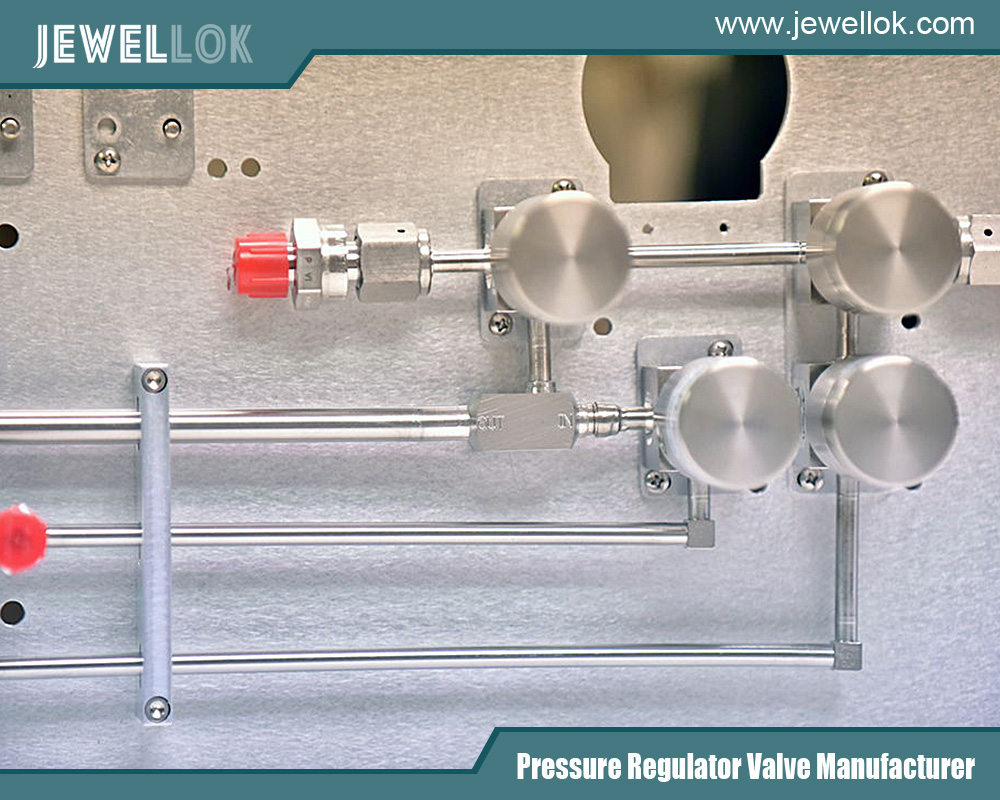
What Are Integrated Gas Systems?
Integrated gas systems refer to the interconnected network of equipment—cylinders, valves, regulators, purifiers, and delivery pipelines—designed to store, purify, and distribute gases in a controlled manner. In semiconductor fabrication plants (fabs), these systems are engineered to handle a variety of gases, categorized into bulk gases (e.g., nitrogen, oxygen) and specialty gases (e.g., dopants like arsine or process gases like tetrafluoromethane). Unlike standalone gas delivery setups, IGS are centralized, automated, and optimized for high-purity applications. They integrate advanced monitoring and control technologies to maintain gas quality and operational safety, ensuring that contaminants—measured in parts per trillion—are minimized. This section could elaborate on the evolution of IGS from simple gas cabinets to sophisticated, software-driven systems tailored to modern fabs.
Key Uses of Integrated Gas Systems in Semiconductor Manufacturing
1. Thin Film Deposition
One of the primary uses of IGS is in thin film deposition, a cornerstone of semiconductor manufacturing. Processes like Chemical Vapor Deposition (CVD) and Atomic Layer Deposition (ALD) rely on precise gas mixtures to deposit layers of materials—such as silicon dioxide or metal nitrides—onto wafers. For instance, silane (SiH₄) combined with oxygen or ammonia is delivered via IGS to form insulating or conductive layers. The system ensures that gas flow is consistent and free of impurities, as even minute contamination can lead to defects in the nanometer-scale features of modern chips. Automation within IGS adjusts flow rates in real-time, adapting to process requirements and enhancing yield.
2. Etching and Patterning
Etching removes material from wafers to create intricate circuit patterns, and IGS supplies reactive gases like chlorine (Cl₂) or sulfur hexafluoride (SF₆) for plasma etching. These gases must be delivered at exact pressures and purities to achieve uniform etching without damaging underlying layers. Wet etching, though less common today, may use nitrogen as a carrier gas, also managed by IGS. The precision of IGS in controlling gas delivery directly impacts the resolution and reliability of the etched features, critical for advanced nodes like 3nm or 2nm processes.
3. Doping and Ion Implantation
Doping introduces impurities into silicon to alter its electrical properties, and IGS supplies gases like phosphine (PH₃) or boron trifluoride (BF₃) for this purpose. In ion implantation, these gases are ionized and accelerated into the wafer. The IGS ensures a stable supply of these hazardous gases while mitigating risks through leak detection and emergency shutoff systems.
4. Cleaning and Purging
Post-process cleaning of chambers and wafers uses inert gases like nitrogen or argon, delivered via IGS, to remove residues and prevent contamination. Purging with high-purity nitrogen also maintains an inert atmosphere in process tools, protecting sensitive materials from oxidation.
Safety and Environmental Considerations
Many gases used in semiconductor manufacturing are toxic, flammable, or environmentally harmful. Integrated gas systems incorporate safety features like gas detectors, scrubbers, and exhaust management to protect workers and comply with regulations. For example, silane is pyrophoric, igniting spontaneously in air, so IGS includes interlocks to prevent leaks. Environmentally, IGS helps reduce waste by optimizing gas usage and capturing unreacted gases for recycling or safe disposal. This section could explore how IGS aligns with sustainability goals, such as reducing greenhouse gas emissions from perfluorocarbons used in etching.
Future Trends and Innovations
As semiconductor technology advances toward smaller nodes and new materials (e.g., 2D materials like graphene), IGS must evolve. Innovations include AI-driven gas flow optimization, modular systems for flexible fab designs, and greener gas alternatives. The rise of extreme ultraviolet (EUV) lithography, for instance, increases demand for ultra-pure hydrogen, pushing IGS to achieve even higher purity levels. This section could discuss emerging technologies and their implications for IGS design and deployment.
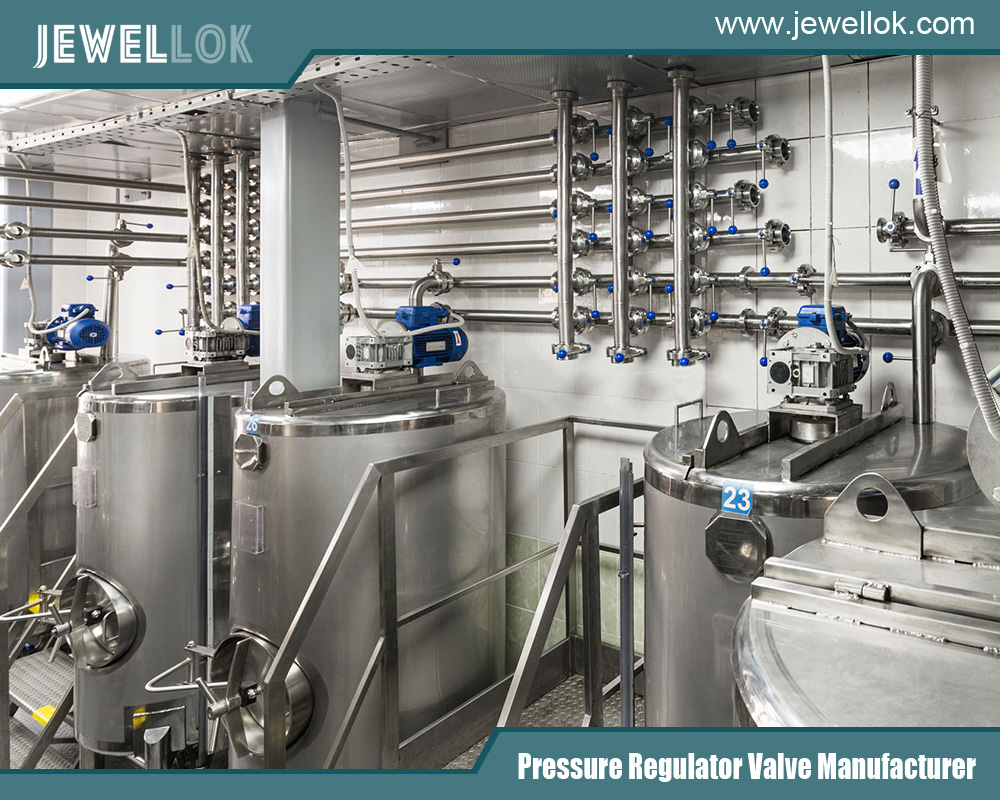
Conclusion
Integrated gas systems are indispensable to semiconductor manufacturing, enabling the precision and scalability required to produce cutting-edge microchips. From deposition and etching to safety and sustainability, their role spans the entire fabrication process. As the industry pushes the boundaries of physics and engineering, IGS will continue to adapt, ensuring that the gases powering tomorrow’s innovations are delivered with unmatched reliability. The seamless integration of these systems exemplifies the synergy of chemistry, engineering, and technology that defines the semiconductor revolution.
For more about the uses of integrated gas system in the semiconductor manufacturing process, you can pay a visit to Jewellok at https://www.jewellok.com/semiconductor/ for more info.
Recent Posts
Tags
Recommended Products
-
766L High Purity Female Connector UHP Fitting Female Connector
-
763L Stainless Steel High Purity Pressure Reducing Union Fittings And Tubing Pressure Reducing Valve Adjustment
-
Ultra High Purity Pressure Gauge For Laboratory And Semiconductor JR Series
-
7102L Stainless Steel 316L SS Union Cross Ultra High Purity Long Arm Union Elbow Tee Cross Butt Weld Fittings
-
High Purity High Pressure Stainless Steel Needle Valve Natural Gas Flow Control Valve JNV Series
-
Stainless Steel Ultra Clean Welding Joint Fittings TW Series TRW Series & CW Series
-
765LR Reducing Tee | Stainless Steel 316 High Purity Butt Weld Fittings Metal Face Seal For Welding Pipe Fitting Reducing Tee
-
765L Stainless Steel Union Elbow Reducing High Purity Fitting Tubing Extension Tubing Connection