Blog
Jewellok is a professional pressure regulator and valve manufacturer and supplier.
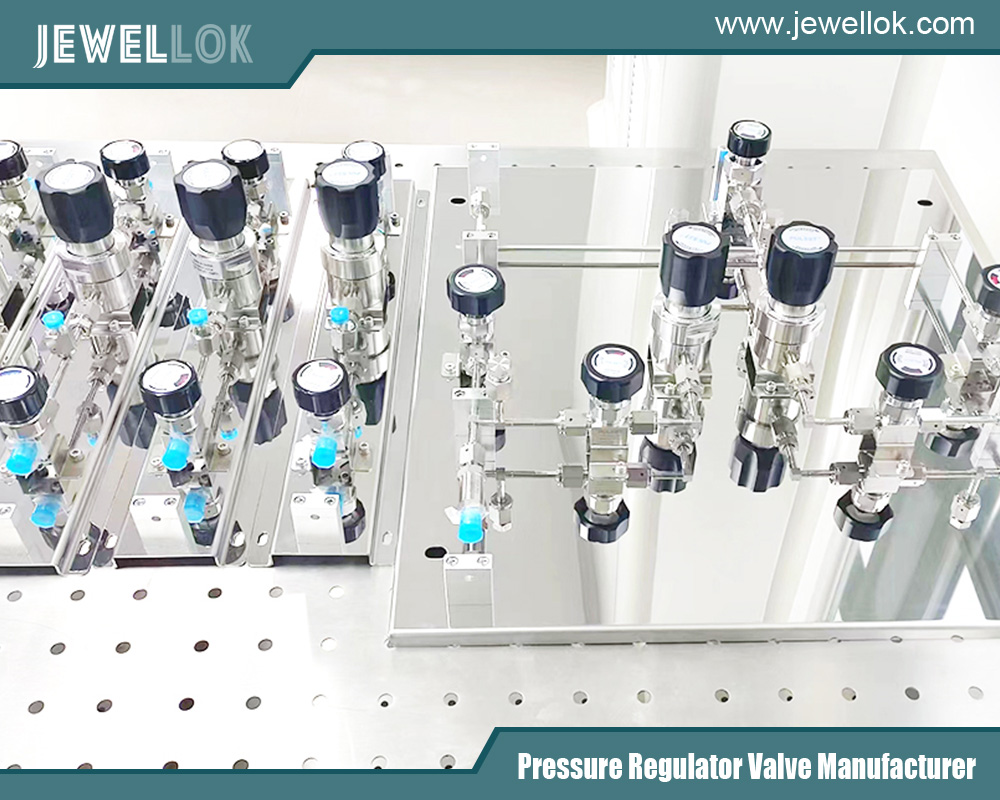
The Uses Of Hydrogen Pressure Regulators And Valves In Semiconductor Manufacturing
- Pressure Regulator Valve Manufacturer
- high pressure hydrogen regulator, high purity Hydrogen regulators, Hydrogen Cylinder Pressure Regulator, Hydrogen Fuel Cell Pressure Regulators, Hydrogen Gas Pressure Gas Regulators, Hydrogen Gas Pressure Regulators, Hydrogen Gas Regulator Manufacturers, Hydrogen Gas Regulator Manufacturers china, Hydrogen Gas Regulators, Hydrogen Pressure Regulator, Hydrogen Pressure Regulators And Valves, Hydrogen Regulators and Valves, Hydrogen regulators manufacturers, Hydrogen valve manufacturers, Hydrogen valve manufacturers China, Industrial Gas Regulators, Top Industrial Regulator Manufacturers, Two Stage Hydrogen Gas Regulator
- No Comments
The Uses Of Hydrogen Pressure Regulators And Valves In Semiconductor Manufacturing
Introduction
Semiconductor manufacturing is a cornerstone of modern technology, enabling the production of microchips that power everything from smartphones to advanced artificial intelligence systems. This intricate process relies on a delicate balance of precision, purity, and control, particularly when handling gases like hydrogen. Hydrogen plays a critical role in various stages of semiconductor fabrication, such as deposition, annealing, and etching. However, its flammable and highly reactive nature demands stringent safety and precision in its delivery and application. This is where hydrogen pressure regulators and valves come into play. These devices ensure that hydrogen is delivered at the correct pressure, flow rate, and purity, safeguarding both the manufacturing process and the personnel involved. This article explores the pivotal uses of hydrogen pressure regulators and valves in semiconductor manufacturing, highlighting their technical significance, operational mechanisms, and contributions to efficiency and safety.
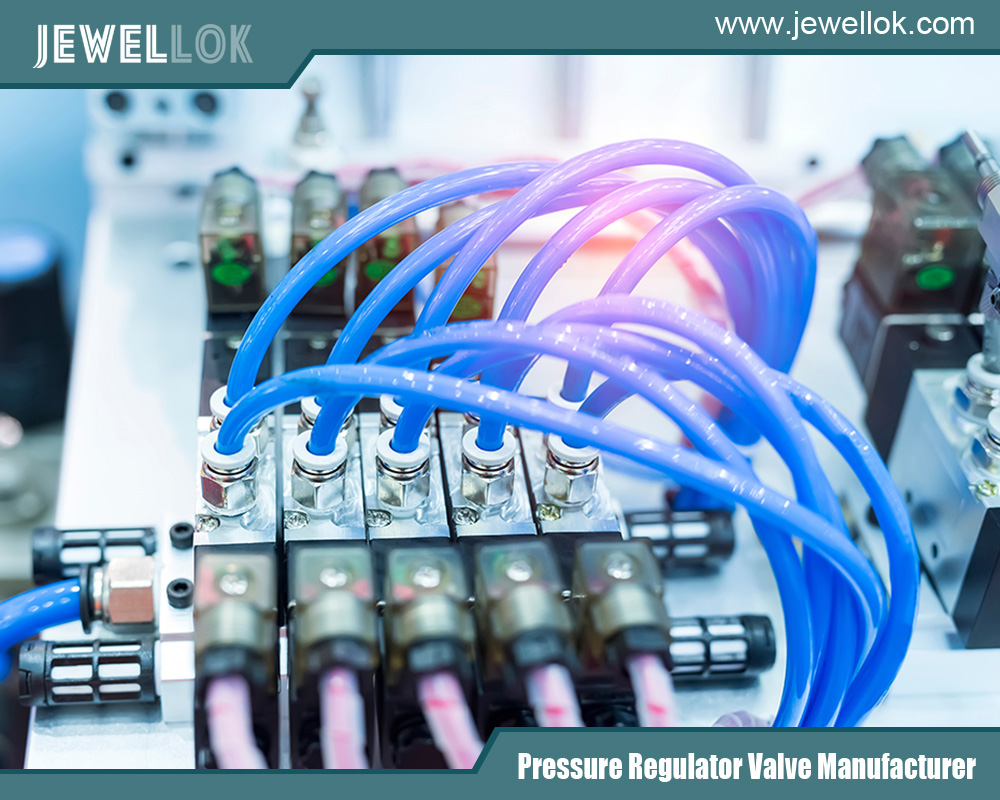
The Role of Hydrogen in Semiconductor Manufacturing
Before delving into the specifics of pressure regulators and valves, it’s essential to understand why hydrogen is indispensable in semiconductor production. Hydrogen is a versatile gas used in several key processes:
-
Chemical Vapor Deposition (CVD): In CVD, hydrogen acts as a carrier gas or reducing agent, facilitating the deposition of thin films (e.g., silicon or metal layers) onto wafers. It ensures uniform film growth, critical for the performance of microchips.
-
Annealing: Hydrogen is used in annealing furnaces to remove defects in silicon wafers by reducing oxides and improving crystal structure. This enhances the electrical properties of the semiconductor.
-
Etching: In plasma etching, hydrogen can be part of gas mixtures that selectively remove material from wafers, shaping intricate circuit patterns.
-
Epitaxy: During epitaxial growth, hydrogen maintains a clean environment by preventing contamination and aiding in the precise layering of crystalline structures.
Given its widespread use, hydrogen must be delivered with exacting control. Too much pressure could damage equipment or wafers, while insufficient flow might compromise process quality. This precision is achieved through specialized pressure regulators and valves designed for hydrogen applications.
What Are Hydrogen Pressure Regulators and Valves?
Hydrogen pressure regulators and valves are critical components of gas delivery systems in semiconductor fabs (fabrication plants). They work in tandem to manage the flow, pressure, and distribution of hydrogen from high-pressure storage cylinders to the low-pressure environments required in manufacturing tools.
-
Pressure Regulators: These devices reduce the high pressure of hydrogen gas (often stored at 2000–3000 psi) to a stable, usable level (e.g., 10–100 psi) suitable for specific processes. They maintain consistent output pressure despite fluctuations in supply or demand, ensuring process stability.
-
Valves: Valves control the direction, start, and stop of hydrogen flow. Types include shut-off valves, check valves (to prevent backflow), and flow control valves, each tailored to specific points in the gas delivery system.
In semiconductor manufacturing, these components must meet stringent standards for purity, reliability, and safety due to hydrogen’s properties and the sensitivity of the processes involved.
Key Uses of Hydrogen Pressure Regulators and Valves
1. Ensuring Process Precision and Consistency
Semiconductor manufacturing demands repeatability and precision at the nanoscale. A single deviation in gas pressure or flow can lead to defects in chip production, rendering entire batches unusable. Hydrogen pressure regulators maintain a steady output pressure, compensating for variables like cylinder depletion or temperature changes. For instance, in a CVD reactor, a regulator ensures that hydrogen flows at a constant rate, enabling uniform film deposition across multiple wafers. Valves complement this by precisely starting or stopping flow, ensuring that hydrogen enters the process chamber only when needed.
Modern regulators often feature dual-stage designs, which provide even greater stability. The first stage reduces the high inlet pressure, while the second stage fine-tunes the output, minimizing pressure fluctuations. This is particularly vital in high-volume production where consistency across thousands of wafers is non-negotiable.
2. Maintaining Gas Purity
Contamination is the nemesis of semiconductor manufacturing. Even trace impurities in hydrogen—such as moisture, oxygen, or hydrocarbons—can degrade wafer quality, leading to reduced chip performance or failure. Pressure regulators and valves designed for hydrogen use are typically constructed from materials like stainless steel or Hastelloy, which resist corrosion and outgassing (the release of trapped gases). They also incorporate features like metal diaphragms and high-purity seals to prevent contamination.
In ultra-high-purity (UHP) applications, regulators and valves are cleaned and assembled in cleanrooms to eliminate particulates. For example, a hydrogen regulator might be paired with a purge valve to flush the system with inert gas (like nitrogen) before introducing hydrogen, ensuring that no residual contaminants remain. This purity is critical in processes like epitaxy, where even parts-per-billion (ppb) levels of impurities can disrupt crystal growth.
3. Enhancing Safety
Hydrogen’s flammability poses significant risks in semiconductor fabs. With a low ignition energy and a wide flammable range (4–75% in air), any leak or pressure surge could lead to catastrophic fires or explosions. Pressure regulators mitigate these risks by preventing over-pressurization, which could rupture lines or fittings. Many regulators include built-in relief valves that vent excess pressure safely to a designated exhaust system.
Valves, such as emergency shut-off valves, provide an additional layer of protection. In the event of a leak detection or system failure, these valves can instantly isolate hydrogen flow, minimizing exposure. Automated valves linked to gas detection systems are increasingly common, allowing real-time monitoring and rapid response to anomalies. This combination of regulators and valves ensures that hydrogen is handled safely, protecting both personnel and multimillion-dollar equipment.
4. Optimizing Gas Delivery Systems
Semiconductor fabs rely on complex gas distribution networks to supply hydrogen and other gases to multiple process tools. Pressure regulators and valves are strategically placed throughout these systems to optimize performance. For example:
-
Point-of-Use Regulation: Regulators installed near process chambers fine-tune pressure for specific tools, reducing variability caused by long gas lines.
-
Flow Control: Mass flow control valves paired with regulators adjust hydrogen delivery rates dynamically, matching the needs of real-time process adjustments.
-
Zoning: Valves segment the gas system into zones, allowing maintenance or upgrades in one area without shutting down the entire fab.
This modular approach enhances efficiency, reduces gas waste, and minimizes downtime—a critical factor in an industry where every minute of production stoppage translates to significant financial losses.
5. Supporting Advanced Semiconductor Processes
As semiconductor technology advances, processes like extreme ultraviolet (EUV) lithography and 3D NAND fabrication push the boundaries of gas control. Hydrogen is increasingly used in these cutting-edge applications—for instance, in EUV systems to clean optics or in 3D NAND to facilitate high-aspect-ratio etching. These processes require ultra-low pressures and precise flow rates, often in the millitorr range.
Advanced hydrogen pressure regulators, such as those with electronic feedback systems, meet these demands by integrating sensors and controllers to adjust pressure in real time. Similarly, microvalves with rapid response times enable fine-tuned flow adjustments. These innovations ensure that hydrogen delivery keeps pace with the evolving complexity of semiconductor manufacturing.
Challenges and Considerations
While hydrogen pressure regulators and valves are indispensable, their deployment in semiconductor manufacturing comes with challenges:
-
Material Compatibility: Hydrogen can embrittle certain metals (e.g., carbon steel), leading to cracks or failures over time. Selecting hydrogen-compatible materials increases costs but is essential for long-term reliability.
-
Maintenance: Regular calibration and inspection are required to ensure regulators and valves perform within tight tolerances. Any drift in performance could compromise process quality.
-
Cost: High-purity, high-precision components are expensive, reflecting the rigorous engineering and testing they undergo. For smaller fabs, balancing cost and performance can be a hurdle.
-
Regulatory Compliance: Semiconductor fabs must adhere to safety standards (e.g., SEMI S2, OSHA guidelines) that dictate the design and operation of hydrogen systems, adding complexity to implementation.
Manufacturers address these challenges through rigorous design, such as using hydrogen-specific alloys, incorporating redundant safety features, and offering modular systems that simplify maintenance.
Future Trends
The role of hydrogen pressure regulators and valves is evolving alongside semiconductor technology. As chipmakers pursue smaller nodes (e.g., 2nm processes) and greener manufacturing, hydrogen use is expected to grow. Trends shaping their future include:
-
Smart Systems: Integration with IoT and AI allows regulators and valves to self-diagnose issues, predict maintenance needs, and optimize gas usage.
-
Sustainability: Hydrogen produced via renewable energy (green hydrogen) is gaining traction, requiring regulators and valves to handle varying supply pressures efficiently.
-
Miniaturization: Compact, high-performance components are being developed to fit the shrinking footprints of next-generation fabs.
These advancements promise to enhance the precision, safety, and sustainability of hydrogen delivery in semiconductor production.
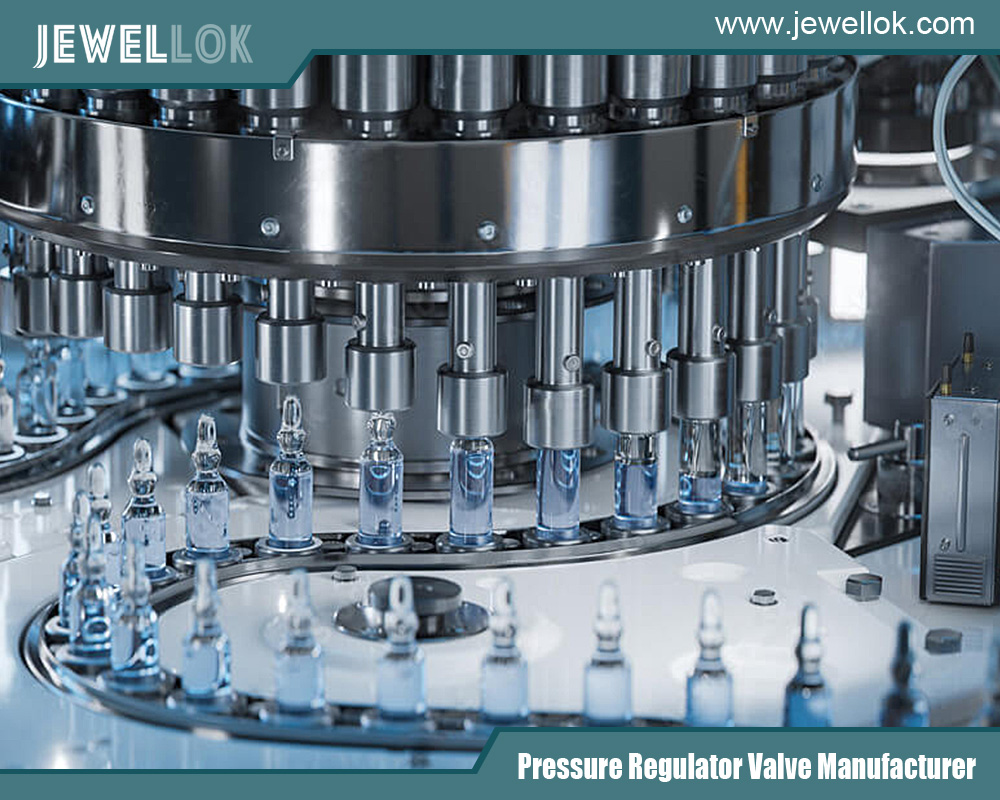
Conclusion
Hydrogen pressure regulators and valves are unsung heroes in the semiconductor manufacturing ecosystem. They ensure that hydrogen—a vital yet challenging gas—is delivered with the precision, purity, and safety required to produce the microchips powering our digital world. From maintaining process consistency to mitigating safety risks and supporting cutting-edge innovations, these devices are integral to the success of modern fabs. As the industry continues to evolve, so too will the technology behind these components, adapting to new demands and driving the future of semiconductor fabrication. In an era where technological progress hinges on the tiniest of details, hydrogen pressure regulators and valves stand as testaments to the power of precision engineering.
For more about the uses of hydrogen pressure regulators and valves in semiconductor manufacturing, you can pay a visit to Jewellok at https://www.jewellok.com/semiconductor/ for more info.
Recent Posts
Tags
1 1 2 gas pressure regulator
1 2 gas regulator
1/2 gas pressure regulator
2 inch irrigation solenoid valve
6mm compression fitting
6mm equivalent
adjustable low pressure propane regulator
adjustable propane pressure regulator
adjustable propane regulator
adjusting propane regulator
air compressor non return valve
argon hose fitting
characteristics of pressure
diaphragm suppliers
fluid systems components
gas regulator
gas used in semiconductor manufacturing
how a gas pressure regulator works
how a pressure regulator works
how a solenoid valve works
how does a needle valve work
how does pressure regulator work
how do pressure regulators work
how often should pressure relief valves be replaced
how solenoid valves work
humming propane regulator
low pressure regulator
pressure gauge manufacturers
pressure regulator
pressure regulator valve leaking
pressure relief valve vs safety relief valve
relief vs safety valve
safety relief valve vs pressure relief valve
safety relief valve vs safety valve
safety valve and relief valve
safety valve and relief valve difference
safety valve vs pressure relief valve
single stage pressure regulator
solenoid valve for ammonia gas 1 inch pipe
solenoid water valve
stainless pressure regulator
stainless steel 1/4 in. pressure gauge fitting - 3/8 qc
two stage pressure regulator
water solenoid valve 24v
what is a gas pressure regulator
Recommended Products
-
7121L Plug High Purity Plug Fitting And Blanking Plug
-
FT-BOX JW-FTB-C Valve Manifold Panels And Boxes With High Purity Configurable Systems
-
Stainless Steel 316L Single Stage Regulator Pressure Control Panels JSP-1E Series For Semiconductor Fluid Control
-
739LF High Purity Female Adapter Tube To Pipe Fittings And Connectors
-
DPR1 Ultra High Purity Two Stage Dual Stage Pressure Reducing Regulator Semiconductor Grade Regulators
-
767LP Port Connector Ultra High Purity VCR Metal Gasket Face Seal Tube Fittings
-
Stainless Steel Mini Elbow Mini Tee Mini Cross Mini Tribow Ultrahigh Purity Mini Butt Weld Fittings
-
Stainless Steel Low Pressure Seal Pneumatic Diaphragm Control Valve For For HP & UHP Gases