Blog
Jewellok is a professional pressure regulator and valve manufacturer and supplier.
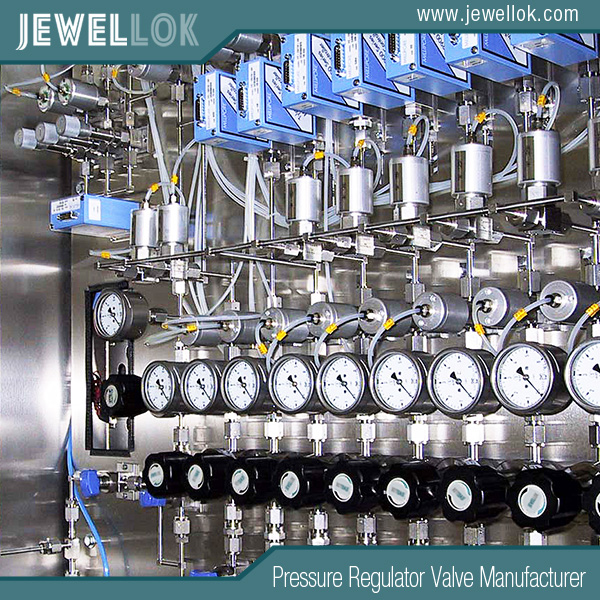
The Uses Of Argon Gas Flow Gauge Regulator And Valves In The Semiconductor Industry
- Pressure Regulator Valve Manufacturer
- Argon Flow Gauge Regulator, Argon Gas Flow Gauge Regulator And Valves, Argon Gas Regulators, Argon Mini Regulator, Argon Regulator, argon regulator for mig welder, Argon Regulator for TIG Welding, Argon Regulator with Dual Flow Meter, argon regulator with flow meter, Dual Flow Argon Regulator, Dual Output Argon Regulator, high pressure argon regulator, high purity argon regulator, Industrial Gas Regulators, Single Stage Argon Regulators
- No Comments
The Uses Of Argon Gas Flow Gauge Regulator And Valves In The Semiconductor Industry
Introduction
The semiconductor industry stands as a cornerstone of modern technology, powering everything from smartphones to advanced medical devices. At the heart of this industry lies a complex ecosystem of materials, processes, and equipment, among which argon gas plays a critical role. Argon, an inert noble gas, is widely used in semiconductor manufacturing due to its stability and non-reactive properties. However, its effective application hinges on precise control, which is where argon gas flow gauge regulators and valves come into play. These devices ensure that argon is delivered at the right pressure, flow rate, and purity, safeguarding the integrity of delicate semiconductor processes like deposition, etching, and ion implantation. This article explores the multifaceted uses of argon gas flow gauge regulators and valves in the semiconductor industry, delving into their technical significance, operational mechanisms, and impact on production efficiency and product quality. By understanding their role, we can appreciate how these unsung heroes enable the creation of cutting-edge microchips that drive the digital age.

The Role of Argon Gas in Semiconductor Manufacturing
Argon gas is a staple in semiconductor fabrication due to its inert nature, which prevents unwanted chemical reactions during high-precision processes. Its primary applications include:
-
Plasma Etching: Argon is used in plasma etching to physically bombard and remove material from wafer surfaces. The gas is ionized into a plasma state, allowing it to etch intricate patterns onto silicon wafers with nanoscale precision.
-
Sputtering and Deposition: In physical vapor deposition (PVD), argon ions dislodge atoms from a target material, depositing them onto the wafer to form thin films critical for chip functionality.
-
Ion Implantation: Argon assists in doping processes, where specific ions are embedded into the wafer to alter its electrical properties.
-
Purging and Blanketing: Argon is used to purge chambers of reactive gases like oxygen and moisture, creating a controlled, contamination-free environment.
These processes demand exacting conditions—any deviation in gas flow or pressure can compromise wafer quality, leading to defective chips. This is where flow gauge regulators and valves become indispensable. They regulate argon delivery, ensuring consistency and reliability across production cycles.
Understanding Argon Gas Flow Gauge Regulators
A flow gauge regulator is a precision instrument designed to control the pressure and flow rate of argon gas from a high-pressure cylinder to the semiconductor processing equipment. Here’s how it functions and why it matters:
-
Components: A typical regulator includes a pressure gauge (to monitor cylinder and delivery pressure), a diaphragm or piston mechanism (to reduce pressure), and a flow meter (to measure gas output in liters per minute or cubic feet per hour).
-
Pressure Reduction: Argon is stored at pressures up to 3000 psi, far too high for delicate semiconductor tools. Regulators reduce this to a usable range (e.g., 10-50 psi), tailored to specific processes.
-
Flow Control: Semiconductor processes require precise gas volumes. Flow gauge regulators ensure that argon enters the system at a steady, controlled rate, preventing surges that could disrupt plasma stability or deposition uniformity.
In practice, regulators are critical in maintaining process repeatability. For instance, during plasma etching, inconsistent argon flow could lead to uneven etching depths, ruining the wafer. Advanced regulators may also feature dual-stage designs, offering finer control by reducing pressure in two steps, which is vital for ultra-high-purity applications in cutting-edge 5nm or 3nm chip production.
The Importance of Valves in Argon Gas Delivery
Valves complement regulators by providing on-off control, directional flow management, and safety features in argon gas systems. Their key types and uses include:
-
Shut-Off Valves: These allow operators to isolate argon flow during maintenance or emergencies, protecting equipment and personnel.
-
Needle Valves: Offering fine-tuned flow adjustment, needle valves are used in processes requiring micro-level precision, such as ion implantation.
-
Check Valves: These prevent backflow, ensuring argon moves only toward the processing chamber and not back into the supply line, which could introduce contaminants.
-
Purge Valves: Essential for removing residual gases from lines before introducing argon, maintaining system purity.
In semiconductor cleanrooms, valves are often made from stainless steel or other non-reactive materials to avoid contaminating the ultra-pure argon (typically 99.999% purity or higher). Automated valves integrated with control systems also enable real-time adjustments, enhancing process efficiency. For example, during sputtering, a sudden pressure drop detected by sensors can trigger a valve to adjust argon inflow, stabilizing the deposition rate.
Synergy Between Regulators and Valves
Regulators and valves work in tandem to create a seamless argon delivery system. The regulator sets the baseline pressure and flow, while valves fine-tune and direct the gas to its destination. This synergy is evident in a typical deposition chamber: the regulator maintains a steady 20 psi output, while a needle valve adjusts the flow to 10 sccm (standard cubic centimeters per minute) for precise thin-film growth. Meanwhile, a check valve ensures no backflow disrupts the process, and a shut-off valve stands ready for rapid isolation if needed. This coordinated effort minimizes waste, enhances safety, and ensures the tight tolerances required for modern chips.
Impact on Semiconductor Industry Efficiency and Quality
The precision offered by argon gas flow gauge regulators and valves directly impacts production outcomes:
-
Yield Improvement: Consistent argon delivery reduces defects, boosting the percentage of usable chips per wafer—a critical metric given the high cost of silicon substrates.
-
Cost Efficiency: By minimizing gas overuse and preventing process interruptions, these devices lower operational expenses in an industry where margins are razor-thin.
-
Scalability: As chip designs shrink to sub-5nm scales, the demand for tighter control over gas dynamics grows. Advanced regulators and valves enable manufacturers to meet these challenges without redesigning entire systems.
-
Safety: Properly regulated argon flow prevents over-pressurization incidents, protecting both equipment and cleanroom personnel.
For instance, a leading foundry like TSMC relies on such systems to produce billions of transistors per chip, where even a 1% improvement in yield translates to millions in savings.
Challenges and Innovations
Despite their importance, argon gas flow systems face challenges. Contamination risks from valve wear, calibration drift in regulators, and the high cost of ultra-pure components can complicate operations. Innovations are addressing these issues:
-
Smart Regulators: Equipped with IoT sensors, these devices monitor flow and pressure in real-time, alerting operators to anomalies.
-
Corrosion-Resistant Materials: Advances in metallurgy and coatings extend valve lifespans in harsh cleanroom environments.
-
Modular Designs: Newer systems allow easy swapping of components, reducing downtime during maintenance.
These developments ensure that argon delivery systems keep pace with the semiconductor industry’s relentless drive toward smaller, faster, and more efficient chips.
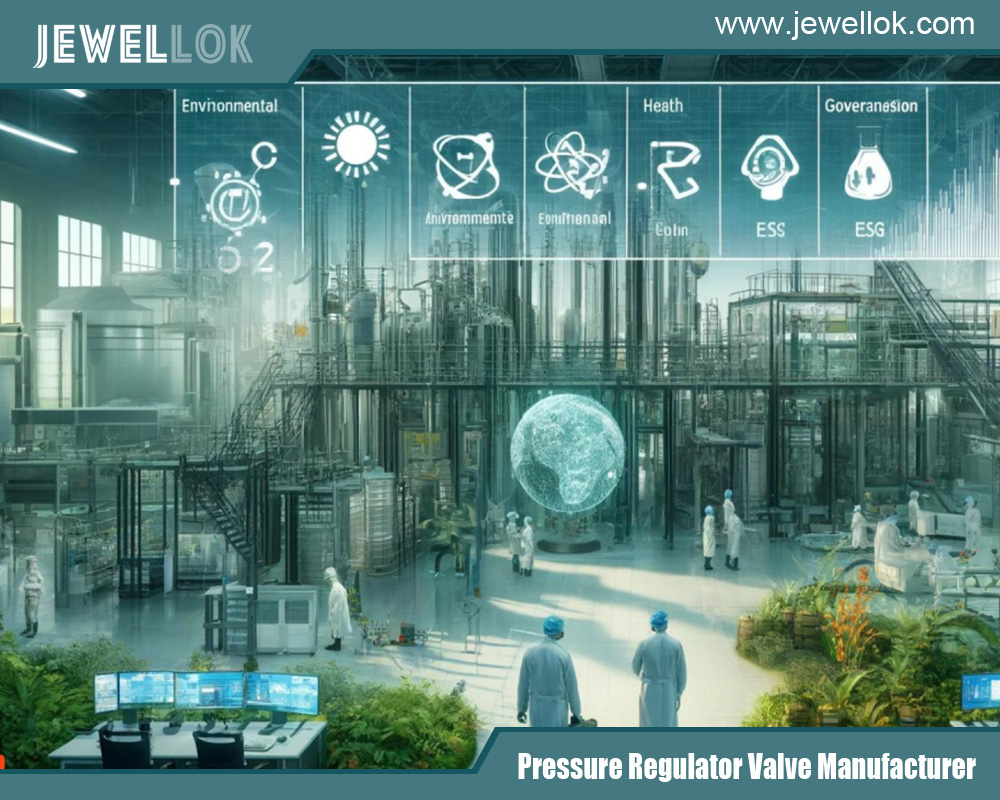
Conclusion
Argon gas flow gauge regulators and valves are linchpins in the semiconductor industry, enabling the precise, reliable, and safe use of argon in critical manufacturing processes. From plasma etching to thin-film deposition, their ability to control gas flow and pressure underpins the production of the microchips that power our world. As the industry pushes toward ever-smaller nodes and higher performance, the role of these devices will only grow, supported by innovations that enhance their precision and durability. By ensuring process consistency, improving yields, and reducing costs, they exemplify how even the smallest components can have an outsized impact on technological progress. For engineers, researchers, and manufacturers, understanding and optimizing these tools is key to staying competitive in a field where precision is paramount.
For more about the uses of argon gas flow gauge regulator and valves in the semiconductor industry, you can pay a visit to Jewellok at https://www.jewellok.com/semiconductor/ for more info.
Recent Posts
Tags
1 1 2 gas pressure regulator
1 2 gas regulator
1 2 propane regulator
1/2 gas pressure regulator
2 inch irrigation solenoid valve
6mm equivalent
adjustable low pressure propane regulator
adjustable propane pressure regulator
adjustable propane regulator
adjusting propane regulator
air compressor non return valve
argon hose fitting
characteristics of pressure
diaphragm suppliers
gas regulator
gas used in semiconductor manufacturing
high pressure argon regulator
high pressure flexible hose
how a gas pressure regulator works
how a pressure regulator works
how does a needle valve work
how does pressure regulator work
how do pressure regulators work
how often should pressure relief valves be replaced
how solenoid valves work
humming propane regulator
low pressure regulator
pressure gauge manufacturers
pressure regulator
pressure relief valve vs safety relief valve
propane adjustable pressure regulator
purpose of flame arrester
relief vs safety valve
safety relief valve vs pressure relief valve
safety relief valve vs safety valve
safety valve and relief valve
safety valve and relief valve difference
safety valve vs pressure relief valve
solenoid valve for ammonia gas 1 inch pipe
solenoid water valve
stainless pressure regulator
stainless steel 1/4 in. pressure gauge fitting - 3/8 qc
two stage pressure regulator
water solenoid valve 24v
what is a gas pressure regulator
Recommended Products
-
High Purity Configurable Systems VMB Valve Manifold Box JW-200-VMB-C & JW-100-VMB-C
-
767LP Port Connector Ultra High Purity VCR Metal Gasket Face Seal Tube Fittings
-
771L Male Run Tee | Stainless Steel High Quality High Purity Male Run Tee Branch Tee Pipe Fittings
-
DPR1 Ultra High Purity Two Stage Dual Stage Pressure Reducing Regulator Semiconductor Grade Regulators
-
T-BOX JW-TB-C Special Gas Delivery System Gas Valve Manifold Boxes
-
772L Male Branch Tee | Stainless Steel High-Purity Tube Fitting Male Branch Tee
-
Long Gland LG Series For Ultra High Purity Gas And Chemical Delivery Systems
-
Pressure Control Panels For High Purity Gas Control System JSP-3AE Series From Pressure Control Panels Suppliers And Manufacturer