Blog
Jewellok is a professional pressure regulator and valve manufacturer and supplier.
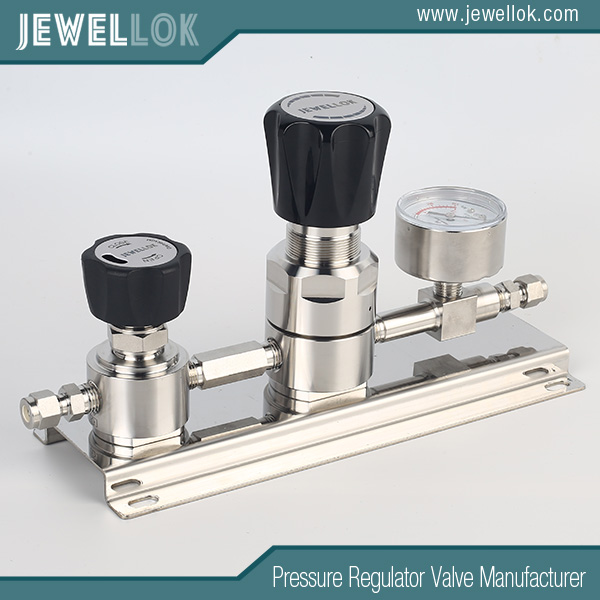
The Key Role Of Ultra-High Purity Pressure Regulators In The Semiconductor Industry
- Pressure Regulator Valve Manufacturer
- 3000PSI Nitrogen Panel Mount Pressure Regulator, Brass Wall Mount Pressure Regulator, Dual stage ultra high purity gas regulators, High-Flow Manual Gas Pressure Regulators, laboratory pressure regulators, Panel Mount Pressure Regulator, Panel mounted pressure regulator with pressure gauge, Pressure instruments for semiconductor manufacturing, Pressure regulator manufacturers, Single-Stage Ultra High-Purity Semiconductor Grade Regulator, Surface mount pressure regulator, UHP Ultra High Purity Gas Regulator Panels Manifolds, Ultra High Purity Gas Regulators, Ultra High Purity Pressure Regulators, Ultra High Purity Single Stage High Flow Regulator, Ultra-High Purity Surface Mount Tied-diaphragm Pressure Regulator
- No Comments
The Key Role Of Ultra-High Purity Pressure Regulators In The Semiconductor Industry
Introduction
The semiconductor industry is the cornerstone of modern scientific and technological development, and its products are widely used in computers, communications, consumer electronics, automotive electronics, medical equipment and other fields. The semiconductor manufacturing process has extremely high requirements for the purity of the environment and the precise control of process parameters. Among them, gas pressure regulation is one of the most important links in semiconductor manufacturing. As a core component in the gas delivery system, the ultra-high purity pressure regulator (Ultra-High Purity Pressure Regulator, UHP Regulator) plays an irreplaceable role in ensuring gas purity, stability and precise control. This article will explore the importance of ultra-high purity pressure regulators in the semiconductor industry in depth, and analyze its technical principles, application scenarios and future development trends through reasoning and in-depth thinking.
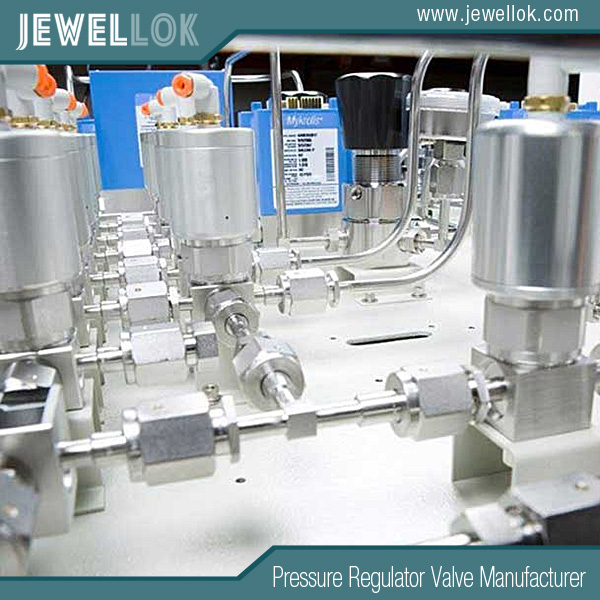
Extreme requirements for gas purity in semiconductor manufacturing
The semiconductor manufacturing process involves multiple key steps, such as photolithography, etching, thin film deposition, ion implantation, etc. These steps have extremely high requirements for gas purity and pressure control. For example:
Gas purity requirements: Gases used in semiconductor manufacturing (such as nitrogen, argon, hydrogen, oxygen, etc.) must reach ultra-high purity (usually 99.9999% or higher). Any trace impurities (such as moisture, oxygen, hydrocarbons, etc.) will cause wafer defects and affect device performance.
Pressure control accuracy: During film deposition and etching, slight fluctuations in gas pressure will affect the uniformity and repeatability of the process, which in turn affects the performance and yield of the chip.
Chemical stability: Gases used in semiconductor manufacturing are often corrosive or highly active (such as hydrogen fluoride, chlorine, etc.), so the pressure regulator must be able to withstand chemical erosion by these gases.
Ultra-high purity pressure regulators are designed to meet these extreme requirements. It not only ensures that the gas maintains ultra-high purity during delivery, but also achieves precise pressure control, while having excellent chemical stability and durability.
Technical principle of ultra-high purity pressure regulators
The design and working principle of ultra-high purity pressure regulators embody the combination of precision engineering and materials science. The following is an in-depth analysis of its core technologies and principles:
1. Material selection
The materials of ultra-high purity pressure regulators must meet the following requirements:
High cleanliness: The surface of the material must be specially treated (such as electrolytic polishing, passivation) to reduce gas adsorption and contamination.
Corrosion resistance: The material must be able to withstand the erosion of corrosive gases, usually stainless steel (such as 316L), nickel-based alloys or special coating materials.
Low permeability: The material must have low gas permeability to prevent external impurities from entering the system.
2. Sealing technology
Sealing is the key to ensuring gas purity. Ultra-high purity pressure regulators usually use metal seals or perfluoroelastomer seals to avoid possible contamination caused by traditional rubber seals.
3. Precision pressure control
Ultra-high purity pressure regulators achieve precise control of pressure through precision springs and diaphragm structures. Its core components include:
Sensing diaphragm: used to sense gas pressure changes.
Adjusting spring: adjust the valve opening according to pressure changes.
Valve assembly: control gas flow to ensure stable output pressure.
4. Flow channel design
The flow channel design of ultra-high purity pressure regulators usually adopts a straight-through or angle structure to reduce gas stagnation and dead zones, thereby reducing the risk of contamination.
Application scenarios of ultra-high purity pressure regulators in semiconductor manufacturing
Ultra-high purity pressure regulators play a key role in multiple links of semiconductor manufacturing. The following is an in-depth analysis of several typical application scenarios:
1. Thin film deposition
During chemical vapor deposition (CVD) and physical vapor deposition (PVD), the stability of gas pressure directly affects the thickness and uniformity of the film. Ultra-high purity pressure regulators ensure the uniformity and consistency of thin film deposition by precisely controlling gas pressure.
2. Etching process
During dry etching, the pressure and flow rate of etching gas must be precisely controlled to ensure the accuracy of etching rate and pattern. Ultra-high purity pressure regulators can provide stable gas pressure, thereby improving the repeatability of etching process.
3. Ion implantation
During ion implantation, the purity and pressure of doping gas have an important influence on doping concentration and distribution. Ultra-high purity pressure regulators can ensure the purity and pressure stability of doping gases, thereby improving the accuracy of ion implantation.
4. Photolithography process
During the photolithography process, the purity and pressure of protective gases (such as nitrogen) have an important impact on the performance of photoresists and pattern resolution. Ultra-high purity pressure regulators can provide a stable protective gas environment, thereby improving the yield of photolithography processes.
Future development trends of ultra-high purity pressure regulators
With the continuous advancement of semiconductor technology, ultra-high purity pressure regulators are also facing new challenges and opportunities. The following is a deep thinking on future development trends:
1. Higher purity and stricter control requirements
With the continuous reduction in the size of semiconductor devices (such as 3nm and below nodes), the requirements for gas purity and pressure control will be more stringent. Future ultra-high purity pressure regulators need to further improve cleanliness and control accuracy.
2. Intelligence and digitalization
With the development of Industry 4.0 and smart manufacturing, ultra-high purity pressure regulators will gradually develop in the direction of intelligence and digitalization. For example, integrated sensors and Internet of Things technology to achieve real-time monitoring and remote control.
3. Application of new materials and new processes
In the future, ultra-high purity pressure regulators may adopt more new materials (such as ceramics, composite materials) and advanced manufacturing processes (such as 3D printing) to improve performance and reduce costs.
4. Environmental protection and sustainable development
With the increase of environmental awareness, the design and manufacture of ultra-high purity pressure regulators will pay more attention to environmental protection and sustainable development. For example, recyclable materials and low-energy manufacturing processes are used.
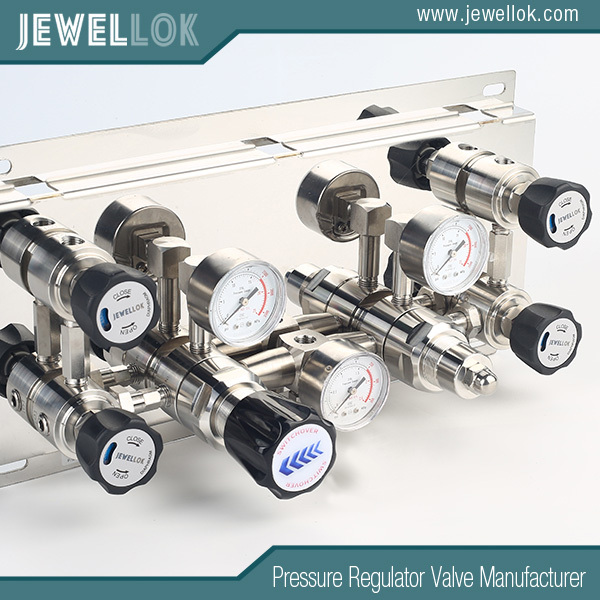
Conclusion
As a key component in semiconductor manufacturing, ultra-high purity pressure regulators play an irreplaceable role in ensuring gas purity, stability and precise control. Its technical principles and application scenarios reflect the high combination of precision engineering and materials science. With the continuous advancement of semiconductor technology, ultra-high purity pressure regulators will face higher technical requirements and broader development space. Through continuous innovation and technological upgrading, ultra-high purity pressure regulators will continue to provide strong support for the development of the semiconductor industry.
In the future, ultra-high purity pressure regulators will not only need to meet higher performance requirements, but also need to adapt to the trend of intelligence, digitalization and environmental protection. Only through continuous technological breakthroughs and innovations can we take the lead in the fierce competition in the global semiconductor industry and contribute to the advancement of human science and technology.
For more about the key role of ultra-high purity pressure regulators in the semiconductor industry, you can pay a visit to Jewellok at https://www.jewellok.com/semiconductor/ for more info.
Recent Posts
Tags
Recommended Products
-
Stainless Steel Ultra Clean Welding Joint Fittings TW Series TRW Series & CW Series
-
763L Stainless Steel High Purity Pressure Reducing Union Fittings And Tubing Pressure Reducing Valve Adjustment
-
High Purity Chemical Dispense System & Packing System For Semiconductors JW-200L-CDM & JW-1000L-CDM
-
765L Stainless Steel Union Elbow Reducing High Purity Fitting Tubing Extension Tubing Connection
-
764LR Stainless Steel 316 Reducing Tee UHP Fitting Automatic Buttweld Reducing Tee
-
739 High Purity LMR Male Adapter Tube To Pipe Fittings And Adapters
-
DPR1 Ultra High Purity Two Stage Dual Stage Pressure Reducing Regulator Semiconductor Grade Regulators
-
775L Bulkhead Reducing Union | Stainless Steel High Purity Double Ferrule Bulkhead Reducing Unions