Blog
Jewellok is a professional pressure regulator and valve manufacturer and supplier.
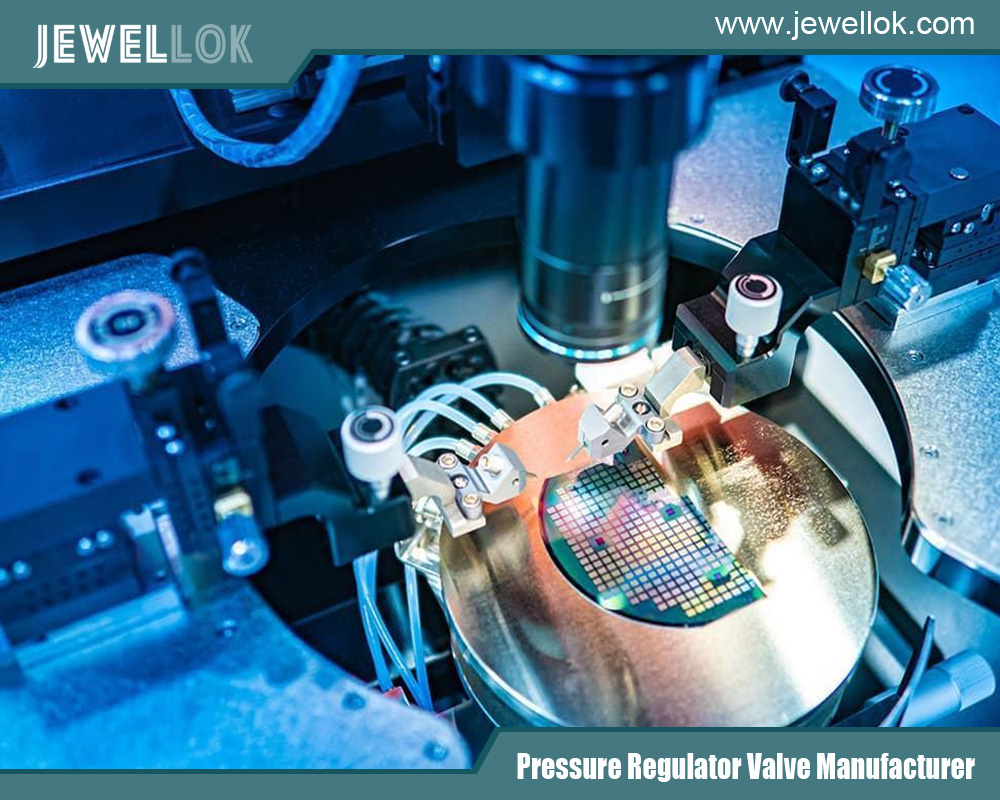
The Influence of Diaphragm Material and Structure on the Performance of Ultra High Purity Diaphragm Valves
- Pressure Regulator Valve Manufacturer
- 1inch of water, 6mm compression fitting, air compressor non return valve, argon hose fittings, compression fitting 6mm, electric water valve 12v, ferrule connector, fire arrestor, gas semiconductor, high purity regulators, how a gas pressure regulator works, how a pressure regulator works, how do pressure regulators work, how do regulators work, how often should pressure relief valves be replaced, humming propane regulator, male fitting for argon hose, oxygen cylinder manifold, pressure regulator valve leaking, pressure relief valve vs safety valve, propane adjustable pressure regulator, propane manifold with valves, purpose of flame arrester, regulator valve alibaba international market, relief valve safety valve difference, safety relief valve vs safety valve, safety valve vs pressure relief valve, second stage propaneregulator, timer water valve, two stage pressure regulator, two stage pressure regulator manufacturer, two stage pressure regulator supplier, Ultra High Purity Diaphragm Valves, ultra high purity diaphragm valves hotsale, ultra high purity diaphragm valves manufacturer, ultra high purity diaphragm valves supplier, ultra high purity diaphragm valves wholesale
- No Comments
The Influence of Diaphragm Material and Structure on the Performance of Ultra High Purity Diaphragm Valves
In industries with extremely high requirements for medium purity, such as semiconductors, pharmaceuticals, and food and beverage, ultra high purity diaphragm valves play a crucial role. As a core component for controlling the on-off and flow rate of fluids, the performance of diaphragm valves is directly related to the stability of the production process, product quality, and the safety of the system. The diaphragm, as the core element of the diaphragm valve, its material properties and structural design largely determine the overall performance of the valve, including key indicators such as service life, sealing performance, and corrosion resistance. An in-depth exploration of the influence of the diaphragm’s material and structure on the performance of ultra high purity diaphragm valves is of great practical significance for optimizing valve design, improving system operation efficiency, and reducing production costs.
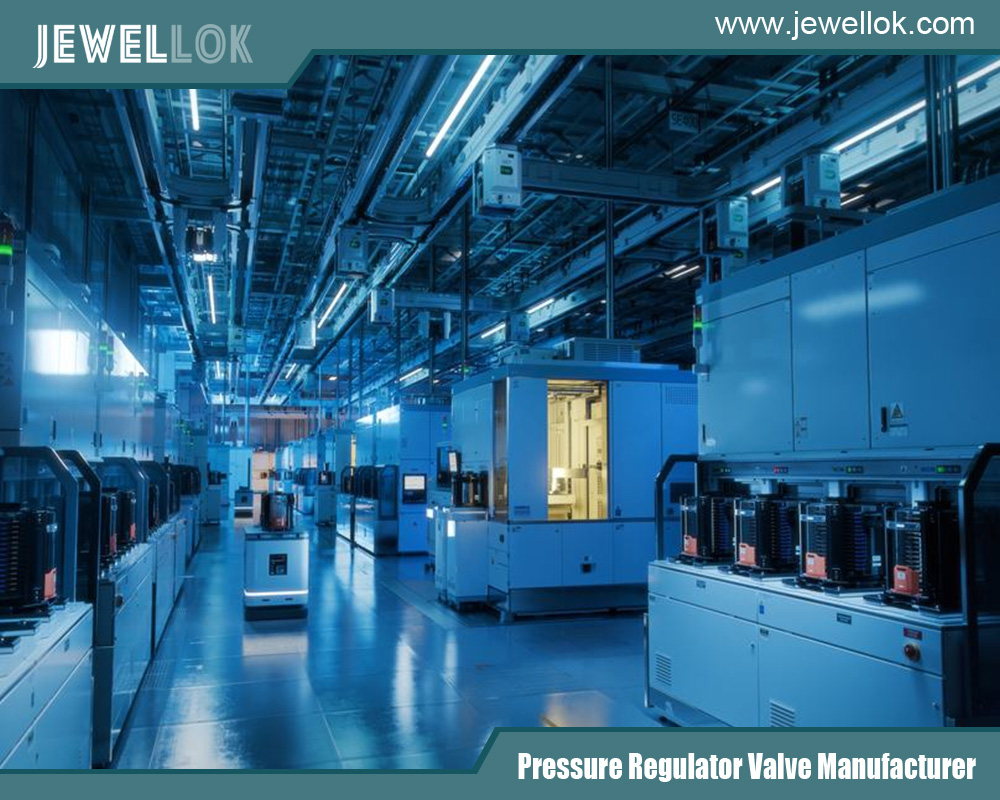
Working Principle and Structural Overview of Ultra High Purity Diaphragm Valves
Working Principle
Ultra high purity diaphragm valves control the flow of fluids through the deformation of the diaphragm. When the diaphragm is in the closed state, it closely adheres to the valve seat, preventing the fluid from passing through; when the diaphragm is opened, it moves away from the valve seat, allowing the fluid to flow inside the valve body. The movement of the diaphragm is usually achieved by manual, pneumatic, or electric driving methods to meet the operation requirements under different working conditions.
Structural Composition
Ultra high purity diaphragm valves mainly consist of components such as the valve body, diaphragm, valve cover, and driving device. The valve body serves as the outer shell of the valve, providing a flow channel for the fluid and bearing the system pressure; the diaphragm is the key component of the valve, dividing the internal space of the valve body into upper and lower parts, playing the role of isolating the medium and controlling the fluid; the valve cover is used to fix the diaphragm and the driving device and ensure the sealing of the valve; the driving device is responsible for providing power to make the diaphragm open and close.
The Key Role of the Diaphragm in the Valve
The diaphragm plays a vital role in ultra high purity diaphragm valves. On the one hand, as a sealing element, it prevents the leakage of the medium and ensures the sealing and safety of the system; on the other hand, it separates the fluid inside the valve body from the external driving components and the atmospheric environment, avoiding the contamination of the fluid and ensuring the ultra high purity of the medium. In addition, the flexibility and elasticity of the diaphragm enable it to deform flexibly under the action of the driving device, realizing the rapid opening and closing of the valve to meet the requirements of flow control in the production process.
The Influence of Diaphragm Material on the Performance of the Valve
Common Diaphragm Materials and Their Characteristics
- Polytetrafluoroethylene (PTFE): It has excellent chemical stability and hardly reacts with any chemical substances. It is resistant to strong acids, strong alkalis, and various organic solvents; it has an extremely low coefficient of friction, making the movement of the diaphragm less resistant and the operation smoother; it has good high-temperature resistance and can work stably at high temperatures for a long time. The working temperature range is usually from -200°C to 260°C; however, its mechanical strength is relatively low, and it is easily damaged by external forces.
- Perfluoroalkoxyalkane (PFA): Its chemical stability is equivalent to that of PTFE, and it also has excellent corrosion resistance; compared with PTFE, PFA has better molding and processing performance and can be made into more complex shapes and structures; its mechanical properties have also been improved, with better creep resistance and wear resistance; the cost is relatively high, which limits its wide application in some cost-sensitive fields.
- Fluororubber (FKM): It has outstanding chemical corrosion resistance and has good tolerance to most chemical substances; it has good elasticity and flexibility, which can compensate for the manufacturing and installation errors of valve components to a certain extent and ensure good sealing performance; it has excellent high-temperature resistance and can maintain stable performance at high temperatures. The general working temperature range is from -20°C to 200°C; however, its low-temperature resistance is relatively poor, and it may become hard and brittle in a low-temperature environment, affecting the normal operation of the valve.
The Influence of Material Characteristics on Service Life
- Corrosion Resistance: The diaphragm is in long-term contact with various corrosive media. If the corrosion resistance of the material is insufficient, it will lead to corrosion, swelling, aging, etc. of the diaphragm surface, thereby reducing the strength and elasticity of the diaphragm and shortening its service life. For example, in the semiconductor industry, etching agents containing strong corrosive acids are often used. If the diaphragm material cannot effectively resist the corrosion of these acids, it will be damaged quickly.
- Wear Resistance: During the opening and closing process of the valve, there will be friction between the diaphragm and the valve seat; particulate impurities in the fluid may also cause wear to the diaphragm surface. A diaphragm material with good wear resistance can reduce the impact of this friction and wear and extend the service life of the diaphragm. For example, in some suspension conveying systems in the pharmaceutical industry, a diaphragm with good wear resistance can better cope with the erosion of particles.
- Temperature Resistance: Changes in the working temperature will have a significant impact on the performance of the diaphragm material. Excessively high temperatures may cause the material to soften, deform, and decompose, while excessively low temperatures may make the material brittle and lose its elasticity. Only by selecting a diaphragm material with a suitable temperature resistance range can the diaphragm maintain good performance at different working temperatures and extend its service life. For example, in the high-temperature sterilization process of the food and beverage industry, the diaphragm needs to work stably in a high-temperature environment.
The Influence of Material Characteristics on Sealing Performance
- Flexibility and Elasticity: A diaphragm material with good flexibility and elasticity can closely adhere to the valve seat when closed, forming an effective sealing surface and preventing the leakage of the medium. Even if there is a certain degree of unevenness on the valve seat surface, the diaphragm can be compensated by its own deformation to ensure the sealing performance. For example, the high elasticity of the fluororubber diaphragm enables it to better adapt to the shape of the valve seat during sealing.
- Chemical Stability: A diaphragm material with good chemical stability will not react chemically with the medium, avoiding changes in material performance and sealing failure caused by chemical reactions. In the pharmaceutical industry, the purity and stability of the medium are of great importance. Using a diaphragm material with high chemical stability can ensure that the drug production process is not contaminated and maintain good sealing performance.
- Low Permeability: The low permeability of the diaphragm material can prevent the diffusion of medium molecules through the diaphragm, thus ensuring the reliability of the seal. For some volatile and permeable media, such as organic solvents, a diaphragm material with low permeability is particularly important. For example, in the transportation of electronic chemicals, preventing the leakage of the medium is crucial for ensuring product quality and production safety.
The Influence of Diaphragm Structure on the Performance of the Valve
Common Diaphragm Structure Types
- Flat Diaphragm: It has a simple structure and is in a planar shape, which is the most basic diaphragm structure form. The manufacturing process is relatively simple, and the cost is low; however, when the flat diaphragm bears pressure, the force distribution is uneven, and stress concentration is likely to occur at the edges and the center, leading to diaphragm damage.
- Domed Diaphragm: It has a certain arc and is in a domed structure. This structure enables the diaphragm to evenly distribute the force across the entire diaphragm when under pressure, reducing the stress concentration phenomenon and improving the pressure resistance of the diaphragm; compared with the flat diaphragm, the deformation of the domed diaphragm is smaller under the same pressure, which can better maintain the sealing performance of the valve; the manufacturing process is relatively complex, and the cost is higher.
- Corrugated Diaphragm: Its surface has a corrugated structure, which increases the flexibility and deformability of the diaphragm. The corrugated structure enables the diaphragm to produce a large deformation under a small external force, thus realizing the rapid opening and closing of the valve; when under pressure, the corrugated diaphragm can adapt to the pressure change through the compression and extension of the corrugations and has good pressure resistance; due to the complex structure, the manufacturing difficulty of the corrugated diaphragm is relatively large, and the requirements for the material are also higher.
The Influence of Structural Design on Service Life
- Stress Distribution: A reasonable diaphragm structural design can make the stress evenly distributed on the diaphragm, avoiding premature damage to the diaphragm caused by local stress concentration. For example, the domed diaphragm and the corrugated diaphragm effectively disperse the stress through their special structural designs, extending the service life of the diaphragm. However, due to the uneven stress distribution of the flat diaphragm, problems such as cracking are likely to occur in weak parts, shortening the service life.
- Fatigue Strength: During the frequent opening and closing process of the valve, the diaphragm will be subjected to repeated stretching and compression, which is likely to cause fatigue damage. A diaphragm with a good structural design can improve its fatigue strength, reduce the generation and propagation of fatigue cracks, and thus extend its service life. For example, a corrugated diaphragm with optimized corrugation shape and size can effectively reduce the fatigue stress and improve the fatigue life.
The Influence of Structural Design on Sealing Performance
- Sealing Surface Fit: The structural design of the diaphragm directly affects the fit of the sealing surface between the diaphragm and the valve seat. For example, when the flat diaphragm is closed, if there are slight unevenness on the valve seat surface, it may lead to an improper fit of the sealing surface and leakage; while the domed diaphragm and the corrugated diaphragm can better adapt to the shape of the valve seat and form a tighter sealing surface when closed, improving the sealing performance.
- Deformation Characteristics: The deformation characteristics of the diaphragm during operation also have an important impact on the sealing performance. A reasonable structural design should enable the diaphragm to deform flexibly during the opening and closing process and maintain stable sealing performance in the closed state. For example, the good flexibility of the corrugated diaphragm enables it to deform rapidly when opened, reducing the fluid resistance; when closed, it can closely adhere to the valve seat to ensure reliable sealing.
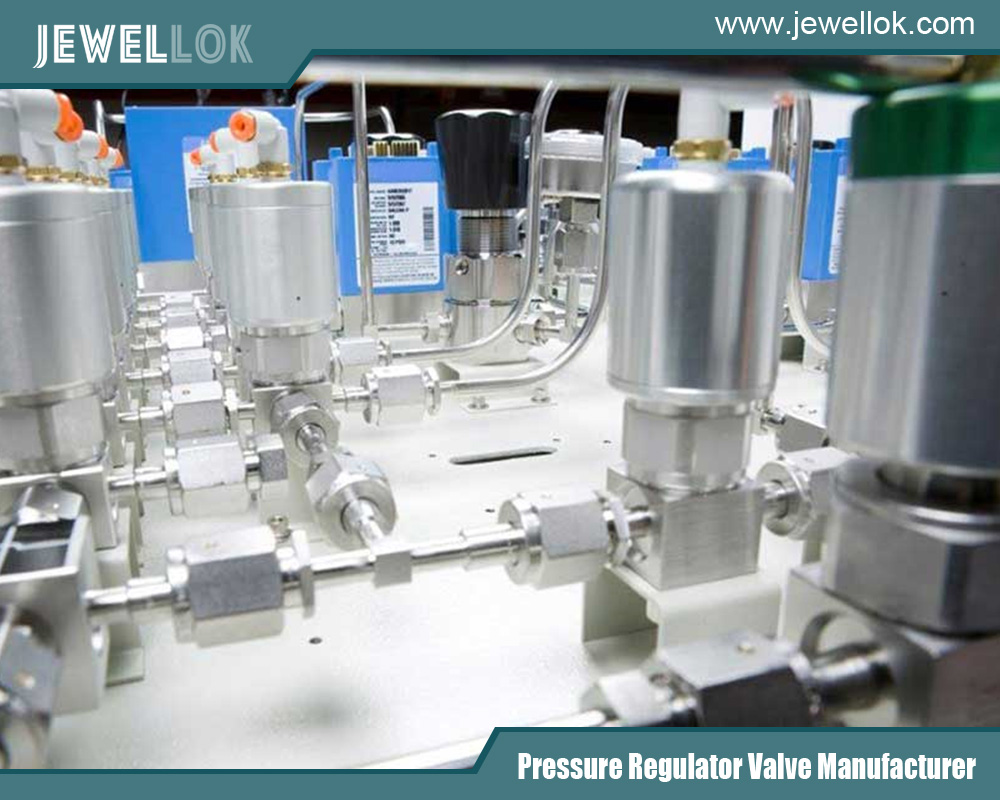
Conclusion and Outlook
Research Summary
The material and structure of the diaphragm have a crucial impact on the performance of ultra high purity diaphragm valves. Different diaphragm materials have their own unique characteristics, and these characteristics largely determine the service life and sealing performance of the valve. At the same time, a reasonable diaphragm structural design can optimize the stress distribution, improve the fatigue strength, and thus extend the service life of the valve; a good structural design can also improve the fit of the sealing surface between the diaphragm and the valve seat and enhance the sealing performance. In practical applications, it is necessary to comprehensively consider the selection of diaphragm materials and structures according to specific working conditions to ensure that the ultra high purity diaphragm valves can operate stably and reliably.
Future Development Directions
With the continuous improvement of the requirements for the transportation of ultra high purity media in industries such as semiconductors and pharmaceuticals, the research and development of ultra high purity diaphragm valves will also develop towards higher performance and greater reliability. In terms of diaphragm materials, new materials with more excellent comprehensive performance may be developed in the future, such as higher corrosion resistance, wear resistance, temperature resistance, as well as better flexibility and elasticity, while reducing the material cost. In terms of diaphragm structural design, with the help of advanced computer-aided design (CAD) and finite element analysis (FEA) technologies, more precise structural optimization will be achieved, further improving the performance and reliability of the valve. In addition, with the development of intelligent manufacturing technology, the production and manufacturing process of ultra high purity diaphragm valves will also become more intelligent and automated to meet the market demand for high-quality valves.
For more about the influence of diaphragm material and structure on the performance of ultra high purity diaphragm valves, you can pay a visit to Jewellok at https://www.jewellok.com/ for more info.
Recent Posts
Tags
Recommended Products
-
JR1300 Series Ultra High Purity Single Stage Regulator High Flow Line Regulator For Ultra High Purity Intermediate Flow
-
775L Bulkhead Reducing Union | Stainless Steel High Purity Double Ferrule Bulkhead Reducing Unions
-
Flow Control Stainless Steel Low Pressure Manual Diaphragm Valve For High Purity And Ultra High Purity Gases
-
Stainless Steel Ultra High Purity (UHP) High Pressure Manual Diaphragm Valve
-
Fully Automated Gas Cabinet For Precise UHP Gas Delivery And High Purity Gas Delivery Systems JW-300-GC
-
772L Male Branch Tee | Stainless Steel High-Purity Tube Fitting Male Branch Tee
-
316L Stainless Steel Tube Butt Weld Reducing Fittings Union Reducer RW Series Ultrahigh Purity Process
-
Fully Automated Gas Cabinet Gas Rack Gas Delivery Systems JW-300-GR