Blog
Jewellok is a professional pressure regulator and valve manufacturer and supplier.
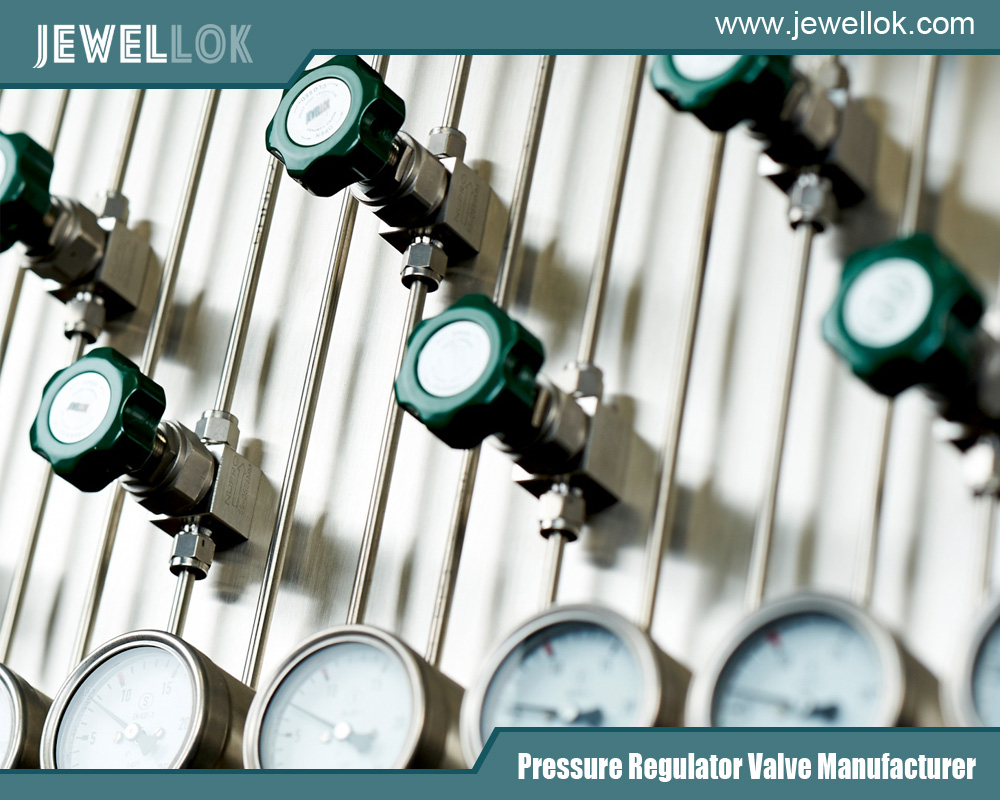
The Difference Between High Purity Regulator And Ultra High Purity Regulator
- Pressure Regulator Valve Manufacturer
- Brass High Purity Single Stage Pressure Regulators, High Purity Gas Regulators, High Purity Single Stage Corrosion Resistant Regulator, High Purity Single Stage Medium Flow Line Regulator, Single Stage Compact Regulator for Ultra High Purity, Single Stage High Purity Gas Regulators, Single Stage Regulator for Ultra High Purity, Single-stage diaphragm pressure regulator, UHP Pressure Regulators, Ultra High Purity Dual Stage Pressure Reducing Regulator, Ultra High Purity Gas Regulators, Ultra High Purity Regulators, Ultra High Purity Single Stage Medium Flow Regulator, Ultra High Purity Single Stage Pressure Regulator, Ultra High Purity Stainless Steel Gas Regulator, Ultra High Purity Stainless Steel Single Stage Regulator, Ultra High Purity Two Stage Pressure Reducing Regulator, Ultra-High Purity Line Gas Regulator
- No Comments
The Difference Between High Purity Regulator And Ultra High Purity Regulator
Introduction
In modern industry and high-tech fields, the control of gas purity is crucial. Whether it is semiconductor manufacturing, biomedicine, or high-precision laboratory research, the purity of gas directly affects the quality of products and the reliability of experiments. Therefore, as a key device for controlling gas purity and pressure, the performance and quality of gas regulators are particularly important. This article will explore the difference between high purity regulators and ultra high purity regulators, and analyze their advantages and limitations in different application scenarios.
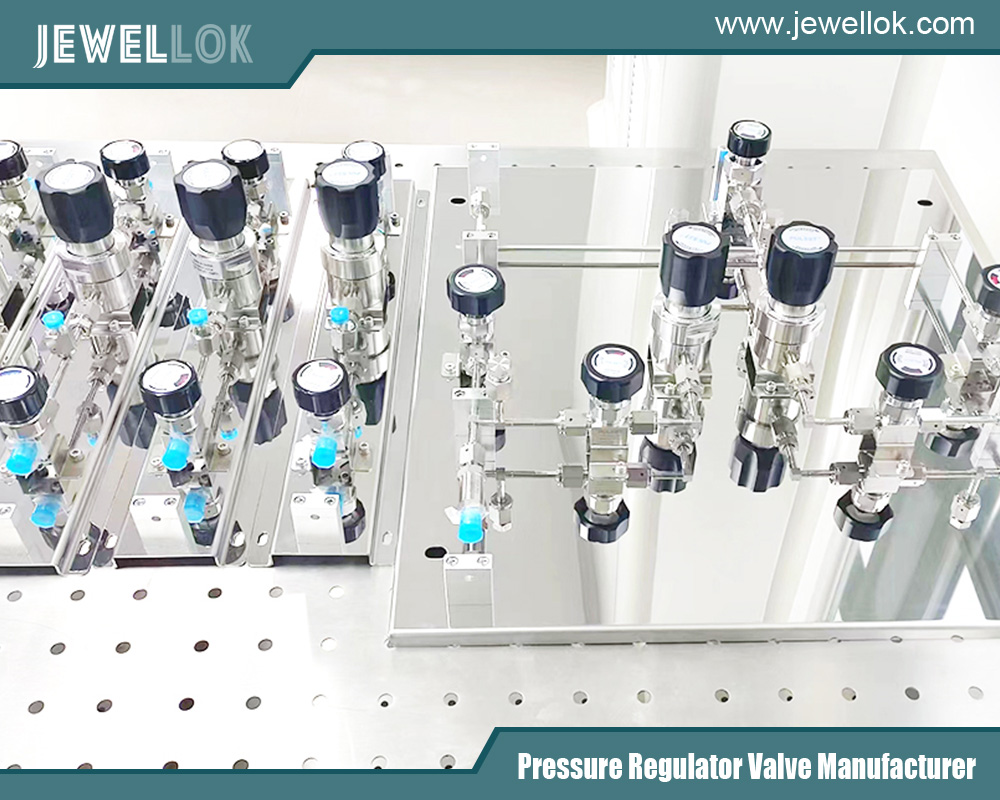
1. Definition and standard of gas purity
Before discussing high purity regulators and ultra high purity regulators, we first need to clarify the definitions of “high purity” and “ultra high purity”. Gas purity is usually expressed in percentage or parts per million (ppm). High purity gas usually refers to gas with a purity of 99.999% (5N) or more, while ultra high purity gas refers to gas with a purity of 99.9999% (6N) or even higher.
Different industries and applications have different requirements for gas purity. For example, the gases used in semiconductor manufacturing processes usually need to reach ultra-high purity, because even trace amounts of impurities can cause chip performance degradation or failure. In some laboratory studies, high-purity gases may be sufficient to meet experimental needs.
2. Characteristics and applications of high-purity regulators
Structure and materials
High-purity regulators are usually made of stainless steel, brass or other corrosion-resistant materials, and the internal surface is specially treated to reduce the reaction between gas and materials. Its internal structure is designed to reduce dead volume and dead corners, thereby reducing the risk of gas retention and contamination.
Performance characteristics
The main feature of high-purity regulators is that they can provide stable output pressure and high gas purity. They are usually equipped with precision pressure control valves and filters to ensure the purity and pressure stability of the output gas. High-purity regulators have a low leakage rate and can effectively prevent the infiltration of external air or impurities.
Application scenarios
High-purity regulators are widely used in laboratory research, medical equipment, food processing and other fields. In these applications, gas purity requirements are high, but usually do not need to reach ultra-high purity levels. For example, in medical oxygen supply systems, high-purity regulators can ensure the purity and pressure stability of oxygen, thereby ensuring patient safety.
3. Characteristics and applications of ultra-high purity regulators
Structure and materials
Ultra-high purity regulators are more stringent in material selection and structural design. They are usually made of high-grade stainless steel or special alloys, and the internal surface is electrolytically polished or chemically polished to further reduce the reaction and adsorption of gas and materials. The internal structure design of ultra-high purity regulators is more sophisticated, and dead volume and dead corners are almost completely eliminated.
Performance characteristics
The main feature of ultra-high purity regulators is that they can provide extremely high gas purity and extremely low leakage rate. They are usually equipped with ultra-precision pressure control valves and multi-stage filtration devices to ensure the purity and pressure stability of the output gas to the extreme. The ultra-high purity regulator has an extremely low leakage rate, which can effectively prevent the infiltration of external air or impurities, and can even handle trace impurities.
Application scenarios
Ultra-high purity regulators are mainly used in semiconductor manufacturing, photovoltaic industry, high-precision laboratory research and other fields. In these applications, gas purity requirements are extremely high, and any trace impurities may lead to a decline in product performance or deviations in experimental results. For example, in the semiconductor manufacturing process, ultra-high purity regulators can ensure the purity and pressure stability of process gases, thereby improving the yield and performance of chips.
4. The difference between high-purity regulators and ultra-high purity regulators
Materials and manufacturing processes
There are significant differences in materials and manufacturing processes between high-purity regulators and ultra-high purity regulators. High-purity regulators usually use standard stainless steel or brass materials, and the internal surface treatment is relatively simple. Ultra-high purity regulators use high-grade stainless steel or special alloys, and the internal surface is electrolytically polished or chemically polished to further reduce the reaction and adsorption of gas and materials.
Internal structure design
The internal structure design of the high-purity regulator is relatively simple, with more dead volume and dead corners, which may cause gas retention and contamination. The internal structure design of the ultra-high purity regulator is more precise, and the dead volume and dead corners are almost completely eliminated, thereby reducing the risk of gas retention and contamination.
Performance parameters
There are significant differences in performance parameters between high-purity regulators and ultra-high purity regulators. High-purity regulators can usually provide gas purity of more than 99.999% (5N) with a low leakage rate. Ultra-high purity regulators can provide gas purity of 99.9999% (6N) or even higher, with extremely low leakage rates.
Application fields
There are significant differences in application fields between high-purity regulators and ultra-high purity regulators. High-purity regulators are mainly used in laboratory research, medical equipment, food processing and other fields, with high gas purity requirements, but usually do not need to reach ultra-high purity levels. Ultra-high purity regulators are mainly used in semiconductor manufacturing, photovoltaic industry, high-precision laboratory research and other fields, with extremely high gas purity requirements, and any trace impurities may lead to a decline in product performance or deviation in experimental results.
5. Considerations for choosing high-purity regulators vs. ultra-high purity regulators
Application requirements
When choosing between high-purity regulators and ultra-high purity regulators, you first need to consider the application requirements. If the application scenario has extremely high gas purity requirements, such as semiconductor manufacturing or high-precision laboratory research, then an ultra-high purity regulator is a better choice. If the application scenario has high gas purity requirements but does not need to reach ultra-high purity levels, such as medical equipment or food processing, then a high-purity regulator may be sufficient.
Cost considerations
Ultra-high purity regulators are more stringent in materials and manufacturing processes, so the cost is usually higher. If the budget is limited and the application scenario does not require extremely high gas purity, then a high-purity regulator may be a more economical choice.
Maintenance and operation
Ultra-high purity regulators are generally more complicated to maintain and operate, and require regular and rigorous cleaning and calibration. If the application scenario has high requirements for equipment maintenance and operation, then this needs to be taken into account.
6. Future development trends
With the continuous advancement of technology, the requirements for gas purity are also increasing. In the future, the demand for ultra-high purity regulators may further increase, especially in the fields of semiconductor manufacturing, photovoltaic industry, and high-precision laboratory research. At the same time, with the advancement of materials science and manufacturing processes, the cost of ultra-high purity regulators may gradually decrease, making them popular in more application scenarios.
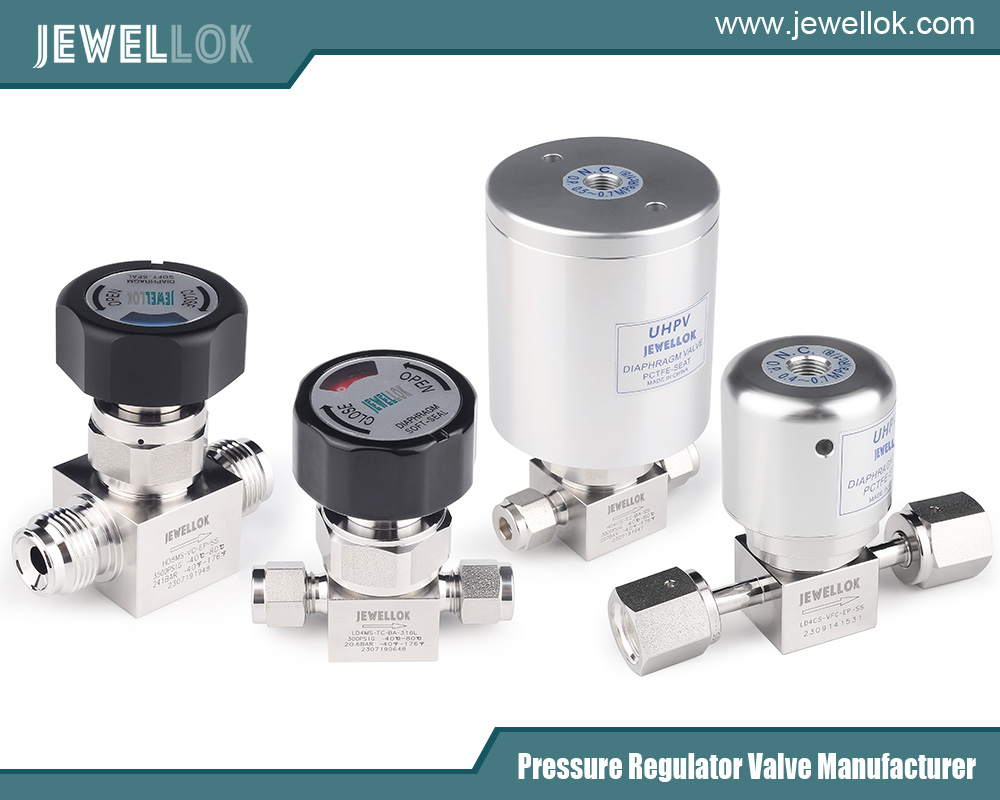
Conclusion
There are significant differences between high-purity regulators and ultra-high purity regulators in materials, structures, performance, and application areas. The choice of which regulator requires a comprehensive evaluation based on specific application requirements, cost considerations, and maintenance operation requirements. With the continuous advancement of science and technology, the demand for ultra-high purity regulators may further increase, and its application prospects in high-end manufacturing and scientific research are broad.
Through the in-depth analysis of this article, readers can better understand the difference between high-purity regulators and ultra-high purity regulators, so as to make more informed choices in practical applications.
For more about the difference between high purity regulator and ultra high purity regulator, you can pay a visit to Jewellok at https://www.jewellok.com/products/ for more info.
Recent Posts
Tags
Recommended Products
-
768LN Stainless Steel Male Pipe Tube Butt Weld Connector And Tube Fittings Supplier
-
770L Female Elbow | Stainless Steel High Purity Weld Fittings Female Micro Elbow Fittings
-
High Purity High Pressure Gas Cylinder Pressure Regulators Pressure Reducing Valve JSR-1E Series
-
772 LF Female Branch Tee | Stainless Steel Tube Fitting Female Branch Tee 1/2 in. Tube OD x 1/2 in. Tube OD x 3/8 in. Female NPT
-
775L Bulkhead Reducing Union | Stainless Steel High Purity Double Ferrule Bulkhead Reducing Unions
-
Stainless Steel High Purity High Temperature Pneumatic Actuated Ball Valves JBV2 Series
-
771LF Female Run Tee | Stainless Steel Tube Fitting Compression Fittings 1/4 In 3-Way Tee Female Run Tee
-
763L Stainless Steel High Purity Pressure Reducing Union Fittings And Tubing Pressure Reducing Valve Adjustment