Blog
Jewellok is a professional pressure regulator and valve manufacturer and supplier.
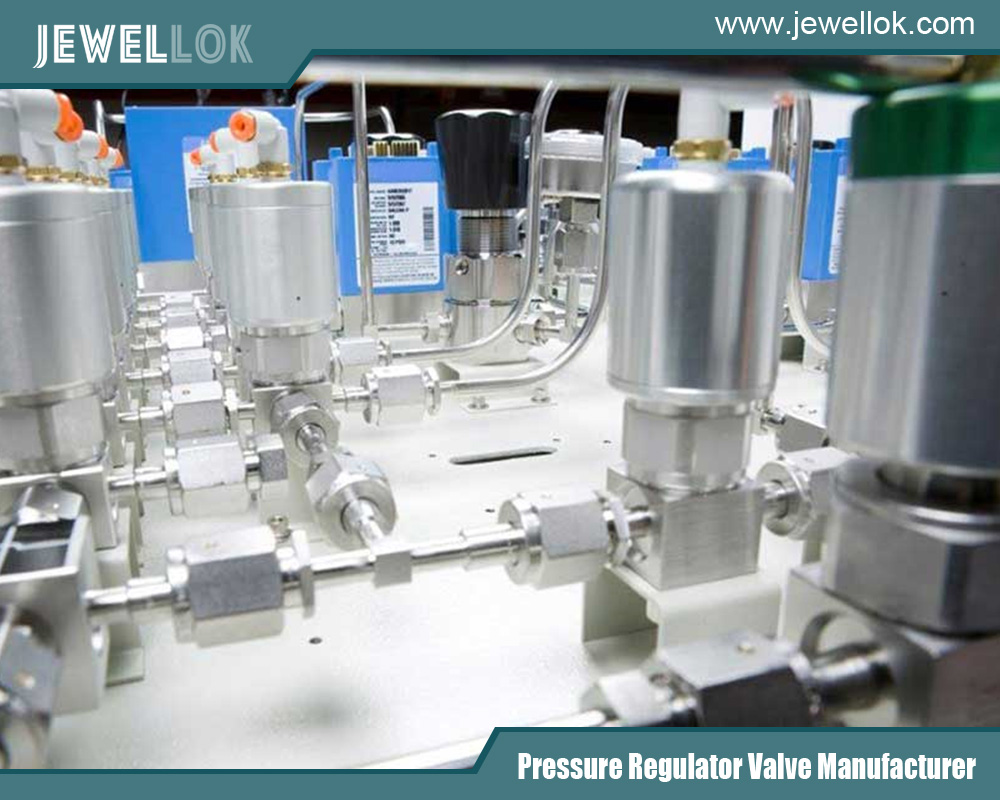
How Does A High-Purity High Flow Nitrogen Regulator Work?
- Pressure Regulator Valve Manufacturer
- High Flow Nitrogen Pressure Regulator, High Flow Nitrogen Regulators, High Flow Pressure Regulators, High Flow Reducing Regulator 6000 psi, High Flow Regulators China, High Flow Regulators Manufacturers, High Pressure 300bar Nitrogen Regulator, High Pressure Multi-Stage Nitrogen Regulator, High pressure regulator for very high flow, High Pressure Single-Stage Nitrogen Regulator, High-Purity High Flow Nitrogen Regulator, nitrogen 0-40 bar high flow pressure regulator, Nitrogen Regulator 2 Stage, Nitrogen Regulator 20/ 40/ 60 Bar High Flow Rate, Nitrogen Regulators, Nitrogen Regulators China, Nitrogen Regulators Manufacturer, Stainless Steel 4000psi High Pressure High Flow Nitrogen Regulator, Ultra High Flow Assist Gas Regulator
- No Comments
How Does A High-Purity High Flow Nitrogen Regulator Work?
Nitrogen is one of the most versatile and widely used gases in industrial, scientific, and medical applications. Its inert properties make it ideal for processes requiring a stable, non-reactive environment, such as semiconductor manufacturing, food preservation, and chemical synthesis. However, delivering nitrogen at the right pressure, purity, and flow rate is critical to ensuring these processes run smoothly. This is where a high-purity, high-flow nitrogen regulator comes into play. But how exactly does this sophisticated device work? In this article, we’ll explore the principles behind its operation, break down its key components, and examine its role in various applications.
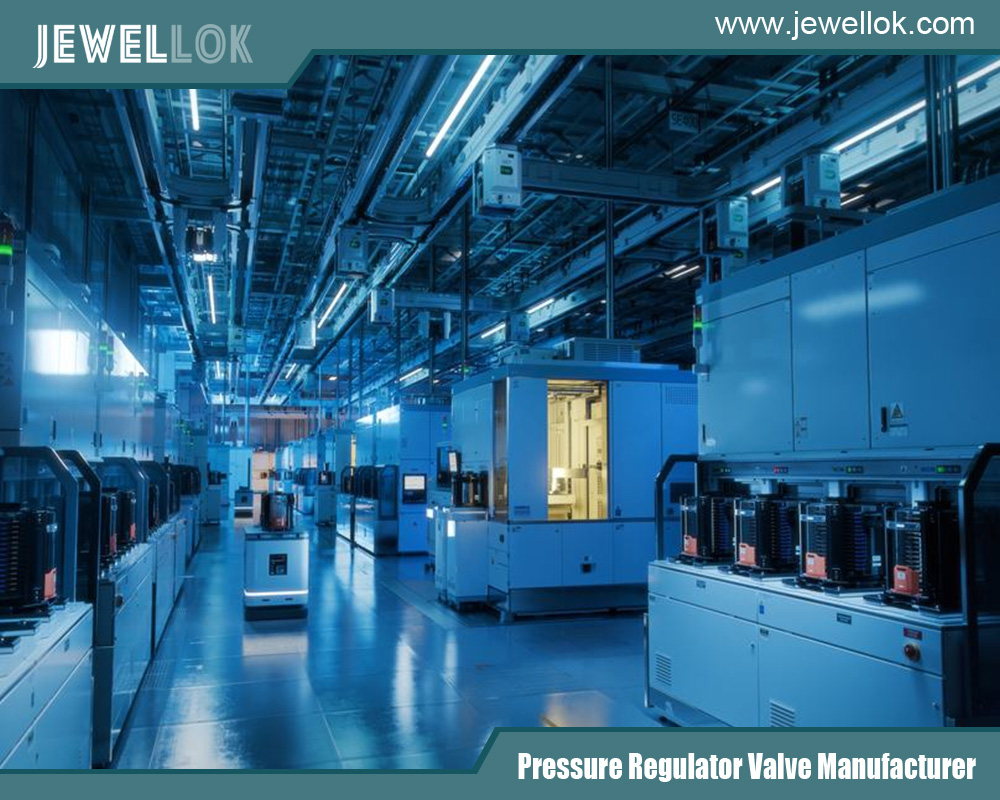
Introduction to nitrogen regulators
A nitrogen regulator is a device designed to control the pressure and flow of nitrogen gas from a high-pressure source—such as a cylinder or a bulk tank—to a level suitable for a specific application. Standard regulators are common in many industries, but high-purity, high-flow nitrogen regulators are specialized tools engineered for scenarios where contamination must be minimized, and large volumes of gas are required. These regulators are essential in fields like electronics manufacturing, pharmaceuticals, and laser cutting, where even trace impurities or inconsistent flow can compromise results.
At its core, a nitrogen regulator reduces the high pressure of stored gas (often exceeding 2000 psi in a cylinder) to a usable level (e.g., 50 psi or less) while maintaining the gas’s purity and delivering it at a high flow rate. To understand how this is achieved, we need to dive into the mechanics of pressure regulation, the design considerations for purity, and the adaptations for high flow.
The Basics of Pressure Regulation
Pressure regulation is governed by a simple principle: balancing forces. Nitrogen stored in a cylinder is under high pressure, determined by the volume of gas compressed into a confined space. When released without control, this gas would exit at an dangerously high pressure and flow rate, making it unusable or unsafe. A regulator steps in to moderate this release.
The fundamental mechanism involves a diaphragm or piston, a spring, and a valve. Here’s a simplified explanation of how it works:
-
High-Pressure Input: Nitrogen enters the regulator from the cylinder through an inlet port.
-
Valve Control: A valve, controlled by the diaphragm or piston, restricts the flow of gas into a low-pressure chamber.
-
Spring and Diaphragm Interaction: The diaphragm (a flexible membrane) or piston responds to the pressure in the low-pressure chamber. A spring applies force to the diaphragm, pushing it against the gas pressure. The user adjusts this spring tension via a knob or handle to set the desired output pressure.
-
Equilibrium: When the downstream pressure matches the spring’s force, the valve partially closes, stabilizing the output. If the downstream pressure drops (e.g., due to increased demand), the spring pushes the diaphragm to open the valve further, allowing more gas through. If pressure rises too high, the valve restricts flow.
-
Output Delivery: The regulated gas exits through an outlet port to the application.
This feedback system ensures a consistent output pressure regardless of fluctuations in the cylinder’s pressure (as it depletes) or downstream demand. However, a high-purity, high-flow regulator builds on this basic design with enhancements to meet stricter requirements.
Design Features for High Purity
In applications like semiconductor fabrication or analytical chemistry, even minute contaminants—such as oxygen, moisture, or hydrocarbons—can ruin processes or skew results. A high-purity nitrogen regulator is designed to prevent such contamination. Here’s how:
-
Material Selection: Components exposed to nitrogen are made from materials like stainless steel or brass with electroless nickel plating. These resist corrosion and minimize outgassing (the release of trapped gases or particles from the material itself). Plastic or rubber components, which might degrade or leach contaminants, are avoided in critical areas.
-
Clean Manufacturing: High-purity regulators are assembled in cleanroom environments to prevent dust, oils, or particulates from adhering to surfaces. They’re often cleaned with specialized solvents and purged with ultra-pure nitrogen before packaging.
-
Sealing Technology: High-quality seals, such as those made from PTFE (Teflon) or other inert materials, ensure no leaks introduce ambient air or contaminants. Metal-to-metal seals may also be used for extreme purity needs.
-
Minimal Dead Volume: The internal design minimizes “dead spaces” where gas could stagnate and accumulate impurities over time.
These features ensure that the nitrogen exiting the regulator retains its original purity, often specified at 99.999% or higher (commonly referred to as “5.0 grade” or better).
Adaptations for High Flow
While purity is critical, some applications demand high flow rates—think laser cutting, where nitrogen is used to blow away molten metal, or large-scale inerting in chemical plants. Standard regulators might choke under such demand, causing pressure drops or inconsistent flow. High-flow nitrogen regulators address this through several key adaptations:
-
Larger Orifices and Pathways: The valve and internal passages are oversized to allow greater gas volume to pass without restriction. This reduces turbulence and pressure loss.
-
Robust Diaphragm or Piston: A larger, more durable diaphragm (or a piston in some designs) can handle the forces associated with high flow while maintaining precise control.
-
Dual-Stage Regulation: Many high-flow regulators use a two-stage design. The first stage reduces cylinder pressure to an intermediate level (e.g., 200 psi), and the second stage fine-tunes it to the final output (e.g., 50 psi). This improves stability under high demand and compensates for declining cylinder pressure.
-
Flow Capacity Specifications: Manufacturers rate these regulators in terms of flow capacity, often measured in standard cubic feet per minute (SCFM) or liters per minute (LPM). A high-flow regulator might deliver 100 SCFM or more, compared to 10-20 SCFM for a standard model.
These modifications ensure the regulator can supply large volumes of nitrogen without sacrificing pressure control or purity.
Key Components of a High-Purity High-Flow Nitrogen Regulator
To bring this all together, let’s examine the main components and their roles:
-
Inlet Connection: A threaded or flange connection (e.g., CGA 580 for nitrogen cylinders in the U.S.) links the regulator to the gas source. It includes a filter or screen to block debris.
-
Pressure Gauges: Two gauges are typical—one for inlet pressure (showing cylinder status) and one for outlet pressure (indicating regulated output). High-purity models use gauges with stainless steel internals.
-
Adjustment Knob or T-Handle: This allows the user to set the output pressure by compressing the spring.
-
Diaphragm or Piston Assembly: The heart of the regulator, responding to pressure changes to modulate the valve.
-
Poppet Valve: A spring-loaded valve that opens or closes to control gas flow. In high-purity designs, it’s polished to reduce particle generation.
-
Relief Valve: A safety feature that vents excess pressure if the regulator fails or downstream pressure spikes.
-
Outlet Port: Where the regulated gas exits, often with fittings for tubing or hoses compatible with the application.
Each component is precision-engineered to work in harmony, balancing purity, flow, and safety.
Applications of High-Purity High-Flow Nitrogen Regulators
The unique capabilities of these regulators make them indispensable across industries:
-
Electronics Manufacturing: In semiconductor production, nitrogen purges moisture and oxygen from chambers during wafer processing. High flow ensures rapid purging, while purity prevents defects.
-
Laser Cutting: High-pressure nitrogen (up to 400 psi) at high flow rates acts as an assist gas, expelling molten metal and preventing oxidation on cut edges.
-
Pharmaceuticals: Nitrogen blankets reactors or fills vials to prevent oxidation of sensitive compounds. High purity is non-negotiable here.
-
Food and Beverage: High-flow nitrogen preserves freshness in packaging by displacing oxygen, with purity ensuring no off-flavors or contamination.
-
Research Laboratories: Analytical instruments like gas chromatographs require consistent, pure nitrogen at moderate to high flows for carrier or purge gas.
These examples highlight the regulator’s versatility and the critical role it plays in modern technology and industry.
Installation and Operation Tips
Using a high-purity, high-flow nitrogen regulator effectively requires proper setup and handling:
-
Purge the System: Before connecting, briefly open the cylinder valve to blow out dust or debris from the inlet, then attach the regulator securely.
-
Check Compatibility: Ensure the regulator’s pressure and flow ratings match the application and cylinder specifications.
-
Adjust Gradually: Turn the adjustment knob slowly while monitoring the outlet gauge to avoid overshooting the desired pressure.
-
Monitor Purity: Use downstream filters or analyzers if the application demands ultra-high purity beyond the regulator’s capability.
-
Shut Down Properly: Close the cylinder valve first, then vent residual pressure from the regulator before disconnecting.
Maintenance and Troubleshooting
To keep a regulator performing optimally, regular maintenance is key:
-
Inspection: Check for leaks using a soap solution or leak detector at connections. Look for signs of wear on seals or the diaphragm.
-
Cleaning: For high-purity models, use only approved solvents and avoid touching internal surfaces with bare hands.
-
Calibration: Periodically verify gauge accuracy and pressure control with a reference standard.
-
Common Issues: If flow drops, check for blockages or a depleted cylinder. If pressure creeps up, the valve seat may be dirty or damaged—professional servicing may be required.
Manufacturers often provide lifespan estimates (e.g., 5-10 years), but this depends on usage and environmental conditions.
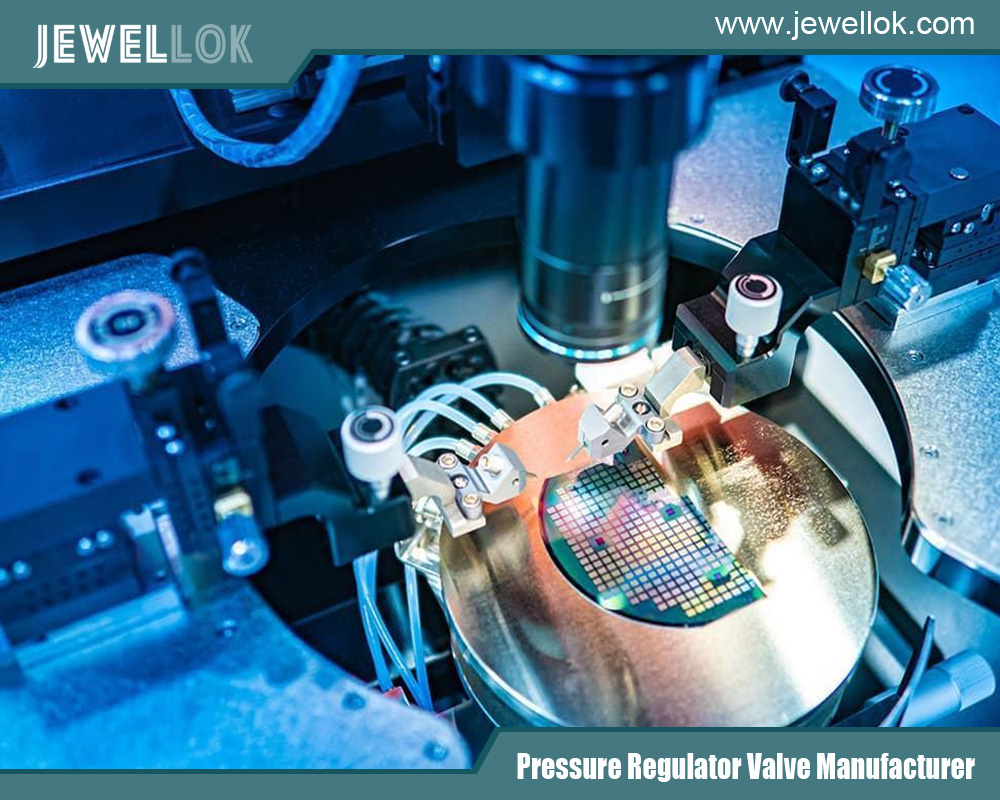
Conclusion
A high-purity, high-flow nitrogen regulator is a marvel of engineering, blending precision pressure control with the ability to deliver large volumes of uncontaminated gas. By leveraging a diaphragm-based feedback system, specialized materials, and high-capacity design, it meets the stringent demands of modern applications. From enabling cutting-edge electronics to ensuring food safety, this device quietly powers industries worldwide. Understanding its operation not only demystifies a critical tool but also underscores the importance of precision in gas handling—a testament to human ingenuity in harnessing the elements for progress.
For more about how does a high-purity high flow nitrogen regulator work, you can pay a visit to Jewellok at https://www.jewellok.com/products/ for more info.
Recent Posts
Tags
1 1 2 gas pressure regulator
1 2 gas regulator
1/2 gas pressure regulator
2 inch irrigation solenoid valve
2 inch irrigation valve
6mm compression fitting
6mm equivalent
8mm compression fitting
adjustable low pressure propane regulator
adjustable propane pressure regulator
adjustable propane regulator
adjusting propane regulator
air compressor non return valve
argon hose fitting
characteristics of pressure
diaphragm suppliers
gases used in semiconductor manufacturing
gas pipeline valve
gas pipeline valves
gas regulator
high purity valves
how does a needle valve work
how does pressure regulator work
how often should pressure relief valves be replaced
how solenoid valves work
humming propane regulator
irrigation timer valve
low pressure regulator
pressure gauge manufacturers
pressure regulator
pressure regulator valve leaking
pressure relief valve vs safety relief valve
regulator valve alibaba international market
relief vs safety valve
safety relief valve vs pressure relief valve
safety valve and relief valve
safety valve and relief valve difference
safety valve vs pressure relief valve
single stage pressure regulator
solenoid water valve
stainless pressure regulator
stainless steel 1/4 in. pressure gauge fitting - 3/8 qc
timed water valve
two stage pressure regulator
what is a gas pressure regulator
Recommended Products
-
Clean Connection Cabinet JW-300-CCB Valve Manifold Box And Control Valve Box
-
765LR Reducing Tee | Stainless Steel 316 High Purity Butt Weld Fittings Metal Face Seal For Welding Pipe Fitting Reducing Tee
-
Long Gland LG Series For Ultra High Purity Gas And Chemical Delivery Systems
-
High Purity Stainless Steel Mini Tube Butt Weld Fittings For Semiconductor
-
Manual Gas Rack High Purity Gas Delivery Systems JW-100-GR
-
7108L Cylinder Cap Connectors For Ultra High Purity Gases
-
Stainless Steel Ultra High Purity Mini Butt Weld Mini Tee Reducer MTRW Series Fittings
-
JR1300 Series Ultra High Purity Single Stage Regulator High Flow Line Regulator For Ultra High Purity Intermediate Flow