Blog
Jewellok is a professional pressure regulator and valve manufacturer and supplier.
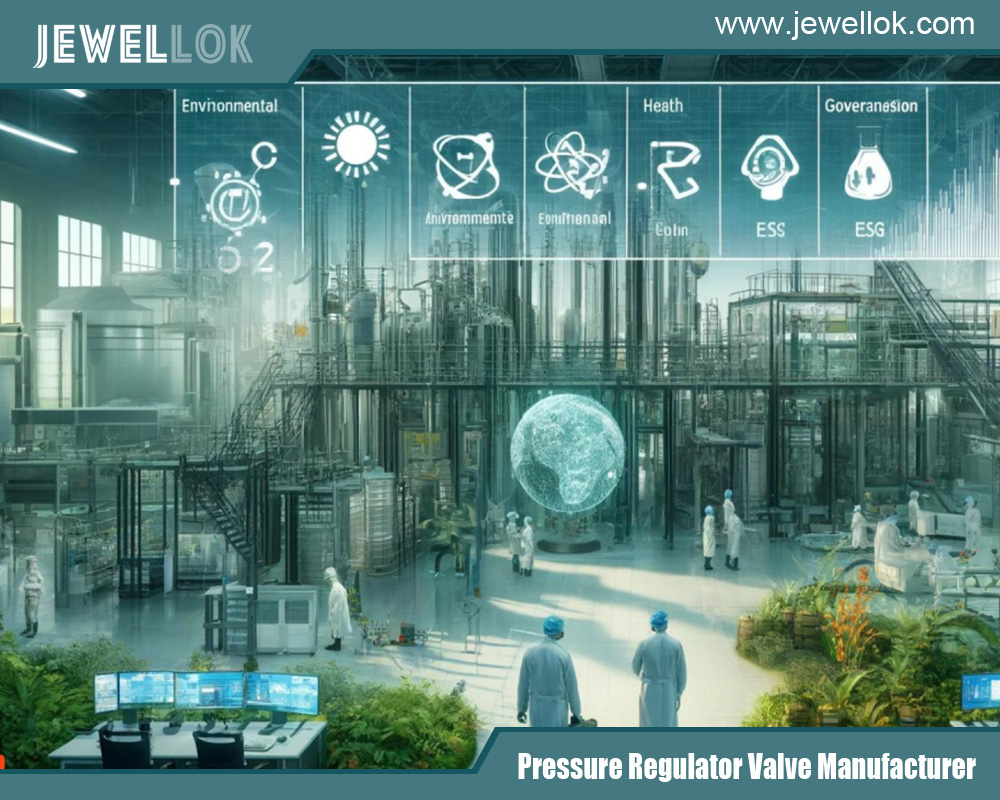
Exploring the Verification and Certification System of Ultra-High Purity Diaphragm Valves: Ensuring Strict Compliance with Industry Standards
- Pressure Regulator Valve Manufacturer
- 1 2 gas regulator, 1inch of water, 2 inch irrigation valve, 6mm compression fitting, argon hose connector, automatic switching valve, electric water valve 12v, fluid systems components, gas pipeline valve, gas pipeline valves, gas semiconductor, gases used in semiconductor manufacturing, high flow co2 regulator, high purity regulators, high purity valves, irrigation timer valve, laboratory gas valves, male fitting for argon hose, pressure regulator, pressure regulator valve leaking, propane adjustable pressure regulator, purpose of flame arrester, regulator valve alibaba international market, relief valve safety valve difference, safety valve and relief valve, safety valve vs pressure relief valve, single stage pressure regulator, two stage pressure regulator, ultra high purity diaphragm valve manufacturer, Ultra High Purity Diaphragm Valves, ultra high purity diaphragm valves supplier, ultra-high purity diaphragm valves factory
- No Comments
Exploring the Verification and Certification System of Ultra-High Purity Diaphragm Valves: Ensuring Strict Compliance with Industry Standards
In the ultra-high purity field, ultra-high purity diaphragm valves are widely used in industries with extremely high requirements for medium purity, such as semiconductors, pharmaceuticals, and food and beverage. The product quality and production safety in these industries are directly related to the health of consumers and the reputation of enterprises. Therefore, there are extremely strict requirements for the quality and performance of ultra-high purity diaphragm valves. The valves need to go through strict verification and certification to ensure that they can meet the relevant international and industry standards. This is not only a guarantee of product quality but also a key support for the reliability of the entire production process.

The Importance of Verification and Certification of Ultra-High Purity Diaphragm Valves
In semiconductor manufacturing, even the tiniest impurity particles can lead to a decline in chip performance or even scrapping. In the pharmaceutical industry, the purity and safety of drugs are directly related to the lives and health of patients. In the food and beverage industry, the purity and hygiene standards of products affect the health of consumers and the market reputation. As a key component for controlling fluids, any flaw in the quality and performance of ultra-high purity diaphragm valves may lead to serious consequences. Strict verification and certification are the keys to ensuring the stable operation of valves in complex and high-demand environments. They can effectively prevent problems such as leakage and contamination, and ensure the smooth progress of the production process and the reliability of product quality.
Aspects Covered by Verification and Certification
Material Verification
Material verification of ultra-high purity diaphragm valves is of vital importance. The valve body usually uses materials with excellent corrosion resistance and low extractability, such as 316L stainless steel, PFA (Perfluoroalkoxy resin), and PTFE (Polytetrafluoroethylene). These materials need to undergo strict chemical composition analysis to ensure that they meet the corresponding standard specifications. For 316L stainless steel, it is necessary to detect whether the contents of elements such as chromium, nickel, and molybdenum are within the specified range to ensure its corrosion resistance and mechanical properties. Microstructure analysis of materials is also indispensable. Through means such as metallographic analysis, check whether there are defects, impurities, or inhomogeneities inside the material. These microscopic defects may affect the strength and corrosion resistance of the valve. The extractable substance test of materials is used to evaluate whether the material will release impurities into the medium during use, which is particularly crucial for ultra-high purity applications. Through specific immersion tests, detect the impurity content in the immersion liquid to determine whether the extractability performance of the material meets the requirements.
Design Verification
Design verification aims to ensure that the valve design can meet the performance requirements of actual use. The rationality of the flow channel design directly affects the flow characteristics and pressure loss of the valve. Through computational fluid dynamics (CFD) simulation, the flow of fluid inside the valve can be predicted, the shape of the flow channel can be optimized, eddy currents and pressure loss can be reduced, and the stability and precise control of the flow rate can be ensured. The design of the sealing structure is the key to the valve, and the sealing performance is directly related to the leakage rate of the valve. Using methods such as finite element analysis (FEA), simulate the stress distribution and deformation of the sealing structure, and evaluate its sealing performance under different working conditions to ensure good sealing even under harsh conditions such as high pressure and high temperature. The design of the valve operating mechanism should consider the convenience, reliability, and durability of operation. Through mechanical analysis and actual operation tests, verify whether the torque of the operating mechanism is appropriate, whether the valve can be easily opened and closed, and whether there will be no failures during long-term use.
Performance Verification
Performance verification is a comprehensive inspection of the actual working performance of the valve. The pressure test is an important part of performance verification, including the pressure resistance test and the sealing pressure test. During the pressure resistance test, the valve is placed in an environment with a pressure higher than the normal working pressure to check whether the valve body can withstand the pressure without cracking or deformation. The sealing pressure test detects the sealing performance of the valve under different pressure conditions to ensure that the leakage rate is lower than the specified allowable value. The flow test is used to evaluate the flow characteristics of the valve at different opening degrees. By actually measuring the flow rate of the fluid flowing through the valve, draw the flow curve to verify whether it meets the design requirements and whether it can achieve precise flow regulation. The life test simulates the number of opening and closing cycles of the valve in actual use, and detects the performance changes of the valve during long-term use, such as the decrease in sealing performance and component wear, to ensure that it can meet the expected service life.
Cleanliness Verification
In the ultra-high purity field, cleanliness is an important indicator for measuring the quality of valves. Particle counting detection uses specialized instruments to detect the number and size of particles on the internal surface and fluid channels of the valve to ensure that the number of particles is lower than the specified limit and avoid particle pollution to the medium. Organic residue detection is used to analyze whether there are organic residues on the valve surface. These organic substances may dissolve into the medium during use and affect the product quality. Using appropriate analysis methods, such as gas chromatography-mass spectrometry (GC-MS), detect the types and contents of organic substances to ensure that they meet the requirements of ultra-high purity applications. Metal ion residue detection is to analyze whether metal ions are released from the valve material into the medium. Through technologies such as inductively coupled plasma mass spectrometry (ICP-MS), detect the concentration of metal ions and strictly control it at an extremely low level.
Certification Aspects
Common international certification standards include the ISO 9001 quality management system certification, which emphasizes the enterprise’s quality management capabilities in aspects such as design, development, production, installation, and service, ensuring that the enterprise has the ability to stably produce products that meet quality requirements. The ISO 14001 environmental management system certification focuses on the enterprise’s environmental performance, prompting enterprises to reduce the negative impact on the environment during the production process, including the reasonable treatment of production waste and the reduction of energy consumption. For valve manufacturing enterprises, this helps to promote the adoption of more environmentally friendly production processes and materials. In the pharmaceutical industry, the FDA (US Food and Drug Administration) certification has extremely high authority. The FDA has strict regulatory requirements for the design, manufacturing, installation, verification, and other aspects of pharmaceutical production equipment, including ultra-high purity diaphragm valves. Passing the FDA certification means that the valve meets the strict standards for pharmaceutical production in the United States and can enter the US market and be recognized by many pharmaceutical enterprises around the world. The Good Manufacturing Practice (GMP) certification in the European Union for pharmaceutical production also puts forward comprehensive requirements for the quality and safety of pharmaceutical production equipment, ensuring that the valve will not introduce impurities during the pharmaceutical production process and guaranteeing the quality of drugs. In the food and beverage industry, the 3A certification is a hygiene standard certification for food processing equipment in the United States. It specifies the hygiene requirements for the design, manufacturing, material selection, cleaning, and maintenance of food processing equipment. An ultra-high purity diaphragm valve that has passed the 3A certification indicates that it can meet the strict hygiene standards during food production and ensure food safety and quality. The NSF (National Sanitation Foundation) certification in the United States also focuses on public health and safety in fields such as food, water, and consumer goods, and evaluates the material safety and hygienic design of the valve to ensure that the product will not cause pollution to food and water. In the semiconductor industry, SEMI (Semiconductor Equipment and Materials International) has formulated a series of standards. For example, the SEMI F57 standard puts forward strict requirements for the cleanliness, particle release, sealing performance, and other aspects of valves used in ultra-high purity gas and chemical delivery systems. Valves that have passed the SEMI certification can meet the requirements for ultra-high purity and high precision in the semiconductor manufacturing process.
Measures Taken by Valve Manufacturers to Ensure Product Compliance with Standards
Establish a Sound Quality Management System
Valve manufacturers usually establish a full-process quality control system from raw material procurement, production processing, assembly and commissioning to finished product inspection in accordance with quality management system standards such as ISO 9001. In the raw material procurement link, conduct strict audits and evaluations of suppliers to ensure that the purchased materials meet the quality requirements and are traceable. During the production process, formulate detailed operation instructions and quality inspection plans, and strictly control the quality of each process to promptly discover and correct quality problems in production.
Advanced Production and Detection Equipment
Adopt advanced processing equipment, such as high-precision CNC machining centers, to ensure the machining accuracy of valve components and meet the design requirements. Equip with advanced detection equipment, such as a scanning electron microscope (SEM) for material microstructure analysis, an atomic absorption spectrometer (AAS) for metal ion detection, and a helium mass spectrometer leak detector for sealing performance detection, etc., which can accurately detect various performance indicators of the valve.
Professional R&D and Quality Teams
Have a professional R&D team that deeply studies industry standards and customer needs and continuously optimizes the design and manufacturing process of valves. The quality team is composed of experienced quality engineers and inspectors who are familiar with various standards and detection methods and can strictly inspect and verify products in accordance with the standards to ensure that the product quality meets the requirements.
Continuous Training and Improvement
Provide continuous training for employees to enable them to understand the latest industry standards, technical requirements, and quality control methods, and improve their professional qualities and quality awareness. Regularly conduct internal audits and management reviews of the quality management system and production process, discover problems and make improvements in a timely manner, and continuously improve the enterprise’s quality management level and product quality.
Participate in Standard Setting and Industry Exchanges
Actively participate in the formulation and revision of international and industry standards, integrate the enterprise’s technical advantages and practical experience into the standards, and at the same time, be able to understand the changing trends of the standards in a timely manner and make preparations in advance. Strengthen exchanges and cooperation with other enterprises and scientific research institutions in the industry, share experiences, and jointly promote the technological progress and quality improvement of the industry.
Strict verification and certification are the key guarantees for ultra-high purity diaphragm valves to meet international and industry standards, covering many important aspects such as materials, design, performance, and cleanliness. Valve manufacturers ensure the reliability of product quality through measures such as establishing a sound quality management system, adopting advanced production and detection equipment, having a professional team, continuous training and improvement, and actively participating in industry exchanges, providing solid support for the production process in the ultra-high purity field. With the continuous development of the industry and the progress of technology, the verification and certification system of ultra-high purity diaphragm valves will also be continuously improved and tightened, promoting the entire industry to develop in a direction of higher quality, greater safety, and reliability.
For more about exploring the verification and certification system of ultra-high purity diaphragm valves: ensuring strict compliance with industry standards, you can pay a visit to Jewellok at https://www.jewellok.com/ for more info.
Recent Posts
Tags
Recommended Products
-
Clean Connection Cabinet JW-300-CCB Valve Manifold Box And Control Valve Box
-
Pressure Control Panels For High Purity Gas Control System JSP-3AE Series From Pressure Control Panels Suppliers And Manufacturer
-
Stainless Steel 316L Single Stage Regulator Pressure Control Panels JSP-1E Series For Semiconductor Fluid Control
-
Single Stage Wall And Cabinet Mounting Pressure Control Panels JSP-2E Series For High Purity Gases
-
Stainless Steel Single Stage Semiconductor Grade Pressure Control Module Pressure Control Panels JSP-6A Series
-
DPR1 Ultra High Purity Two Stage Dual Stage Pressure Reducing Regulator Semiconductor Grade Regulators
-
768LN Stainless Steel Male Pipe Tube Butt Weld Connector And Tube Fittings Supplier
-
High Purity Stainless Steel Mini Tube Butt Weld Fittings For Semiconductor