Blog
Jewellok is a professional pressure regulator and valve manufacturer and supplier.
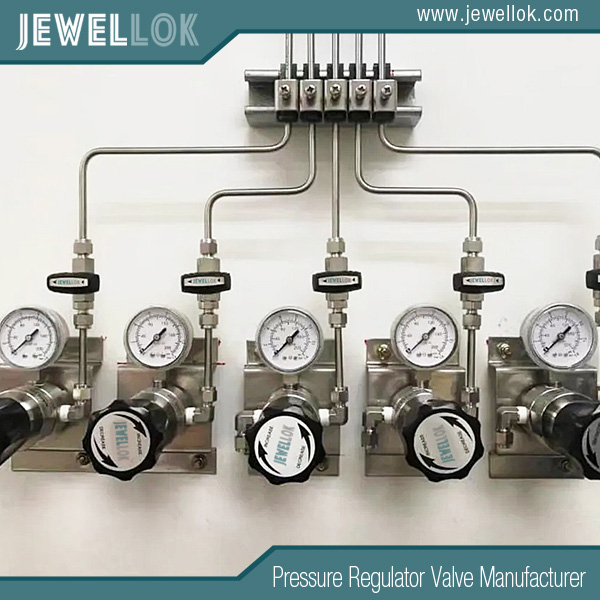
Comparison of Performance Parameters between Ultra-High Purity Diaphragm Valves and Common Diaphragm Valves and Selection Guidelines
- Pressure Regulator Valve Manufacturer
- 1/2 gas pressure regulator, 12v electric valve, adjusting propane regulator, block & bleed valve, characteristics of pressure, China Excess Flow Valve manufacturers, chinese propane gas cylinder, diaphram valve, double block & bleed, double block and bleed valve, double block bleed valve, electric water valve, excess flow valve, excess flow valvebcf connector, fusible plug, gas regulator, gas used in semiconductor manufacturing, high pressure argon regulator, high pressure flexible hose, how a solenoid valve works, hydraulic regulator, industrial grade purity, Natural gas Excess flow valve, o ring face seal fittings, pressure gauge fitting - 3/8 qc, pressure relief valve vs safety relief valve, quick connect, quick connect valve, relief valve and safety valve difference, safety relief valve vs pressure relief valve, solenoid valve for ammonia gas 1 inch pipe, ultra high purity, ultra high purity diaphragm valve manufacturer, Ultra High Purity Diaphragm Valves, ultra-high purity diaphragm valves factory, v, water solenoid valve 24v
- No Comments
Comparison of Performance Parameters between Ultra-High Purity Diaphragm Valves and Common Diaphragm Valves and Selection Guidelines
In the field of industrial fluid control, diaphragm valves are widely used due to their unique structure and performance characteristics. Among them, there are significant differences in performance parameters between ultra-high purity diaphragm valves and common diaphragm valves. Correctly understanding these differences and selecting valves with appropriate parameters according to specific process requirements are crucial for ensuring the efficient, stable, and safe operation of industrial production.
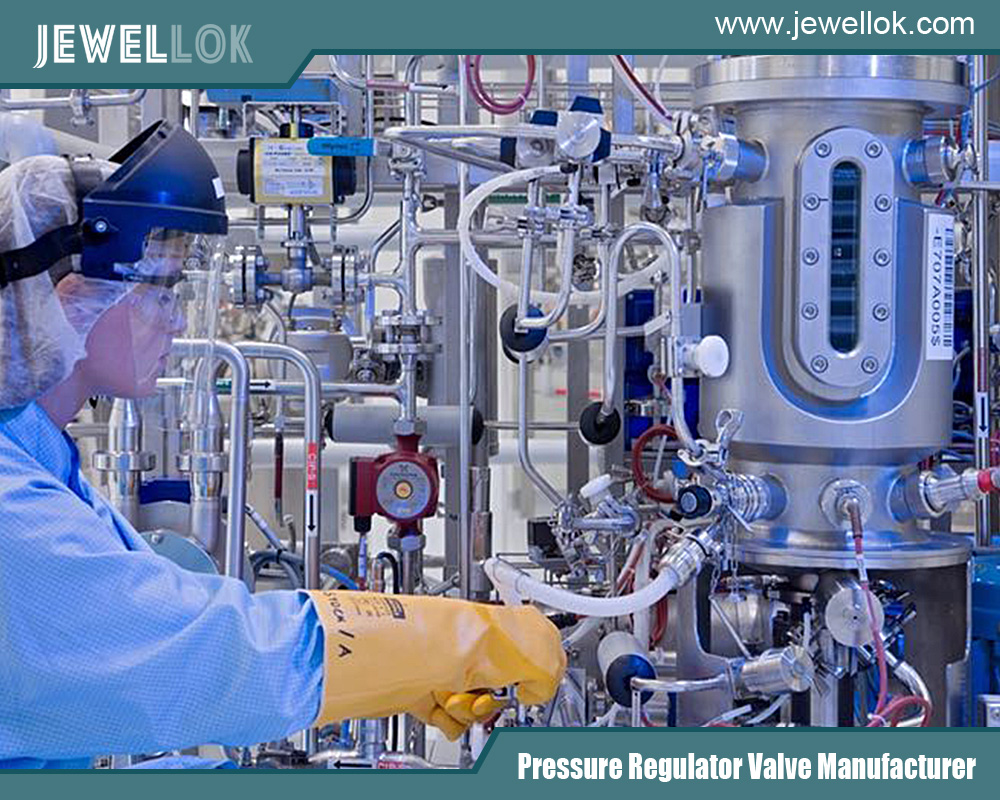
Differences in Performance Parameters between Ultra-High Purity Diaphragm Valves and Common Diaphragm Valves
Flow Coefficient
The flow coefficient is a key indicator for measuring the flow capacity of a valve. It represents the fluid flow rate when a unit pressure loss occurs during the fluid flowing through the valve. The larger the flow coefficient value, the smaller the pressure loss of the fluid flowing through the valve.
- Common Diaphragm Valves: Their flow coefficient is affected by various factors, including the valve’s size, type, and structure. Generally speaking, the flow coefficient of a common diaphragm valve is relatively fixed when it is fully open, but the flow coefficients of valves with different specifications and types will vary. For example, for a common straight-through diaphragm valve, its flow characteristics are close to the quick-opening characteristics. It is approximately linear before 60% of the stroke, and the flow change is not significant after 60%. For common diaphragm valves with a nominal diameter ranging from 20mm to 200mm, their rated flow coefficients range from 9.8 to 1114 when there is no lining, and from 7.8 to 1000 when there is a lining.
- Ultra-High Purity Diaphragm Valves: The design goal of ultra-high purity diaphragm valves is to achieve high-precision flow control in an ultra-high purity environment. Therefore, the design and optimization of their flow coefficients are more refined. Some ultra-high purity diaphragm valves reduce the resistance of the fluid inside the valve through special flow channel design and material selection, thus increasing the flow coefficient. For example, certain ultra-high purity diaphragm valves adopt patented fluid flow paths, reducing fluid stagnation, allowing the process fluid to be purged quickly, reducing the risk of contamination, and also improving the flow coefficient. The flow coefficient of some ultra-high purity diaphragm valves can reach 0.62 or even higher, which makes them perform well when dealing with ultra-high purity processes with high flow rate requirements.
Pressure Rating
The pressure rating determines the working pressure range that the valve can withstand, and it is one of the important bases for valve selection.
- Common Diaphragm Valves: Due to the limitations of the diaphragm and lining materials, the pressure resistance and temperature resistance of common diaphragm valves are relatively poor. Generally, common diaphragm valves are suitable for working environments with a nominal pressure of 1.6MPa and a temperature below 150°C. Of course, there are some common diaphragm valves with special designs or made of high-performance materials, and their pressure rating and applicable temperature range will be higher. However, overall, there is still a gap compared with ultra-high purity diaphragm valves.
- Ultra-High Purity Diaphragm Valves: When ultra-high purity diaphragm valves are applied in fields with extremely high purity requirements such as semiconductor manufacturing, they often need to withstand a certain pressure. The pressure ratings of different types of ultra-high purity diaphragm valves are different. For example, some ultra-high purity diaphragm valves used in the atomic layer deposition (ALD) process have a working pressure range from vacuum to 145psig (10.0bar), while the working pressure of some high-pressure ultra-high purity diaphragm valves can reach 10000psig (700bar). Ultra-high purity diaphragm valves can maintain stable performance under relatively high pressure, and at the same time ensure that the ultra-high purity state of the fluid is not affected.
Differences in Other Performance Parameters
In addition to the flow coefficient and pressure rating, there are also differences in other performance parameters between ultra-high purity diaphragm valves and common diaphragm valves.
- Temperature Range: Common diaphragm valves are generally suitable for working temperatures below 150°C, while the working temperature range of ultra-high purity diaphragm valves varies according to specific application scenarios and material selection. Some ultra-high purity diaphragm valves can work stably in the temperature range of – 23°C to 200°C.
- Sealing Performance: Ultra-high purity diaphragm valves have extremely high requirements for sealing performance to prevent any tiny leakage from causing contamination of the process fluid. Special sealing materials and structural designs are usually adopted to ensure zero leakage or an extremely low leakage rate during long-term use. Although common diaphragm valves also have good sealing performance, they still have a certain gap in the face of the strict requirements of the ultra-high purity environment.
- Cleanliness and Corrosion Resistance: The valve body, diaphragm, and other components of ultra-high purity diaphragm valves usually use high-purity and corrosion-resistant materials such as 316L VIM – VAR stainless steel, cobalt-based superalloys, and modified polytetrafluoroethylene (PTFE) to meet the stringent requirements for cleanliness and corrosion resistance of ultra-high purity processes. The material selection of common diaphragm valves is relatively conventional, and their cleanliness and corrosion resistance cannot be compared with those of ultra-high purity diaphragm valves.
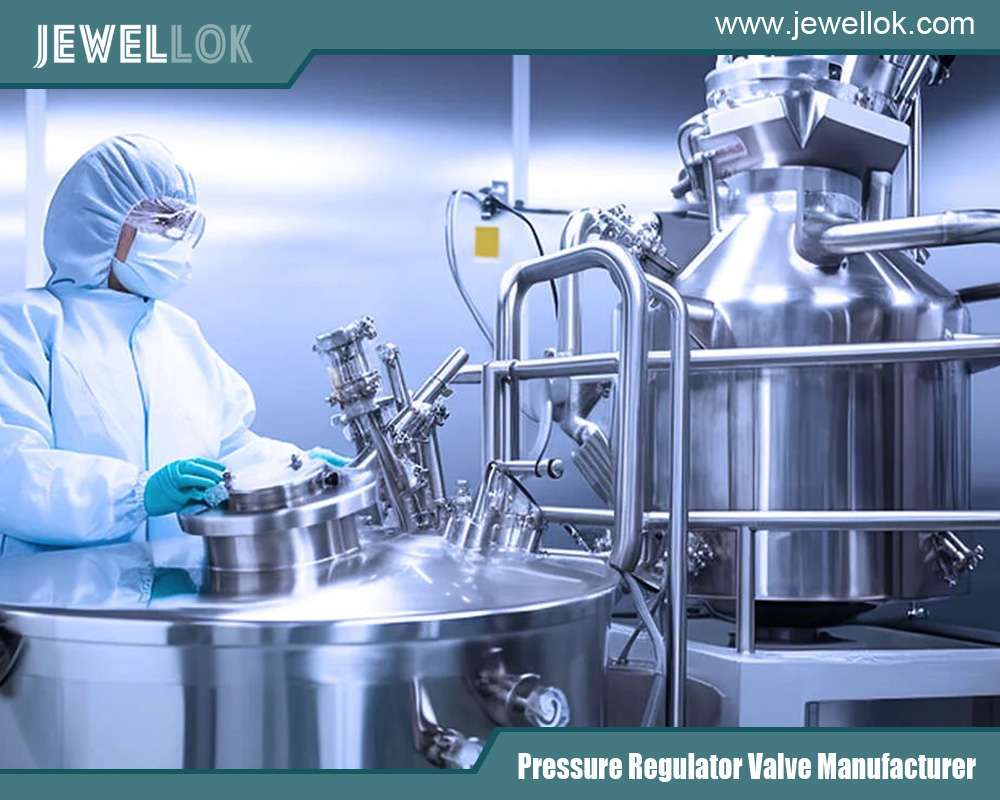
Selecting Appropriate Parameters According to Process Requirements
Clarifying Process Requirements
Before selecting the parameters of the diaphragm valve, it is necessary to have an in-depth understanding of the specific process requirements. This includes but is not limited to the following aspects:
- Fluid Properties: It is necessary to clarify whether the process fluid is a corrosive medium or a non-corrosive medium, as well as the chemical composition, viscosity, and particle content of the fluid. For example, for ultra-high purity process fluids containing strong corrosive chemicals, an ultra-high purity diaphragm valve with excellent corrosion resistance must be selected, and the internal materials of the valve should not chemically react with the fluid to avoid contaminating the fluid.
- Flow Requirements: Accurately calculate the required flow range of the process, including the maximum flow rate and the minimum flow rate. If the flow rate requirement is high, a valve with a large flow coefficient should be selected to ensure that the fluid can pass through smoothly and meet the production requirements.
- Pressure Conditions: Determine the working pressure, maximum pressure, and minimum pressure of the process system. According to these pressure parameters, select a diaphragm valve with an appropriate pressure rating to ensure that the valve can operate safely and stably within the working pressure range and avoid valve damage or leakage caused by excessive pressure.
- Temperature Range: Clearly define the temperature range of the process fluid and select a diaphragm valve that can work normally within this temperature range. If the temperature is too high or too low and exceeds the applicable range of the valve, it may affect the performance and service life of the valve.
Selection of Flow Coefficient
Select an appropriate flow coefficient according to the required flow rate of the process and the allowable pressure loss. The following steps can be taken:
- Calculate the Flow Requirement: According to the process design, determine the required fluid flow rate Q (the unit can be m³/h, L/min, etc.).
- Estimate the Pressure Loss: Consider factors such as the resistance of the pipeline system and the pressure difference before and after the valve, and estimate the allowable pressure loss Δp (the unit can be bar, MPa, etc.).
- Refer to the Flow Coefficient Table: According to the type, size, and structure of the valve, refer to the corresponding flow coefficient table to find the flow coefficient Cv or Kv value that meets the flow requirement and the pressure loss requirement. If there is no ready-made table available, you can refer to the technical materials provided by the valve manufacturer or consult a professional.
- Consider the Margin: To ensure that the valve can work normally under various working conditions, it is recommended to appropriately consider a certain margin when selecting the flow coefficient. Generally, the flow coefficient can be increased by 10% – 20%.
Selection of Pressure Rating
When selecting the pressure rating, ensure that the rated pressure of the valve is greater than the maximum working pressure of the process system. The specific steps are as follows:
- Determine the Maximum Working Pressure: Through process calculation or actual measurement, determine the maximum working pressure Pmax that may occur in the process system during normal operation and abnormal conditions.
- Consider the Pressure Fluctuation: Since there may be pressure fluctuations in the process system, such as the start and stop of the pump and the change of the flow rate, when selecting the pressure rating, a certain safety margin should be considered. Generally, the maximum working pressure can be multiplied by a safety factor of 1.2 – 1.5 to obtain the reference value for selecting the valve’s pressure rating.
- Select the Appropriate Pressure Rating: According to the calculated reference value, refer to the valve’s pressure rating standard and select a diaphragm valve whose rated pressure is greater than the reference value. For example, if the calculated reference value is 1.5MPa, a valve with a pressure rating of 2.0MPa or higher can be selected.
Consideration of Other Parameters
- Temperature Range: Ensure that the applicable temperature range of the diaphragm valve covers the temperature of the process fluid. If the process temperature is close to the limit temperature of the valve, additional heat preservation or cooling measures should be considered to ensure the normal operation of the valve.
- Sealing Performance: For processes with strict requirements for leakage, such as ultra-high purity processes and the transportation of toxic and harmful fluids, select a diaphragm valve with good sealing performance. You can refer to the leakage rate index of the valve and select a product with a low leakage rate.
- Cleanliness and Corrosion Resistance: In ultra-high purity processes, an ultra-high purity diaphragm valve that meets the cleanliness requirements must be selected, and its materials should have good corrosion resistance to prevent the internal materials of the valve from being corroded and contaminating the process fluid. For common industrial applications, if the fluid has a certain degree of corrosiveness, a corrosion-resistant diaphragm valve should also be selected, and the appropriate corrosion-resistant material should be selected according to the degree of corrosion.
There are obvious differences in performance parameters such as flow coefficient and pressure rating between ultra-high purity diaphragm valves and common diaphragm valves. In practical applications, it is necessary to comprehensively consider various performance parameters according to specific process requirements and select appropriate diaphragm valves. Only in this way can we ensure the safe, stable, and efficient operation of the industrial production process and meet the strict requirements for fluid control in different industries.
For more about comparison of performance parameters between ultra-high purity diaphragm valves and common diaphragm valves and selection guidelines, you can pay a visit to Jewellok at https://www.jewellok.com/ for more info.
Recent Posts
Best Top 10 Specialty Gas Regulators Suppliers In Thailand
Best Top 10 Specialty Gas Regulators Manufacturers In India
Can Industrial Gas Regulators Be Used In Laboratories?
Tags
Recommended Products
-
Single Stage Wall And Cabinet Mounting Pressure Control Panels JSP-2E Series For High Purity Gases
-
Low Pressure High Flow Line Pressure Regulators And Control Valves JSR-4L Series For Laboratory Pressure Control
-
771L Male Run Tee | Stainless Steel High Quality High Purity Male Run Tee Branch Tee Pipe Fittings
-
764L Stainless Steel Union Tee High Purity Fitting Union Tee Reducing Tubing Connection
-
FT-BOX JW-FTB-C Valve Manifold Panels And Boxes With High Purity Configurable Systems
-
Fully Automated Gas Cabinet For Precise UHP Gas Delivery And High Purity Gas Delivery Systems JW-300-GC
-
JF Series In-Line Gas Filters | High Purity High Precision High Flow Semiconductor Gas Filter Gas Filtration & Purification
-
Fully Automated Gas Cabinet Gas Rack Gas Delivery Systems JW-300-GR