Blog
Jewellok is a professional pressure regulator and valve manufacturer and supplier.
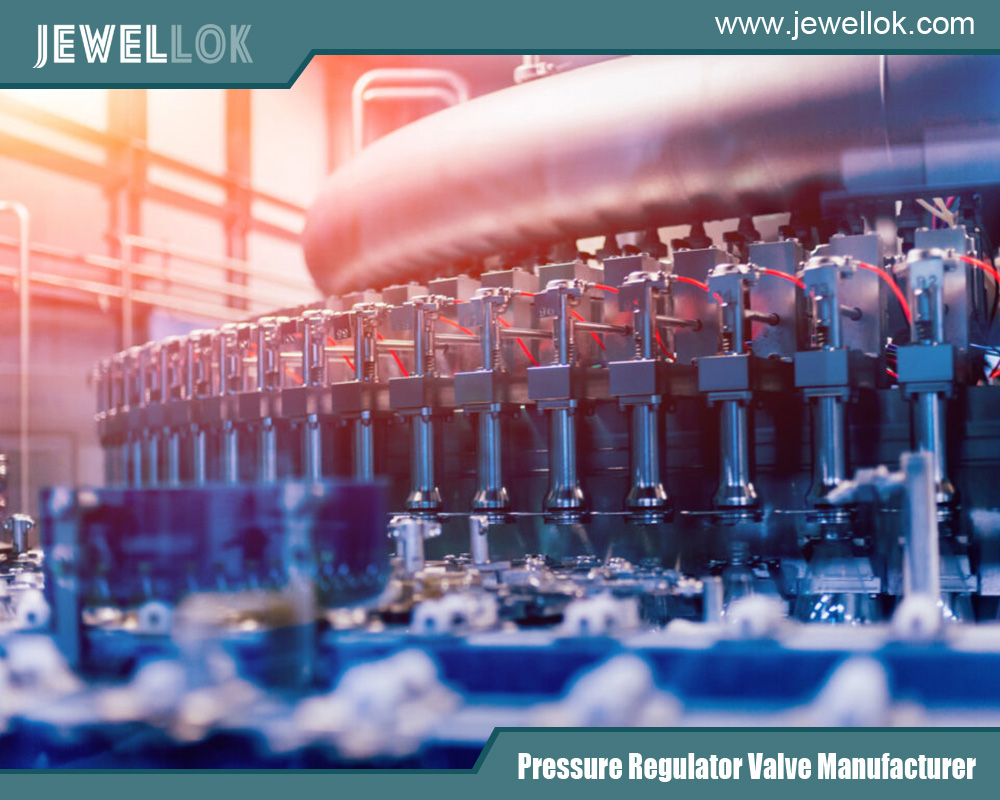
Analyzing the Sealing Technology and Performance Assurance of Ultra High Purity Diaphragm Valves
- Pressure Regulator Valve Manufacturer
- 1 2 gas regulator, 2 inch irrigation valve, 6mm compression fitting, 8mm compression fitting, argon hose connector, automatic switching valve, ferrule connector, fluid systems components, gas pipeline valve, gas pipeline valves, gas semiconductor, gases used in semiconductor manufacturing, high flow co2 regulator, high purity regulators, high purity valves, how does a needle valve work, how solenoid valve works, irrigation timer valve, laboratory gas valves, low pressure gas regulator, pressure regulator, pressure regulator valve leaking, pressure safety valve vs relief valve, regulator valve alibaba international market, relief valve safety valve difference, safety valve and relief valve, single stage pressure regulator, timed water valve, two stage pressure regulator, ultra high purity diaphragm valve factory, ultra high purity diaphragm valve hotsale, ultra high purity diaphragm valve manufacturer, ultra high purity diaphragm valve OEM, ultra high purity diaphragm valve wholesale, Ultra High Purity Diaphragm Valves, ultra high purity diaphragm valves manufacturer, valve timer water
- No Comments
Analyzing the Sealing Technology and Performance Assurance of Ultra High Purity Diaphragm Valves
In many fields of modern industry, such as semiconductor manufacturing, pharmaceuticals, food and beverage, and high-end scientific research, there are extremely high requirements for the purity of the medium and the absence of contamination during the fluid transportation process. As a key control element, the reliable sealing performance of ultra high purity diaphragm valves has become the core factor to ensure the stable operation of the system, the compliance of product quality, and the safety of the production environment. This article will deeply explore how ultra high purity diaphragm valves achieve reliable sealing, as well as the technical principles and methods for ensuring the sealing performance under different working pressures and temperatures.
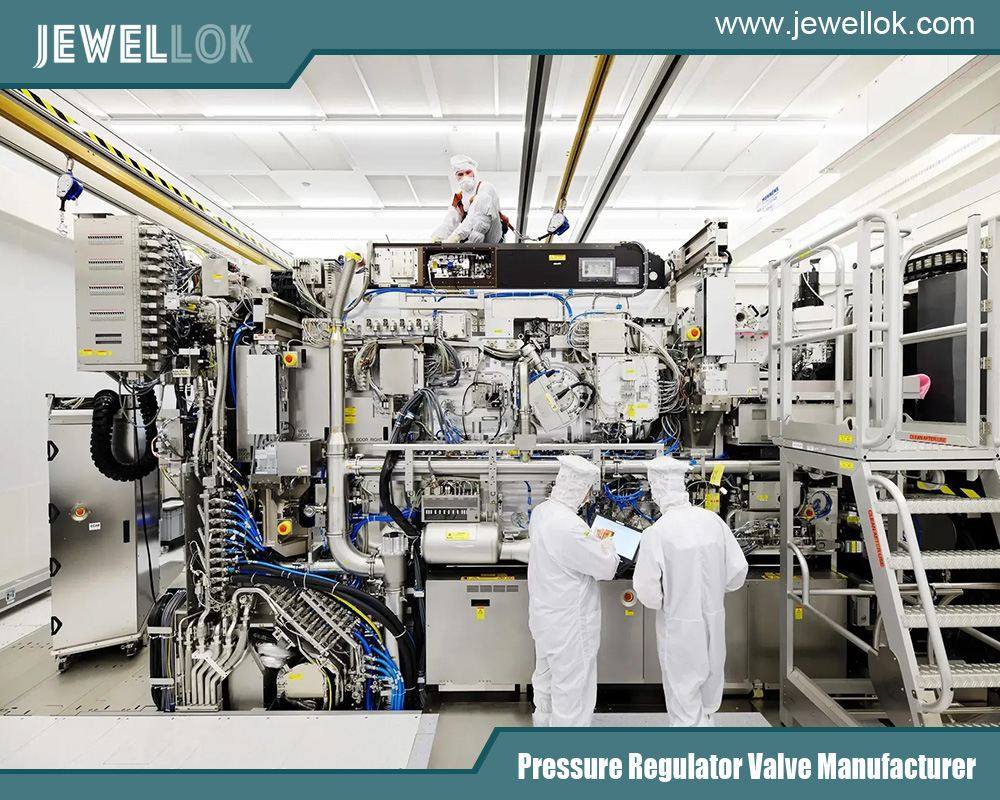
Sealing Structure and Principle of Ultra High Purity Diaphragm Valves
I. Basic Sealing Structure
Ultra high purity diaphragm valves are mainly composed of key components such as the valve body, diaphragm, and valve cover. Among them, the diaphragm is the core component for achieving sealing. It completely separates the inner cavity of the valve body from the inner cavity of the valve cover, preventing components such as the valve stem, valve stem nut, valve disc, and various control mechanisms located above the diaphragm from coming into contact with the medium. This fundamentally eliminates the possibility of medium leakage and also prevents external impurities from invading the medium passage through these components. For example, in the ultrapure water system of semiconductor chip manufacturing, the structure of the diaphragm valve ensures that the ultrapure water will not be contaminated by any external substances, meeting the high-precision requirements of the chip manufacturing process.
II.Sealing Principle
The sealing principle of a diaphragm valve is based on the tight fit between the diaphragm and the valve body passage. When the operating mechanism drives the diaphragm to move downward, the diaphragm will closely fit with the weir-type lined valve body or the straight-through lined valve body passage, thus preventing the flow of the medium and achieving sealing. The magnitude of the sealing specific pressure is mainly adjusted and achieved through the downward pressure of the closing member. Since the valve body is usually lined with various soft materials, such as rubber, polytetrafluoroethylene (PTFE), etc., and the diaphragm is also made of soft materials, such as PTFE with a rubber or synthetic rubber lining, only a small sealing force is required to achieve complete sealing. This characteristic enables the diaphragm valve to ensure the sealing performance while reducing the pressure requirements on the driving mechanism, improving the overall performance and service life of the valve.
Key Factors for Achieving Reliable Sealing
I. Selection and Characteristics of Diaphragm Materials
1. Material Performance Requirements
Ultra high purity applications impose strict requirements on diaphragm materials. Firstly, the material must have excellent chemical stability and be able to withstand the erosion of various strongly corrosive media, ensuring that its performance will not deteriorate due to the chemical action of the medium during long-term use. Secondly, the diaphragm material should have good flexibility and elasticity to ensure that it can closely fit the valve body passage during frequent opening and closing operations, achieving reliable sealing. At the same time, it should also be able to effectively resist fatigue damage and extend the service life. For example, in the pharmaceutical industry, the pharmaceutical production process involves a variety of chemical reagents, and the diaphragm material needs to be able to withstand the corrosion of these reagents while maintaining stable sealing performance to prevent the drugs from being contaminated.
2. Common Diaphragm Materials and Their Advantages
Common diaphragm materials include fluoroelastomer (FKM), silicone rubber (VMQ), polytetrafluoroethylene (PTFE), and their composite materials. Fluoroelastomer has excellent chemical corrosion resistance, high-temperature resistance, and good mechanical properties, making it suitable for sealing in a variety of corrosive media and high-temperature environments. Silicone rubber is renowned for its excellent flexibility, low-temperature resistance, and physiological inertness, and is widely used in fields with extremely high hygiene requirements, such as food and medicine. Polytetrafluoroethylene has an extremely low coefficient of friction, excellent chemical stability, and weather resistance, and is resistant to almost all chemical substances, often being used for the sealing of ultra high purity media. Some composite diaphragm materials combine the advantages of multiple materials, further enhancing the comprehensive performance of the diaphragm to meet more complex and stringent working conditions.
II.Valve Body Design and Manufacturing Precision
1. Flow Channel Design
The flow channel design of the valve body has an important impact on the sealing performance and the flow characteristics of the medium. A reasonable flow channel design should ensure that the medium can flow smoothly within the valve body, reducing flow resistance and pressure loss. At the same time, it should avoid the occurrence of medium stagnation and dead corner areas to prevent impurities from accumulating in these areas, which may affect the sealing performance. For example, the flow channel design of a straight-through diaphragm valve is relatively simple, with low flow resistance, and the medium can quickly pass through the valve, reducing the impact and wear of the medium on the diaphragm, which is conducive to improving the reliability of the seal. The weir-type diaphragm valve, while having a certain throttling characteristic, can also achieve good sealing performance and stable flow control by optimizing the shape and size of the weir opening.
2. Manufacturing Precision
Ultra-high manufacturing precision is the key to ensuring the sealing performance of diaphragm valves. The machining precision of the valve body and the diaphragm directly affects the fitting precision and sealing effect between them. During the manufacturing process, strictly control the dimensional tolerances, surface roughness, and geometric tolerances of the valve body and the diaphragm to ensure that the diaphragm can closely fit the valve body passage and avoid the occurrence of gaps and leakage points. For example, by using advanced CNC machining technology and precision measurement equipment, high-precision machining and inspection of the valve body and the diaphragm can effectively improve the sealing performance and consistency of the valve. The internal surface roughness of some high-end diaphragm valves can be controlled at an extremely low level, such as below Ra0.25μm, providing a solid foundation for achieving reliable sealing.
III. Sealing Auxiliary Structures and Technologies
1. Valve Seat Design
The valve seat is an important part of the sealing system of a diaphragm valve, and its design and material selection have a direct impact on the sealing performance. The valve seat is usually made of soft materials that match the diaphragm material or metal materials with good sealing performance. For example, in some ultra high purity diaphragm valves, the valve seat is made of fluoroplastic (such as PFA) and used in conjunction with a PTFE diaphragm, which can achieve excellent sealing performance and chemical compatibility. The structural design of the valve seat should also consider the uniform distribution of the sealing specific pressure to ensure that when the valve is closed, a uniform sealing pressure can be formed between the diaphragm and the valve seat to avoid the situation of local unsealing.
2. Gaskets and O-rings
At the connection part between the valve body and the valve cover of the diaphragm valve, gaskets or O-rings are usually used to enhance the sealing performance. These sealing elements should be made of materials that meet the ultra high purity requirements and have good corrosion resistance, temperature resistance, and sealing performance. Common materials for gaskets include PTFE, rubber, and spiral wound gaskets, which are selected according to different working conditions and medium characteristics. O-rings are widely used due to their simple structure and reliable sealing performance, and common materials include fluoroelastomer, silicone rubber, etc. During the installation process, ensure the correct installation and compression amount of the gaskets and O-rings to ensure their sealing effect.
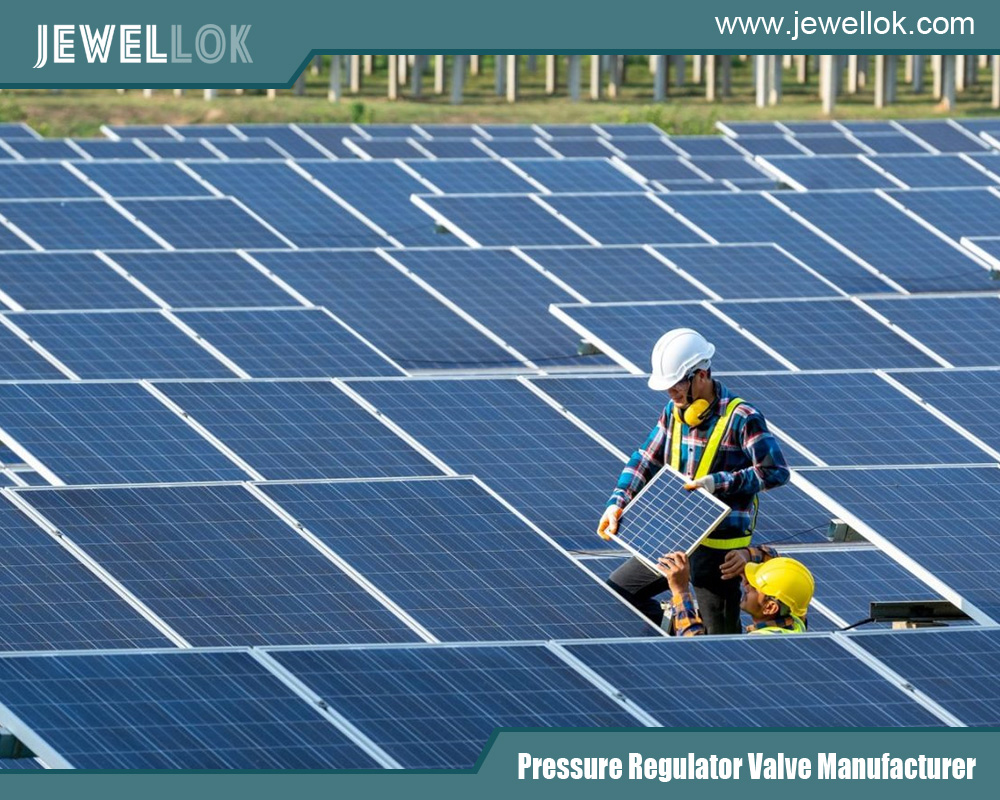
Sealing Performance Assurance under Different Working Pressures and Temperatures
I. Influence of Working Pressure on Sealing Performance and Countermeasures
1. Low Pressure Working Conditions
Under low pressure working conditions, although the pressure of the medium on the diaphragm is small, it is still necessary to ensure the sealing reliability between the diaphragm and the valve body passage. At this time, the flexibility and elasticity of the diaphragm material play an important role and can achieve good sealing under a small sealing specific pressure. Some diaphragm valves with rubber or silicone rubber diaphragms exhibit excellent sealing performance in low pressure environments and can meet the sealing requirements for low-pressure fluid transportation in industries such as food and beverages. In addition, a reasonable design of the structure and shape of the valve seat to reduce the leakage gap of the sealing surface also helps to improve the sealing performance under low pressure working conditions.
2. High Pressure Working Conditions
As the working pressure increases, the pressure borne by the diaphragm also increases accordingly, posing higher challenges to the strength and sealing performance of the diaphragm. To deal with high pressure working conditions, first of all, it is necessary to select high-strength and high-pressure resistant diaphragm materials, such as cobalt-based superalloy diaphragms. These materials have excellent mechanical properties and fatigue resistance and can maintain stable sealing performance under high pressure. Secondly, optimize the structure design of the valve body and the diaphragm to enhance their pressure resistance and ensure that the sealing surface between the diaphragm and the valve body passage will not be deformed or damaged under high pressure. At the same time, adopt appropriate sealing auxiliary structures, such as increasing the thickness of the gasket or using a multi-layer sealing structure, to improve the overall pressure resistance of the sealing system.
II. Influence of Working Temperature on Sealing Performance and Countermeasures
1. Low Temperature Working Conditions
In a low temperature environment, the performance of the diaphragm material will change, such as a decrease in flexibility and an increase in brittleness, which may lead to the diaphragm cracking or poor sealing during the sealing process. Therefore, under low temperature working conditions, diaphragm materials with good low temperature performance, such as silicone rubber and low temperature type fluoroelastomer, should be selected. These materials can still maintain a certain degree of flexibility and elasticity at low temperatures to ensure that the sealing performance is not affected. In addition, appropriately optimize the structure of the valve, such as adding thermal insulation measures or using low temperature adaptable sealing auxiliary materials, to prevent the performance of the sealing elements from decreasing due to too low a temperature.
2. High Temperature Working Conditions
High temperature will change the physical and chemical properties of the diaphragm material, such as material expansion, aging, degradation, etc., thus affecting the sealing performance. To adapt to high temperature working conditions, it is necessary to select high temperature resistant diaphragm materials, such as PTFE and its modified materials, high temperature type fluoroelastomer, etc. These materials have good thermal stability and chemical stability and can maintain the sealing performance for a long time at high temperatures. At the same time, carry out heat dissipation design for the valve body and the sealing structure to reduce the working temperature of the sealing elements and reduce the performance degradation caused by high temperature. For example, in some high temperature application occasions, use a valve body design with heat dissipation fins or cool the valve through a cooling medium to ensure the stability of the sealing performance.
III. Sealing Performance Assurance under Alternating Pressure and Temperature Working Conditions
In actual industrial applications, many working conditions involve frequent alternations of pressure and temperature, which pose more severe challenges to the sealing performance of ultra high purity diaphragm valves. During the alternation of pressure and temperature, the diaphragm and valve body materials will suffer from fatigue damage due to thermal expansion and contraction and stress changes, resulting in a decrease in the sealing performance. To deal with such complex working conditions, on the one hand, it is necessary to select diaphragm and valve body materials with good fatigue resistance and thermal stability. On the other hand, it is necessary to optimize the structural design of the valve to reduce stress concentration points and improve the reliability of the valve under alternating working conditions. For example, adopt a special structural design to enable the diaphragm to expand and contract freely when the pressure and temperature change, reducing the generation of stress. At the same time, use means such as finite element analysis to optimize the structure of the valve to ensure that the strength and sealing performance of each component meet the requirements under alternating loads. In addition, regularly maintain and inspect the valve and replace the worn or aged sealing elements in a timely manner, which is also an important measure to ensure the sealing performance.
The reliable sealing performance of ultra high purity diaphragm valves is the basis for their wide application in high-end industrial fields. Through the reasonable selection of diaphragm materials, optimization of valve body design and manufacturing precision, adoption of effective sealing auxiliary structures and technologies, and taking corresponding countermeasures for different working pressures and temperatures, it is possible to ensure that the diaphragm valve can achieve stable and reliable sealing under various complex working conditions, meeting the high-purity and pollution-free requirements of modern industrial fluid transportation systems. With the continuous development of industrial technology, the sealing technology of ultra high purity diaphragm valves will also continue to innovate and improve, providing a more reliable guarantee for the development of various industries.
For more about analyzing the sealing technology and performance assurance of ultra high purity diaphragm valves, you can pay a visit to Jewellok at https://www.jewellok.com/ for more info.
Recent Posts
Tags
Recommended Products
-
Stainless Steel High Purity High Temperature Pneumatic Actuated Ball Valves JBV2 Series
-
Ultra High Purity Oxygen Pressure Gauge For Semiconductor Gases JG Series Pressure Instruments For Semiconductor Manufacturing
-
VMB Valve Manifold Panels And Boxes High Purity Configurable Systems JW-200-VMB & JW-100-VMB
-
767LT Reducer Pressure Reducing Valve Adjustment High purity Pressure Reducing Union Fittings And Tubing
-
Stainless Steel Ultra Clean Welding Joint Fittings TW Series TRW Series & CW Series
-
Low Pressure High Flow Line Pressure Regulators And Control Valves JSR-4L Series For Laboratory Pressure Control
-
770L Female Elbow | Stainless Steel High Purity Weld Fittings Female Micro Elbow Fittings
-
Stainless Steel Ultra High Purity (UHP) High Pressure Manual Diaphragm Valve