Blog
Jewellok is a professional pressure regulator and valve manufacturer and supplier.
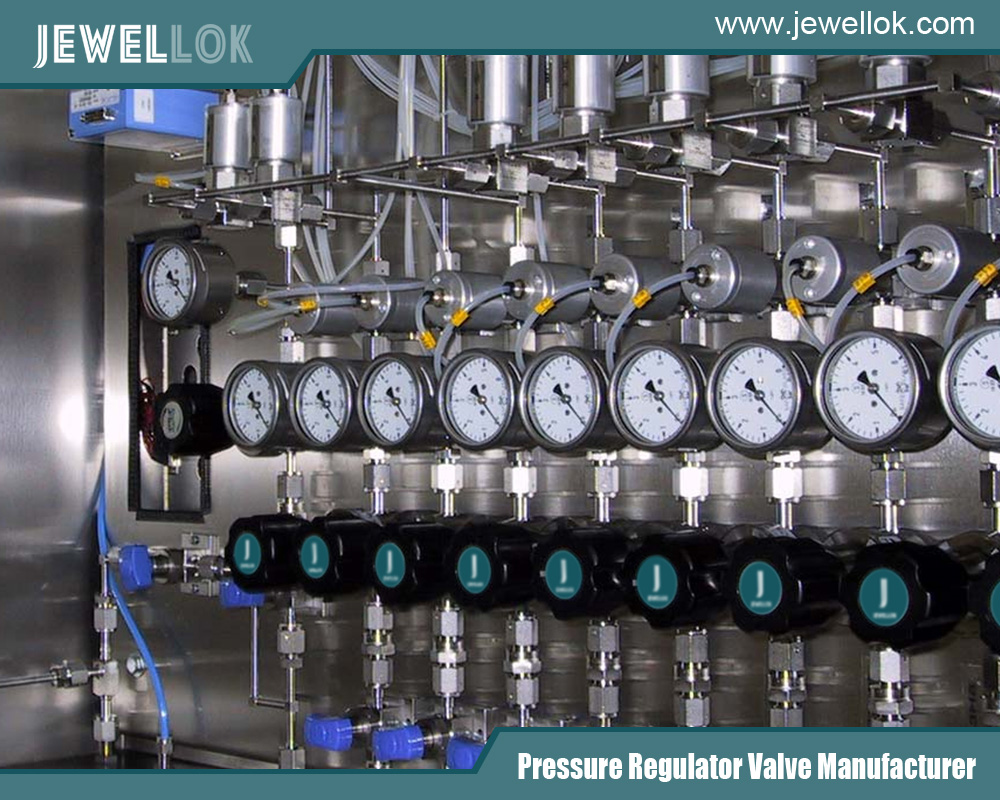
Analysis of the Service Life and Maintenance Key Points of Ultra High Purity Diaphragm Valves
- Pressure Regulator Valve Manufacturer
- 1inch of water, 2 inch irrigation valve, 6mm compression fitting, adjustable low pressure propane regulator, air compressor non return valve, argon hose connector, argon hose fittings, compression fitting 6mm, electric water valve 12v, ferrule connector, fire arrestor, fluid system components, gas semiconductor, high purity regulators, how a gas pressure regulator works, how a pressure regulator works, how do pressure regulators work, how do regulators work, how often should pressure relief valves be replaced, humming propane regulator, male fitting for argon hose, oxygen cylinder manifold, pressure relief valve vs safety valve, propane adjustable pressure regulator, propane manifold with valves, purpose of flame arrester, safety or relief valves, safety relief valve vs safety valve, safety valve vs pressure relief valve, second stage propaneregulator, timer water valve, two stage pressure regulator, Ultra High Purity Diaphragm Valves
- No Comments
Analysis of the Service Life and Maintenance Key Points of Ultra High Purity Diaphragm Valves
In industries with extremely high requirements for medium purity, such as semiconductors, pharmaceuticals, and biotechnology, ultra high purity diaphragm valves play a crucial role. The stability and reliability of their performance are directly related to the quality and efficiency of production. Understanding the expected service life of ultra high purity diaphragm valves, maintenance work under normal operating conditions, and maintenance costs is essential for ensuring the stable operation of the production system.
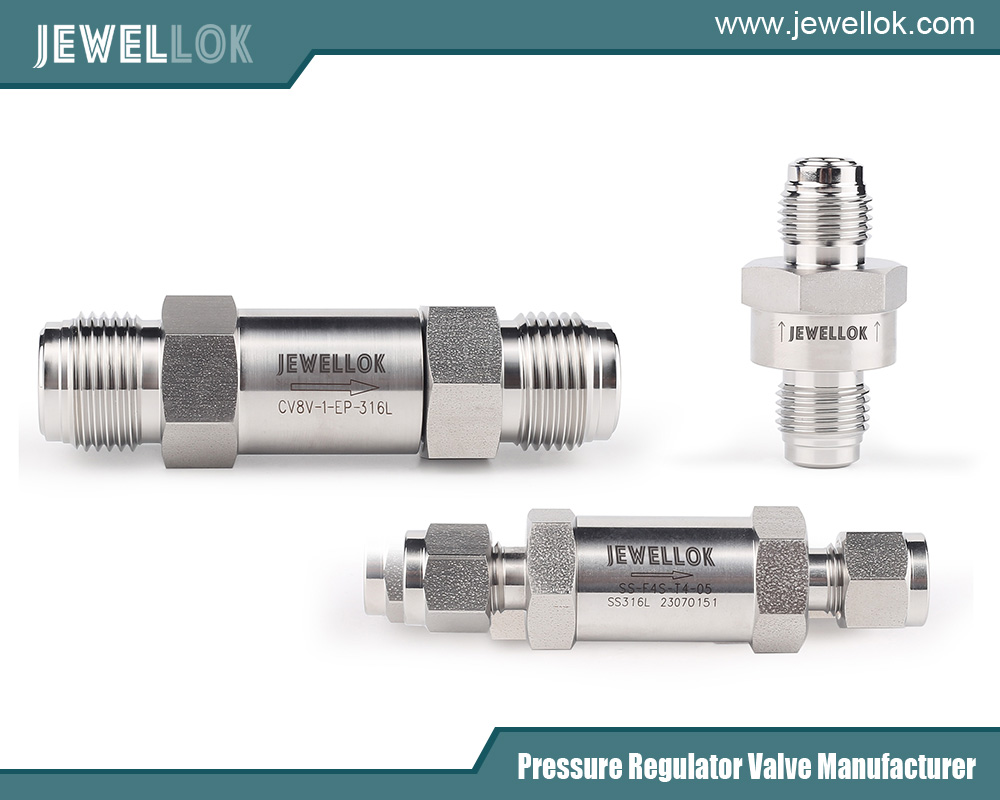
Influencing Factors of the Expected Service Life of Ultra High Purity Diaphragm Valves
I. The Key Role of Materials
The materials of key components of ultra high purity diaphragm valves, such as the valve body and diaphragm, have a decisive impact on their service life. The valve body mostly uses 316L VIM – VAR stainless steel. This material has excellent corrosion resistance and high strength, which can adapt to a variety of complex working environments and effectively extend the overall service life of the valve. For example, in the semiconductor manufacturing process, various corrosive gases and chemical reagents are involved. The valve body made of 316L VIM – VAR stainless steel can resist the erosion of these media and ensure the integrity of the valve structure.
The selection of diaphragm materials is also extremely important, such as cobalt-based superalloys, modified polytetrafluoroethylene (PTFE), etc. The diaphragm made of cobalt-based superalloy has good strength and fatigue resistance, and is suitable for working conditions that require frequent opening and closing. The modified PTFE diaphragm has excellent chemical stability and low friction coefficient, which can effectively reduce adhesion and wear with the medium and perform well in the transportation of high-purity chemical media. If the performance of the diaphragm material is not good, it is easy to have problems such as fatigue fracture and deformation during frequent opening and closing processes, resulting in valve failure.
II. Challenges of Working Conditions
- Pressure and Temperature: Working pressure and temperature are important working condition factors that affect the service life of the valve. When the valve works under too high pressure, the stress on the valve body and diaphragm increases, which may lead to a decrease in sealing performance, component deformation, or even rupture. For example, under working conditions exceeding the rated pressure of the valve, the diaphragm may be torn due to excessive pressure. The influence of temperature cannot be ignored either. Too high or too low temperature will affect the performance of the valve material. In a high-temperature environment, the mechanical properties of the material may decrease, resulting in a decrease in the sealing performance and structural strength of the valve. In a low-temperature environment, some materials may become brittle, increasing the risk of rupture.
- Medium Characteristics: The media transported by ultra high purity diaphragm valves usually have characteristics such as high purity and strong corrosiveness. If the medium is highly corrosive, it will gradually erode the valve body and diaphragm, shortening the service life of the valve. For example, in the pharmaceutical industry, some chemical agents have strong corrosiveness to the valve materials. If the valve materials are not corrosion-resistant, problems such as corrosion perforation will soon occur, affecting the normal use of the valve. At the same time, particulate impurities in the medium may also scratch the diaphragm or wear the valve seat, destroying the sealing performance of the valve and thus reducing the service life of the valve.
III. The Test of Usage Frequency
The usage frequency of the valve also has a significant impact on its service life. Frequent opening and closing actions will cause the diaphragm to be continuously stretched and compressed, making it prone to fatigue damage. Take the atomic layer deposition process in semiconductor manufacturing as an example. This process requires frequent control of the flow and on-off of gases, and the usage frequency of ultra high purity diaphragm valves is extremely high, which puts forward high requirements for the fatigue resistance of the diaphragm. In contrast, for valves with a lower usage frequency, the wear rate of their diaphragms and other components will be relatively slower, and the service life will be correspondingly extended.
The expected service life of different types and brands of ultra high purity diaphragm valves varies to some extent. Some high-end brand high-quality valves, through strict design and manufacturing processes, can have a service life of hundreds of thousands of times or even higher opening and closing cycles under normal working conditions. For example, some ultra high purity diaphragm valves specially designed for the semiconductor industry, through special optimized design and material selection, the service life of their diaphragms can reach more than 500,000 opening and closing cycles, while ordinary ultra high purity diaphragm valves may be around 100,000 to 300,000 opening and closing cycles. In practical applications, users can refer to the product specifications and performance parameters provided by the manufacturer to understand the expected service life of this model of valve under different working conditions.
Maintenance Work under Normal Operating Conditions
I. Key Points of Regular Inspection
- Appearance Inspection: Regularly conduct an appearance inspection of the ultra high purity diaphragm valve to check whether there are any abnormal conditions such as corrosion, scratches, and deformation on the valve surface. Especially for the valve body and connection parts, carefully check for any signs of leakage. If slight corrosion marks are found on the surface, they should be treated in a timely manner to prevent the corrosion from further expanding. For scratches and deformations, assess their impact on the valve performance, and repair or replace components if necessary.
- Sealing Performance Inspection: The sealing performance is one of the key performance indicators of ultra high purity diaphragm valves. Regularly check the sealing performance of the valve, which can be carried out through pressure tests or leakage detection. During the pressure test, charge the valve with a certain pressure of gas or liquid, and observe whether the pressure drops steadily to determine whether there is internal leakage. Leakage detection can use professional leakage detection instruments to detect whether there is medium leakage outside the valve. If a decrease in sealing performance is found, promptly find out the cause, which may be problems such as diaphragm damage, valve seat wear, or seal aging. Carry out corresponding repairs or replacements for specific problems.
- Diaphragm Inspection: The diaphragm is the core component of the ultra high purity diaphragm valve and also one of the most easily damaged components. Regularly check the condition of the diaphragm to see if there are any phenomena such as cracks, damage, deformation, or aging. You can open the valve to directly observe the surface condition of the diaphragm, or use some detection tools, such as an endoscope, to more comprehensively check the condition of the diaphragm. If slight damage to the diaphragm is found, it can be repaired according to the situation, but if the damage is severe, a new diaphragm should be replaced in a timely manner to ensure the normal operation of the valve.
II. The Importance of Cleaning and Maintenance
- Cleaning Methods: The cleaning of ultra high purity diaphragm valves is of great importance. It is necessary to ensure the cleanliness of the inside and outside of the valve to prevent impurities and contaminants from affecting the valve performance. For the cleaning of the inside of the valve, on-line cleaning (CIP) or off-line cleaning methods can be adopted. The CIP method is to clean the inside of the valve by circulating and conveying the cleaning solution without disassembling the valve. This method is suitable for some occasions with high cleanliness requirements and difficult disassembly. Off-line cleaning is to disassemble the valve and carry out a more thorough cleaning, including steps such as soaking, flushing, and wiping. During the cleaning process, select appropriate cleaning agents and avoid using cleaning agents that are corrosive to the valve materials.
- Maintenance Measures: Appropriately lubricate the moving parts of the valve to reduce wear and improve the operation flexibility and service life of the valve. For example, apply an appropriate amount of lubricant to the valve stem, actuator, and other components, but pay attention to the selection of lubricant. Use a lubricant that meets the ultra high purity requirements and will not contaminate the medium. At the same time, regularly check whether the connection parts of the valve are loose, such as bolts and nuts, and tighten them in a timely manner to ensure the structural stability of the valve.
III. Replacement of Vulnerable Parts
- Diaphragm Replacement: As mentioned before, the diaphragm is a vulnerable part of the ultra high purity diaphragm valve. When the diaphragm shows obvious cracks, damage, or a decrease in sealing performance, it must be replaced in a timely manner. When replacing the diaphragm, select a diaphragm that matches the original valve model and strictly follow the operation procedures for replacement. When removing the old diaphragm, operate carefully to avoid damaging the valve body and other components. When installing the new diaphragm, ensure that the diaphragm is installed correctly and has a good seal to prevent problems such as leakage.
- Seal Replacement: In addition to the diaphragm, the seals of the valve are also one of the vulnerable parts. As the usage time increases, the seals may age and wear, resulting in a decrease in sealing performance. When the seals show signs of aging, deformation, or damage, replace the new seals in a timely manner. When selecting seals, consider the compatibility of their materials with the medium and the reliability of the sealing performance to ensure that the replaced seals can meet the usage requirements of the valve.
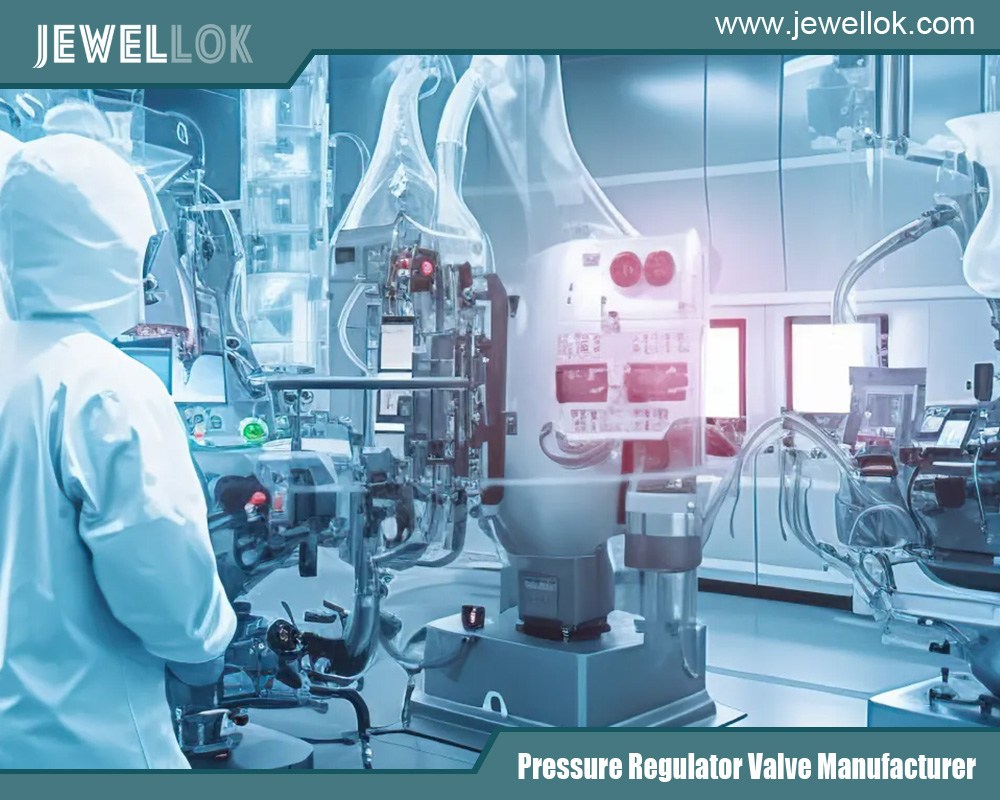
Analysis of Maintenance Cycle and Cost
I. Determination of the Maintenance Cycle
The maintenance cycle of ultra high purity diaphragm valves should be determined according to the actual usage situation. For valves with a high usage frequency and complex working conditions, the maintenance cycle should be relatively shortened; for valves with a low usage frequency and stable working conditions, the maintenance cycle can be appropriately extended. In industries such as semiconductor manufacturing, due to the extremely high requirements for the reliability of valves in the production process, it is generally recommended to inspect the valves once a week or a month, and carry out a comprehensive maintenance every 3 to 6 months. In some non-critical production links in the pharmaceutical industry where the valve usage frequency is low, the valves can be inspected once a quarter and comprehensively maintained once a year.
II. Composition of Maintenance Costs
- Labor Cost: Maintenance work requires professional technicians to operate, and labor cost is an important part of the maintenance cost. It includes the wages of technicians, training costs, and overtime costs incurred due to maintenance work. The professional level and experience of technicians have a direct impact on the efficiency and quality of maintenance work. Therefore, enterprises need to invest a certain cost to cultivate and improve the skills of technicians.
- Material Cost: Vulnerable parts that need to be replaced during the maintenance process, such as diaphragms, seals, etc., as well as cleaning agents, lubricants, etc. required for cleaning and lubrication, all constitute the material cost. High-quality vulnerable parts and maintenance materials are relatively expensive in price, but they can ensure the performance and service life of the valve. In the long run, it helps to reduce the overall maintenance cost. The prices of vulnerable parts of different brands and qualities vary greatly. For example, the price of imported high-quality diaphragms may be several times that of domestic ordinary diaphragms, but they have obvious advantages in performance and service life.
- Equipment Cost: In order to carry out maintenance work, some professional detection equipment and tools may be required, such as pressure testers, leakage detectors, endoscopes, etc. The purchase, maintenance, and calibration costs of these equipment should also be included in the maintenance cost. In addition, if the valve fails and needs to be repaired, some maintenance equipment and tools may also be required, such as welding equipment, machining machine tools, etc., further increasing the maintenance cost.
III. Strategies for Reducing Maintenance Costs
- Select High-Quality Products: When purchasing ultra high purity diaphragm valves, choose products with reliable quality and good brand reputation. Although the initial purchase cost may be higher, due to their stable performance and long service life, they can effectively reduce the number of subsequent maintenance times and maintenance costs. High-quality valves usually adopt more advanced technologies and processes in the design and manufacturing process, and the material quality is also more guaranteed. They can better adapt to complex working conditions and reduce the probability of failure.
- Optimize the Maintenance Plan: According to the actual usage situation of the valve, formulate a reasonable maintenance plan to avoid excessive maintenance or insufficient maintenance. Through the monitoring and analysis of the valve operation data, adjust the maintenance cycle and maintenance content in a timely manner to improve the pertinence and effectiveness of the maintenance work. For example, use an intelligent monitoring system to monitor the working status of the valve in real time, predict the possible faults of the valve in advance according to the monitoring data, and carry out maintenance in advance to avoid greater losses caused after the fault occurs.
- Train Maintenance Personnel: Strengthen the training of maintenance personnel to improve their professional skills and maintenance level, so that they can accurately judge the cause of valve faults and take effective repair measures. Skilled maintenance personnel can complete the maintenance work in a shorter time, reducing the production losses caused by shutdown maintenance, and at the same time, they can better ensure the maintenance quality and extend the service life of the valve.
The service life and maintenance work of ultra high purity diaphragm valves are comprehensive issues, involving multiple aspects such as material selection, working conditions, usage frequency, and maintenance measures. Only by fully understanding these factors and taking effective measures for management and maintenance can we ensure that ultra high purity diaphragm valves operate stably and reliably in a high-requirement production environment, while reducing maintenance costs and improving production efficiency and economic benefits.
For more about analysis of the service life and maintenance key points of ultra high purity diaphragm valves, you can pay a visit to Jewellok at https://www.jewellok.com/ for more info.
Recent Posts
Best Top 10 Specialty Gas Regulators Suppliers In Thailand
Best Top 10 Specialty Gas Regulators Manufacturers In India
Can Industrial Gas Regulators Be Used In Laboratories?
Tags
Recommended Products
-
772L Male Branch Tee | Stainless Steel High-Purity Tube Fitting Male Branch Tee
-
765LR Reducing Tee | Stainless Steel 316 High Purity Butt Weld Fittings Metal Face Seal For Welding Pipe Fitting Reducing Tee
-
Long Gland LG Series For Ultra High Purity Gas And Chemical Delivery Systems
-
764LR Stainless Steel 316 Reducing Tee UHP Fitting Automatic Buttweld Reducing Tee
-
Semi Automatic Gas Cabinet Gas Panels High Purity Gas Delivery Systems JW-200-GC
-
Stainless Steel High Purity High Temperature Pneumatic Actuated Ball Valves JBV2 Series
-
JR1300 Series Ultra High Purity Single Stage Regulator High Flow Line Regulator For Ultra High Purity Intermediate Flow
-
Ultra High Purity Oxygen Pressure Gauge For Semiconductor Gases JG Series Pressure Instruments For Semiconductor Manufacturing