Blog
Jewellok is a professional pressure regulator and valve manufacturer and supplier.
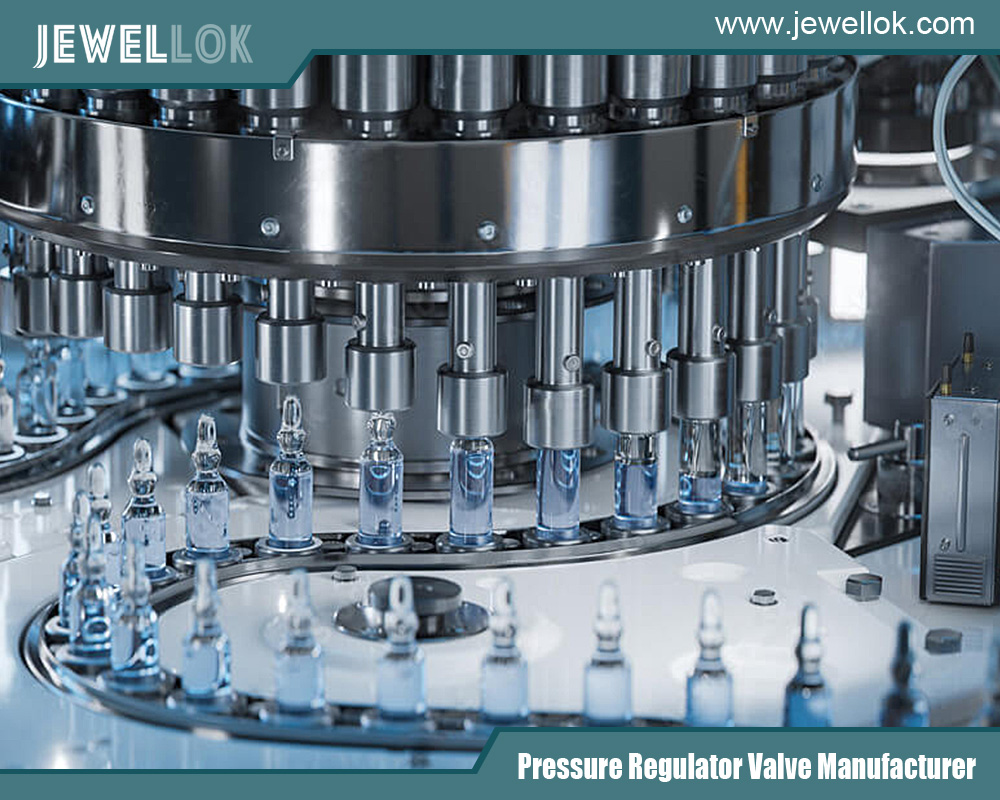
A Comprehensive Analysis of the Installation and Maintenance of Ultra High Purity Diaphragm Valves
- Pressure Regulator Valve Manufacturer
- 1/2 gas pressure regulator, 2 inch irrigation solenoid valve, 6mm compression union, 6mm equivalent, adjustable propane pressure regulator, adjustable propane regulator, argon gas pressure regulator, argon hose fitting, characteristics of pressure, diaphragm suppliers, Diaphragm Valve Manufacturers, gas filter, gas manifold system, gas regulator, gas used in semiconductor manufacturing, high pressure flexible hose, high purity regulator, how a solenoid works, how does pressure regulator work, how solenoid valves work, industrial grade purity, industrial regulators, low pressure regulator, oxygen regulator gauge, pressure gauge manufacturers, relief vs safety valve, safety relief valve vs pressure relief valve, safety valve and relief valve difference, safety valve vs relief valve, semiconductor gas, solenoid water valve, stainless pressure regulator, stainless steel 1/4 in, Ultra High Purity Diaphragm Valves, what is a gas pressure regulator
- No Comments
A Comprehensive Analysis of the Installation and Maintenance of Ultra High Purity Diaphragm Valves
Ultra high purity diaphragm valves play a crucial role in fields with extremely high requirements for fluid purity, such as semiconductor manufacturing, pharmaceuticals, and the preparation of ultra-pure water for electronics. Their correct installation and regular maintenance are essential for ensuring the stable operation of the system and maintaining the ultra-pure quality of the fluid. Even a slight oversight may introduce impurities, affecting the entire production process and causing serious losses.
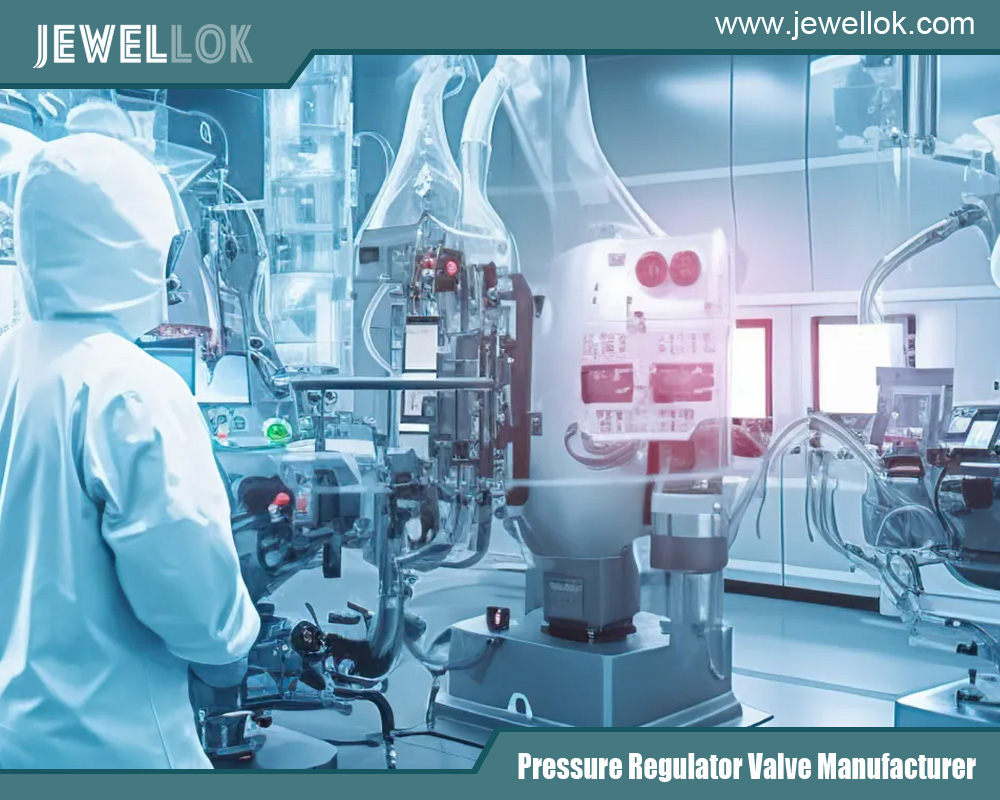
Overview of Ultra High Purity Diaphragm Valves
Ultra high purity diaphragm valves are a type of valve specifically designed for the control of ultra-pure fluids. Their uniqueness lies in the use of a corrosion-resistant and pollution-resistant diaphragm to separate the fluid from other parts of the valve, preventing the fluid from being contaminated. They possess excellent sealing performance, precise flow control capabilities, and the characteristics to adapt to harsh chemical environments.
Pre-installation Preparations
- Environmental Assessment: The installation environment should be kept clean, and it is best to carry out the operation in a dust-free workshop. Dust particles in the air, once they enter the valve or pipeline system, may contaminate the ultra-pure fluid. The temperature and humidity of the installation area also need to be controlled within an appropriate range to prevent the generation of condensed water due to changes in temperature and humidity, which may further contaminate the system.
- Component Inspection: Carefully inspect all components of the ultra high purity diaphragm valve, including the valve body, diaphragm, valve stem, and seals, for any damage, deformation, or impurity adhesion. As the core component, the diaphragm especially needs to be ensured to have no scratches, perforations, or other defects, because even a tiny flaw may lead to fluid leakage and contamination.
- Tool Preparation: Prepare dedicated clean installation tools, such as clean wrenches and screwdrivers. The tools need to go through strict cleaning and drying processes before use to avoid the impurities carried by the tools themselves from contaminating the valve.
Special Requirements and Precautions for Installation
- Pipeline Connection
- Welding Connection: If the welding method is used to connect the valve and the pipeline, inert gas shielded welding, such as argon arc welding, should be employed. This can prevent metal oxidation during the welding process from generating impurities that mix into the fluid. Before welding, the welding parts of the pipeline and the valve should be thoroughly cleaned and polished to remove surface oil stains, oxides, etc. The welding parameters need to be strictly controlled to ensure the welding quality and avoid defects such as poor welding and air holes.
- Compression Fitting Connection: When using a compression fitting connection, ensure the precision and cleanliness of the compression fitting and the joint. During the installation process, tighten the nut evenly to make the compression fitting fit closely to the interface between the pipeline and the valve to achieve a good sealing effect. Over-tightening may damage the compression fitting and the pipeline, while insufficient tightening will lead to leakage.
- Valve Installation Direction: Install the valve strictly according to the fluid flow direction indicated on the valve to ensure that the diaphragm works under the correct force direction. If the installation direction is wrong, it will not only affect the normal opening and closing of the valve and flow control but also accelerate the wear of the diaphragm and reduce the service life of the valve.
- Avoid Stress Concentration: During installation, ensure that the valve is not subjected to additional external forces and avoid stress concentration on the valve caused by improper pipeline installation. This may cause the valve body to deform and damage the sealing performance of the diaphragm. Stress can be eliminated by reasonably setting pipeline supports and using flexible connection pipe fittings.
- Clean Installation Process: Installers need to wear clean clothes, gloves, and masks to avoid human hair, dandruff, and other pollutants from coming into contact with the valve. During the installation process, clean the inside of the valve and the pipeline multiple times. It can be flushed with ultra-pure water and then dried with clean nitrogen. It is strictly prohibited to use cleaning agents that may leave impurities.
Key Points of Regular Maintenance
- Appearance Inspection: Regularly inspect the appearance of the valve, check whether there are signs of corrosion and deformation on the valve body, and whether there are aging, cracking, etc. on the diaphragm. If slight corrosion is found on the surface of the valve body, it should be treated in a timely manner to prevent the corrosion from expanding further. For minor damages to the diaphragm, it needs to be replaced in a timely manner to avoid affecting the performance of the valve and the purity of the fluid.
- Sealing Test: Use special testing equipment to conduct a sealing test on the valve. It can adopt air pressure testing or hydraulic pressure testing, and check whether there is any leakage of the valve under the specified pressure. If leakage is found, first check whether the seal is damaged or improperly installed, and replace or adjust the seal in a timely manner.
- Diaphragm Replacement: According to the usage frequency and working environment of the valve, formulate a reasonable diaphragm replacement cycle. Generally speaking, in working conditions with high corrosion and high flow rate, the diaphragm replacement cycle is relatively short. When replacing the diaphragm, it is necessary to follow the operation procedures strictly to ensure that the new diaphragm is installed correctly without wrinkles, twists, and other phenomena.
- Cleaning Maintenance: Regularly clean the inside of the valve to remove possible accumulated impurities and dirt. It can be soaked and flushed with ultra-pure water, and then use a cleaning agent with good chemical compatibility for auxiliary cleaning. Finally, rinse it thoroughly with ultra-pure water and dry it with clean nitrogen. Avoid using cleaning tools and cleaning agents that will leave impurities.
- Lubrication and Maintenance: Carry out appropriate lubrication on the moving parts such as the valve stem. Select lubricants that meet the ultra-pure requirements to prevent the generation of particle impurities due to the wear of the parts caused by friction, which may contaminate the fluid. The lubrication frequency is determined according to the usage situation of the valve, and it is generally checked and replenished with lubricant during each maintenance.
Maintenance Records and Data Analysis
Record the maintenance content in detail each time, including the maintenance time, maintenance items, replaced components, test results, etc. Through the analysis of the maintenance records, potential problems in the operation of the valve can be found in a timely manner, the possibility of a fault occurrence can be predicted, and the maintenance plan can be optimized. For example, if it is found that the sealing test results of a certain valve are gradually deteriorating, a more detailed inspection and maintenance can be arranged in advance to avoid sudden leakage accidents.
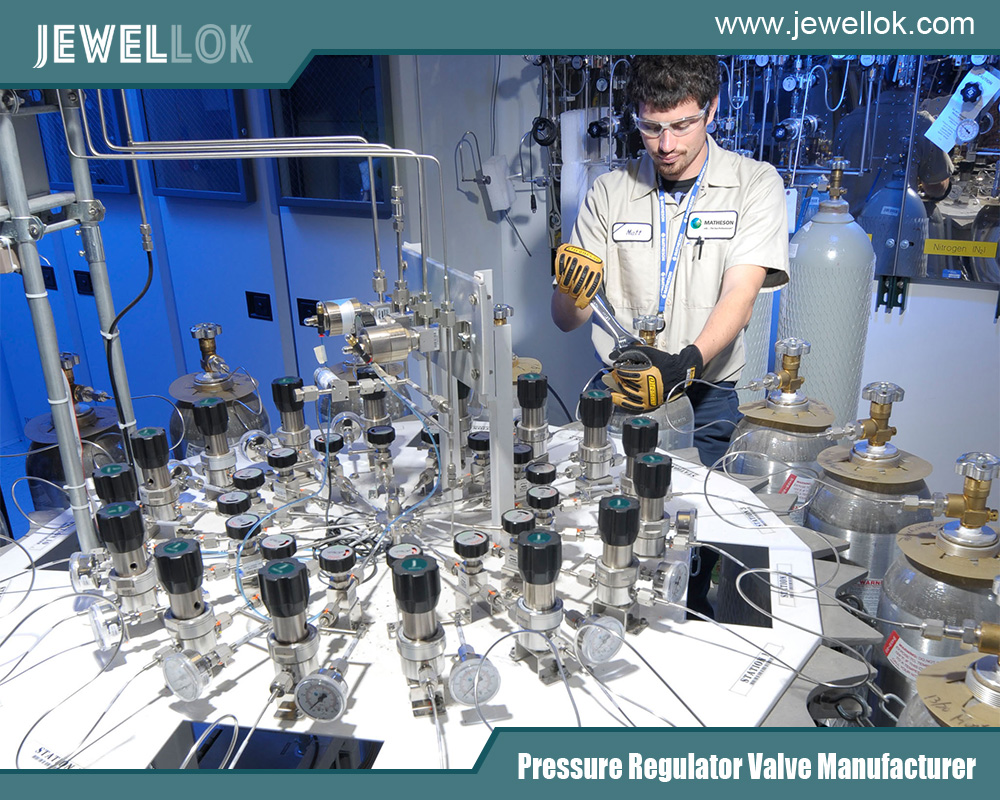
Conclusion
The correct installation and regular maintenance of ultra high purity diaphragm valves are the keys to ensuring their reliable operation in ultra-pure fluid systems. From the meticulous preparations before installation, to the strict requirements during the installation process, and then to the comprehensive implementation of regular maintenance, each link is closely linked. Only by attaching great importance to these aspects can the ultra high purity diaphragm valve play its best performance, maintain the ultra-pure quality of the fluid, and provide a strong guarantee for high-quality production in related industries. With the continuous development of technology, the installation and maintenance technologies of ultra high purity diaphragm valves will also be continuously improved in the future to meet more stringent production requirements.
For more about a comprehensive analysis of the installation and maintenance of ultra high purity diaphragm valves, you can pay a visit to Jewellok at https://www.jewellok.com/ for more info.
Recent Posts
Best Top 10 Specialty Gas Regulators Suppliers In Thailand
Best Top 10 Specialty Gas Regulators Manufacturers In India
Can Industrial Gas Regulators Be Used In Laboratories?
Tags
Recommended Products
-
Stainless Steel Ultra High Purity (UHP) High Pressure Manual Diaphragm Valve
-
T-BOX JW-TB-C Special Gas Delivery System Gas Valve Manifold Boxes
-
Flow Control Stainless Steel Low Pressure Manual Diaphragm Valve For High Purity And Ultra High Purity Gases
-
Semi Automatic Gas Cabinet Gas Panels High Purity Gas Delivery Systems JW-200-GC
-
Low Pressure High Flow Line Pressure Regulators And Control Valves JSR-4L Series For Laboratory Pressure Control
-
316L Stainless Steel Tube Butt Weld Reducing Fittings Union Reducer RW Series Ultrahigh Purity Process
-
Stainless Steel High Purity High Temperature Pneumatic Actuated Ball Valves JBV2 Series
-
Stainless Steel Mini Elbow Mini Tee Mini Cross Mini Tribow Ultrahigh Purity Mini Butt Weld Fittings