Blog
Jewellok is a professional pressure regulator and valve manufacturer and supplier.
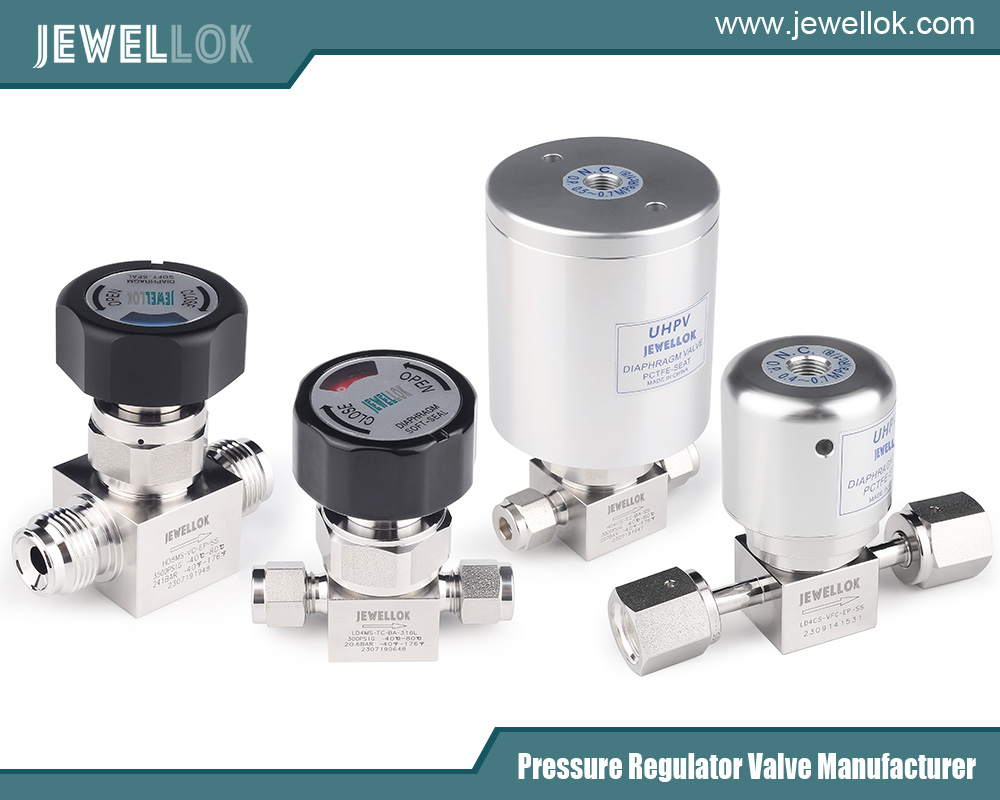
Can Industrial Gas Regulators Be Used In Laboratories?
- Pressure Regulator Valve Manufacturer
- can industrial gas regulator be used in laboratory, industrial gas regulator, industrial gas regulator china, industrial gas regulator manufacturer, industrial gas regulator supplier, Industrial Gas Regulator Wholesale Trader from Mumbai, Industrial Gas Regulators, Industrial Gas Regulators Manufacturer from Pune, industrial lng pressure reducing regulator, natural gas pressure reducing valve, natural gas regulator for house, natural gas regulator high pressure
- No Comments
Can Industrial Gas Regulators Be Used In Laboratories?
Gas regulators are vital devices employed across various sectors to manage the pressure of gases from high-pressure sources, such as cylinders, to levels suitable for specific applications. In industrial environments, they facilitate processes like welding, cutting, and manufacturing, often handling substantial gas volumes. Conversely, in laboratories, gas regulators support precise scientific tasks, such as gas chromatography (GC), spectroscopy, or maintaining controlled environments, where accuracy and stability are paramount. This article delves into the question: Can industrial gas regulators be used in laboratory settings? To address this, we will explore the differences between industrial and laboratory gas regulators, examine potential scenarios for their use, assess associated risks, and consider whether adaptations could make them viable, culminating in practical recommendations.
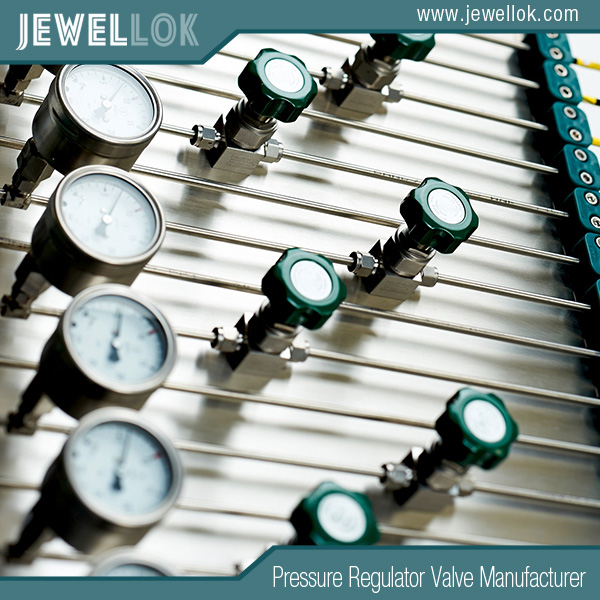
Understanding Gas Regulators: Purpose and Function
Gas regulators serve a fundamental purpose: they reduce the high pressure of stored gas to a lower, usable pressure while maintaining consistent flow. In industrial settings, regulators are built to withstand rugged conditions and deliver high flow rates for tasks requiring significant gas volumes, such as powering machinery or supporting large-scale chemical processes. In laboratories, regulators are integral to experiments and analytical instruments, where they must deliver gas with exceptional precision to ensure reliable results. The question of interchangeability hinges on whether industrial regulators can meet the stringent demands of laboratory applications.
Differences Between Industrial and Laboratory Gas Regulators
To determine if industrial gas regulators can substitute for laboratory ones, we must first compare their design and performance characteristics across several key dimensions.
Precision and Accuracy
Laboratories demand regulators with high precision and accuracy. Analytical techniques like GC or mass spectrometry rely on stable, repeatable gas flows—any variation can skew results or render experiments invalid. Laboratory regulators are engineered to maintain tight pressure control, often within narrow tolerances. Industrial regulators, however, prioritize robustness over finesse. Designed for high-flow applications, they may exhibit greater pressure fluctuations, making them less suitable for tasks requiring meticulous control.
Material Compatibility
The materials used in regulators are critical, especially in laboratories handling reactive, corrosive, or high-purity gases. Laboratory regulators are often constructed from stainless steel, specialized alloys, or inert polymers to prevent reactions with gases or contamination of samples. Industrial regulators, built for durability and cost-efficiency, may use materials like brass or less resistant alloys, which could degrade or introduce impurities when exposed to certain laboratory gases, compromising experimental integrity.
Safety Standards
Safety is non-negotiable in both settings, but laboratories face unique challenges. Handling hazardous gases—flammable, toxic, or reactive—requires regulators that meet rigorous standards, such as those from the Occupational Safety and Health Administration (OSHA) or the Environmental Protection Agency (EPA). Laboratory regulators are designed and certified to minimize risks like leaks or pressure surges. Industrial regulators, while safe for their intended use, may not comply with laboratory-specific safety certifications, posing potential hazards or regulatory violations.
Additional Features
Laboratory regulators often incorporate specialized features tailored to scientific needs. Built-in filters remove particulates, purge valves allow safe gas venting, and specific connectors ensure compatibility with lab equipment. Industrial regulators typically lack these enhancements, focusing on basic pressure regulation, which may limit their adaptability to laboratory setups.
Cost Considerations
Cost is a practical differentiator. Industrial regulators are generally less expensive due to their simpler design and mass production, appealing to budget-conscious laboratories. However, this initial saving must be balanced against potential performance trade-offs, as cheaper equipment could lead to costly experimental failures or safety incidents.
Scenarios Where Industrial Regulators Might Be Used in Laboratories
Despite these differences, certain laboratory contexts might accommodate industrial gas regulators. Let’s explore these possibilities.
Teaching Laboratories
In educational settings, the focus is often on demonstrating concepts rather than achieving cutting-edge precision. For example, a chemistry class illustrating gas laws might use nitrogen or air at controlled pressures where exact flow stability is secondary to cost and availability. Here, an industrial regulator could suffice, provided it delivers the required pressure safely and reliably.
Field Laboratories
Laboratories operating in remote or rugged environments, such as environmental monitoring stations, prioritize durability. Industrial regulators, designed for tough conditions, might outperform delicate laboratory models in these settings. For instance, monitoring air quality with compressed air might not demand the precision of a lab-grade regulator, making an industrial option viable if it meets basic performance needs.
Research Simulating Industrial Processes
Some research labs aim to replicate industrial conditions, such as developing manufacturing processes or testing large-scale gas delivery systems. In these cases, industrial regulators align with the experimental goals, providing high flow rates and robustness that mirror real-world applications. A lab studying industrial welding gases, for example, might benefit from using the same regulators as the industry.
Less Critical Applications
Not all laboratory tasks require high precision. Using compressed air for pneumatic controls, powering tools, or maintaining general utilities might tolerate an industrial regulator’s capabilities, especially if gas purity and exact flow are not critical. However, even here, labs often specify oil-free or filtered air, which industrial regulators may not guarantee without modification.
Risks and Downsides of Using Industrial Regulators in Laboratories
While these scenarios suggest potential uses, significant risks accompany the adoption of industrial regulators in labs.
Safety Concerns
Industrial regulators may lack the fail-safes or certifications required for laboratory environments. A regulator not designed to handle a toxic gas like hydrogen sulfide could leak, endangering personnel. Similarly, pressure surges from imprecise control might damage equipment or cause accidents, a risk amplified in confined lab spaces.
Compliance with Standards
Laboratories must adhere to strict regulations governing equipment use. An industrial regulator lacking laboratory certification might violate OSHA or EPA guidelines, leading to fines, legal liability, or shutdowns if an incident occurs. For instance, a university lab using an uncertified regulator could face scrutiny during an audit.
Impact on Experimental Accuracy
Precision is the cornerstone of scientific research. An industrial regulator’s inability to maintain stable pressure could disrupt experiments, such as skewing GC peaks or altering reaction conditions in a synthesis lab. The cost of repeating experiments or discarding unreliable data often outweighs any savings from using cheaper equipment.
Maintenance and Calibration Challenges
Laboratory regulators are designed for regular calibration to ensure accuracy, often with accessible adjustment mechanisms. Industrial regulators may require specialized tools or procedures, complicating maintenance. In a lab needing frequent recalibration—say, for a long-term study—an industrial model could increase downtime and costs.
Adapting Industrial Regulators for Laboratory Use
Could industrial regulators be modified to meet laboratory needs? Let’s consider some approaches.
Two-Stage Regulation Systems
A common strategy is pairing an industrial regulator with a secondary, laboratory-grade regulator or flow controller. The industrial unit reduces high cylinder pressure to an intermediate level, while the second stage fine-tunes it for precision. For example, delivering helium to a mass spectrometer might use this setup, with the industrial regulator handling the initial drop and a lab regulator ensuring stability. This hybrid approach could work but adds complexity and cost.
Adding Filters or Components
To address purity concerns, filters or purifiers could be installed downstream of an industrial regulator. For instance, a particulate filter might clean compressed air for a lab application. However, this doesn’t resolve material compatibility issues within the regulator itself, and additional components introduce potential failure points, such as leaks at connections.
Limitations of Adaptations
Adaptations can’t fully bridge all gaps. Safety certifications remain a hurdle—modified equipment might still lack official approval. Likewise, inherent design limitations, like coarse pressure adjustment, persist despite add-ons. A lab needing consistent low-flow nitrogen for spectroscopy would likely find such a setup inadequate compared to a purpose-built regulator.
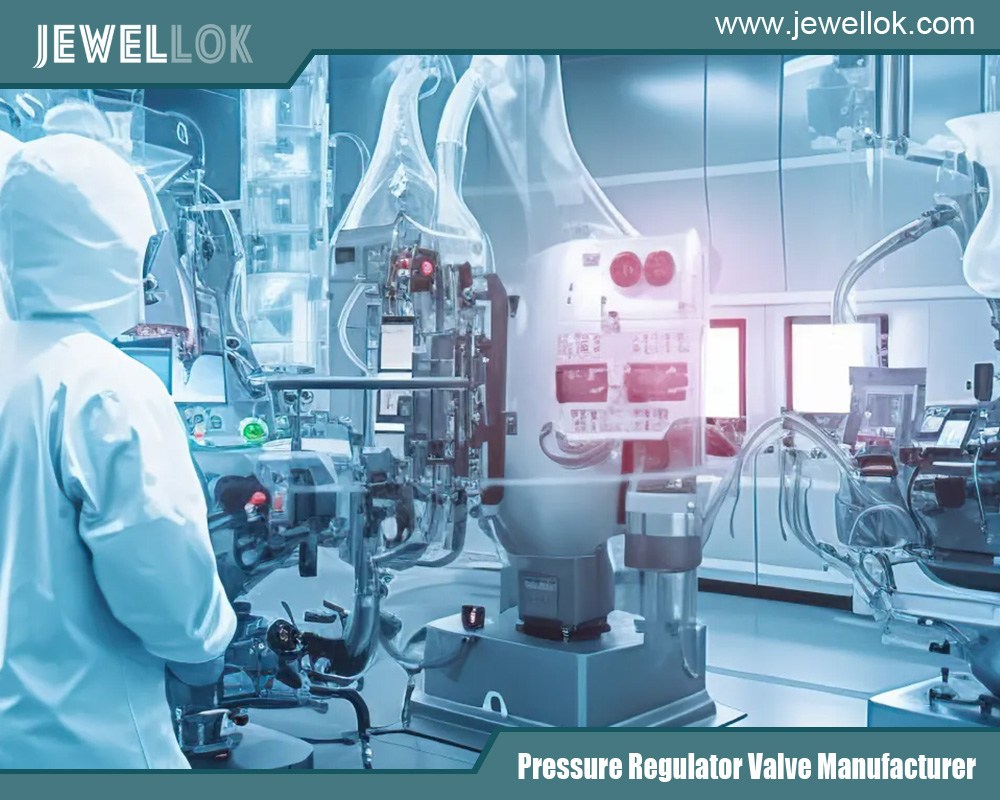
Conclusion and Recommendations
Industrial and laboratory gas regulators, while sharing a core function, diverge significantly in design and application. Laboratory regulators excel in precision, material compatibility, and safety compliance, making them the standard for scientific work. Industrial regulators, optimized for high flow and durability, fall short in most lab contexts, particularly where accuracy and safety are paramount.
However, their use isn’t universally precluded. In teaching labs, field settings, or research mimicking industrial conditions, industrial regulators might serve adequately if they meet specific pressure, flow, and safety criteria. Cost savings could justify their use in non-critical applications, but only with careful evaluation.
The risks—safety hazards, regulatory non-compliance, and compromised accuracy—often outweigh benefits unless mitigated by adaptations. Even then, modifications like secondary regulators or filters may not fully align industrial models with lab standards, suggesting a purpose-built solution is usually preferable.
Practical Recommendations
Critical Applications: For experiments requiring high precision, purity, or safety (e.g., analytical chemistry with hazardous gases), invest in laboratory-grade regulators to ensure reliability and compliance.
Teaching or Non-Critical Use: Consider industrial regulators for educational demos or utility tasks, but verify they meet safety and performance needs through testing and documentation.
Adaptations: If adapting industrial regulators, validate the entire system—regulator plus add-ons—for accuracy, safety, and compatibility, and document compliance with lab protocols.
Safety First: Prioritize equipment certified for laboratory use, especially with hazardous gases, to avoid risks and legal issues.
In most cases, the prudent choice is a laboratory-grade regulator tailored to scientific demands. While industrial regulators offer cost and durability advantages, their limitations make them a niche rather than a universal solution. By aligning equipment selection with specific laboratory goals, researchers can balance performance, safety, and budget effectively.
For more about can industrial gas regulator be used in laboratory, you can pay a visit to Jewellok at https://www.jewellok.com/laboratory/ for more info.
Recent Posts
Tags
Recommended Products
-
Stainless Steel Single Stage Semiconductor Grade Pressure Control Module Pressure Control Panels JSP-6A Series
-
774L Stainless Steel UHP Fittings Butt Weld Bulkhead Union For High Flow Special Gas Fluid
-
Fully Automated Gas Cabinet For Precise UHP Gas Delivery And High Purity Gas Delivery Systems JW-300-GC
-
Line And Panel Mounting Adjustable Low Pressure Propane And Nitrogen Pressure Regulator JSR-3L & JSR-3LP Series
-
T-BOX JW-TB-C Special Gas Delivery System Gas Valve Manifold Boxes
-
JF Series In-Line Gas Filters | High Purity High Precision High Flow Semiconductor Gas Filter Gas Filtration & Purification
-
772 LF Female Branch Tee | Stainless Steel Tube Fitting Female Branch Tee 1/2 in. Tube OD x 1/2 in. Tube OD x 3/8 in. Female NPT
-
High Purity Chemical Dispense System & Packing System For Semiconductors JW-200L-CDM & JW-1000L-CDM