Blog
Jewellok is a professional pressure regulator and valve manufacturer and supplier.
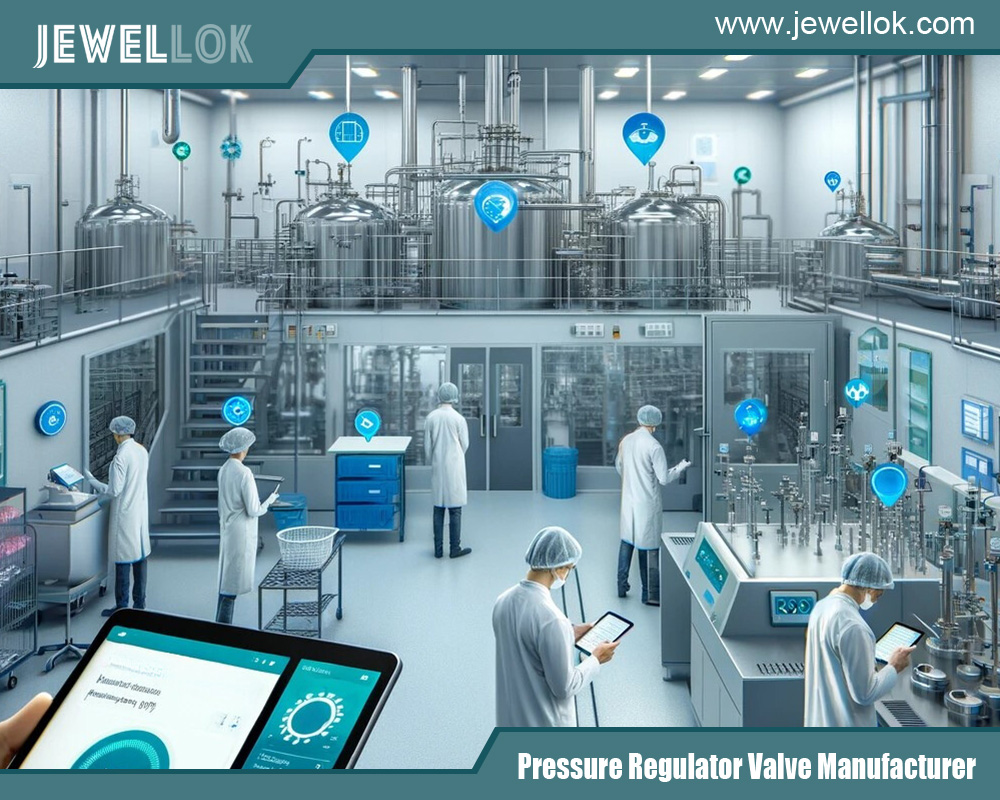
Integration and Performance Optimization of Ultra High Purity Diaphragm Valves in Automated Control Systems
- Pressure Regulator Valve Manufacturer
- 1inch of water, adjustable low pressure propane regulator, air compressor non return valve, argon hose fittings, compression fitting 6mm, electric water valve 12v, fire arrestor, fluid system components, how a gas pressure regulator works, how a pressure regulator works, how do pressure regulators work, how often should pressure relief valves be replaced, how solenoid works, humming propane regulator, oxygen cylinder manifold, pressure relief valve vs safety valve, propane adjustable pressure regulator, propane manifold with valves, safety or relief valves, safety relief valve vs safety valve, safety valve vs pressure relief valve, second stage propaneregulator, solenoid valve for ammonia gas 2 inch pipe, timer water valve, Ultra High Purity Diaphragm Valves, ultra high purity diaphragm valves hotsale, ultra high purity diaphragm valves manufacturer, Ultra High Purity Diaphragm Valves OEM, ultra high purity diaphragm valves supplier, ultra high purity diaphragm valves wholesale
- No Comments
Integration and Performance Optimization of Ultra High Purity Diaphragm Valves in Automated Control Systems
In modern industrial production, especially in industries with extremely high requirements for medium purity, such as semiconductors, pharmaceuticals, and electronics, ultra high purity diaphragm valves play a crucial and vital role. With the rapid development of automation technology, the integration of ultra high purity diaphragm valves with automated control systems has become an inevitable trend to meet the strict requirements for fast and precise control in the production process. This article will deeply explore how ultra high purity diaphragm valves are integrated with automated control systems, as well as the realization and optimization of their response speed and control accuracy on automated production lines.
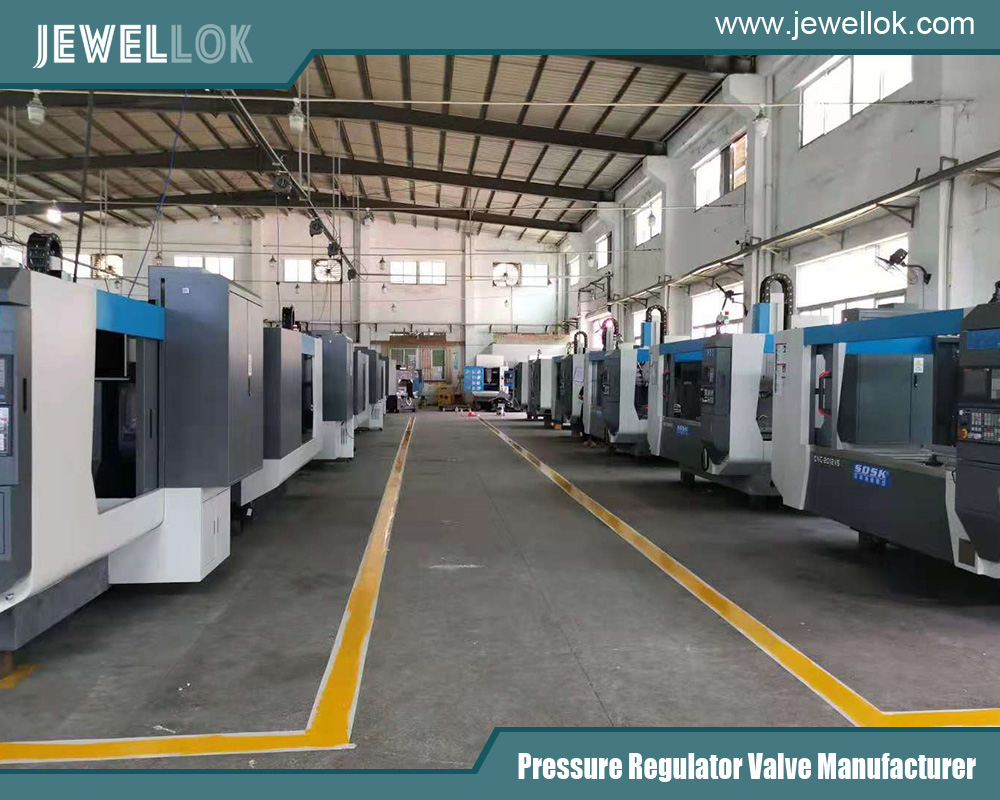
Working Principle and Characteristics of Ultra High Purity Diaphragm Valves
Working Principle
Ultra high purity diaphragm valves control the on-off and flow rate of fluids through the deformation of the diaphragm. The diaphragm separates the upstream and downstream chambers of the valve body. When the diaphragm moves upward, the fluid passage opens, allowing the medium to flow through; when the diaphragm moves downward and closely adheres to the valve seat, the fluid passage closes, achieving the shut-off function. This working mode avoids the direct contact between the medium and other components of the valve body, effectively preventing contamination and ensuring the high purity of the medium.
Characteristics
- High Purity: Special materials and manufacturing processes are adopted, such as 316L VIM-VAR stainless steel valve bodies and corrosion-resistant diaphragm materials, which can meet the transportation requirements of ultra high purity media, reducing the precipitation of impurities and contamination.
- Good Sealing Performance: The tight fit between the diaphragm and the valve seat can achieve reliable sealing, prevent medium leakage, and ensure the safety and stability of the production process.
- Corrosion Resistance: It is suitable for the transportation of various corrosive media and has a wide range of applications in the chemical industry, semiconductor manufacturing, and other fields.
- Simple Structure: Compared with other types of valves, the diaphragm valve has a relatively simple structure, which is easy to maintain and clean, reducing maintenance costs and downtime.
Integration Methods with Automated Control Systems
Hardware Connection
- Selection of Actuators: Common actuators include pneumatic actuators and electric actuators. Pneumatic actuators use compressed air as the power source, which has the advantages of fast response speed and large thrust, and is suitable for occasions requiring rapid action; electric actuators are driven by motors, with high control accuracy, and are convenient for realizing remote control and automatic adjustment. When integrating with the automated control system, the appropriate actuator should be selected according to specific process requirements and control accuracy.
- Signal Transmission Lines: Connect the automated control system to the actuator of the diaphragm valve through signal transmission lines. For pneumatic actuators, it is usually necessary to connect the solenoid valve lines that control the air source. The automated control system controls the on-off of the solenoid valve to achieve the action control of the pneumatic actuator; for electric actuators, it is necessary to connect the power lines and control signal lines. The control signals can be analog signals (such as 4-20mA current signals, 0-10V voltage signals) or digital signals (such as pulse signals, communication protocol signals, etc.), which are used to transmit control instructions and feedback the status information of the valve.
- Installation of Sensors: In order to realize the real-time monitoring of the valve status and fluid parameters, various sensors are usually installed on the valve. For example, position sensors are used to detect the opening and closing position of the diaphragm valve, pressure sensors are used to monitor the pressure of the fluid, and flow sensors are used to measure the flow rate of the fluid, etc. These sensors transmit the collected signals to the automated control system, so that the system can make real-time adjustments and controls according to the actual situation.
Software Communication and Control
- Communication Protocols: A specific communication protocol is required for data exchange between the automated control system and the ultra high purity diaphragm valve. Common communication protocols include Modbus, Profibus, DeviceNet, etc. The Modbus protocol is a widely used serial communication protocol, which has the characteristics of simplicity and reliability and supports a variety of physical interfaces such as RS-232 and RS-485; the Profibus protocol is mainly used in the field of industrial automation, with the characteristics of high speed and high reliability, and is suitable for complex automated control systems; the DeviceNet protocol is an open communication protocol based on the CAN bus, which has good real-time performance and interoperability and is often used to connect various industrial devices. During the integration process, it is necessary to ensure that the controller of the diaphragm valve and the automated control system support the same communication protocol and perform correct parameter settings.
- Control Algorithms: The automated control system precisely controls the diaphragm valve through preset control algorithms. According to the process requirements, control algorithms such as Proportional-Integral-Derivative (PID) control algorithm, fuzzy control algorithm, and adaptive control algorithm can be adopted. The PID control algorithm is a classic control algorithm. Through the proportional, integral, and derivative operations of the deviation signal, it outputs a control signal to adjust the opening degree of the valve, so as to achieve the precise control of parameters such as flow rate and pressure; the fuzzy control algorithm is based on fuzzy logic and fuzzy reasoning, and can effectively control complex nonlinear systems, which is suitable for occasions where it is difficult to establish an accurate mathematical model; the adaptive control algorithm can automatically adjust the control parameters according to the operating status of the system to adapt to different working conditions and improve the control performance.
Realization and Optimization of Response Speed and Control Accuracy
Response Speed
- Performance Optimization of Actuators: Select actuators with fast response speed, such as high-speed pneumatic actuators or high-performance electric actuators. For pneumatic actuators, the air source system can be optimized to ensure the stable supply and rapid response of compressed air; at the same time, the cylinder size and piston stroke of the actuator can be reasonably designed to reduce the motion inertia and improve the action speed. For electric actuators, high-torque motors and precise transmission devices are used to shorten the start-up and stop time of the motor and improve the response speed of the valve.
- Optimization of Signal Transmission and Processing: Reduce the delay of signal transmission, and use high-speed communication lines and efficient communication protocols. For example, use optical fiber communication instead of traditional cable communication to improve the speed and reliability of signal transmission; optimize the hardware and software of the automated control system to accelerate the processing and response speed of signals, and ensure that control instructions can be sent to the actuator of the diaphragm valve in a timely and accurate manner.
- System Integration Optimization: In the entire automated control system, all devices and modules are reasonably configured to reduce the complexity of the system and the signal transmission path. By optimizing the system architecture, the collaborative work between various devices can be realized, and the overall response speed of the system can be improved.
Control Accuracy
- Application of High-Precision Sensors: Install high-precision sensors to monitor fluid parameters such as flow rate, pressure, and temperature in real time. Through accurate measurement of these parameters, the automated control system can precisely adjust the opening degree of the diaphragm valve according to the actual situation to meet the requirements for fluid control accuracy in the production process. For example, using a flow sensor with an accuracy of ±0.5% and a pressure sensor with an accuracy of ±0.2% can provide accurate feedback information for the control system, enabling high-precision control of fluid flow rate and pressure.
- Optimization of Control Algorithms: Select the appropriate control algorithm according to specific process requirements and system characteristics and optimize it. For some occasions with extremely high requirements for control accuracy, advanced control algorithms such as adaptive control algorithms and model predictive control algorithms can be adopted. These algorithms can adjust the control parameters in real time according to the dynamic characteristics and changes of the system, improving the control accuracy and stability. At the same time, by optimizing and debugging the parameters of the control algorithm, it can better adapt to different working conditions and further improve the control accuracy.
- Valve Characteristic Compensation: Considering the characteristics of the ultra high purity diaphragm valve itself, such as the valve’s flow characteristic curve and leakage rate, etc., carry out characteristic compensation. By establishing a mathematical model of the valve, analyzing the flow characteristics and pressure loss of the valve at different opening degrees, and making corresponding compensation for the control signal of the valve in the control system to eliminate the influence of the valve characteristics on the control accuracy. For example, if the flow characteristic curve of the valve is nonlinear, the control signal can be linearized through software algorithms in the control system, so that there is a better linear relationship between the actual flow rate of the valve and the control signal, thereby improving the control accuracy.
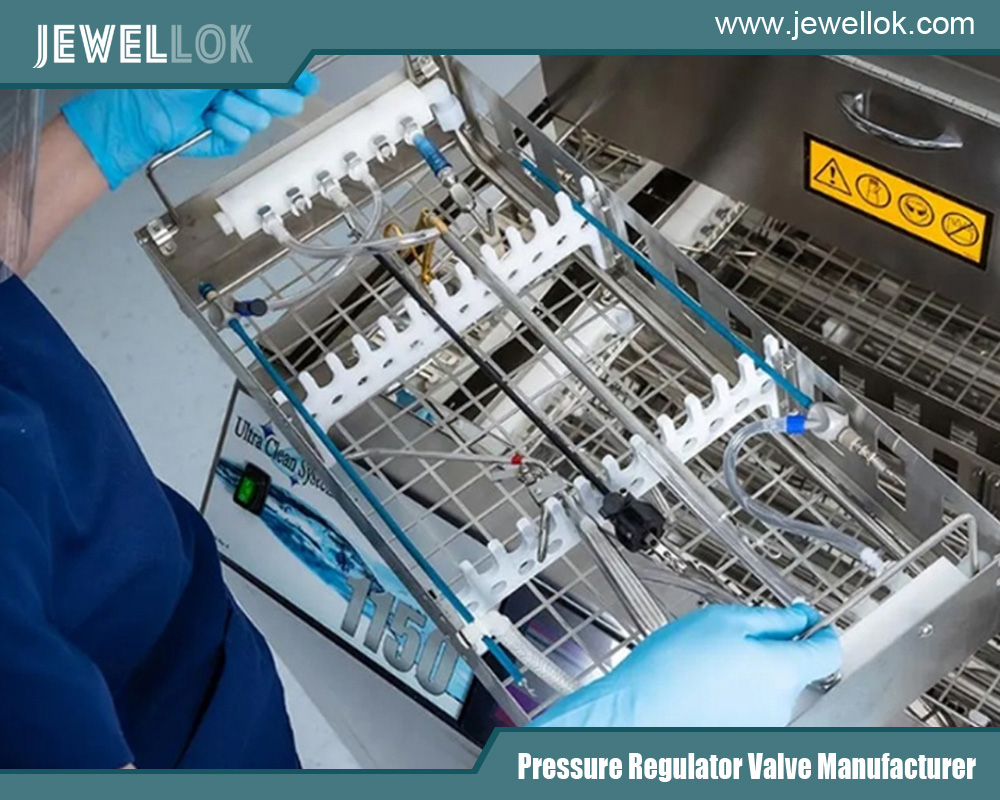
Conclusion
The integration of ultra high purity diaphragm valves with automated control systems is an inevitable trend in the development of modern industrial production, which can meet the needs of industries with extremely high requirements for medium purity and control accuracy. Through reasonable hardware connection, software communication and control, as well as the optimization of response speed and control accuracy, the efficient operation of ultra high purity diaphragm valves on automated production lines can be realized. In the future development, with the continuous progress of automation technology and valve manufacturing technology, the integration of ultra high purity diaphragm valves with automated control systems will be closer and more intelligent, providing stronger support for the high-quality development of industrial production.
For more about Integration and performance optimization of ultra high purity diaphragm valves in automated control systems, you can pay a visit to Jewellok at https://www.jewellok.com/ for more info.
Recent Posts
Tags
Recommended Products
-
7102L Stainless Steel 316L SS Union Cross Ultra High Purity Long Arm Union Elbow Tee Cross Butt Weld Fittings
-
Stainless Steel Ultra High Purity (UHP) High Pressure Manual Diaphragm Valve
-
JF Series In-Line Gas Filters | High Purity High Precision High Flow Semiconductor Gas Filter Gas Filtration & Purification
-
High Purity Configurable Systems VMB Valve Manifold Box JW-200-VMB-C & JW-100-VMB-C
-
High Purity High Pressure Gas Cylinder Pressure Regulators Pressure Reducing Valve JSR-1E Series
-
Stainless Steel High-Purity High Temperature Metal Seated Ball Valves JBV3 Series
-
Pressure Control Panels For High Purity Gas Control System JSP-3AE Series From Pressure Control Panels Suppliers And Manufacturer
-
Flow Control Stainless Steel Low Pressure Manual Diaphragm Valve For High Purity And Ultra High Purity Gases