Blog
Jewellok is a professional pressure regulator and valve manufacturer and supplier.
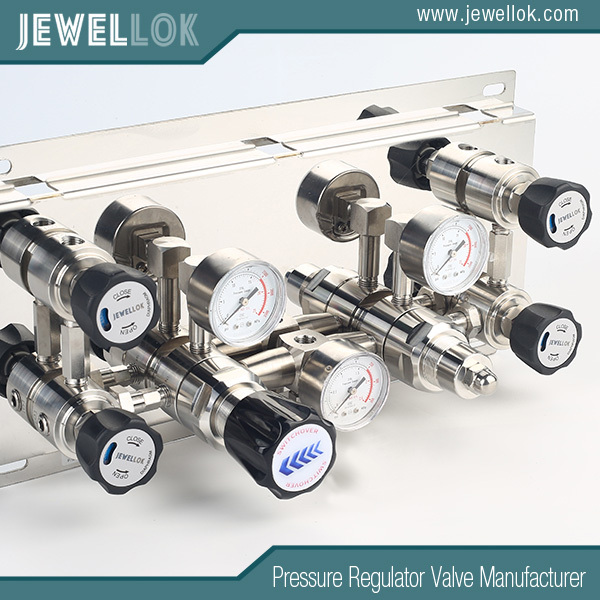
Flow Characteristics of Ultra High Purity Diaphragm Valves: The Key to Precisely Meeting Process Requirements
- Pressure Regulator Valve Manufacturer
- adjusting propane regulator, argon hose fitting, block & bleed valve, characteristics of pressure, chinese propane gas cylinder, double block and bleed valve, double block bleed valve, excess flow valve, fusible plug, gas filter, gas regulator, gas used in semiconductor manufacturing, how a solenoid valve works, hydraulic regulator, industrial grade purity, low pressure regulator, o ring face seal fittings, pressure gauge manufacturers, pressure relief valve vs safety relief valve, quick connect valve, relief vs safety valve, safety relief valve vs pressure relief valve, solenoid valve for ammonia gas 1 inch pipe, solenoid water valve, stainless pressure regulator, ultra high purity, Ultra High Purity Diaphragm Valves, ultra high purity diaphragm valves hotsale, ultra high purity diaphragm valves manufacturer, Ultra High Purity Diaphragm Valves OEM, ultra high purity diaphragm valves supplier, ultra high purity diaphragm valves wholesale
- No Comments
Flow Characteristics of Ultra High Purity Diaphragm Valves: The Key to Precisely Meeting Process Requirements
In modern industrial production, the precision of fluid control is of great significance for product quality, production efficiency, and cost control. Ultra high purity diaphragm valves, as a type of valve widely used in industries with extremely high purity requirements such as semiconductors, pharmaceuticals, and food, how their flow characteristics adapt to different process requirements, especially ensuring precise flow regulation in high-precision fluid control, has become the focus of industry attention.
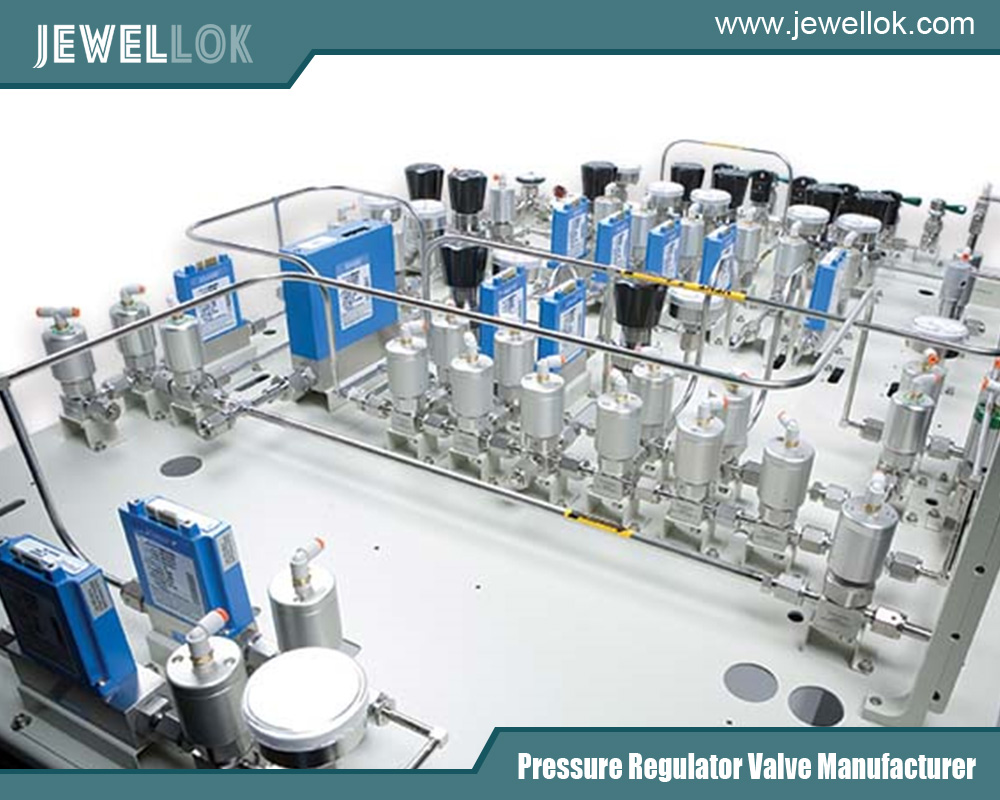
Basics of the Flow Characteristics of Ultra High Purity Diaphragm Valves
I. Flow Characteristic Curve
The flow characteristic of a valve refers to the relationship curve between the relative flow rate of the valve (the ratio of the actual flow rate to the rated flow rate) and the relative opening degree of the valve (the ratio of the actual opening degree to the rated opening degree). Common flow characteristics include linear, equal percentage, quick opening, and parabolic types. For ultra high purity diaphragm valves, their flow characteristics are usually close to the quick opening characteristic, but are approximately linear before 60% of the stroke, and the flow rate changes little after 60%. This unique flow characteristic is closely related to the structure and working principle of the diaphragm valve. The diaphragm valve controls the on-off and flow rate of the fluid through the up and down movement of the diaphragm. During the opening process of the diaphragm, the change in the flow passage area makes the flow rate show the above characteristics.
II. Flow Coefficient (Cv value)
The flow coefficient Cv is an important indicator for measuring the flow capacity of a valve, indicating the flow rate (in US gallons per hour) that can pass through the valve when it is fully open under specific conditions (normal temperature water, 1psi pressure difference). For ultra high purity diaphragm valves, different models and specifications have different Cv values. For example, the ALD3 and ALD6 series diaphragm valves of Swagelok have a maximum flow coefficient of up to 0.62. The larger the flow coefficient, the greater the flow rate that the valve can pass through under the same conditions, which has an advantage in meeting the process requirements of large flow rates. At the same time, in high-precision fluid control, accurately understanding the flow coefficient helps to accurately select the appropriate valve according to the process requirements.
Adjustment of Flow Characteristics to Adapt to Different Process Requirements
I. Diversity of Process Requirements
The requirements for fluid control vary greatly in different industries and different production processes. In the semiconductor manufacturing process, the atomic layer deposition (ALD) process requires precise control of the flow rate of precursor gases to ensure the accuracy and quality of chip manufacturing. A slight deviation in the flow rate may lead to a decline in chip performance. In the pharmaceutical industry, the control of the flow rate of various raw materials and solvents in the process of drug synthesis and production is also extremely strict, which is directly related to the safety and effectiveness of drugs. In the food industry, in processes such as beverage blending and dairy product processing, accurate control of fluid flow is also required to ensure the consistency of product taste and quality.
II. Selection of Flow Characteristics Based on the Process
- Application Scenarios of Linear Flow Characteristics: In some processes that require relatively uniform flow rate changes and a proportional relationship between the flow rate and the opening degree, ultra high purity diaphragm valves with linear flow characteristics are more suitable. For example, in some cleaning processes in semiconductor manufacturing, it is necessary to stably and uniformly supply the cleaning solution. The diaphragm valve with linear flow characteristics can more accurately control the flow rate of the cleaning solution by adjusting the opening degree, meeting the requirements of the cleaning process for flow rate accuracy and stability. In the pharmaceutical industry, in some simple mixing processes, when it is necessary to mix different liquid raw materials in a certain proportion, the diaphragm valve with linear flow characteristics can conveniently achieve the precise proportioning of the flow rate according to the opening degree.
- Advantages of Equal Percentage Flow Characteristics: For processes with a large flow rate change range and requiring fine adjustment at both small and large flow rates, ultra high purity diaphragm valves with equal percentage flow characteristics have obvious advantages. Taking the semiconductor ALD process as an example, at different stages of the deposition process, the flow rate requirements for precursor gases vary greatly. From the initial precise control of a small flow rate to the subsequent supply of a large flow rate according to the deposition rate requirements, the diaphragm valve with equal percentage flow characteristics has a slow flow rate change at a small opening degree, which can achieve fine adjustment of a small flow rate and avoid excessive adjustment; at a large opening degree, the flow rate changes more quickly, which can quickly meet the demand for a large flow rate and ensure the smooth progress of the deposition process. In the feeding process of a reaction kettle in the pharmaceutical industry, as the reaction proceeds, the flow rate requirements of the raw materials change continuously. The diaphragm valve with equal percentage flow characteristics can better adapt to this change and ensure the stability of the reaction and the consistency of product quality.
- Special Applications of Quick Opening Flow Characteristics: Although the overall flow characteristics of ultra high purity diaphragm valves are close to the quick opening characteristic but not exactly the same as the typical quick opening characteristic, and the flow rate change after 60% of the stroke is relatively small. However, in some special processes, such as emergency shutdown or rapid on-off fluid control scenarios, some characteristics of the quick opening characteristic still have application value. For example, in a high-purity gas transmission system, when an abnormal situation (such as leakage, abnormal pressure, etc.) is detected, it is necessary to quickly cut off the gas supply. The diaphragm valve can respond quickly and, by taking advantage of the characteristic that the flow rate changes greatly at a small opening degree, quickly cut off the fluid to ensure the safety of the system.
Precise Flow Regulation in High-Precision Fluid Control
I. Control Principles and Technologies
- Feedback Control Technology: In high-precision fluid control, feedback control technology is usually adopted to achieve precise flow regulation. The flow rate of the fluid is monitored in real-time by a flow sensor installed in the pipeline, and the flow rate signal is fed back to the controller. The controller compares the actual flow rate with the set flow rate, calculates the required valve opening degree adjustment according to the deviation value, and sends a control signal to the valve actuator, thus realizing the closed-loop control of the flow rate. For example, in semiconductor manufacturing equipment, the high-precision mass flow controller (MFC) is used in conjunction with the ultra high purity diaphragm valve. The MFC accurately measures the gas flow rate and feeds the signal back to the equipment control system. The control system adjusts the opening degree of the diaphragm valve according to the process requirements to ensure that the gas flow rate is always stable at the set value.
- Intelligent Control Algorithms: In order to further improve the accuracy and response speed of flow control, various intelligent control algorithms, such as the Proportional-Integral-Derivative (PID) control algorithm and the fuzzy control algorithm, have been introduced into modern control systems. The PID control algorithm adjusts the valve opening degree according to the proportional, integral, and derivative values of the flow rate deviation, which can effectively eliminate the steady-state error and improve the stability and response speed of the system. The fuzzy control algorithm is based on fuzzy logic, fuzzifies the information such as the flow rate deviation and the deviation change rate, and infers the control quantity through fuzzy rules. It can better adapt to complex nonlinear systems and uncertain factors, and achieve more precise flow control in situations where the flow rate changes frequently and the process requirements are complex.
II. Influence of Valve Structure and Materials on Flow Regulation Precision
- Diaphragm Material and Structure: The diaphragm is a key component of the ultra high purity diaphragm valve, and its material and structure directly affect the flow regulation precision. High-quality diaphragm materials should have good flexibility, wear resistance, corrosion resistance, and low permeability to ensure accurate flow control during long-term use. For example, the diaphragm made of cobalt-based superalloy materials not only has high strength and corrosion resistance, but also can maintain stable performance under different pressure and temperature conditions, ensuring the sealing performance and flow regulation precision of the valve. At the same time, the structural design of the diaphragm is also crucial. A reasonable shape and thickness distribution can make the diaphragm move more smoothly during the opening and closing process, reducing flow rate fluctuations.
- Valve Body and Seat Design: The design of the valve body and seat also has an important impact on the flow regulation precision. The fully enclosed valve seat design can effectively prevent impurities from entering the valve interior, improve the valve’s anti-pollution ability, and ensure the stability of flow control. The optimized design of the valve body flow passage can reduce the resistance and turbulence of the fluid, making the fluid flow more smoothly through the valve, reducing the flow rate loss, and improving the accuracy of flow regulation. In addition, using high-precision processing technology to manufacture the valve body and seat to ensure the matching precision between them can further improve the valve’s sealing performance and flow control precision.
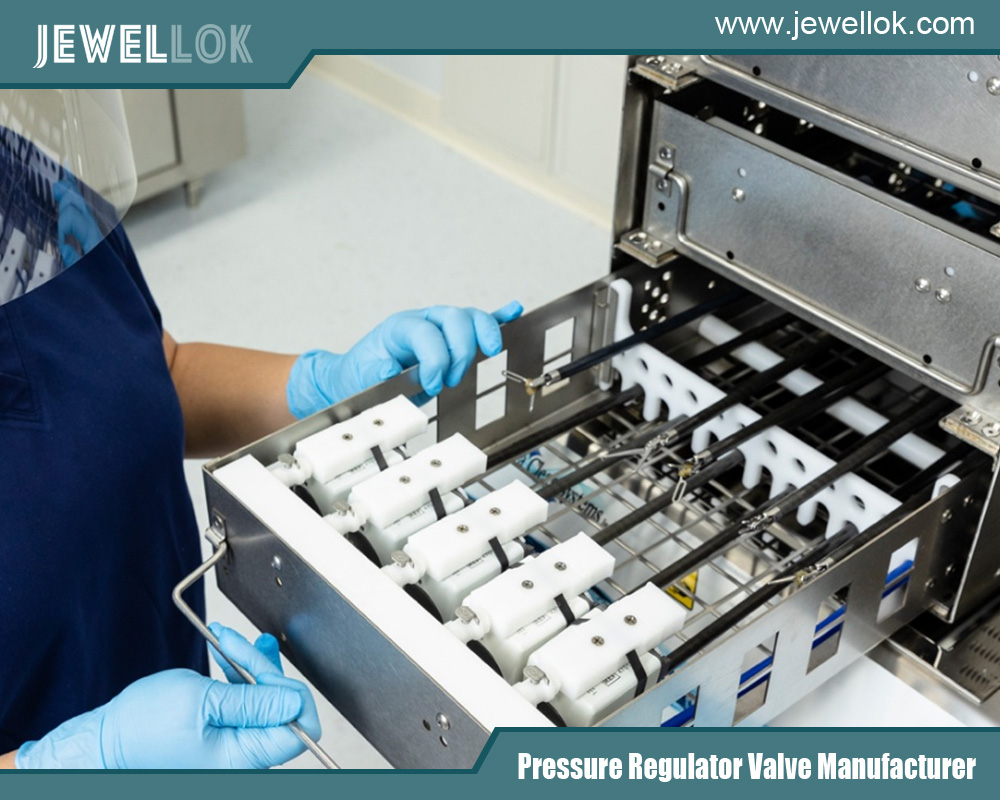
Challenges and Prospects
I. Current Challenges
With the continuous development of industrial technology, the requirements for the flow characteristics and flow control precision of ultra high purity diaphragm valves are getting higher and higher. On the one hand, in some emerging high-end manufacturing fields, such as quantum chip manufacturing and gene therapy in biopharmaceuticals, unprecedented challenges have been put forward for the precision and stability of fluid control, and the existing diaphragm valve technology is difficult to meet these extremely demanding process requirements in some cases. On the other hand, with the increasing awareness of environmental protection and sustainable development, higher requirements have also been put forward for the energy efficiency and resource utilization rate during the fluid control process. How to reduce the energy consumption of the valve and minimize fluid waste while ensuring the flow control precision is a problem that needs to be solved.
II. Future Development Trends
In the future, ultra high purity diaphragm valves are expected to achieve new breakthroughs in optimizing flow characteristics and improving flow control precision. In terms of materials science, new high-performance diaphragm materials and valve body materials will be developed to further improve the corrosion resistance, wear resistance, and high-temperature resistance of the valves, while reducing the cost of materials and the impact on the environment. In terms of manufacturing processes, advanced processing technologies such as additive manufacturing (3D printing) and nanomanufacturing will be adopted to realize the refined design and manufacturing of the valve structure, improving the flow control performance and reliability of the valves. In terms of control technology, by combining emerging technologies such as artificial intelligence, big data, and the Internet of Things, more intelligent and adaptive flow control systems will be developed to achieve remote monitoring, predictive maintenance, and optimized control of the valve flow rate, meeting the continuously evolving industrial production needs.
The flow characteristics of ultra high purity diaphragm valves play a key role in adapting to different process requirements and achieving high-precision fluid control. By deeply understanding the basic principles of flow characteristics, selecting appropriate flow characteristics according to different processes, and using advanced control technologies and optimized valve structures, precise regulation of the fluid flow rate can be achieved to meet the strict requirements of various industries for high-purity fluid control. With the continuous progress of technology, ultra high purity diaphragm valves will play a more important role in industrial production, providing strong support for promoting the high-quality development of various industries.
For more about flow characteristics of ultra high purity diaphragm valves: the key to precisely meeting process requirements, you can pay a visit to Jewellok at https://www.jewellok.com/ for more info.
Recent Posts
Tags
Recommended Products
-
Flow Control Stainless Steel Low Pressure Manual Diaphragm Valve For High Purity And Ultra High Purity Gases
-
VMB Valve Manifold Panels And Boxes High Purity Configurable Systems JW-200-VMB & JW-100-VMB
-
764LR Stainless Steel 316 Reducing Tee UHP Fitting Automatic Buttweld Reducing Tee
-
High Purity High Pressure Gas Cylinder Pressure Regulators Pressure Reducing Valve JSR-1E Series
-
768LN Stainless Steel Male Pipe Tube Butt Weld Connector And Tube Fittings Supplier
-
Low Pressure High Flow Line Pressure Regulators And Control Valves JSR-4L Series For Laboratory Pressure Control
-
7121L Plug High Purity Plug Fitting And Blanking Plug
-
7108L Cylinder Cap Connectors For Ultra High Purity Gases