Blog
Jewellok is a professional pressure regulator and valve manufacturer and supplier.
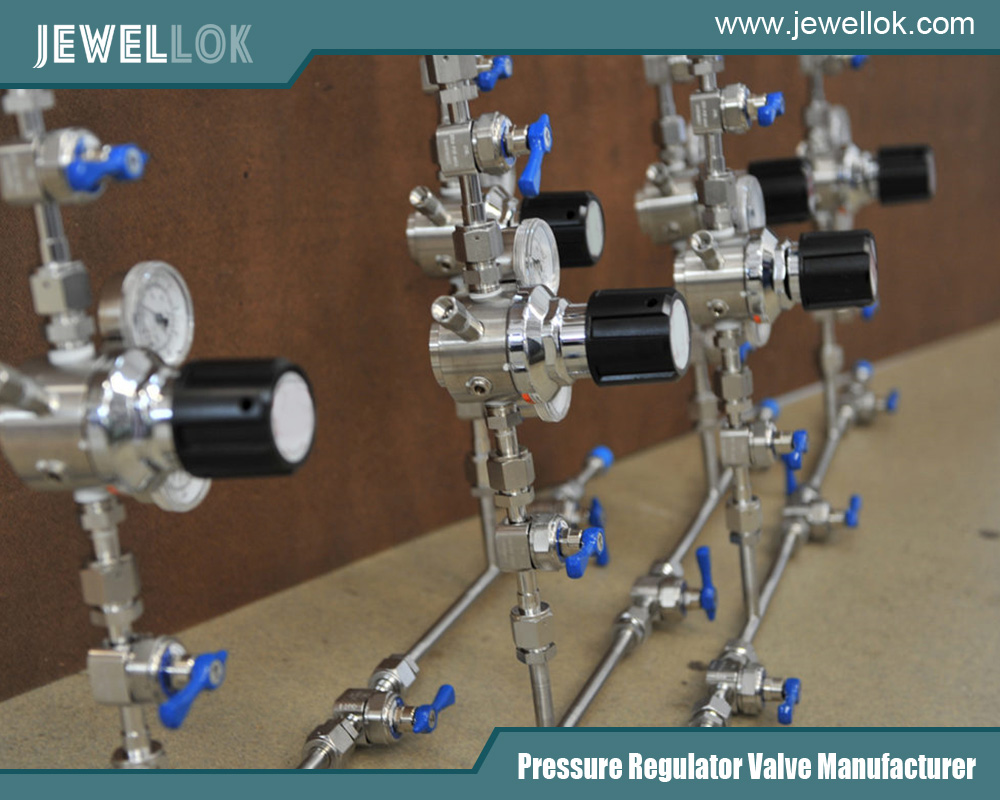
Design of CIP and SIP and Pollution Control Strategies for Ultra-High Purity Diaphragm Valves
- Pressure Regulator Valve Manufacturer
- 1/2 gas pressure regulator, 2 inch irrigation solenoid valve, 6mm compression union, 6mm equivalent, adjustable propane pressure regulator, adjustable propane regulator, argon gas pressure regulator, diaphragm suppliers, Diaphragm Valve Manufacturers, gas filter, gas manifold system, high purity regulator, how a solenoid works, how does pressure regulator work, how solenoid valves work, industrial regulators, low pressure regulator, oxygen regulator gauge, pressure gauge manufacturers, relief vs safety valve, safety valve and relief valve difference, safety valve vs relief valve, semiconductor gas, solenoid water valve, stainless pressure regulator, stainless steel 1/4 in, Ultra High Purity Diaphragm Valves, ultra high purity diaphragm valves manufacturer, ultra high purity diaphragm valves supplier, ultra-high purity diaphragm valves factory, what is a gas pressure regulator
- No Comments
Design of CIP and SIP and Pollution Control Strategies for Ultra-High Purity Diaphragm Valves
In modern industries, especially in fields with extremely high requirements for medium purity, such as semiconductors, pharmaceuticals, and food and beverage, ultra-high purity diaphragm valves play a crucial role. These industries have extremely strict requirements for pollution control during the production process. Even trace amounts of impurities, microorganisms, or particulate contamination can lead to a decline in product quality, production interruptions, or even safety accidents. Therefore, the cleaning of ultra-high purity diaphragm valves, especially the design of in-line cleaning (CIP) and in-place sterilization (SIP) functions, is of great importance. It is directly related to whether the production system can continuously and stably produce products that meet high-purity standards.
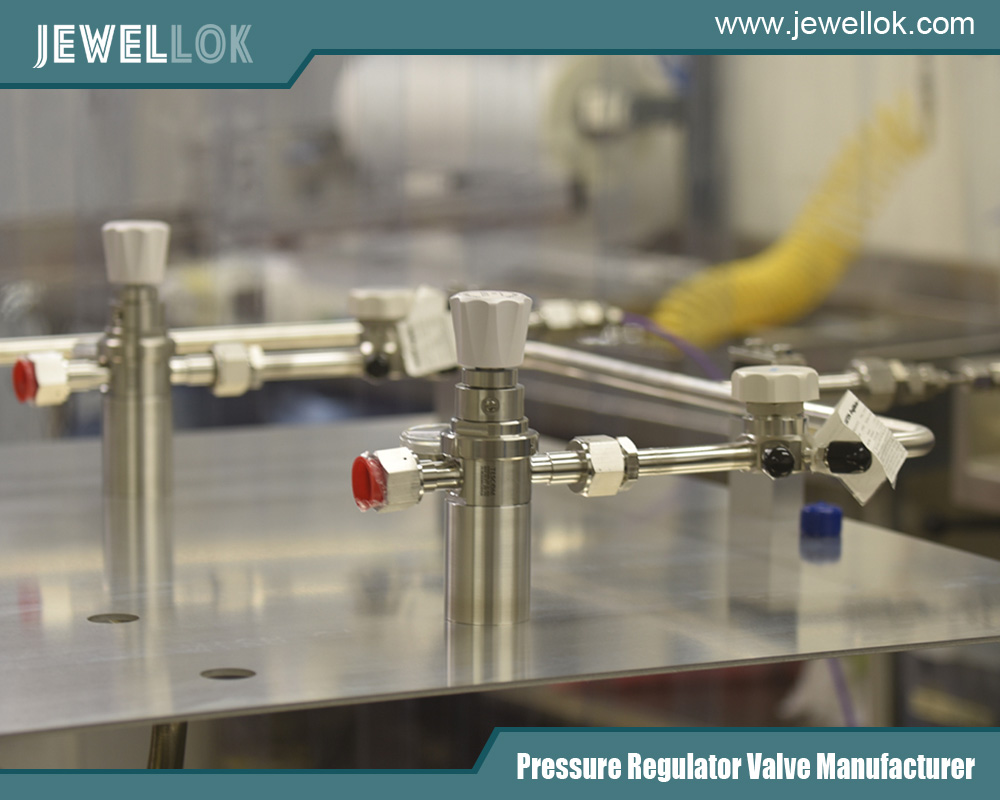
Structure and Characteristics of Ultra-High Purity Diaphragm Valves
The ultra-high purity diaphragm valve is a specially designed valve, and its core component is the diaphragm, which completely isolates the fluid passage of the valve from the driving components. The diaphragm is usually made of materials that are corrosion-resistant, chemically resistant, and meet food-grade or pharmaceutical-grade standards, such as polytetrafluoroethylene (PTFE), perfluoroalkoxy (PFA), etc. This structural feature enables the diaphragm valve to achieve zero leakage when closed, effectively preventing the medium from coming into contact with the external environment and avoiding contamination. At the same time, when the valve is open, the fluid can pass through smoothly, reducing flow resistance and pressure loss, and ensuring the stable transportation of high-purity media. The valve body is mostly made of 316L stainless steel, and through a special surface treatment process, such as electropolishing (EP), its surface roughness is extremely low, further reducing the possibility of impurities and microorganisms adhering.
Design Considerations for In-Line Cleaning (CIP)
I. Flow Path of Cleaning Solution
- Full Bore Design: To ensure that the cleaning solution can fully contact all surfaces inside the valve, ultra-high purity diaphragm valves usually adopt a full bore design. This design minimizes the flow resistance of the cleaning solution inside the valve, allowing it to flush key parts such as the valve inner wall, diaphragm, and valve seat at a relatively high flow rate. For example, in the gas transportation system of the semiconductor industry, the full bore design of the valve can ensure that the cleaning solution quickly reaches and cleans the corners where particulate deposition may occur, effectively removing impurities generated by gas adsorption or chemical reactions.
- Dead-Free Structure: The internal structure design of the valve avoids any dead corners where the cleaning solution or impurities may accumulate. The connection between the diaphragm, valve body, and valve seat is tight and has a smooth transition, without grooves, gaps, or protrusions. In the liquid transportation pipeline of the pharmaceutical industry, this dead-free design can prevent drug residues and ensure that the inside of the valve is completely clean after each cleaning, without causing cross-contamination to the production of subsequent batches of drugs.
II. Compatibility of Cleaning Solution
- Chemical Tolerance: The materials selected for ultra-high purity diaphragm valves must have good chemical tolerance to common cleaning solutions. For example, for alkaline cleaning solutions (such as sodium hydroxide solution) and acidic cleaning solutions (such as nitric acid solution), the diaphragm and valve body materials should be able to be in long-term contact with them within the specified concentration and temperature range without corrosion, swelling, or degradation. In the food and beverage industry, alkaline and acidic cleaning solutions are frequently used to clean and disinfect equipment, and the chemical tolerance of the valve materials ensures the performance stability of the valve during long-term use.
- Low Extractability: The materials themselves should have extremely low extractability during the cleaning process to avoid releasing any substances that may contaminate the medium into the cleaning solution. This is particularly important for high-purity applications, such as the production of electronic-grade chemicals. Even trace amounts of impurity extraction may affect the performance and quality of electronic products.
III. Automatic Control of Cleaning Program
- Integration with Control System: Ultra-high purity diaphragm valves can be seamlessly integrated with the automatic cleaning control system to achieve the automatic operation of the cleaning program. By presetting cleaning parameters, such as the flow rate, pressure, temperature, and cleaning time of the cleaning solution, the control system can precisely control the cleaning process. In large-scale pharmaceutical production, the automatic cleaning system can automatically select the appropriate cleaning program according to different production batches and process requirements, improving cleaning efficiency and consistency.
- Real-Time Monitoring and Feedback: The valve is equipped with sensors during the cleaning process to real-time monitor parameters such as the flow rate, pressure, and temperature of the cleaning solution, and feedback the data to the control system. Once an abnormal parameter is detected, such as insufficient flow rate or excessive pressure, the control system can immediately take corresponding measures, such as adjusting the operating parameters of the cleaning pump or issuing an alarm, to ensure the smooth progress of the cleaning process.
Design Key Points of In-Place Sterilization (SIP)
I. Applicability of Disinfection Medium
- Steam Compatibility: For ultra-high purity diaphragm valves sterilized by steam, the valve materials must be able to withstand the action of high-temperature steam. The diaphragm and seals are usually made of high-temperature-resistant rubber or plastic materials, such as silicone rubber, ethylene propylene diene monomer (EPDM), etc. These materials can still maintain good elasticity and sealing performance in a high-temperature steam environment. The valve body material needs to have good thermal stability, and 316L stainless steel can maintain its mechanical properties and corrosion resistance during the high-temperature steam sterilization process.
- Compatibility with Chemical Disinfectants: In addition to steam, some industries may use chemical disinfectants for sterilization, such as hydrogen peroxide, peracetic acid, etc. The valve materials also need to have good tolerance to these chemical disinfectants and will not undergo chemical reactions or performance degradation due to contact with the disinfectants. In the biopharmaceutical industry, when using chemical disinfectants to disinfect production equipment, the chemical compatibility of the valve materials ensures the effectiveness and safety of the disinfection process.
II. Pressure and Temperature Control During the Disinfection Process
- Pressure Resistance: During the SIP process, the valve needs to withstand a certain pressure, especially during steam sterilization, the pressure of the steam may be relatively high. The design of the ultra-high purity diaphragm valve should ensure that it can withstand the highest pressure during the disinfection process while ensuring the structural integrity and sealing performance of the valve. Through reasonable structural design and material selection, the valve can work normally in a high-pressure steam environment without deformation, leakage, or other problems.
- Temperature Uniformity: To ensure the consistency of the disinfection effect, the temperature inside the valve should be uniform during the disinfection process. This requires that the structural design of the valve can promote the uniform distribution of steam or chemical disinfectants inside the valve body to avoid situations where the local temperature is too low or too high. For example, a special steam introduction structure is adopted to enable the steam to quickly fill all corners inside the valve and ensure that the entire valve surface can reach the effective disinfection temperature.
III. Rapid Cooling and Drying After Disinfection
- Rapid Cooling Design: After the disinfection is completed, the valve needs to be quickly cooled to the operating temperature to reduce the impact of high temperature on the valve materials and the system. Some ultra-high purity diaphragm valves are designed with special cooling channels, and the cooling process of the valve is accelerated by circulating cooling media (such as water or air). In semiconductor manufacturing equipment, rapid cooling can shorten the equipment downtime and improve production efficiency.
- Drying Measures: Drying is an important link to prevent the growth of microorganisms. The valve should be able to dry quickly after disinfection to avoid residual water becoming a breeding ground for microorganisms. Methods such as hot air purging and vacuum drying can be used to dry the valve. In the food processing industry, the dried valve can effectively prevent the growth of bacteria and molds and ensure the hygiene and safety of food.
Measures to Avoid Residues and Secondary Contamination During the Cleaning Process
I. Selection and Control of Cleaning Solution
- Optimization of Cleaning Solution Formula: According to different application scenarios and types of pollutants, select appropriate cleaning solution formulas and strictly control parameters such as the concentration, pH value, and temperature of the cleaning solution. In the semiconductor industry, special cleaning solution formulas have been developed for different process pollutants, which can effectively remove pollutants and minimize the impact on the valve materials.
- Recovery and Treatment of Cleaning Solution: Recover and treat the cleaning solution to avoid direct discharge causing environmental pollution. At the same time, purify the recovered cleaning solution through methods such as filtration and ion exchange to make it reusable and reduce production costs. In large-scale production, the recovery and treatment of the cleaning solution are not only environmentally friendly but also have significant economic benefits.
II. Cleaning and Maintenance of Cleaning Equipment
- Regular Cleaning of Cleaning Equipment: The cleaning equipment itself also needs regular cleaning and maintenance to prevent the accumulation of dirt and microorganisms inside, which may cause secondary contamination to the valve. The pipelines, pumps, filters, and other components of the cleaning equipment should be regularly disassembled, cleaned, and disinfected to ensure that the cleaning equipment is always in a clean state.
- Monitoring of Cleaning Equipment Performance: Regularly monitor the performance parameters of the cleaning equipment, such as flow rate, pressure, temperature, etc., and promptly discover and solve equipment failures. When the performance of the cleaning equipment declines, such as insufficient flow rate or unstable pressure, it may lead to incomplete cleaning and increase the risk of residues and secondary contamination.
III. Flushing and Detection After Cleaning
- Thorough Flushing: After the cleaning is completed, use high-purity water or gas to thoroughly flush the valve to ensure that the cleaning solution is completely removed. The flushing process should last for a sufficient period of time, and the flow rate and pressure of the flushing medium should meet the requirements to ensure that there is no cleaning solution residue inside the valve.
- Detection Methods: Adopt advanced detection methods to detect the valve after cleaning, such as particle counting, microbial detection, chemical residue detection, etc., to ensure that the valve meets the specified cleanliness standards. In the pharmaceutical industry, the strict detection process is a key link to ensure the quality and safety of drugs, and only the valves that pass the detection can be put into use.
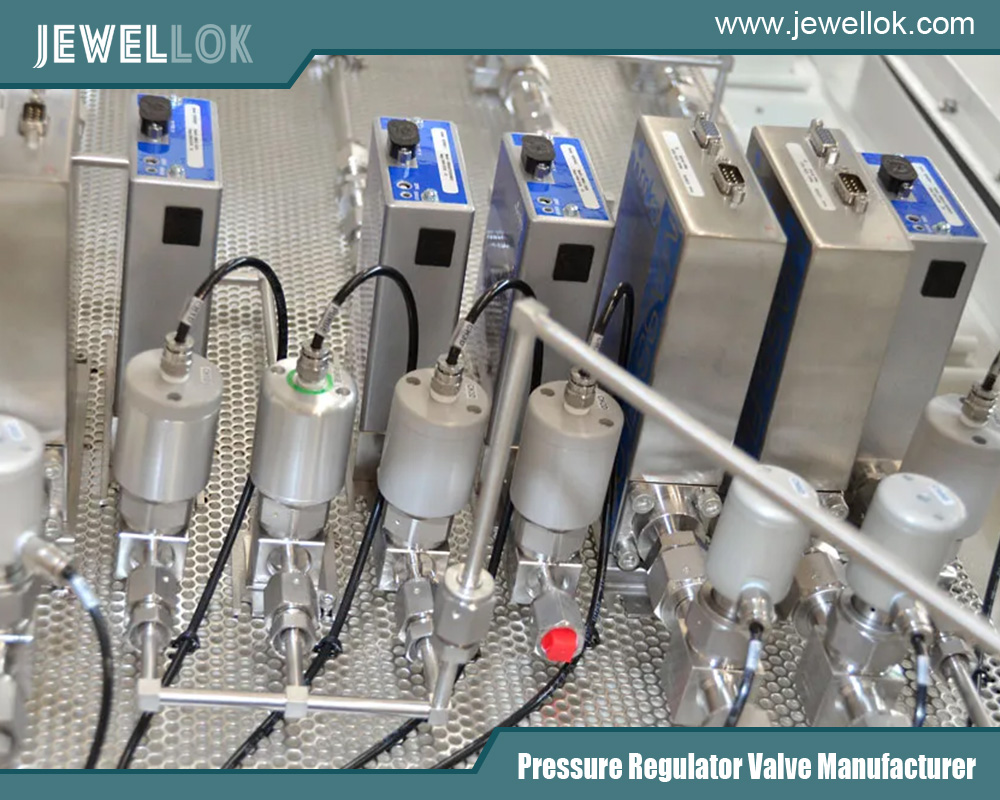
The design of CIP and SIP and the measures to avoid residues and secondary contamination for ultra-high purity diaphragm valves in high-purity industrial applications are a systematic and complex project. From the structural design and material selection of the valve to the control and detection of the cleaning and disinfection process, every link is closely connected and indispensable. With the continuous improvement of the requirements for product purity in various industries, the design and manufacturing technology of ultra-high purity diaphragm valves will also continue to develop and innovate to meet the increasingly strict production requirements and provide a reliable guarantee for the production of high-purity products. By continuously optimizing the cleaning and washing performance of the valve, the production cost can be effectively reduced, the production efficiency can be improved, and at the same time, the stability and safety of product quality can be ensured, promoting the high-quality development of related industries.
For more about design of CIP and SIP and pollution control strategies for ultra-high purity diaphragm valves, you can pay a visit to Jewellok at https://www.jewellok.com/ for more info.
Recent Posts
Tags
Recommended Products
-
772L Male Branch Tee | Stainless Steel High-Purity Tube Fitting Male Branch Tee
-
High Purity High Pressure Stainless Steel Needle Valve Natural Gas Flow Control Valve JNV Series
-
762L Stainless Steel High Purity Union High-Purity Gas System Fittings
-
Stainless Steel Single Stage Semiconductor Grade Pressure Control Module Pressure Control Panels JSP-6A Series
-
JR1000 Series UHP Ultra High Purity Single Stage Pressure Reducing Regulator And Low To Intermediate Flow
-
766L High Purity Female Connector UHP Fitting Female Connector
-
High Purity Configurable Systems VMB Valve Manifold Box JW-200-VMB-C & JW-100-VMB-C
-
767LP Port Connector Ultra High Purity VCR Metal Gasket Face Seal Tube Fittings