Blog
Jewellok is a professional pressure regulator and valve manufacturer and supplier.
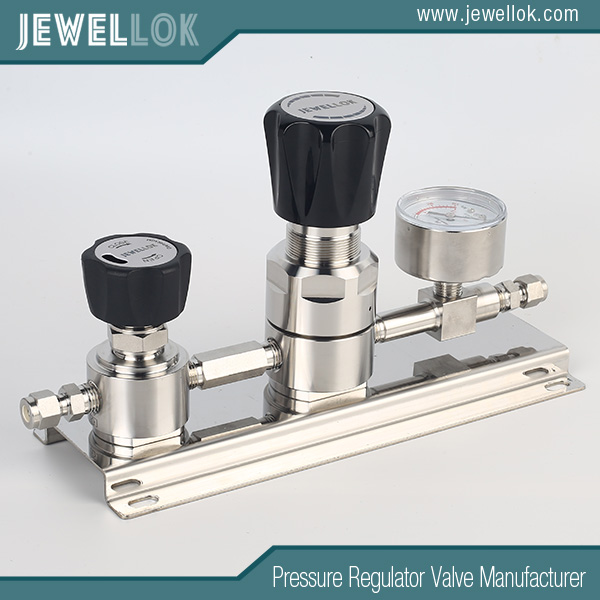
Why Ultra High Purity Gas Delivery Systems Are Important In The Semiconductor Industry
- Pressure Regulator Valve Manufacturer
- China High Purity Gas System Manufacturer, Custom Ultra High Purity Gas Delivery Solution, High Purity Gas Delivery Equipment, High Purity Gas Pipeline Manufacturer, High purity specialty gas supply equipment, Malaysia Ultra High Purity Gas Delivery Systems, OEM Ultra High Purity Gas Manufacturer, UHP Gas Distribution Panel, UHP Gas Purity Monitoring, ultra high purity gas delivery system in china, Ultra High Purity Gas Delivery System Manufacturer, Ultra High Purity Gas Distribution Systems, Ultra High Purity Gas Taps, Ultra High Purity Liquid Delivery Systems, Ultra High Purity Regulator 3500psi, Ultra-High-Purity Gas Delivery Systems
- No Comments
Why Ultra High Purity Gas Delivery Systems Are Important In The Semiconductor Industry
Introduction
In the intricate world of semiconductor manufacturing, precision at the atomic level is not just a goal—it’s a necessity. Semiconductors, the tiny chips that power everything from smartphones to supercomputers, are produced through a series of highly controlled processes where even the slightest deviation can lead to failure. Among the critical materials used in these processes are gases, which play essential roles in deposition, etching, and doping. However, not just any gas will do; the semiconductor industry demands ultra high purity (UHP) gases—gases purified to levels where impurities are measured in parts per billion (ppb) or even parts per trillion (ppt). Delivering these gases from their source to the point of use without contamination requires sophisticated ultra high purity gas delivery systems.
These systems are the unsung heroes of semiconductor fabrication plants, or “fabs,” ensuring that gases remain uncontaminated throughout their journey. In an industry where a single particle or trace impurity can ruin an entire batch of chips, the importance of UHP gas delivery systems cannot be overstated. This article explores why these systems are vital to the semiconductor industry, delving into the stringent purity requirements of manufacturing processes, the components that make up these systems, the challenges in their design and operation, real-world examples of their impact, and future trends that will shape their evolution.
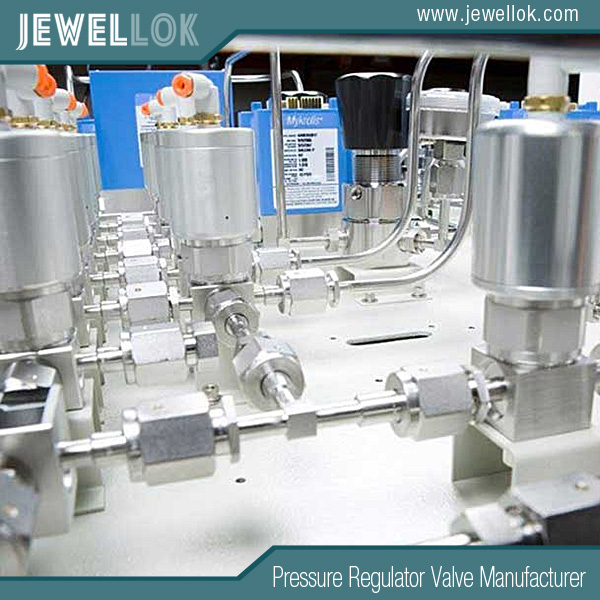
Section 1: Gas Purity Requirements in Semiconductor Manufacturing
Semiconductor manufacturing is a complex dance of physics and chemistry, involving processes that build and shape the microscopic structures of chips. Gases are indispensable in several key steps:
Chemical Vapor Deposition (CVD): This process deposits thin films onto wafers using gases like silane (SiH₄), ammonia (NH₃), and tungsten hexafluoride (WF₆). The purity of these gases determines the quality of the film.
Etching: Gases such as chlorine (Cl₂), sulfur hexafluoride (SF₆), and carbon tetrafluoride (CF₄) selectively remove material to create patterns. Impurities can alter etch rates or introduce unwanted residues.
Ion Implantation: Dopants like boron trifluoride (BF₃) and arsine (AsH₃) are ionized and implanted into the wafer to modify its electrical properties. Contaminants can disrupt this precision.
The stakes are high because impurities in these gases can wreak havoc:
Crystal Defects: A trace of oxygen or moisture can disrupt the semiconductor’s lattice structure, degrading its performance.
Unintended Reactions: Contaminants might react with the wafer or process chemicals, leading to defective layers or patterns.
Yield Loss: Even a small percentage of defective chips can translate to millions of dollars in losses in high-volume production.
To prevent such outcomes, the industry imposes rigorous purity standards. For example, nitrogen, widely used for purging and inerting, might require a purity of 99.9999% (six nines), limiting impurities to ppb levels. Specialty gases like silane have even stricter specifications, targeting specific contaminants like moisture or hydrocarbons known to affect chip quality. As semiconductor devices shrink to nanometer scales—think 3nm or 2nm nodes—the tolerance for impurities diminishes further, making UHP gases and their delivery systems ever more critical.
Section 2: Components of Ultra High Purity Gas Delivery Systems
An ultra high purity gas delivery system is a meticulously engineered network designed to transport gases without compromising their purity. Its key components include:
Gas Sources
Gases originate from high-pressure cylinders, bulk storage tanks, or on-site generators. The choice depends on usage rates and gas type—nitrogen might come from a bulk tank, while rare gases like xenon might be cylinder-based.
Piping and Tubing
The conduits for gas must be inert and ultra-smooth to prevent contamination. Electropolished stainless steel is a gold standard, with surface roughness below 10 microinches Ra, minimizing particle trapping. Piping layouts avoid dead spaces where gases could stagnate and accumulate impurities.
Valves, Regulators, and Fittings
These components control gas flow and pressure. Made from high-grade stainless steel, they feature designs like diaphragm valves that reduce particle shedding and outgassing compared to alternatives like ball valves. Metal-to-metal seals ensure leak-tight connections.
Filtration and Purification
To maintain purity, systems employ:
Particle Filters: Rated down to 0.003 microns, these remove dust or debris.
Chemical Purifiers: Technologies like heated getters (reactive metals that bind oxygen and moisture), molecular sieves (adsorbents), and catalytic purifiers (converting impurities into harmless compounds) tackle gaseous contaminants.
Point-of-Use Purification: Additional purifiers near process tools provide a final purity check.
Control Systems
Precision is key. Pressure regulators maintain consistent delivery, while mass flow controllers ensure accurate gas volumes. Sensors monitor for deviations, alerting operators to potential purity issues.
Gas Cabinets and Valve Manifold Boxes (VMBs)
These enclosures house cylinders and distribute gases to multiple tools. They isolate the gas from the environment, enhancing purity and safety. Automatic switchover systems within cabinets transition between cylinders seamlessly, avoiding supply interruptions or contamination.
Every component is assembled in cleanroom conditions, ensuring no impurities are introduced during setup. The result is a closed, pristine pathway that safeguards gas purity from source to application.
Section 3: Design and Operational Challenges
Building and running UHP gas delivery systems is no small feat. Several challenges must be addressed:
Cleanliness During Installation and Maintenance
Installation occurs in cleanrooms to avoid contamination. Tools and techniques minimize particle generation, and post-installation, systems are purged with inert gases or baked out to remove residuals. Maintenance follows similar protocols, with careful cleaning before recommissioning.
Leak Detection and Prevention
A leak as small as 10⁻⁹ std cc/sec can introduce ambient air, ruining purity. Helium leak testing verifies integrity, while high-quality seals and precise fittings prevent breaches. Regular inspections ensure long-term reliability.
System Reliability and Downtime Minimization
Semiconductor fabs run continuously, and downtime costs millions. UHP systems incorporate redundancy—dual supply lines or backup cylinders—and automatic switchovers to maintain operation. Preventive maintenance schedules preempt failures.
Monitoring and Verification
In-line analyzers track moisture, oxygen, and particles, while periodic sampling confirms compliance with specs. This vigilance ensures purity isn’t just achieved but sustained.
Safety Considerations
Many gases—silane (flammable), arsine (toxic)—are hazardous. Systems include:
Gas Detectors: Trigger alarms or shutoffs.
Emergency Valves: Isolate leaks.
Ventilation: Removes escaped gases.
Pressure Relief: Prevents over-pressurization.
Operators receive extensive training to handle these risks. Safety and purity go hand in hand, protecting both the process and personnel.
These challenges demand advanced engineering and strict controls, reflecting the high stakes of semiconductor production.
Section 4: Case Studies and Examples
Real-world incidents highlight the consequences of purity lapses:
Case Study 1: Moisture in Nitrogen
A fab discovered a valve leak in its nitrogen delivery system, allowing air ingress. The resulting moisture oxidized wafer surfaces during processing, cutting yield by 5%. The financial hit reached millions, underscoring the need for leak-tight systems.
Case Study 2: Particle Shedding
After upgrading its gas lines, a facility used inadequately polished piping. Particles shed into the gas stream contaminated wafers during CVD, causing defects and a costly production halt for system replacement.
These examples, while illustrative, mirror industry experiences where purity failures led to significant operational and financial impacts. They reinforce why UHP gas delivery systems are non-negotiable.
Section 5: Future Trends and Developments
As chips evolve, so must gas delivery systems. Emerging trends include:
Stricter Purity Requirements
Smaller nodes (e.g., 2nm) demand purity beyond current limits. New purification methods and materials will be essential.
Advanced Technologies
Research explores nanotechnology filters and novel alloys with lower outgassing. Point-of-use innovations may further enhance purity.
Smart Manufacturing
Industry 4.0 integrates sensors and analytics for real-time monitoring and predictive maintenance, catching issues before they affect purity.
Sustainability
Efficient gas use and closed-loop systems could reduce waste, aligning with environmental goals.
These advancements will keep UHP gas delivery systems at the forefront of semiconductor progress.
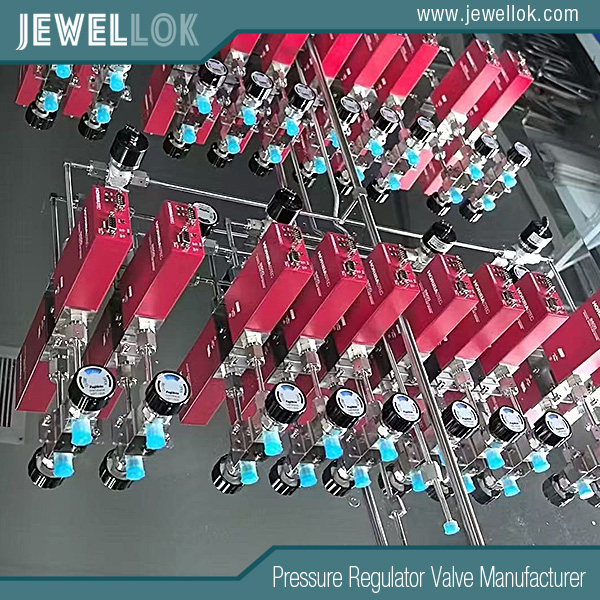
Conclusion
Ultra high purity gas delivery systems are the backbone of semiconductor manufacturing, ensuring that process gases meet exacting purity standards. From source to tool, their components and design overcome formidable challenges to deliver uncontaminated gases, safeguarding chip quality and yield. As technology advances, these systems will evolve, meeting tighter requirements and embracing smart, sustainable solutions. In an industry where precision defines success, UHP gas delivery systems are not just important—they are indispensable, enabling the innovations that drive our digital world.
For more about why ultra high purity gas delivery systems important in the semiconductor industry, you can pay a visit to Jewellok at https://www.jewellok.com/ for more info.
Recent Posts
Tags
Recommended Products
-
High Purity High Flow Pressure Control Regulators & Valves Gas Stick Assemblies JSR-2TG Series
-
High Purity Stainless Steel Mini Tube Butt Weld Fittings For Semiconductor
-
316L Stainless Steel Tube Butt Weld Reducing Fittings Union Reducer RW Series Ultrahigh Purity Process
-
Fully Automated Gas Cabinet For Precise UHP Gas Delivery And High Purity Gas Delivery Systems JW-300-GC
-
768L Stainless Steel Male Tube Butt Weld Connector | Clean Weld Fittings And Ultra-High Purity Fittings
-
Low Pressure High Flow Line Pressure Regulators And Control Valves JSR-4L Series For Laboratory Pressure Control
-
Stainless Steel 316L Single Stage Regulator Pressure Control Panels JSP-1E Series For Semiconductor Fluid Control
-
High Purity High Pressure 316 Stainless Steel Ball Valves JBV1 Series From High Pressure Ball Valve Manufacturer And Supplier In China