Blog
Jewellok is a professional pressure regulator and valve manufacturer and supplier.
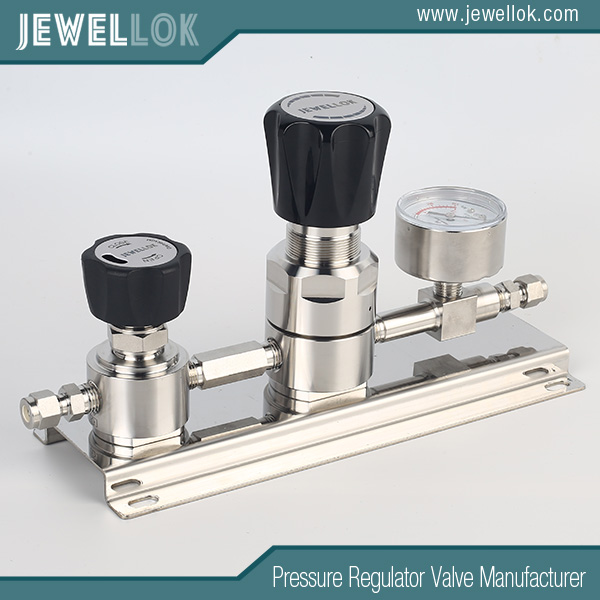
Types Of Ultra-High Purity Gases Used In The Semiconductor Industry
- Pressure Regulator Valve Manufacturer
- Gas pressure regulator for hydrogen, Helium Bottle and Cylinder Regulators, Helium Gas Regulator Manufacturer, Helium Gas Regulators, Helium High Pressure Regulator, Helium Single Stage High Pressure Gas Regulators, High Pressure 316l Helium Pressure Regulator, high pressure argon regulator, high pressure helium regulator, high pressure natural gas regulator, high pressure nitrogen regulator 2000 psi, High pressure Nitrogen regulator 4000 psi, high pressure nitrogen regulator 6000 psi, high purity argon regulator, high purity nitrogen regulator, nitrogen gas pressure regulator, single stage ultra high purity nitrogen regulator
- No Comments
Types Of Ultra-High Purity Gases Used In The Semiconductor Industry
Introduction
The semiconductor industry stands as the backbone of modern technology, powering everything from smartphones and computers to advanced medical devices and renewable energy systems. At the heart of this industry lies a complex manufacturing process that demands precision, cleanliness, and control at the atomic level. Ultra-high purity (UHP) gases play a critical role in this process, enabling the production of microchips and integrated circuits with unparalleled accuracy. These gases must meet stringent purity standards—often exceeding 99.9999% (6N)—to prevent contamination that could compromise the performance or yield of semiconductor devices. This article explores the key types of UHP gases used in the semiconductor industry, their specific applications, and their importance in ensuring the reliability of modern electronics.
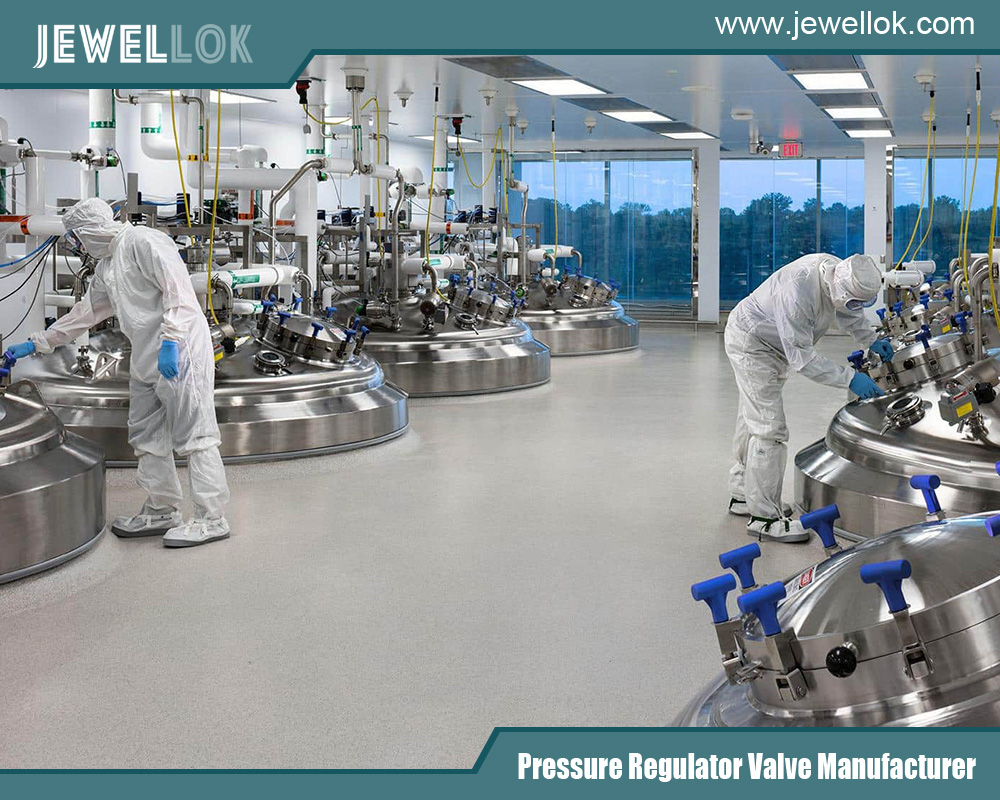
What Are Ultra-High Purity Gases?
Ultra-high purity gases are gases that have been refined to eliminate impurities such as moisture, particulates, hydrocarbons, and other trace contaminants. In the semiconductor industry, even minute levels of impurities (measured in parts per billion or trillion) can lead to defects in the microscopic structures of chips. UHP gases are typically delivered in specialized cylinders or through sophisticated gas distribution systems designed to maintain their purity from production to point of use. The most commonly used UHP gases include nitrogen, argon, helium, hydrogen, oxygen, and various specialty gases like silane and ammonia. Each serves a unique purpose in the fabrication process, from inert shielding to reactive chemical deposition.
1. Nitrogen (N₂)
Nitrogen is one of the most widely used UHP gases in the semiconductor industry due to its inert nature and abundance. With a purity level often exceeding 99.9999%, UHP nitrogen is employed as a purging gas to create a clean, oxygen-free environment inside processing chambers. This prevents unwanted oxidation of silicon wafers during high-temperature processes like annealing or diffusion. Nitrogen is also used as a carrier gas, transporting other reactive gases into the reaction chamber during chemical vapor deposition (CVD) or etching processes. Its versatility and non-reactive properties make it indispensable across multiple stages of semiconductor fabrication.
In addition to its role in maintaining a controlled atmosphere, nitrogen is critical in the production of nitride-based compounds, such as silicon nitride (Si₃N₄), which is used as an insulating layer or mask in chip manufacturing. The demand for UHP nitrogen continues to grow as semiconductor designs shrink to nanometer scales, requiring ever-stricter environmental controls.
2. Argon (Ar)
Argon, another inert noble gas, is prized for its stability and inability to react with other elements under normal conditions. In the semiconductor industry, UHP argon (purity ≥ 99.9999%) is primarily used in plasma-based processes, such as sputtering and plasma etching. During sputtering, argon ions are accelerated toward a target material (e.g., metal or silicon), dislodging atoms that then deposit onto the wafer to form thin films. These films are essential for creating conductive layers or barriers within the chip structure.
Argon’s high ionization potential and heavy atomic mass make it ideal for generating stable plasmas, ensuring uniform etching or deposition. It is also used as a diluent gas in combination with reactive gases to control reaction rates and improve process precision. As advanced nodes (e.g., 3nm and below) push the limits of material science, argon’s role in delivering consistent, contamination-free results remains vital.
3. Helium (He)
Helium is a lightweight, inert gas that plays a dual role in semiconductor manufacturing: as a process gas and a cooling agent. With a purity of 99.9999% or higher, UHP helium is used in leak detection systems to identify minute breaches in vacuum chambers, which are critical for maintaining the integrity of deposition and etching processes. Its small atomic size allows it to penetrate tiny leaks, making it an effective diagnostic tool.
Beyond leak detection, helium’s exceptional thermal conductivity makes it a preferred coolant in processes like rapid thermal processing (RTP) and ion implantation, where precise temperature control is necessary to avoid damaging delicate wafer structures. Although helium is less abundant and more expensive than nitrogen or argon, its unique properties ensure its continued use in high-precision applications.
4. Hydrogen (H₂)
Unlike the inert gases discussed so far, hydrogen is a reactive gas with a wide range of applications in semiconductor fabrication. UHP hydrogen (purity ≥ 99.9999%) is commonly used as a reducing agent to remove oxides from silicon surfaces, preparing them for subsequent processing steps. For example, in the production of epitaxial layers—thin, crystalline films grown on wafers—hydrogen helps maintain a clean substrate by reacting with surface contaminants.
Hydrogen is also a key component in annealing processes, where it facilitates the repair of crystal lattice damage caused by ion implantation. Additionally, it serves as a carrier gas for delivering hydride gases (e.g., silane) in CVD processes. However, hydrogen’s flammability requires strict safety protocols, including specialized delivery systems and monitoring equipment, to prevent accidents in the cleanroom environment.
5. Oxygen (O₂)
Oxygen, though reactive, is essential in controlled amounts during semiconductor manufacturing. UHP oxygen (purity ≥ 99.9999%) is used primarily in oxidation processes to grow silicon dioxide (SiO₂) layers on wafer surfaces. These layers serve as insulators or gate dielectrics in transistors, forming the foundation of chip functionality. The thickness and uniformity of SiO₂ layers are critical to device performance, and UHP oxygen ensures that no impurities interfere with this precision.
Oxygen is also used in plasma etching to remove organic residues or photoresist materials from wafers. Its reactivity must be carefully managed, as excessive oxygen can damage sensitive components. Advanced purification techniques, such as cryogenic distillation and molecular sieves, are employed to achieve the necessary purity levels for semiconductor-grade oxygen.
6. Specialty Gases (Silane, Ammonia, and More)
In addition to the core gases mentioned above, the semiconductor industry relies on a variety of specialty UHP gases tailored to specific processes. Silane (SiH₄), for instance, is a pyrophoric gas used in CVD to deposit silicon layers, including amorphous silicon and polysilicon, which are critical for solar cells and transistor gates. Its purity must exceed 99.9999% to prevent defects in the deposited films.
Ammonia (NH₃) is another specialty gas used to form silicon nitride layers via CVD or plasma-enhanced CVD (PECVD). These layers provide excellent insulation and passivation properties, protecting circuits from moisture and mechanical stress. Other specialty gases, such as phosphine (PH₃) and diborane (B₂H₆), are used as dopants in ion implantation to introduce precise amounts of phosphorus or boron into silicon, altering its electrical properties.
Fluorinated gases like tetrafluoromethane (CF₄) and sulfur hexafluoride (SF₆) are employed in plasma etching to remove material selectively, creating the intricate patterns that define modern chips. Each of these gases requires rigorous purification and handling to meet the industry’s exacting standards.
Importance of Purity in Semiconductor Manufacturing
The need for ultra-high purity gases stems from the semiconductor industry’s relentless pursuit of smaller, faster, and more efficient devices. As feature sizes shrink below 5 nanometers, even a single impurity atom can disrupt the functionality of a transistor or interconnect. Contaminants such as water vapor, carbon dioxide, or metal particles can lead to defects like short circuits, reduced yields, or complete device failure. UHP gases mitigate these risks by providing a pristine environment and enabling precise chemical reactions.
Achieving and maintaining this purity involves advanced production techniques, including multi-stage filtration, distillation, and real-time monitoring. Gas suppliers work closely with semiconductor manufacturers to certify purity levels and ensure compatibility with cleanroom standards, such as ISO Class 1, where particle counts are limited to fewer than 10 per cubic meter.
Challenges and Innovations in UHP Gas Supply
The growing demand for UHP gases has introduced several challenges, including supply chain constraints, environmental concerns, and cost pressures. Helium, for example, is a finite resource extracted from natural gas reserves, and its availability has fluctuated in recent years. Similarly, the production of fluorinated gases raises environmental issues due to their high global warming potential, prompting research into greener alternatives.
Innovations in gas purification and recycling are helping address these challenges. On-site gas generation systems, for instance, allow manufacturers to produce UHP nitrogen or hydrogen directly at the facility, reducing reliance on external suppliers. Advanced sensors and AI-driven analytics are also improving contamination detection, ensuring that gas quality remains consistent throughout the supply chain.
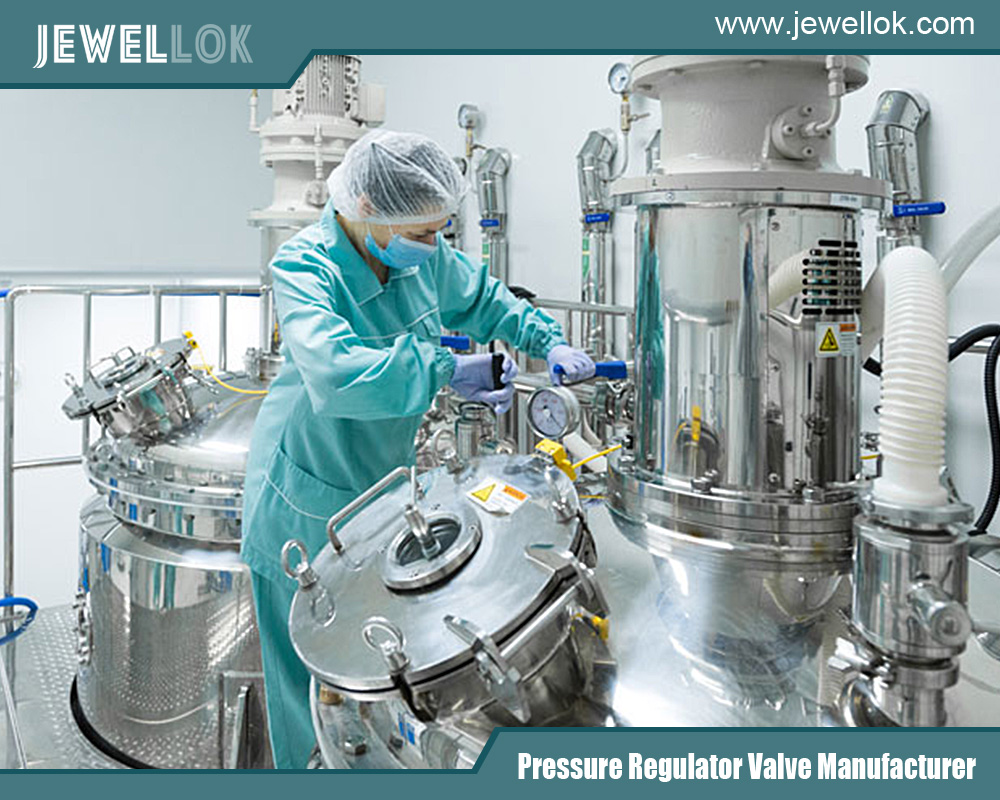
Conclusion
Ultra-high purity gases are the unsung heroes of the semiconductor industry, enabling the creation of the tiny, powerful chips that drive our digital world. From inert gases like nitrogen and argon to reactive species like hydrogen and silane, each type of UHP gas serves a specialized function in the intricate dance of wafer fabrication. As the industry pushes toward smaller nodes and greater complexity, the demand for these gases—and the technologies to deliver them—will only increase. By understanding the roles and requirements of UHP gases, we gain a deeper appreciation for the precision and innovation that define modern semiconductor manufacturing.
For more about the types of ultra high purity gases use in semiconductor industry, you can pay a visit to Jewellok at https://www.jewellok.com/types-of-high-purity-high-pressure-gas-from-specialty-gas-suppliers/ for more info.
Recent Posts
Tags
1 1 2 gas pressure regulator
1 2 gas regulator
1/2 gas pressure regulator
2 inch irrigation solenoid valve
2 inch irrigation valve
6mm compression fitting
6mm equivalent
8mm compression fitting
adjustable low pressure propane regulator
adjustable propane pressure regulator
adjustable propane regulator
adjusting propane regulator
air compressor non return valve
argon hose fitting
diaphragm suppliers
fluid systems components
gases used in semiconductor manufacturing
gas pipeline valve
gas pipeline valves
gas regulator
high purity valves
how a pressure regulator works
how does a needle valve work
how does pressure regulator work
how often should pressure relief valves be replaced
how solenoid valves work
humming propane regulator
irrigation timer valve
low pressure regulator
pressure gauge manufacturers
pressure regulator
pressure regulator valve leaking
regulator valve alibaba international market
relief vs safety valve
safety relief valve vs pressure relief valve
safety relief valve vs safety valve
safety valve and relief valve
safety valve and relief valve difference
safety valve vs pressure relief valve
single stage pressure regulator
stainless pressure regulator
stainless steel 1/4 in. pressure gauge fitting - 3/8 qc
two stage pressure regulator
valve timer water
what is a gas pressure regulator
Recommended Products
-
762L Stainless Steel High Purity Union High-Purity Gas System Fittings
-
772L Male Branch Tee | Stainless Steel High-Purity Tube Fitting Male Branch Tee
-
772 LF Female Branch Tee | Stainless Steel Tube Fitting Female Branch Tee 1/2 in. Tube OD x 1/2 in. Tube OD x 3/8 in. Female NPT
-
High Purity Chemical Dispense System & Packing System For Semiconductors JW-200L-CDM & JW-1000L-CDM
-
Line And Panel Mounting Adjustable Low Pressure Propane And Nitrogen Pressure Regulator JSR-3L & JSR-3LP Series
-
JR1000 Series UHP Ultra High Purity Single Stage Pressure Reducing Regulator And Low To Intermediate Flow
-
Stainless Steel Single Stage Semiconductor Grade Pressure Control Module Pressure Control Panels JSP-6A Series
-
High Purity High Pressure Gas Cylinder Pressure Regulators Pressure Reducing Valve JSR-1E Series