Blog
Jewellok is a professional pressure regulator and valve manufacturer and supplier.
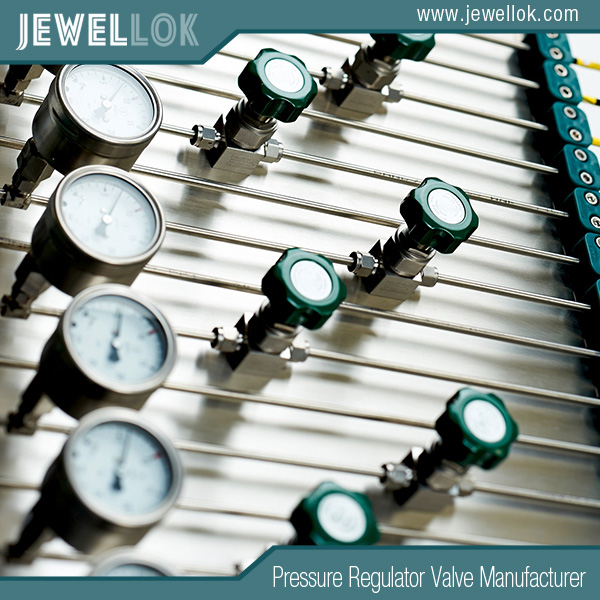
What You Need to Know About Ultra High Purity Gas Regulators
- Pressure Regulator Valve Manufacturer
- 1/4 VCR Stainless Steel Ultra High Purity Gas Regulator, China Customized Gas Regulator Manufacturers, China Gas Regulator Factory, China High Pressure Gas Regulator Manufacturers, China High Pressure Regulator Factory, china ultra high purity gas regulator manufacturer, China Wholesale Nitrogen Gas Pressure Regulator, High pressure gas cylinder regulator, High Purity Gas High Performance High Pressure Single Stage Regulator, High purity gas regulator Manufacturer china, OEM Gas Pressure Closing Regulator, Top 10 Gas Regulator Manufacturers in China, UHP Ultra High Purity Gas Regulator Panels Manifolds, ultra high purity gas regulator china, Ultra High Purity Regulators, Ultra High Purity Single Stage High Flow Regulator
- No Comments
What You Need to Know About Ultra High Purity Gas Regulators
Ultra high purity (UHP) gas regulators are critical devices designed to control the pressure and flow of gases while maintaining their purity at the highest levels. Unlike standard regulators, UHP versions are engineered to prevent contamination, making them indispensable in industries where even microscopic impurities can ruin processes or products. From semiconductor manufacturing to pharmaceutical production, these regulators ensure gases like nitrogen, argon, or hydrogen remain free of particles, moisture, or hydrocarbons. This article explores what UHP gas regulators are, how they work, their applications, and what to consider when choosing one.
At their core, UHP gas regulators reduce high-pressure gas from a cylinder or system to a usable level while preserving its integrity. They’re typically made from materials like 316L stainless steel or exotic alloys like Hastelloy to resist corrosion and outgassing—where trapped gases release contaminants. A diaphragm or piston mechanism adjusts pressure, and the design minimizes dead volume (unused space where impurities could accumulate). This precision is why UHP regulators are trusted in sensitive environments.
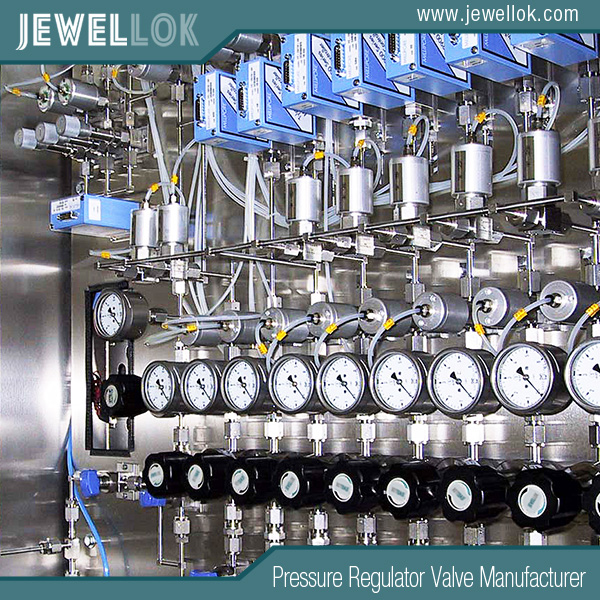
Take semiconductor manufacturing, for instance. Producing microchips requires delivering gases like silane or ammonia to deposition chambers without introducing moisture or dust, which could cause defects. Similarly, in pharmaceuticals, UHP regulators maintain sterile conditions for drug synthesis. Research labs also rely on them for gas chromatography, where purity directly affects accuracy. As industries like nanotechnology grow, demand for these devices continues to rise.
When selecting a UHP regulator, prioritize material compatibility with your gas—corrosive gases need special alloys. Look for leak-tight seals, often certified to standards like SEMI F1, and consider flow rates and pressure ranges suited to your system. Maintenance is another factor; electropolished surfaces reduce particle adhesion and simplify cleaning. However, challenges exist: high costs can deter smaller operations, and improper installation risks contamination. Top manufacturers like Swagelok and Tescom offer reliable options, with innovations like integrated sensors emerging to monitor performance in real time.
Material Properties of Ultra High Purity Gas Regulators
The performance of ultra high purity (UHP) gas regulators hinges on the properties of the materials used in their construction. These devices must deliver gases without introducing contaminants, withstand corrosive environments, and endure varying pressures and temperatures—all while maintaining structural integrity over time. The choice of materials directly impacts purity, durability, and safety, making their properties a cornerstone of UHP regulator design. Here’s a deep dive into the key materials and their characteristics.
1. 316L Stainless Steel
The most common material in UHP gas regulators is 316L stainless steel, prized for its corrosion resistance and low carbon content. The “L” denotes a carbon content below 0.03%, reducing the risk of carbide precipitation during welding, which could create microscopic corrosion sites. With 16-18% chromium, 10-14% nickel, and 2-3% molybdenum, 316L forms a passive oxide layer that resists rust and chemical attack from gases like oxygen or nitrogen. Its surface can be electropolished to a smoothness of 5-10 microinches (0.13-0.25 micrometers) Ra, minimizing particle adhesion and facilitating cleaning. This makes it ideal for inert gas applications in semiconductor and pharmaceutical industries.
-
Density: 8.0 g/cm³
-
Tensile Strength: ~515 MPa (74,700 psi)
-
Yield Strength: ~205 MPa (29,700 psi)
-
Thermal Conductivity: 16.3 W/m·K at 100°C
2. Hastelloy C-22
For corrosive or reactive gases like chlorine, hydrogen chloride, or silane, Hastelloy C-22 is a go-to material. This nickel-chromium-molybdenum alloy (22% Cr, 13% Mo, 56% Ni) excels in resisting pitting, crevice corrosion, and stress corrosion cracking. Its high molybdenum content enhances performance in reducing environments, while tungsten (3%) bolsters resistance to localized attack. Hastelloy’s robustness comes at a higher cost, but its ability to maintain purity with aggressive gases justifies its use in semiconductor etching or chemical synthesis.
-
Density: 8.69 g/cm³
-
Tensile Strength: ~690 MPa (100,000 psi)
-
Yield Strength: ~310 MPa (45,000 psi)
-
Corrosion Resistance: Superior in acidic and halogen-rich conditions
3. Monel 400
Monel 400, a nickel-copper alloy (67% Ni, 23% Cu), is another option for corrosive gases, particularly those with high sulfur or seawater exposure. It resists hydrofluoric acid and alkaline conditions, making it suitable for specialty chemical processes. While less common than 316L or Hastelloy, its ductility and toughness (even at cryogenic temperatures) make it valuable for regulators handling gases like fluorine.
-
Density: 8.8 g/cm³
-
Tensile Strength: ~550 MPa (80,000 psi)
-
Yield Strength: ~240 MPa (35,000 psi)
-
Thermal Expansion: 13.9 µm/m·K
4. Elastomers (Seals and Diaphragms)
Seals and diaphragms in UHP regulators require elastomers with minimal outgassing and chemical inertness. Polytetrafluoroethylene (PTFE) is widely used for its near-zero reactivity and low friction (coefficient ~0.05-0.10), though it’s rigid and less elastic. For flexibility, perfluoroelastomers like Kalrez or Chemraz offer high purity (outgassing <1 ppb) and withstand temperatures from -20°C to 260°C (-4°F to 500°F). Viton, a fluoropolymer, is a cost-effective alternative for less stringent purity needs, though it’s prone to swelling with hydrocarbons.
-
PTFE Hardness: Shore D 50-65
-
Kalrez Tensile Strength: ~15-20 MPa
-
Thermal Stability: PTFE up to 260°C, Kalrez up to 327°C
5. Surface Finish and Treatment
Beyond base materials, surface properties are critical. Electropolishing removes microscopic burrs and impurities, achieving a mirror-like finish that reduces surface area for particle entrapment. Passivation, often with nitric or citric acid, enhances the oxide layer on stainless steel, boosting corrosion resistance. Some regulators feature orbital welding, which ensures smooth, crevice-free joints with minimal heat-affected zones, preserving material integrity.
6. Thermal and Mechanical Considerations
Materials must tolerate operational extremes. Stainless steel retains strength across -40°C to 60°C (-40°F to 140°F), while Hastelloy and Monel handle cryogenic or high-temperature gases (e.g., -196°C for liquid nitrogen or 200°C for sterilization processes). Young’s modulus (e.g., 193 GPa for 316L) ensures rigidity under pressure, while low thermal conductivity (e.g., 16.3 W/m·K for 316L) minimizes heat transfer that could destabilize gas flow.
Why Material Properties Matter
These properties aren’t just technical jargon—they dictate real-world performance. A 316L regulator might suffice for argon in a cleanroom, but swap to hydrogen sulfide, and Hastelloy’s superior corrosion resistance becomes essential. Elastomer degradation could introduce volatile organic compounds (VOCs), ruining a semiconductor wafer or lab analysis. Matching material properties to gas type, pressure, and environment ensures purity levels like 99.9999% (6N) and prevents costly failures.
Technical Specifications of Ultra High Purity Gas Regulators
Ultra high purity (UHP) gas regulators are precision-engineered devices, and their technical specifications determine their suitability for demanding applications. These specs dictate how well a regulator can maintain gas purity, control pressure, and integrate into a system. Below, we explore the critical parameters to understand when selecting or evaluating a UHP gas regulator.
1. Pressure Ratings
UHP gas regulators are designed to handle a wide range of inlet and outlet pressures. Inlet pressure ratings typically span from 100 psi (6.9 bar) to over 4000 psi (275 bar), depending on whether the gas source is a high-pressure cylinder or a bulk system. Outlet pressure, the controlled delivery pressure, often ranges from vacuum levels (e.g., -14.7 psi or -1 bar) up to 500 psi (34.5 bar), though precision models may offer finer increments (e.g., 0-25 psi or 0-1.7 bar). Dual-stage regulators, which use two pressure reduction steps, provide greater stability for low outlet pressures, minimizing fluctuations critical in processes like gas chromatography.
2. Flow Capacity (Cv Value)
The flow coefficient (Cv) measures a regulator’s ability to deliver gas volume. For UHP regulators, Cv values typically range from 0.02 to 0.5, reflecting their focus on precision rather than high throughput. A lower Cv (e.g., 0.06) suits applications requiring tight control, such as semiconductor doping, while a higher Cv (e.g., 0.2) supports processes like laser gas delivery. Flow capacity must align with system demands—undersizing leads to starvation, while oversizing risks pressure instability.
3. Material Construction
Material selection is paramount to prevent contamination. Most UHP regulators use 316L stainless steel due to its low carbon content and corrosion resistance, with a surface finish often electropolished to a roughness average (Ra) of 5-10 microinches (0.13-0.25 micrometers). For reactive or corrosive gases (e.g., chlorine, hydrogen sulfide), alloys like Hastelloy C-22 or Monel are specified, offering superior resistance to pitting and cracking. Elastomeric seals, if present, use high-purity materials like PTFE or Kalrez to avoid outgassing, where volatile compounds could escape and taint the gas stream.
4. Leak Integrity
Leak-tight performance is non-negotiable in UHP systems. Regulators are tested to helium leak rates as low as 1×10⁻⁹ standard cubic centimeters per second (sccs), ensuring no external contaminants infiltrate or internal gas escapes. This specification, often certified to standards like SEMI F1, is critical for maintaining purity levels exceeding 99.9999% (6N purity). Metal-to-metal seals or VCR (vacuum coupling radiation) fittings enhance this integrity over traditional threaded connections.
5. Purity and Cleanliness Standards
UHP regulators are cleaned and assembled in ISO 14644 Class 100 (or better) cleanrooms to eliminate particulates, oils, and moisture. Specifications often guarantee less than 10 parts per billion (ppb) of hydrocarbons or water vapor post-installation. Internal surface finishes minimize particle shedding, with some models featuring orbital welding to reduce crevices where contaminants could lodge.
6. Temperature Range
Operating temperature ranges typically span -40°C to 60°C (-40°F to 140°F), though specialized models handle cryogenic gases (down to -196°C/-321°F for liquid nitrogen) or high-temperature applications (up to 200°C/392°F). Temperature affects seal integrity and material expansion, so compatibility with process conditions is essential.
7. Adjustability and Control
Precision adjustment is a hallmark of UHP regulators. Many feature fine-threaded knobs or micrometer-style controls, offering resolution down to 0.1 psi (0.007 bar). Electronic regulators with PID (proportional-integral-derivative) controllers provide even tighter control, integrating sensors for real-time feedback—an emerging trend in smart gas delivery systems.
8. Porting and Connections
Inlet and outlet ports vary (e.g., 1/4-inch NPT, VCR, or Swagelok tube fittings), with configurations like in-line or panel-mount designs. Porting affects dead volume—unused space where gas stagnates—so compact designs with minimal internal volume (e.g., <5 cm³) are preferred to reduce purge times and contamination risks.
9. Certifications and Compliance
Look for compliance with industry standards: SEMI S2 for safety, ASME B31.3 for process piping, or CGA (Compressed Gas Association) specs for cylinder connections (e.g., CGA-580 for nitrogen). RoHS or REACH compliance may also apply for environmental regulations.
Expanding on Specs
To fully leverage these specifications, consider your application’s gas type, flow requirements, and environmental conditions. For instance, a regulator for argon in a cleanroom might prioritize low Cv and electropolished finishes, while one for silane in semiconductor etching needs Hastelloy and sub-ppb purity guarantees. Manufacturers like Swagelok, Parker Hannifin, or Tescom provide detailed spec sheets, often customizable for niche needs.
Gas Compatibility Standards for Ultra High Purity Gas Regulators
Ultra high purity (UHP) gas regulators must be compatible with the gases they handle to ensure safety, maintain purity, and prevent system failures. Gas compatibility refers to how a regulator’s materials, design, and construction interact with a specific gas—whether inert, reactive, corrosive, or flammable—without degrading, contaminating, or posing hazards. Industry standards and guidelines provide a framework for this compatibility, balancing material properties, operational conditions, and regulatory requirements. Here’s an in-depth look at gas compatibility standards and their implications for UHP regulators.
1. Why Gas Compatibility Matters
Gases vary widely in chemical behavior. Inert gases like helium or argon pose minimal reactivity risks, while corrosive gases like hydrogen chloride (HCl) or ammonia (NH₃) can degrade incompatible materials, releasing contaminants or causing leaks. Flammable gases (e.g., hydrogen, methane) demand ignition-resistant designs, and toxic gases (e.g., silane, phosphine) require zero-leak integrity. In UHP applications—where purity levels often exceed 99.9999% (6N)—even trace reactions between gas and regulator materials can ruin processes like semiconductor fabrication or pharmaceutical synthesis. Compatibility standards mitigate these risks.
2. Key Compatibility Standards
Several industry standards govern gas compatibility for UHP regulators:
-
Compressed Gas Association (CGA) Standards: CGA publications like G-4.1 (Cleaning Equipment for Oxygen Service) and connection standards (e.g., CGA-580 for nitrogen, CGA-350 for hydrogen) specify materials, cleaning methods, and fittings. For example, oxygen compatibility requires oil-free components to prevent combustion, often mandating 316L stainless steel over brass.
-
ASTM International: ASTM G93 (Standard Practice for Cleaning Methods and Cleanliness Levels) outlines material compatibility for high-purity gases, emphasizing corrosion resistance and outgassing limits. ASTM A479 defines stainless steel grades (e.g., 316L) suitable for UHP systems.
-
SEMI Standards: The Semiconductor Equipment and Materials International (SEMI) group sets stringent benchmarks. SEMI F19 specifies stainless steel tubing and fittings for UHP gas delivery, requiring surface finishes below 10 microinches Ra and helium leak rates under 1×10⁻⁹ sccs. SEMI S2 addresses safety for toxic or pyrophoric gases like silane.
-
ISO 23251 (API Standard 521): This standard guides pressure-relieving systems, including regulators, ensuring compatibility with flammable or hazardous gases under varying temperatures and pressures.
-
ASME B31.3: For process piping, this code mandates material selection based on gas properties, pressure (e.g., up to 4000 psi), and temperature (e.g., -40°C to 200°C), critical for UHP regulator design.
3. Material-Gas Interactions
Compatibility hinges on material properties (see prior section) and gas characteristics:
-
Inert Gases (e.g., N₂, Ar, He): 316L stainless steel suffices due to low reactivity. PTFE or Kalrez seals ensure minimal outgassing.
-
Corrosive Gases (e.g., HCl, Cl₂, H₂S): Hastelloy C-22 or Monel resists pitting and cracking. Nickel content (e.g., 56% in Hastelloy) counters acidic attack.
-
Oxidizing Gases (e.g., O₂, N₂O): Oil-free, passivated stainless steel prevents combustion. CGA G-4.1 bans hydrocarbon lubricants.
-
Reactive/Flammable Gases (e.g., H₂, SiH₄): Leak-tight designs (e.g., VCR fittings) and non-sparking materials reduce ignition risks. SEMI S2 requires secondary containment for pyrophoric gases.
4. Cleaning and Purity Requirements
Compatibility extends to cleanliness. Regulators must be free of contaminants like oils, particulates, or moisture that could react with gases. CGA G-5.4 specifies cleaning for hydrogen service, while SEMI F20 details sub-ppb purity for electronics-grade gases. Electropolishing and cleanroom assembly (ISO 14644 Class 100) align with these standards, ensuring no residues compromise gas integrity.
5. Testing and Certification
Manufacturers test compatibility via:
-
Helium Leak Testing: Verifies seals meet 1×10⁻⁹ sccs, per SEMI F1.
-
Corrosion Testing: ASTM G31 assesses material degradation in gas-specific environments.
-
Outgassing Analysis: Measures volatile emissions (e.g., <10 ppb VOCs) using mass spectrometry.
Certifications on spec sheets (e.g., “CGA-compliant” or “SEMI F19-certified”) confirm adherence, giving users confidence in a regulator’s suitability.
6. Challenges in Ensuring Compatibility
Mismatches can be costly. Using brass with ammonia risks stress corrosion cracking, while Viton seals with hydrocarbons may swell, degrading purity. Mixed gas systems (e.g., Ar/H₂ blends) complicate material selection, requiring compromises or hybrid designs. Standards help, but users must verify compatibility for unique conditions—consulting manufacturer gas compatibility charts (e.g., Swagelok’s or Parker’s) is a practical step.
7. Practical Application
In semiconductor plants, a regulator for silane (SiH₄) might pair Hastelloy with SEMI F19-compliant VCR fittings to handle its pyrophoric nature. For helium in gas chromatography, a 316L regulator with PTFE seals meets CGA-580 standards, ensuring 6N purity. These choices reflect how standards translate into real-world reliability.
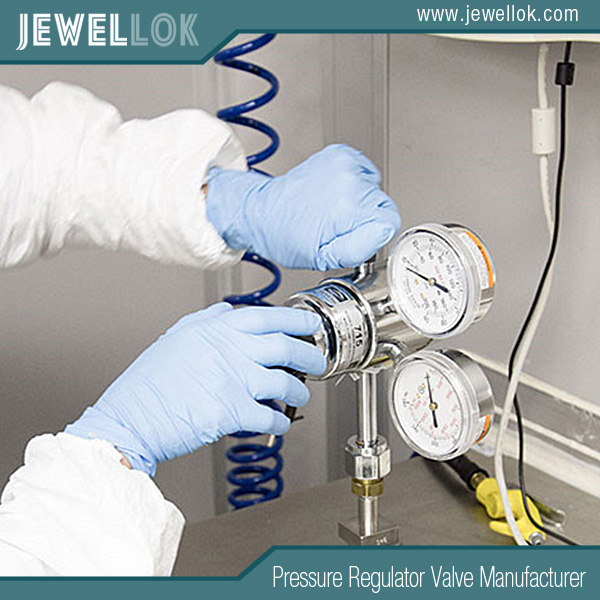
In conclusion, UHP gas regulators are unsung heroes in precision industries. Understanding their role and features empowers users to choose the right tool, ensuring safety, efficiency, and quality in gas delivery systems.
For more about ultra high purity gas regulator, you can pay a visit to Jewellok at https://www.jewellok.com/product-category/ultra-high-purity-regulators/ for more info.
Recent Posts
Tags
1 1 2 gas pressure regulator
1 2 gas regulator
1/2 gas pressure regulator
2 inch irrigation solenoid valve
2 inch irrigation valve
6mm compression fitting
6mm equivalent
8mm compression fitting
adjustable low pressure propane regulator
adjustable propane pressure regulator
adjustable propane regulator
adjusting propane regulator
air compressor non return valve
argon hose fitting
diaphragm suppliers
fluid systems components
gases used in semiconductor manufacturing
gas pipeline valve
gas pipeline valves
gas regulator
high purity valves
how a pressure regulator works
how does a needle valve work
how does pressure regulator work
how often should pressure relief valves be replaced
how solenoid valves work
humming propane regulator
irrigation timer valve
low pressure regulator
pressure gauge manufacturers
pressure regulator
pressure regulator valve leaking
regulator valve alibaba international market
relief vs safety valve
safety relief valve vs pressure relief valve
safety relief valve vs safety valve
safety valve and relief valve
safety valve and relief valve difference
safety valve vs pressure relief valve
single stage pressure regulator
stainless pressure regulator
stainless steel 1/4 in. pressure gauge fitting - 3/8 qc
two stage pressure regulator
valve timer water
what is a gas pressure regulator
Recommended Products
-
762L Stainless Steel High Purity Union High-Purity Gas System Fittings
-
766L High Purity Female Connector UHP Fitting Female Connector
-
7102L Stainless Steel 316L SS Union Cross Ultra High Purity Long Arm Union Elbow Tee Cross Butt Weld Fittings
-
763L Stainless Steel High Purity Pressure Reducing Union Fittings And Tubing Pressure Reducing Valve Adjustment
-
UHP Metal Gasket Face Seal Fittings Vacuum Coupling Metal Face Seal Join Long Gland And Short Gland
-
High Purity And Industria Gas Stick Assemblies Precise Pressure Control Gas Systems JSR-1ETG-BV Series
-
7121L Plug High Purity Plug Fitting And Blanking Plug
-
Stainless Steel Ultra High Purity (UHP) High Pressure Manual Diaphragm Valve