Blog
Jewellok is a professional pressure regulator and valve manufacturer and supplier.
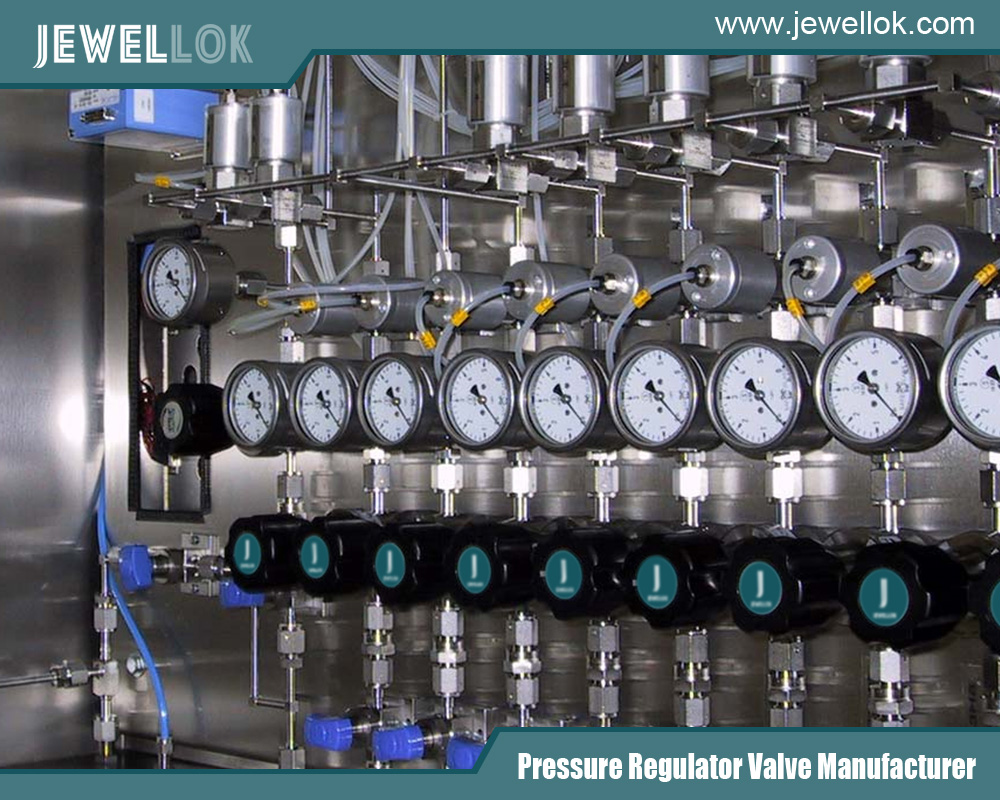
Explaining the Role of a Steam Pressure Regulator in Industrial Systems
- Pressure Regulator Valve Manufacturer
- 1 2 gas regulator, 2 inch irrigation valve, 6mm compression fitting, 8mm compression fitting, argon hose connector, automatic switching valve, fluid systems components, gas pipeline valve, gas pipeline valves, gas semiconductor, gases used in semiconductor manufacturing, high flow co2 regulator, high purity valves, how does a needle valve work, how solenoid valve works, irrigation timer valve, laboratory gas valves, low pressure gas regulator, pressure regulator, pressure regulator valve leaking, regulator valve alibaba international market, relief valve safety valve difference, safety valve and relief valve, single stage pressure regulator, solenoid valve working, Steam Pressure Regulator, Steam Pressure Regulator Hotsale, Steam Pressure Regulator in Industrial Systems, Steam Pressure Regulator Manufacturer, Steam Pressure Regulator Supplier, Steam Pressure Regulator Wholesale, timed water valve, two stage pressure regulator, valve timer water
- No Comments
Explaining the Role of a Steam Pressure Regulator in Industrial Systems
Steam pressure regulators are crucial in various industrial applications, from heating systems to power plants. Their primary role is maintaining consistent steam pressure by adjusting the flow as needed. The ability to control steam pressure ensures the efficient operation of machinery, prevents damage to systems, and improves safety. But how exactly does a steam pressure regulator work? In this article, we’ll explore the principles behind steam pressure regulation, its components, and the steps involved in its operation.
Understanding the Basics of Steam Pressure Regulation
To answer the question, “How does a steam pressure regulator work?” we first need to understand the principles of steam pressure itself. Steam is simply water heated to its boiling point and transformed into vapor. In industrial settings, steam transfers heat or provides power through turbines and engines. However, the pressure of the steam needs to be carefully controlled for both safety and performance.
The Role of Steam Pressure
Steam pressure refers to the f
orce steam molecules exert as they move within a system. This pressure is typically measured in pounds per square inch (PSI) or bar. When steam pressure is too high or too low, it can lead to inefficiency, damage to equipment, and safety hazards. Therefore, a steam pressure regulator helps to ensure that the steam pressure remains within a designated range for optimal operation.
How Steam Pressure Regulators Function
At its core, a steam pressure regulator is a valve that automatically adjusts the steam flow to maintain a consistent pressure in a steam system. While the specifics can vary depending on the application, the basic functionality remains the same. The regulator operates by sensing the downstream pressure and adjusting the steam flow to meet the desired level.
Critical Components of a Steam Pressure Regulator
To understand how a steam pressure regulator works, it’s essential to break down its main components:
- Inlet and Outlet Ports:These are the points where steam enters and exits the regulator. The inlet port connects to the steam source, while the outlet port connects to the equipment or system supplied with steam.
- Sensing Element (Spring or Diaphragm): This component detects the steam pressure. When the pressure deviates from the desired level, the sensing element moves to trigger adjustments in the steam flow.
- Adjustable Spring:This spring is crucial for setting the desired pressure level. When the pressure drops below the set point, the spring helps adjust the regulator to open or close the valve accordingly.
- Regulator Valve:The valve controls the steam flow into the system. As the regulator senses changes in pressure, it adjusts the position of the valve to either allow more steam to flow or restrict it.
- Exhaust Valve: Some regulators have an exhaust valve that helps release excess steam in case of overpressure, preventing damage to the system.
The Mechanism of a Steam Pressure Regulator
A steam pressure regulator works by continuously monitoring and adjusting the pressure within a system. Here’s a step-by-step breakdown of how the mechanism operates:
- Pressure Sensing:The regulator constantly monitors the steam pressure downstream. If the pressure drops below the set point, the regulator recognizes that more steam is needed to maintain the correct pressure.
- Valve Adjustment:To compensate for the pressure drop, the regulator adjusts the valve to increase the steam flow into the system. This is typically done by opening the valve wider.
- Stabilizing the Pressure:As more steam enters, the pressure rises. The regulator continuously adjusts to bring the pressure back to the desired level, keeping the system stable.
- Pressure Maintenance:If the pressure rises above the set point, the regulator closes the valve to reduce the flow of steam, ensuring the pressure does not exceed safe limits.
- Feedback Loop:The regulator works in a constant feedback loop, continuously sensing pressure and making minute adjustments to the valve position, thus keeping the pressure constant over time.
Types of Steam Pressure Regulators
Steam pressure regulators come in various designs to suit different needs. Each type of regulator offers specific features to ensure efficient and safe system operation. Some common types include:
- Direct-Acting Regulators:These regulators use a spring-loaded diaphragm or piston to control the steam flow. The diaphragm responds directly to changes in pressure, providing fast and efficient regulation.
- Pilot-Operated Regulators:These regulators use a small “pilot” valve to control the main valve. The pilot valve responds to changes in system pressure and provides a signal to adjust the steam flow.
- Relief Regulators:These regulators are designed to release excess steam when the pressure rises above a safe limit, ensuring the system remains within operating parameters.
Factors Affecting Steam Pressure Regulation
Several factors can influence the performance and efficiency of steam pressure regulators. These factors must be considered to ensure the regulator functions as intended.
System Demand
- The demand for steam in a system can fluctuate, which requires the pressure regulator to adjust to these changes. If there is a sudden surge in steam demand, the regulator must respond quickly to maintain pressure, often requiring advanced technology or more sensitive regulators.
Temperature Variations
- Since steam is temperature-sensitive, any temperature changes can affect the pressure. Steam pressure regulators must account for temperature variations to maintain consistent pressure levels. For example, steam pressure may drop in colder systems, requiring the regulator to compensate for this loss.
Valve and Regulator Sizing
- Proper sizing of the regulator and valve is crucial for accurate pressure regulation. If the regulator is too small for the system, it may need help to keep up with the pressure demands. Conversely, an oversized regulator can result in inefficiency or unnecessary wear.
System Leaks and Blockages
- Leaks or blockages in the piping or valve system can create irregular pressure readings, leading the regulator to make inaccurate adjustments. Regular maintenance is crucial to prevent these issues from affecting the regulator’s performance.
Advantages of Using Steam Pressure Regulators
Incorporating a steam pressure regulator into an industrial steam system offers several key benefits:
- Consistency in Pressure:By automatically adjusting to fluctuations in pressure, the regulator ensures that the steam pressure remains constant, enhancing system stability.
- Safety:Steam pressure regulators help prevent overpressure situations that could cause equipment damage or safety hazards.
- Energy Efficiency:Maintaining the correct steam pressure helps improve the efficiency of steam systems. By regulating the steam flow, the system uses energy more efficiently, reducing waste and operational costs.
- Prolonged Equipment Lifespan:By controlling the pressure levels, steam pressure regulators help reduce the stress on machinery and components, prolonging their service life and reducing the need for costly repairs.
Common Applications of Steam Pressure Regulators
Steam pressure regulators are used across a wide range of industries and applications. Some of the most common include:
- Power Generation:Steam is a vital component in most power plants. Pressure regulators maintain consistent steam pressure in turbines and other power generation equipment.
- Food and Beverage: Steam is used for cooking, sterilizing, and cleaning in the food processing industry. Regulators ensure that the steam pressure remains stable during these processes, preventing overheating or underheating.
- Heating Systems:Steam provides heat in commercial and industrial heating systems. Pressure regulators help maintain the correct pressure for effective heating.
- Manufacturing:Many processes rely on steam for molding, pressing, and cleaning. Steam pressure regulators ensure that the correct pressure is maintained during these operations.
Maintenance and Troubleshooting of Steam Pressure Regulators
Proper maintenance is essential for ensuring that steam pressure regulators function effectively. Regular checks should include:
- Inspection for Leaks:Ensure no leaks around the regulator or associated piping.
- Cleaning: Regularly clean the valve and internal components to prevent scale or debris buildup that could interfere with the regulator’s operation.
- Calibration:Periodically calibrate the regulator to maintain the correct set pressure.
- Spring Replacement:The spring inside the regulator may wear out over time. Replacing it as part of routine maintenance ensures consistent performance.
Conclusion
Steam pressure regulators are essential devices that help maintain the stability and safety of steam systems. By constantly monitoring and adjusting the steam flow, these regulators ensure that pressure remains within an optimal range, preventing overpressure, inefficiency, and equipment damage. The process is simple yet critical, utilizing a combination of mechanical components to adjust steam flow based on real-time pressure readings. Understanding how a steam pressure regulator works, the factors that affect its performance, and the importance of regular maintenance can help industries optimize their steam systems for maximum efficiency, safety, and longevity.
For more about Explaining the Role of a Steam Pressure Regulator in Industrial Systems, you can pay a visit to Jewellok at https://www.jewellok.com/ for more info.
Recent Posts
Tags
Recommended Products
-
767LP Port Connector Ultra High Purity VCR Metal Gasket Face Seal Tube Fittings
-
770L Female Elbow | Stainless Steel High Purity Weld Fittings Female Micro Elbow Fittings
-
768LN Stainless Steel Male Pipe Tube Butt Weld Connector And Tube Fittings Supplier
-
High Purity And Industria Gas Stick Assemblies Precise Pressure Control Gas Systems JSR-1ETG-BV Series
-
Stainless Steel High Purity High Temperature Pneumatic Actuated Ball Valves JBV2 Series
-
Stainless Steel Ultra High Purity Mini Butt Weld Mini Tee Reducer MTRW Series Fittings
-
762L Stainless Steel High Purity Union High-Purity Gas System Fittings
-
Stainless Steel High-Purity High Temperature Metal Seated Ball Valves JBV3 Series